Robot Vision System RCXiVY2+ New features
Yamaha's own unique solution for integrated robot vision
RCXiVY2+ New features
01High speed positioning of irregular shaped parts (foods or clothes)
Blob search function
Suitable for pick & place or detection of parts with wide tolerance in shape and
size, or high speed counting.
Detection speed is 2 to 10 times faster that edge detection.
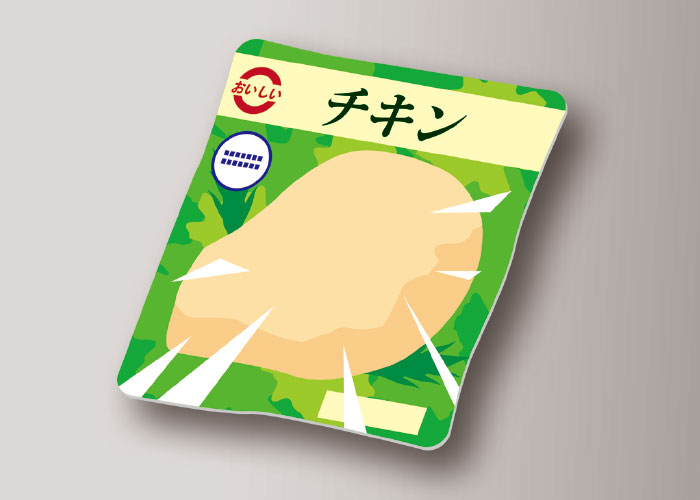
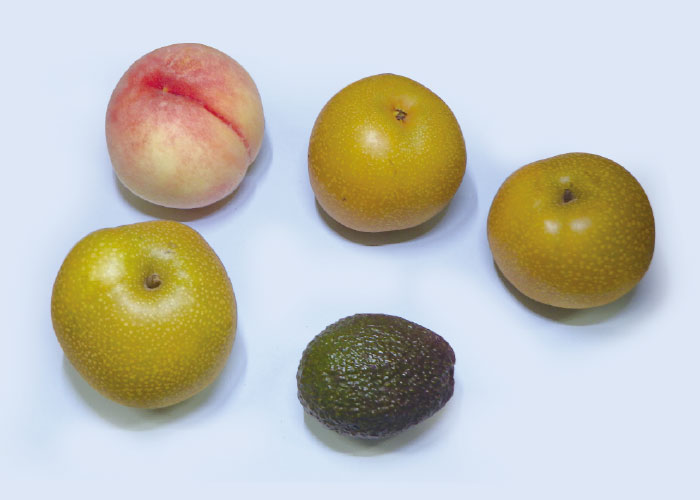
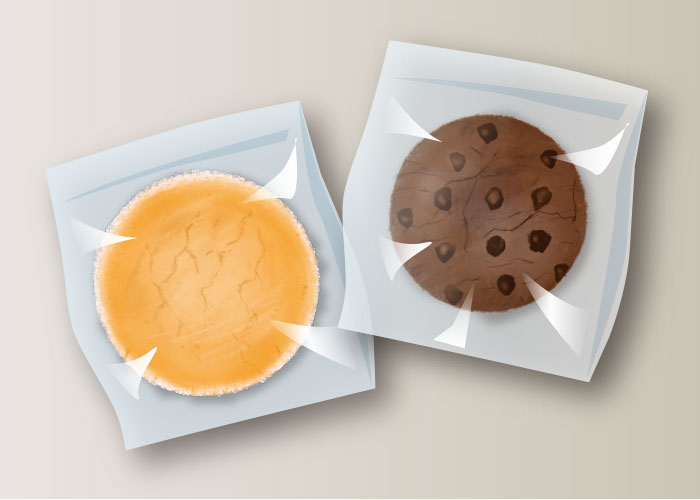
02Detection time is shortened up to 45%.
By adopting a high-performance camera and improving the camera frame rate and CPU capability, detection time is reduced 8 to 45% while the resolution is improved.
