Short breakdown times occur frequently and workers need to stay with the equipment.
The number of drive devices and sensors that caused short breakdown times is minimized. The simple structure makes it possible to prevent short breakdown times.

User:
Operating ratio decreases as short breakdown times occur.

Background of target
- Adverse effects of short breakdown times.
① Delivery delay
② Waste of support man-hour
③ Quality decrease
④ Cost increase due to overtime work
With conventional system...
There are many drive devices and associated sensors, making it easy to stop the equipment.
- Multiple drive devices are required to stop.
- Sensors for controlling drive devices are required.
- If any of drive devices and sensors malfunctions, a short breakdown time occurs.

The number of drive devices and sensors that caused short breakdown times is minimized. The simple structure makes it possible to prevent short breakdown times.

Yamaha's answer to the user's needs:
- The number of drive devices necessary to stop the equipment is minimized.
- Sensors for controlling drive devices are not required.
- The number of load presence sensors and others is minimized.

Production efficiency is improved by reducing short breakdown times and setup work!

As short breakdown times are greatly reduced, the operating ratio is improved and stable production is achieved.

Automotive parts manufacturer
People in charge of production engineering
The number of short breakdown times caused by transfer has been drastically reduced, and we are now able to manufacture products with stable production volume and quality.
Our company is a manufacturer of electronic components built-into automobiles and operates 24 hours a day.
The source of our company's problems was “short breakdown time”. When a short breakdown times occurs, it is necessary to restore it immediately. Sometimes, after resetting the equipment, the short breakdown times might be restored, but it was not a good thing that the short breakdown times was easily restored. Where to recover from the equipment stop was a source of concern at the end of each month.
Particularly in recent years, it has been difficult to manage night shift staffs, and even a minor problem could take a long time to be restored or frequent short breakdown times could cause a small number of workers have to stay with the equipment.
For this reason, we made stable operation one of the themes when considering new equipment. First, as a result of analyzing the causes of short breakdown times, we found that the overwhelming majority of short breakdown times were caused by transfer, so we decided to review the transfer section.
After collecting information from various websites and exhibitions, we became interested in linear conveyor modules.
When we visited the actual machine, we found that the number of driving devices and sensors around the conveyor had been minimized, and we heard that “customers who have installed the equipment are satisfied with the reduced number of short breakdown times!”.
YAMAHA introduced the equipment within the company, and as a result, the equipment received a high evaluation within the company. We were also introduced to a SIer and the equipment was successfully installed.
Currently, as planned, the number of short breakdown times caused by transfer has been drastically reduced and we are now able to manufacture products with stable production volume and quality. The maintenance time also becomes less than half of the conventional time, which is very helpful for the production site. We will continue to manufacture high quality products with stable production.
Functional description and merit of LCM

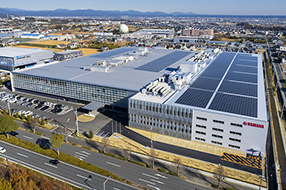
Robotics Business Unit
Sales & Marketing Section
FA Sales & Marketing Division
127 Toyooka, Chūō-ku, Hamamatsu, Shizuoka 433-8103, Japan
Telephone +81-53-525-8350 /
Facsimile +81-53-525-8378