Cost reduction has no choice but going automatic ... Robots that bring down labor rate by 60%
We interviewed the customers who had in fact installed YAMAHA robots. You can find tips that may provide solutions to your problem.
Automobile parts manufacturer, Firm N Production control department
Fierce cost competition made Firm N look for cost reduction measures.
Besides, the most important customer was demanding the firm to increase production.
Issues
Keys to the issue
- Increase the number of automated processes to reduce costs.
- Introducing a robot calls for lifting the ceiling height that is impractically expensive.
More cost reduction has no choice but further automatization!
Diligently coping with repeated cost reduction demands from the important customers, Firm N had come to a point that the current manufacturing processes were unable to reduce costs any further. Worrying that the business would get even worse, Mr. F at the production control department started reviewing the processes of feeding materials to the processing machine and picking up and discharging processed products, then all done manually. He then started studying automatization to achieve rational manufacturing.
It was also a big concern that only one technician worked for the midnight shift - the situation where the firm could do nothing if something wrong, like a personal injury, occurred. If the automatization could achieve complete unmanned operation during the night shift, it would not only reduce labor costs but also get rid of a risk of one-man operation.
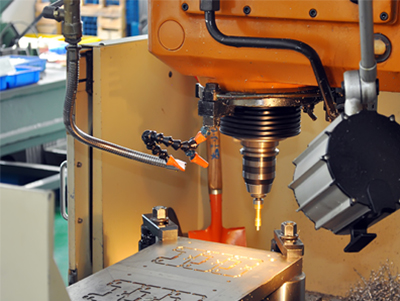
An unexpected cost for lifting the ceiling height became a bottleneck to automatization.
A system integrator firm proposed a takeout robot for automatization. However, the proposal had to lift the ceiling height because the entire vertical axis of the robot moved up and down. The cost including the ceiling modification would significantly go beyond the project budget.
"Since the robot main body was within the budget, I thought this was it for the automatization. However, the further detailed plan required installation footprints that were too demanding for us to cope with ...", Mr. F recalled the time of difficulty.
Solution
Points to solution
- The automatization has reduced the labor rate from the combined rate of labor cost plus machine rate of 130 to the machine rate of 50.
- Introducing a robot was within the budget without a considerable modification.
Achieving automatization without a considerable modification
Mr. F came consulting YAMAHA, which he had had business with.
A person in charge in YAMAHA recommended an articulated robot YA series. Capable of being suspended from a ceiling and easy to install, the robot certainly did not require ceiling modification. The takeout robot that Mr. F had considered previously was with inevitable motion restrictions that were too straightly linear. The articulated robot on the contrary moved flexibly to smoothly access the narrow areas of the processing machine. Even when changing a setup, its point teaching functions made it easy.
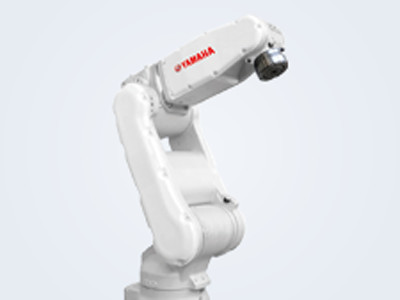
A single controller tames both the articulated robot and long stroke traveling axis.
Since the point of processing was away from the workpiece storage, the automatization required a long stroke traveling axis that the articulated robot alone was unable to cover. As YAMAHA also lined up traveling axes, they came up with a total system including the articulated robot. "It is good that both the articulated robot and long stroke traveling axis are under one single controller. The startup man-hours count has decreased a lot", said Mr. F.
This project of automatization put together dispersed processes while making the pickup and release operation of a workpiece automated. As a result, we reduced the labor rate from the previous combined rate of labor cost plus machine rate of 130 yen per minute to the machine only rate of 50 yen per minute.
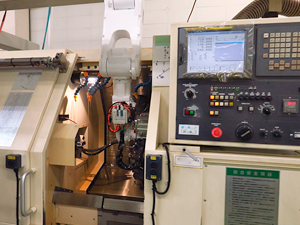
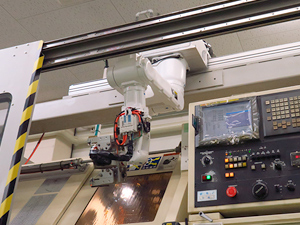
In addition, this particular automatization makes Firm N able to handle a sudden demand for increase in production in good time.
Mr. F was so delighted as to speak "We have achieved a significant cost reduction from the point where we thought it very difficult. Besides, we ensure operator safety, too".
Here’s a solution that gets rid of this issue.
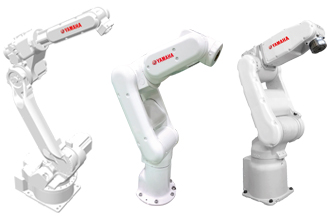
YA series
The articulated robots "YA series" pursue high speed and space saving to contribute to production facilities for improved productivity and downsizing.
The product variations include the 6-axis robots "YA-RJ", "YA-R3F", "YA-R5F", "YA-R5LF", and "YA-R6F" with high axes motion speeds and high wrist load carrying capacities both at the highest level of the class and the 7-axis robots "YA-U5F", "YA-U10F", and "YA-U20F" equipped with an elbow axis that enables free, flexible arm operation.
Related Case Studies
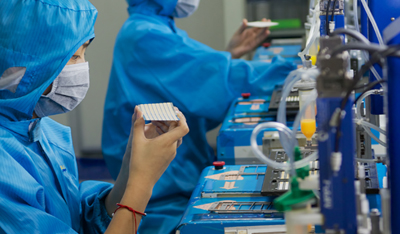
- Shorten takt time by 2 seconds!
- Selection of linear conveyors that defy conventional wisdom for lines.
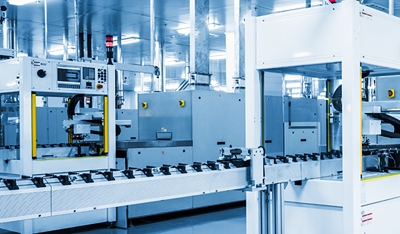
- Challenge to width as narrow as "500 mm"
- What makes it possible to lay out plural processes in a narrow width?
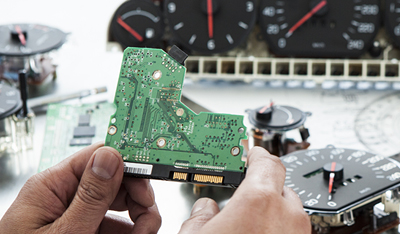
- Reduce setup time by 80%.
- Why does it take surprisingly short time to build up a robot vision system?
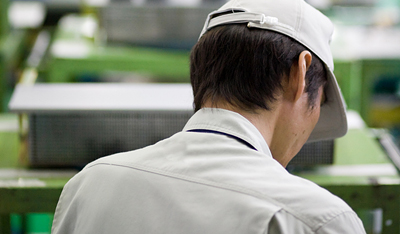
- Shorten equipment startup time to half!
- A brand new idea that replaces index tables
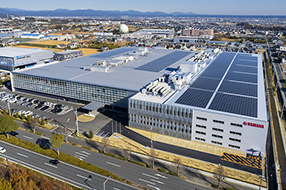
Robotics Business Unit
Sales & Marketing Section
FA Sales & Marketing Division
127 Toyooka, Chūō-ku, Hamamatsu, Shizuoka 433-8103, Japan
Telephone +81-53-525-8350 /
Facsimile +81-53-525-8378