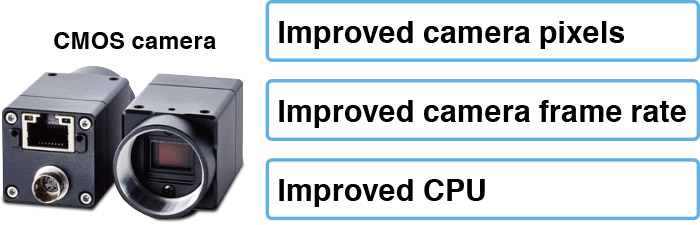
Comparison of search time
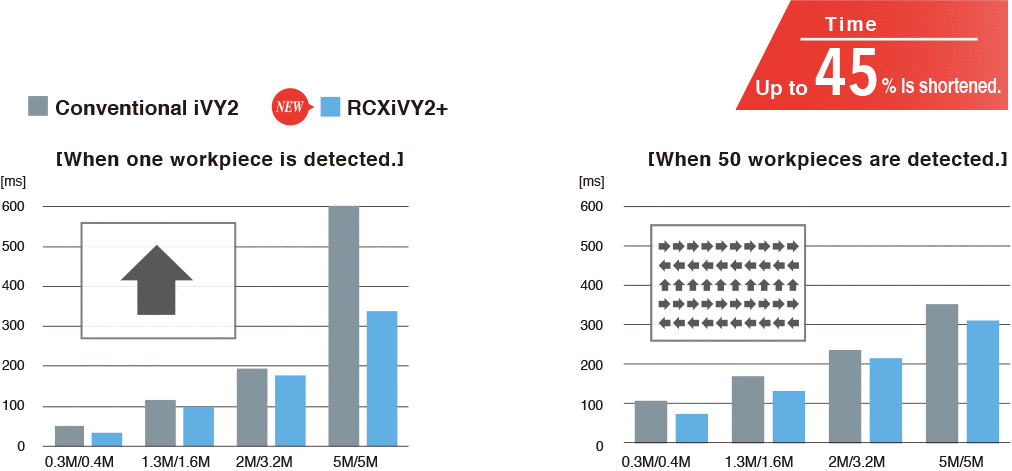
03Suitable for parts detection and high volume parts count
Application examples*Subject to application and conditions.
■ Detection of electronics components on PC board
■ Detection of accessories in package
■ Counting of the number of bottles in pallet
■ Detection of food labels
■ Detection of screws and washers that secure parts
■ Checking drilled holes
■ Counting of electronics components
04Overlap can be eliminated.
Overlapped workpieces are recognized and they can be excluded from the search target.
05Detection with Speed
Comparing with edge search, blob search speed is 2 to 10 times faster.
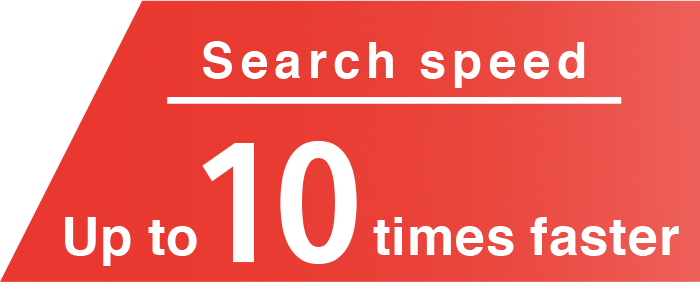
Comparison of edge search and blob search
* Only doughnut shape workpieces are detected.
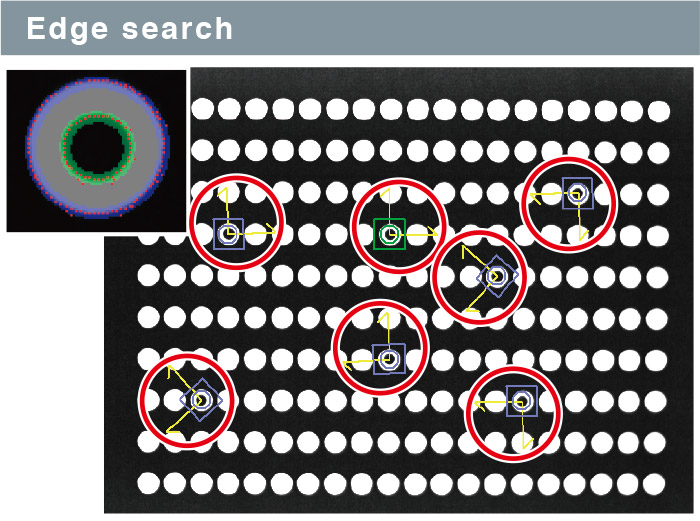
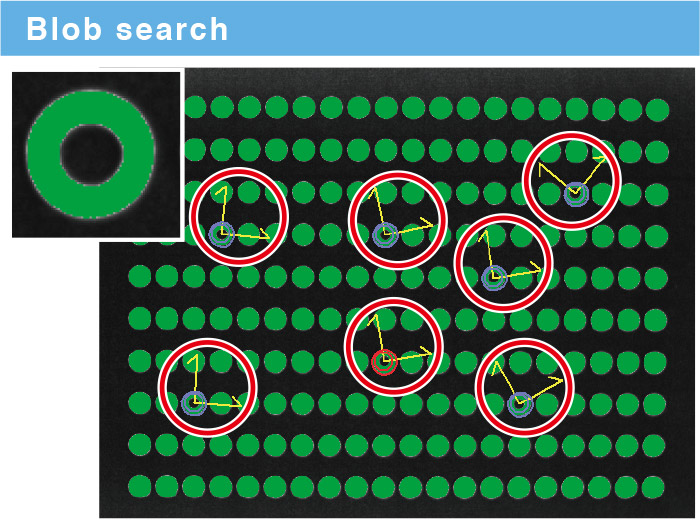
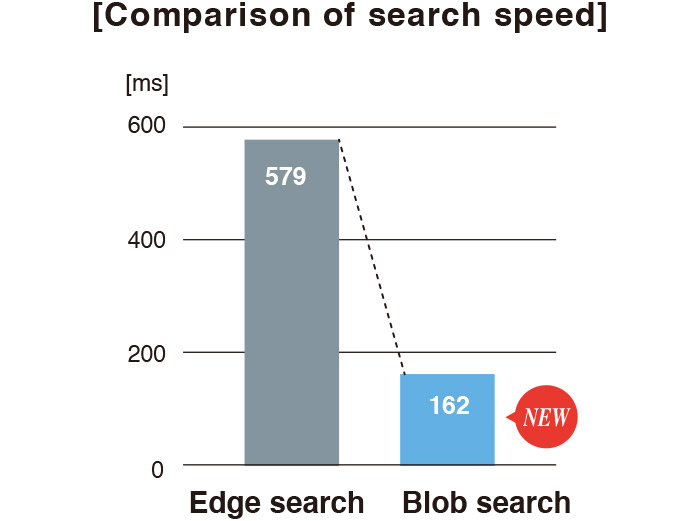
06Code recognition function
Codes such as QR codes, data matrix codes, and barcodes can be recognized.
This code recognition function is optimal for applications that change the operation corresponding to the code contents such as traceability management, workpiece sorting, and tracking change of sealing.
It is not necessary to separately purchase a handy terminal or code reader. Troublesome communication control is also not needed.
