Shorten equipment startup time to half! A brand new idea that replaces index tables
We interviewed the customers who had in fact installed YAMAHA robots. You can find tips that may provide solutions to your problem.
Electronics parts manufacturer, Firm N Manufacturing department, Firm N
The electronics parts industry needs flexible manufacturing facilities to cope with short life cycles of products.
Firm N repeatedly adjusted and modified their facilities every time they had to face product type changes.
Issues
Keys to the issue
- Get the setup done promptly for product type changes.
- Secure the maximum productivity with the minimum space occupation.
We have only 3 months left for product type change ... Man-hours reduction is a must.
It was an issue for the electronics parts manufacturer Firm N to improve the efficiency of manufacturing facility modification associated with a change in product type.
Meanwhile, the firm came up with a plan to build a line for the sale of a new product. The firm had to start up the production in 3 months.
The index tables used previously took a lot of time and labor to adjust the evermore fine-tuned stop position. Every time when modifying the line for product type changes, the persons in charge of equipment had to have a difficult time to make it in time.
Where two or more index tables were laid out, the technicians had to come around many times among the index tables for adjustment and maintenance of the equipment. The poor workability for assembling and adjustment among the index tables gave the equipment technicians a lot of huge stress.
The limited time for building the line made it a must to decrease man-hours and improve efficiency.
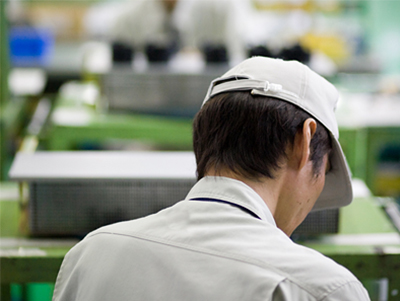
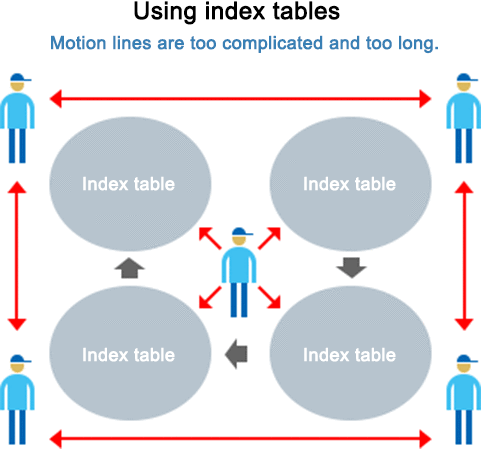
We have no more space for installing additional index tables!
This is not only the issue that troubles equipment technicians. There are more.
To cope with the increased number of processes, we could do nothing but thought that the existing index table was so small that we had to add one more set or introduce a bigger one instead. We then had to hear the shop engineer in charge say "There is no more space available".
Solution
Points to solution
- Review the transport mechanism to shorten the equipment start up time by 50%.
- The line can be built straight to improve the workability.
- Decrease the equipment footprints.
The module type transport mechanism helps design a flexible, easy to use line.
Mr. Y looked for measures to build the line without using index tables, too. While collecting information in manufacturers’ exhibitions, YAMAHA’s linear conveyors "LCM100" drew his attention.
"I saw many pieces of transport equipment. But I have never seen before the linear conveyors that occupy this small space and operate so efficiently. The YAMAHA’s linear conveyors made me feel that this would solve our issues".
Mr. Y diligently listened to YAMAHA’s person in charge down to the details.
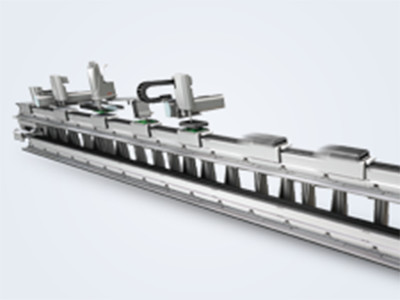
The "LCM100" product is module type linear conveyors that enable free, flexible line design that saves space. More than one slider on the conveyor moves at high speed and at high accuracy. Fine tuning the stop position is as easy as simply entering values. That is all you have to do. With the “LCM100” linear conveyors, you can deal with product type changes promptly and flexibly.
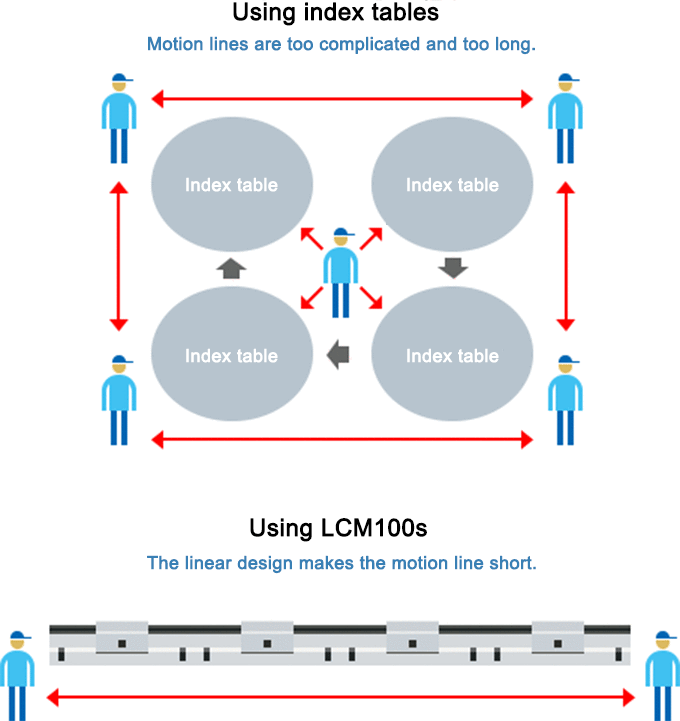
Fits in existing space. You can use the line design for a long term.
