Challenge to width as narrow as "500 mm" What makes it possible to lay out plural processes in a narrow width?
We interviewed the customers who had in fact installed YAMAHA robots. You can find tips that may provide solutions to your problem.
Electronics parts manufacturer, Firm K Production engineering department
Increasing material costs and wage hike prompts many business owners to close overseas factories and move the manufacturing bases back to Japan.
Firm K also decided to shift part of the overseas manufacturing functions back to the small, existing factories in Japan.
Issues
Keys to the issue
- Add a line in a space as narrow as 500 mm wide.
- Make the line flexible because of short life cycles of products.
Move the Chinese manufacturing functions back to their original, small factories in Japan.
With manufacturing costs ever continuing to rise, Firm K decided to close part of the factory in China. It was decided that these manufacturing functions were distributed to plural bases in Japan.
The department which Mr. S works for had a plan to accommodate some of these processes. "To be honest, the team members thought that they could not expand the work floor any further ...", said Mr. S.
We needed to rearrange the processes in order to accommodate the Chinese manufacturing functions while keeping utilizing the present line. Obviously, however, the existing facility did not have enough extra space. We drew layout plans over and over again, but we could give only a space of a little more than 500 mm wide.
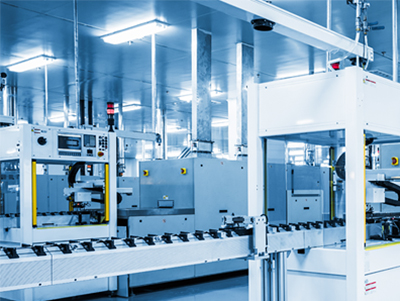
Flexible line design is desired commensurate with the product life cycles, but ...
It was another issue of ours that we had to change the line design periodically. A certain product has a short life cycle, calling for a line design change in a short period of time.
"We actually considered introducing ‘Parallel Links’. In addition to robot main bodies, however, we had to prepare sturdy frames to suspend robots from the ceiling. We anyway did not know how sturdy they were". (Mr. S)
We had had a vibration problem of frames before that were not rigid enough. The bitter experience ending up re-ordering frames had concerned us. Since the frames occupied a fair portion of the cost, it was another concern that we were unable to estimate the total cost.
Solution
Points to solution
- The orbit type SCARA robots suspended from a ceiling can be installed in a limited space.
- The wide movement range makes the robots flexibly compatible with modification of equipment.
Actually installed in space we had given up! "The orbit type SCARA robots with a wide range of movement suspended from the ceiling" was the best solution.
Mr. S decided to talk with a few robot manufacturers. The proposal from YAMAHA, one of them, interested Mr. S very much.
The YAMAHA representative explained to Mr. S and his team members, "Since the ‘YK350TW’ is suspended from a ceiling, it does not require space for installation. A space of 500 mm wide is enough. You can effectively utilize the space immediately under the robot. The robot gives you freedom of layout design." His instinctive feeling told him that it was suitable for installation in a limited space.
"The sales representative showed me a motion video. The motion of the robot that wasted no time or action really surprised me." (Mr. S)
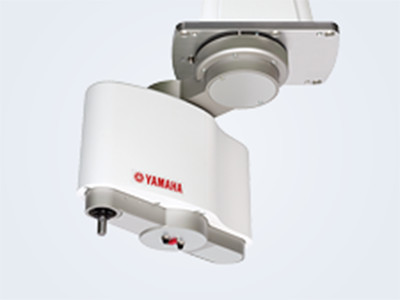
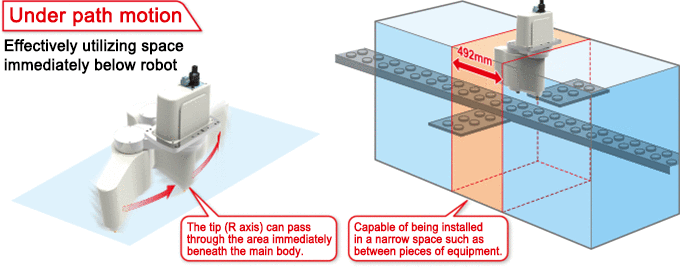
No need to worry about frames. Highly flexible, free layout. The line you can use for a long period of time.