・ QR code
・ Data matrix code
・ Barcode (JAN/EAN-13 JAN/EAN-8 ITF NW7 CODE39 CODE128)
* Up to 255 characters can be read. Only alphanumeric characters and symbols are supported. (2-byte characters such as HIRAGANA and KANJI characters cannot be read.)
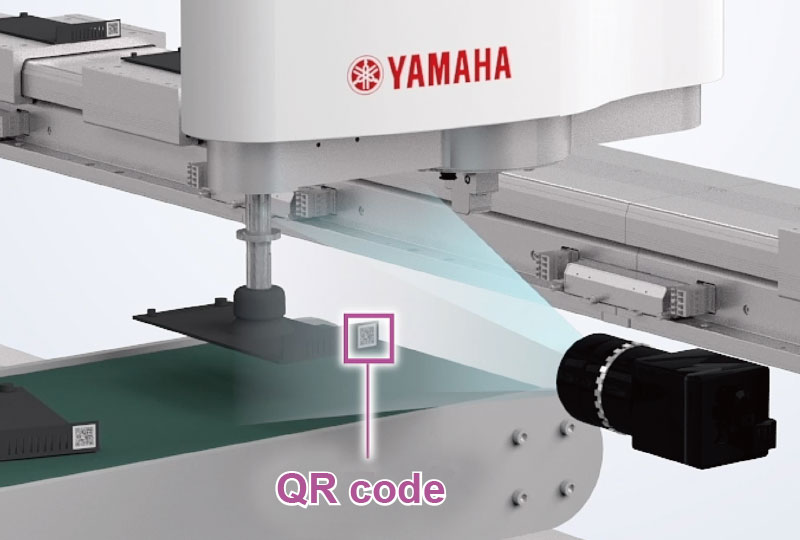
07Automatic image save function/History image function
Images are saved automatically and can be checked easily on an external monitor. These functions are very convenient when you want to check the captured images retrospectively during operation or debugging or save the images for traceability purposes.
Automatic image save function
Images can be saved to a USB memory automatically. An SSD or HDD that can be connected to a USB port can also be used.
Image save mode | All images / NG images / Disabled |
---|---|
Image size | Full size / Reduced size (320 x 240 pix.) |
Overwrite save | Disabled / Enabled (The images are deleted from the oldest image when enabled.) |
Number of camera pixels | Image size | Number of images that can be saved |
---|---|---|
0.4 million pixels | 0.4MB | 327680 |
1.6 million pixels | 1.6MB | 81920 |
3.2 million pixels | 3.2MB | 40960 |
5 million pixels | 5.0MB | 26214 |
Reduced size | 0.08MB | 1638400 |
Number of images that can be saved = Memory size / Image size
81920 images can be saved by 1.6 million pixel camera when 128 GB memory is used.