"Increasing or decreasing the number of modules can cope with changes in the number of process. It is easy to fine tune the stop position. Those are a couple of reasons what make the "LCM100" our people’s favorite. Despite the complicated line that comprises a lot of processes, the equipment startup time shortens to half compared to the previous, a highly good evaluation coming from the team. The dramatically simplified equipment improves workability and decreases equipment installation footprints. We are considering future expansion of lines", said Mr. Y.
Firm N introduced the “LCM100” instead of index tables. Since the equipment startup went smoothly, the sale of a new product launched on time.
"If the number of processes increases in future, we simply add modules to deal with it. We see that this line can serve us long", said hopeful Mr. Y.
Here’s a solution that gets rid of this issue.
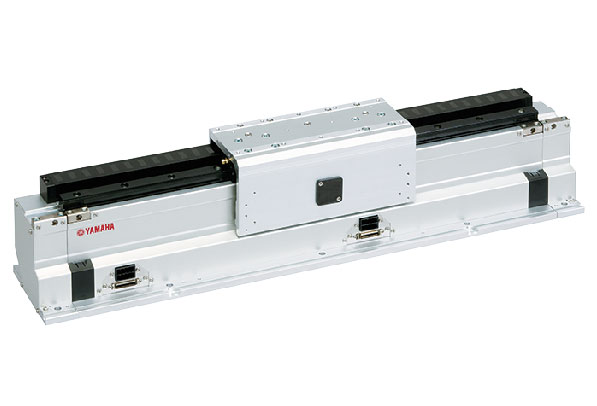
LCM100
The "LCM100" is newly developed next generation transport equipment that provides solutions to uselessness, cost reduction, improving productivity, brushing up quality, and many other issues and problems that trouble customers on workshop floors. With many of its features such as high speed transport, smooth deceleration to a stop, direct positioning, and enabling operators to do the jobs on the sliders, the “LCM100” gets rid of useless things and waste of time between processes to improve productivity.
Related Case Studies
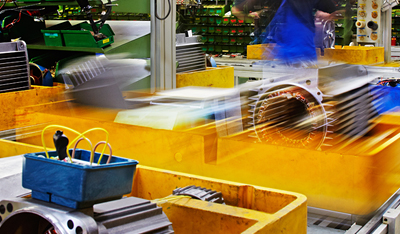
- We need both! - coating accuracy and speed increase.
- What does a sealing process go for to improve productivity?
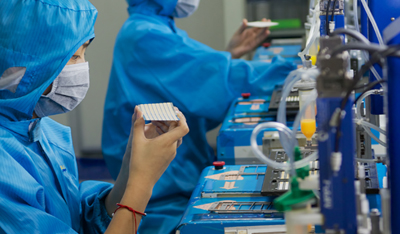
- Shorten takt time by 2 seconds!
- Selection of linear conveyors that defy conventional wisdom for lines.
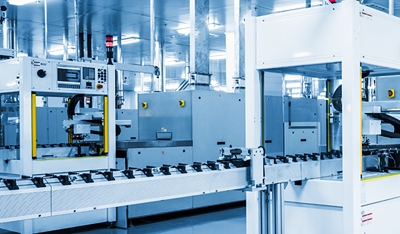
- Challenge to width as narrow as "500 mm"
- What makes it possible to lay out plural processes in a narrow width?
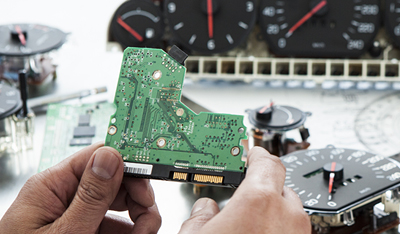
- Reduce setup time by 80%.
- Why does it take surprisingly short time to build up a robot vision system?
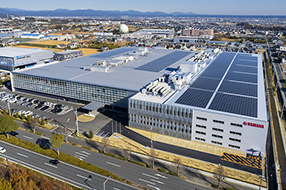
Robotics Business Unit
Sales & Marketing Section
FA Sales & Marketing Division
127 Toyooka, Chūō-ku, Hamamatsu, Shizuoka 433-8103, Japan
Telephone +81-53-525-8350 /
Facsimile +81-53-525-8378