Shorten takt time by 2 seconds! Selection of linear conveyors that defy conventional wisdom for lines.
We interviewed the customers who had in fact installed YAMAHA robots. You can find tips that may provide solutions to your problem.
Electronics devices assembler, Firm A Production control department
Short product life cycles call for device manufacturing facilities to be flexible.
Firm A was dealing with the request for shortening delivery time from their customer.
Issues
Keys to the issue
- Shorten the takt time by 2 seconds.
- Design a line of high productivity within a limited space.
"Cut two more seconds" seemed nowhere to go ... Voice of "give up" from the workshop floor.
Shortening the takt time was the biggest issue in Firm A that assembled the electronics parts and devices for smart phones and tablet terminals. Where number of products put on markets was somehow reducing, every single manufacturer tried to be the first to market their products for the next season. Naturally, such fierce competition affected the device manufacturer of Firm A.
"To fulfill the delivery demanded by the customer manufacturer, we had to shorten the takt time by two seconds or more. The voice from the shop floor said ‘What should we do more? Have we not come to the limit?’", recalled Mr. M, who was in charge of this task. The firm had had not only reviewed the production processes but also added lines to be compatible with production of large variety. Thus, having responded to a demand after a demand, there was a kind of ‘give up’ feeling in the firm.
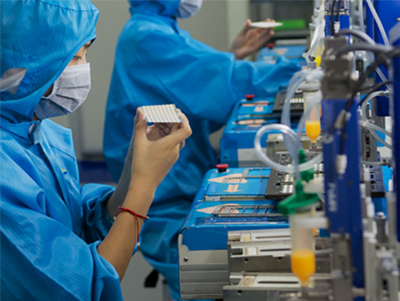
The transport process was the target. Though verifying to increase the tray feed speed, it turned out to create more loss ...
But giving it up was not an option. The project team newly formed with Mr. M as the leader started verification, closing in on reduction of the transport process.
The project team first took a look at the tray feed speed of the conveyor. Being unable to adjust the speed, the impact of hitting the stopper was excessive, causing losses such as a workpiece to get displaced and a pallet to get damaged. To rectify such problems, however, we fell into a vicious cycle in which we had to stop the line, which further degraded the production efficiency.
The production system was not without an issue, either. Repeated layout changes and addition of lines left no more space for an additional line. Setup changes took too many man-hours to fit a small lot production.
"Shortening takt time was far more difficult than I had expected." (Mr. M)
The project members in fact got nowhere without a solution.
Solution
Points to solution
- Improving the transport process shortens the takt time by 1.5 seconds.
- A free line design that moves in both directions cuts down the space required for equipment installation.
A slider moving in both directions suggests possible opportunities of linear drive.
When the Mr. M’s project team was gathering information, they came across the YAMAHA’s "Linear Conveyor Module LCM100" on YouTube.
"Simply surprising! That was the first impression." (Mr. M)
Conventional transport was in one direction only. The motion video, however, showed a slider moving in both directions on the conveyor. Firm A contacted YAMAHA on the spot to collect more detailed information.
The most significant feature of the "LCM100" was high speed, high accuracy motion. A single module packed a linear motor, a slider, and a controller. Servo controlling each slider stops the slider smoothly at the exact position without hitting a stopper. This could shorten the feed time.
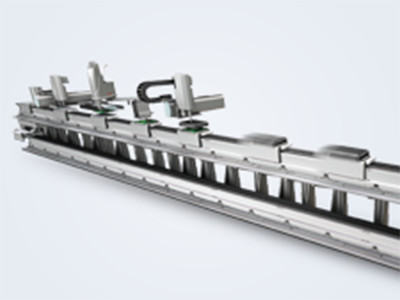
A test operation shortened the takt time by 1.5 seconds! Now, the 2-second barrier seemed a little shorter.
The easy-to-install feature was attractive as a mid to long term capital investment. The layout changes were smooth. All you had to do was increasing or decreasing the number of modules to deal with the line length. Eliminating otherwise necessary jigs and fixtures gave us more freedom and flexibility to build a line. I thought it might help us better deal with high-mix, low-volume production which Firm A was not good at so far. Firm A decided to go through a test that, if passed, led to introduction.
