Linear Conveyor Module LCMR200
Yamaha’s answer to Next Generation of Production Line design
Basic specifications
Drive method | Linear motor with moving magnet type core | |
---|---|---|
Position Search | Magnetic absolute position sensor | |
Maximum payload | 30kg | |
Maximum speed | 2,500mm/sec *1 | |
Repeatability | +/-5 μm | |
Mechanical tolerance between robot sliders | +/-30 μm (Dowel hole standard) | |
Total stroke limit | 25.5m *2 | |
Maximum number of robot sliders | 64 units *2 | |
Minimum spacing between robot sliders | 210mm *3 | |
Main frame dimensions | Max. external size of frame cross-section | W175 × H109 mm (Including robot slider) |
Linear module length | 200 mm / 300 mm / 500 mm / 1000 mm | |
Robot slider length | 198mm | |
Weight | Linear module | Approx 20 kg [Per 1 m of linear module] |
Robot slider | 2.4kg | |
Power supply | Control power supply | 48 VDC +5 %, -10 %, Max. 30 A *4 |
Motor power supply | 48 VDC +/-10 %, Max. 30 A *5 | |
Operating environment | Operating temperature | 0 ℃ to 40 ℃*6 |
Storage temperature | -10 ℃ to 65 ℃ | |
Operating humidity | 35 % to 85 %RH [No condensation] | |
Controller | YHX controller *7 |
- *1.
- When the conveying weight exceeds 10 kg, it will drop to 1,000 mm/sec according to the weight.
- *2.
- It may differ depending on the system configuration.
- *3.
- When the jig palette to equip to the robot slider is longer, it shall be the jig palette length + 10 mm.
- *4.
- Up to 10 m linear module can be supplied with the optional 1000 W power source.
- *5.
- Up to 2 robot sliders can be supplied with the optional 1000 W power source.
- *6.
- Operate LCMR200 in the temperature environment (+/-5 °C) that installation and adjustment were performed.
- *7.
- The YHX controller requires a separate electrical power supply.
Standard profile specification
Applicable controller | YHX-HCU | |
---|---|---|
Operation method | Point trace point No. specified positioning and direct value coordinate specified positioning. | |
Comparative robot | LCMR200, LCM-X and GX series (LCMR200 and LCM-X cannot be controlled together). |
|
Interface | YHX-PP, and field network communication | |
Operation type | Absolute position moving | |
Maximum number of points that can be registered. | 65535 | |
No. of control axes (Total of sliders and single-axis robots, however, up to 16 axes for single-axis robot) |
EtherCAT | 64 |
EtherNet/IP™ | 64 | |
PROFINET | 64 | |
CC-Link | 22 | |
Main input and output See the manual for other functions. |
All axes target input | Servo ON/OFF switch/Interlock/Alarm reset |
All axes target output | Servo State/Interlock State/Alarm State/Heart beat/Emergency stop State | |
Individual axis target input | Servo ON/OFF switch/Return to Origin/Positioning moving inside the control range (including LCM relay operation)/Slider insertion preparation from outside the control range/Slider discharge to outside the control range/Jog movement, inching movement/Movement Stop | |
Individual axis target output | Servo State/Return to origin State/Output specified point No. for various execution state display/Current position/Axis alarm State | |
Main remote command See the manual for other remote commands. |
Writing/reading of setting data | |
Alarm check | ||
Writing and reading of integrated running distance and No of transits. |
Linear Conveyor Module LCMR200
Related contents
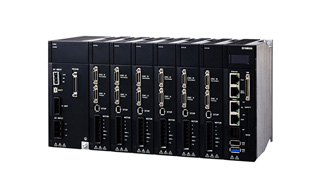
- Universal Controller YHX series
- YAMAHA's Advanced Robotics Automation Platform realizes cooperative motions and synchronized control among all the robots, peripheral units and devices that make up an automated line.
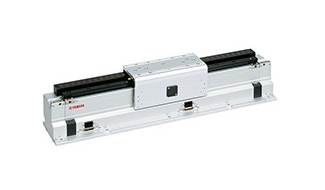
- Linear Conveyor Module LCM100
- Next generation linear conveyor LCM100 supersedes belt conveyors and roller conveyors.
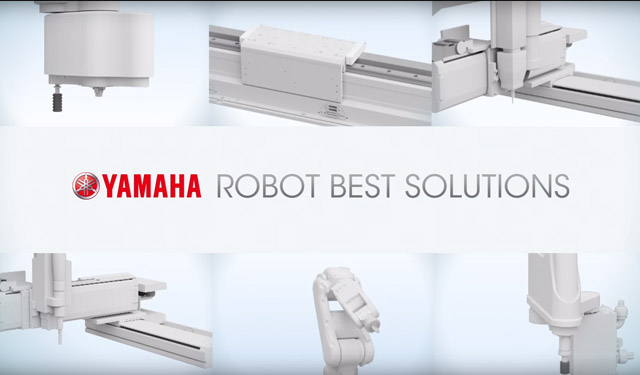
- Robot Movie Channel
- Yamaha Motor Robot Official Channel
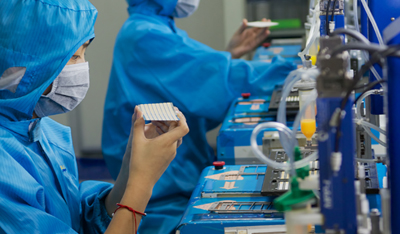
- Shorten takt time by 2 seconds!
- Selection of linear conveyors that defy conventional wisdom for lines.
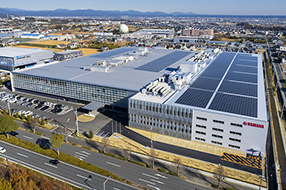
Robotics Business Unit
Sales & Marketing Section
FA Sales & Marketing Division
127 Toyooka, Chūō-ku, Hamamatsu, Shizuoka 433-8103, Japan
Telephone +81-53-525-8350 /
Facsimile +81-53-525-8378