Even under such circumstances, it was easily predicted that I had to hear "Suspended from ceiling!?" from within the members. Since YAMAHA had a series of optional frames in their menu, we just left the line design to YAMAHA, including the strength evaluation of frames. This enabled to introduce the line while minimizing the initial costs. Thus, Firm K decided to install one line as a test case.
Selecting orbit type SCARA robots, Firm K successfully introduced a compact line design. The other manufacturing bases of Firm K are now considering this particular project method that adds a line as planned.
"The persons in charge who had the same headache as we did came visiting us from other manufacturing bases. They saw and learned the installation." All of them reacted "why didn’t I think of it! Nice trick!" (Mr. S)
It is also a favorable evaluation, according to Mr. S, that highly flexible, free layout will make it easier to modify the equipment and thus we can use it for future.
Mr. S said, "This project strongly reminded me of the importance of consulting with the professional. You cannot tell what you can do from the catalog data alone. I am going to come back to YAMAHA for advice on our future projects."
Here’s a solution that gets rid of this issue.
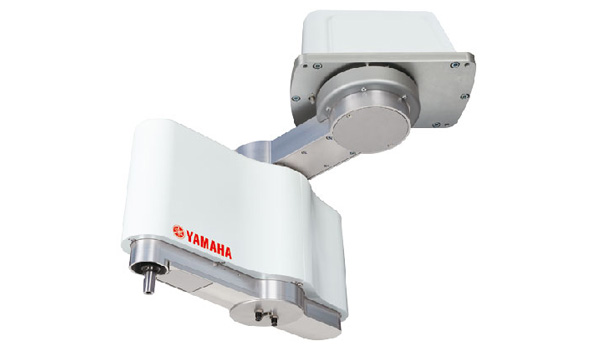
YK350TW/YK500TW
The "YK350TW/YK500TW" are orbit type SCARA robots that eliminate the shortcomings of ordinary SCARA robots and parallel-link robots to achieve high accuracy assembly and shortened takt time while making equipment compact.
A low profile, light weight design for installation in a small space enables flexible, free layout.
Related Case Studies
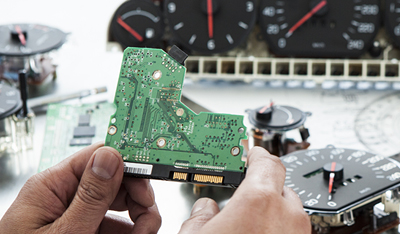
- Reduce setup time by 80%.
- Why does it take surprisingly short time to build up a robot vision system?
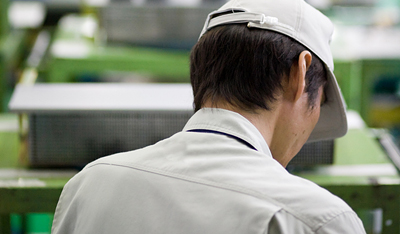
- Shorten equipment startup time to half!
- A brand new idea that replaces index tables
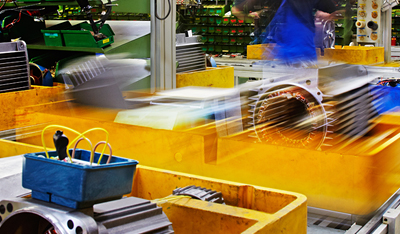
- We need both! - coating accuracy and speed increase.
- What does a sealing process go for to improve productivity?
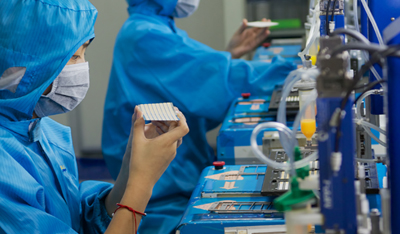
- Shorten takt time by 2 seconds!
- Selection of linear conveyors that defy conventional wisdom for lines.
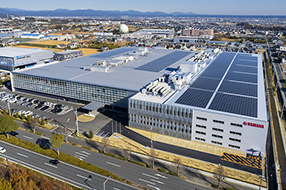
Robotics Business Unit
Sales & Marketing Section
FA Sales & Marketing Division
127 Toyooka, Chūō-ku, Hamamatsu, Shizuoka 433-8103, Japan
Telephone +81-53-525-8350 /
Facsimile +81-53-525-8378