Production quantity needs to be increased with quality problems resolved.
Use of LCMR200 traversing unit makes it possible to perform the inspection on the line.

User:
Production volume needs to be increased with the production efficiency improved.

Background of target
- Some inspection processes take time and cannot be completed in time without performing the inspections off the line.
→ However, repeated line-off to the inspection processes may lead to quality deterioration. (Scratches or particles may occur during transfer.) - Current index table is small and only one workpiece can be placed on one pallet.
Conventional system is improved…
Offline process that takes a time becomes a bottleneck.
- It was considered to increase the size of the index table so that multiple workpieces could be placed on one pallet, but this idea was abandoned because the index table was difficult to adjust.
- Even if the index table can be adjusted to place multiple workpieces, workpieces need to be transferred to the inspection process that is off the line, and quality problems cannot be resolved.
* Particle: Foreign objects (dirt, debris, dust) to be adhered to workpieces

Use of LCMR200 traversing unit makes it possible to perform the inspection on the line.

Yamaha's answer to the user's needs.
- Inspection process can be divided by the traversing unit.
- There is no need to transfer off the line for inspection, eliminating quality problems caused by scratches and particles.
- Multiple workpieces can be placed on a tray, achieving increase in production volume.

Increase in production quantity and decrease in defect rate are achieved at the same time by improving the inspection efficiency!

Securing production quantity and quality improvement are achieved at the same time by increasing the inspection efficiency.

Electronic component manufacturer
People in charge of production engineering
Significant improvement of quality problems is achieved. And then, production volumes to meet market needs can be secured!
Due to increased market demand, we had to increase the production quantity and design additional new equipment.
We were considering the same equipment configuration as the conventional equipment. However, since the overall tact time would be dragged down by the inspection process whose index table is a bottleneck, we would have to prepare two lines of the same equipment to secure the required production volume, which would not fit our budget.
In addition, the current production system involves many transfers among equipment units and also has quality issues such as scratches and particles.
We went to an exhibition to find a good idea. When we stopped by the Yamaha booth, we found the LCMR200 traversing unit. By adopting the LCMR200 traversing unit, three branches allow inspection on the line, so there is no need to perform the inspection off the line as before.
In addition, we find that the high-speed transfer reduces the cycle time and enables simultaneous transfer and inspection of four workpieces, making it possible to achieve the target production volume only on the day shift.
Significant improvement of quality problems is achieved. And then, production volumes to meet market needs can be secured.
Furthermore, reducing the number of workpiece transfers reduces the occurrence of scratches and particles, leading to quality improvement.
All of our employees are very satisfied with the achievement of the production volume, which was thought to be difficult to achieve and the improvement of quality problems.
Functional description and merit of LCM

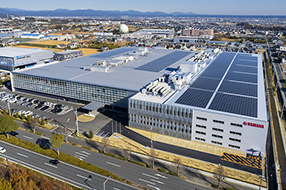
Robotics Business Unit
Sales & Marketing Section
FA Sales & Marketing Division
127 Toyooka, Chūō-ku, Hamamatsu, Shizuoka 433-8103, Japan
Telephone +81-53-525-8350 /
Facsimile +81-53-525-8378