When the cycle time is 3 seconds, images for 68 hours can be saved.
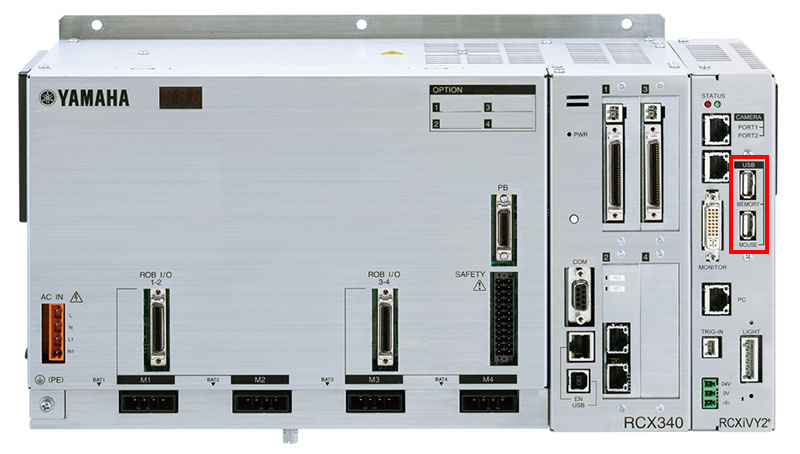
History image function
Images can be displayed on an external monitor during searching. The images and search results can be checked retrospectively with a USB mouse connected.
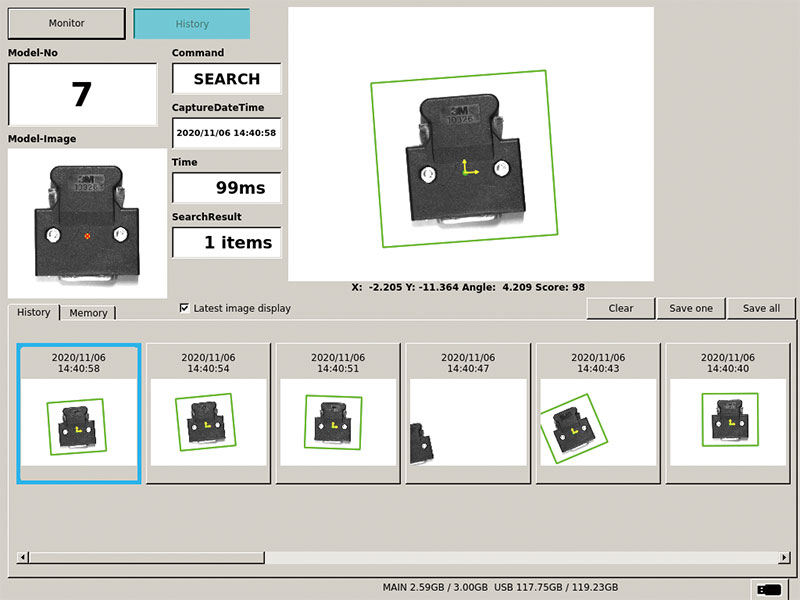
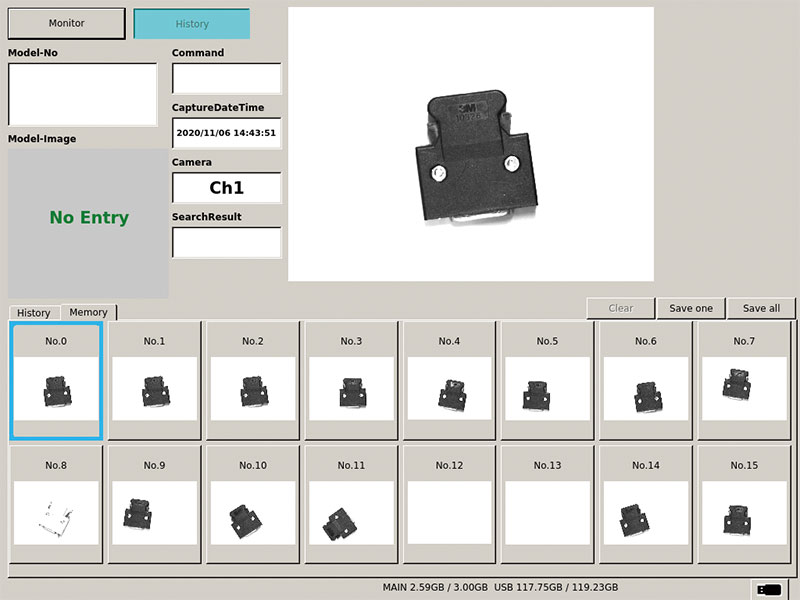
Number of camera pixels | Image size | Number of images that can be saved |
---|---|---|
0.4 million pixels | 0.4MB | 1250 |
1.6 million pixels | 1.6MB | 312 |
3.2 million pixels | 3.2MB | 156 |
5 million pixels | 5.0MB | 100 |
Area for history images 500 MB
Number of images that can be recorded to the history = 500 MB / Image size
08Connection of multiple cameras
Up to eight cameras can be connected via HUB and support various applications such as addition of code recognition camera.