The test went smooth as YAMAHA provided us with technical cooperation. Setting the target of shortening the takt time by 2 seconds from 6 seconds to 4 seconds, the test actually shortened the time by 1.5 seconds. The Mr. M’s project team decided to introduce the system for the line that planned to manufacture the products for the next season. As further improvement is going on with the support from YAMAHA, clearing the 2-second barrier seems just a matter of time.
"Although we have not rolled over the 2-second barrier yet, the entire team members feel definitely positive with the achievement so far. We think we successfully respond to the customer manufacturer’s demand." The moral of the project team members is ever high towards the goal.
Here’s a solution that gets rid of this issue.
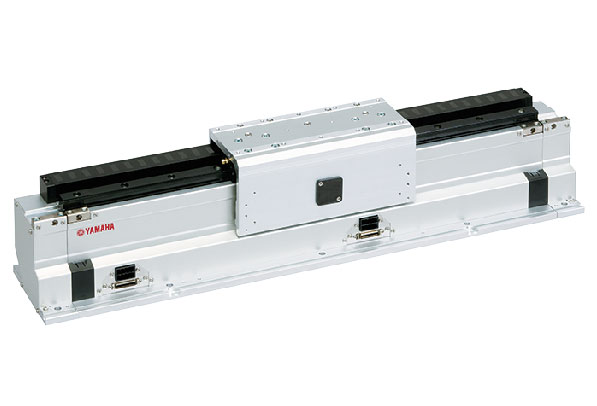
LCM100
The "LCM100" is next generation transport equipment that provides solutions to issues and problems that customers have on manufacturing floors such as useless things, time wasting events, cost reduction, productivity improvement, and better quality. With a variety of features such as high speed transport, smooth deceleration to a stop, direct positioning, and enabling operators to do the jobs on the sliders, the "LCM100" gets rid of unnecessarily wasteful events and elements among processes to improve the productivity.
Related Case Studies
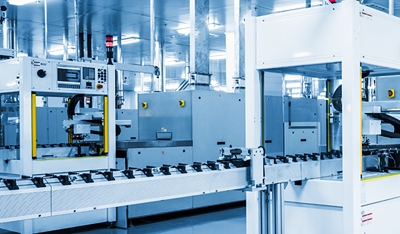
- Challenge to width as narrow as "500 mm"
- What makes it possible to lay out plural processes in a narrow width?
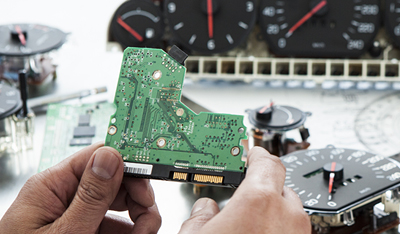
- Reduce setup time by 80%.
- Why does it take surprisingly short time to build up a robot vision system?
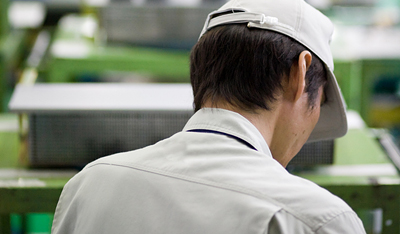
- Shorten equipment startup time to half!
- A brand new idea that replaces index tables
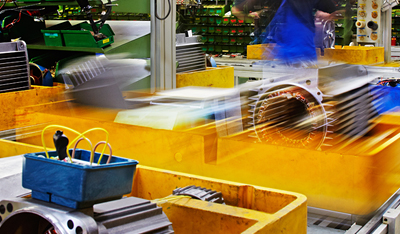
- We need both! - coating accuracy and speed increase.
- What does a sealing process go for to improve productivity?
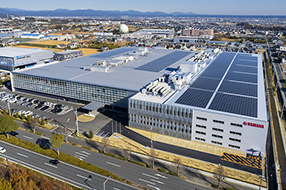
Robotics Business Unit
Sales & Marketing Section
FA Sales & Marketing Division
127 Toyooka, Chūō-ku, Hamamatsu, Shizuoka 433-8103, Japan
Telephone +81-53-525-8350 /
Facsimile +81-53-525-8378