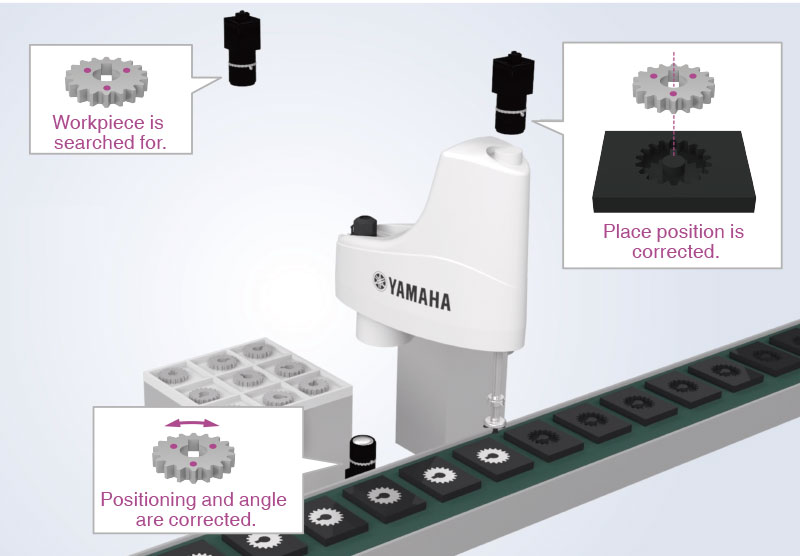
[Application using three cameras]
1. Workpiece supply position is corrected using the downward camera.
2. Workpiece positioning or angle is corrected using the upward camera.
3. Place position is corrected using the downward camera.
Various data
Robot Vision System RCXiVY2+ New features
Related contents
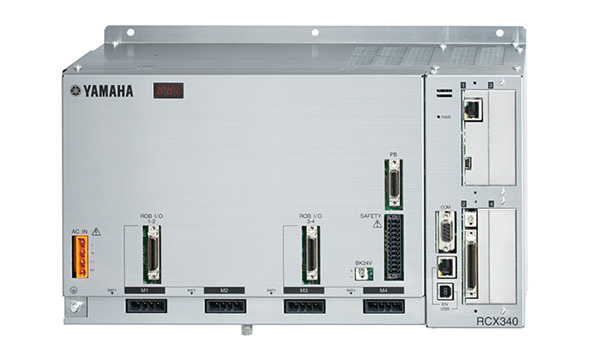
- Multi-axis controller RCX340
- Introduces the multi-axis controllers, RCX340.
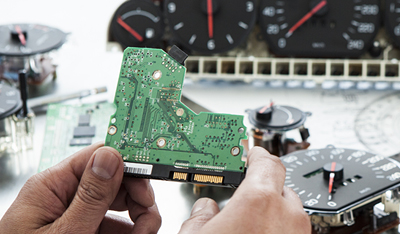
- Reduce setup time by 80%.
- Why does it take surprisingly short time to build up a robot vision system?
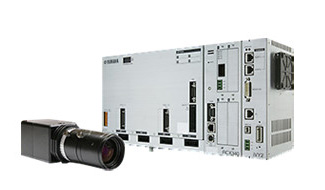
- Robot with vision processing function (Application examples)
- Introduces the applications of the robots with vision processing function.
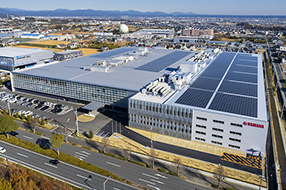
Robotics Business Unit
Sales & Marketing Section
FA Sales & Marketing Division
127 Toyooka, Chūō-ku, Hamamatsu, Shizuoka 433-8103, Japan
Telephone +81-53-525-8350 /
Facsimile +81-53-525-8378