Production lines that enable easy maintenance need to be built.
Use of the LCMR200 increases the workability significantly!
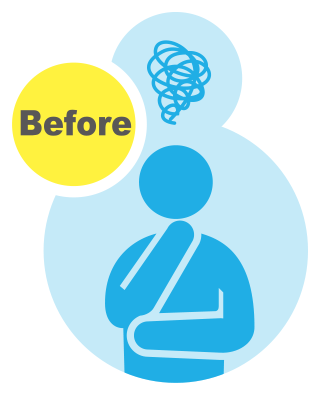
User:
Index table lines are difficult to modify, repair, and maintain.
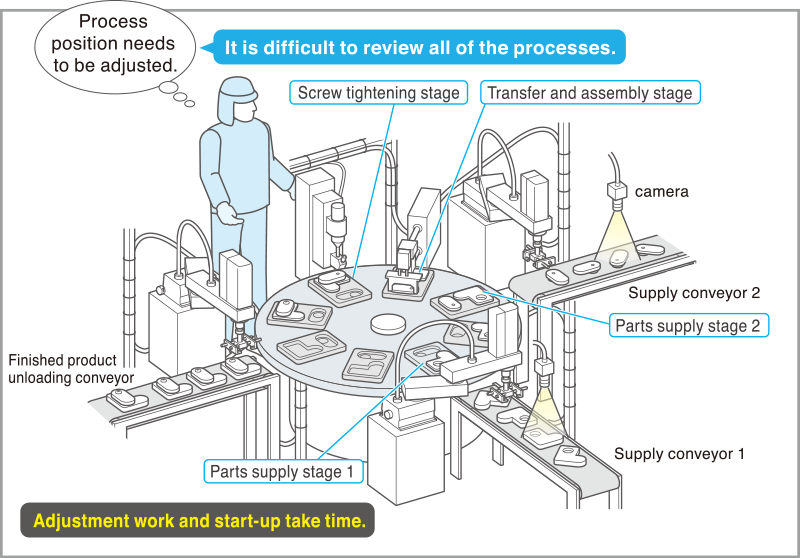
Background of target
- We had a bitter experience with long breakdown times with equipment that uses an index table.
- Before the recovery work was performed, peripheral devices needed to be removed. As a result, we lost a lot of time.
- Workability was poor since the devices tended to be crowded.
With conventional system…
❶ It is difficult to change the stop position.
❷ Peripheral devices are crowded, and the work is difficult to perform.
- Work efficiency drops and it takes time to start up.
- It is difficult to change the stop position since the mechanical positions need to be adjusted.
- It is a difficult hurdle to modify the equipment such as the addition of product types since the number of tables will need to be increased.
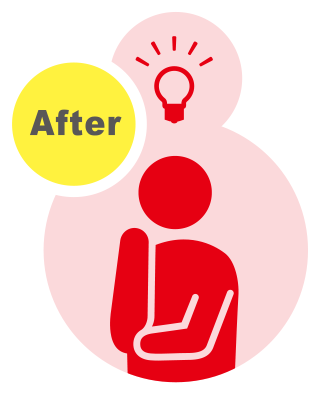
Use of the LCMR200 increases the workability significantly!
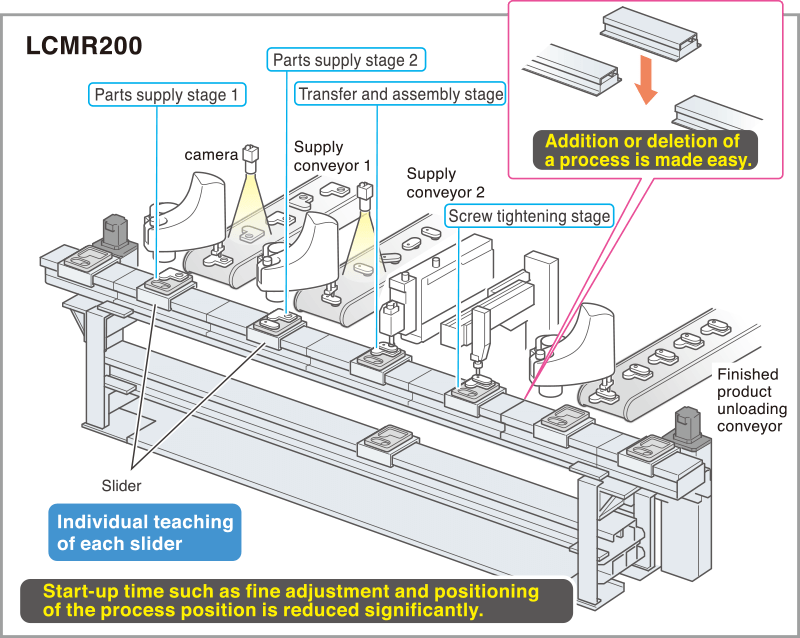
Yamaha’s answer to user’s needs:
- Easy access to the process side as the flow line of the production line is straight.
- To perform the fine adjustment of the stop position, simply change the numeric value setting of the slider position of the LCMR200.
- The modular structure allows for flexible response to minor changes in workpieces and improved maintainability.
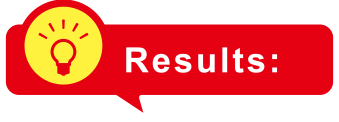
High workability is achieved. Since the time to solve the problem issues is reduced, that provides more time for production.
Time necessary for trouble recovery
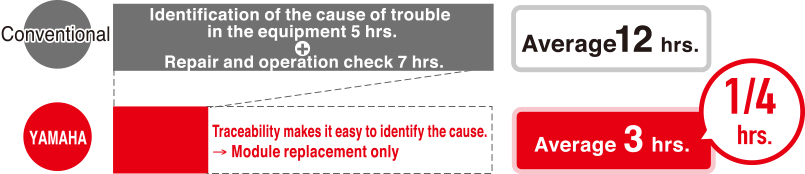
Further effects, or Additional effects.
Time from process addition concept start to process start-up is significantly reduced.
Time from process addition concept start to start-up
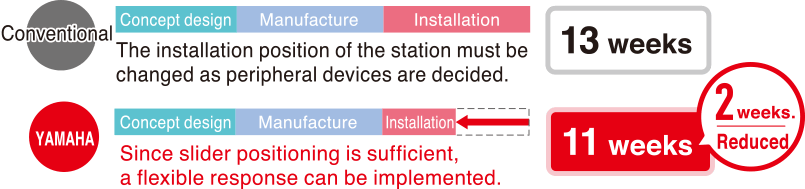
Speedy recovery is now possible even in the event of a problem. Maintenance has become easier and the burden on workers has been greatly reduced.
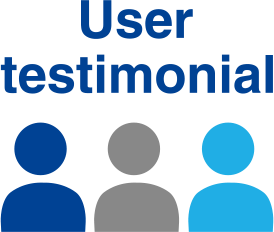
In-vehicle parts manufacturer
People in charge of production engineering
Maintainability improvement/Reduction of start-up man-hour
The production lines we have designed so far have mainly used index tables.
Although the space-saving was good, the equipment was difficult to adjust mechanically inside the equipment when problems occurred, and the poor workability was an issue for the equipment, as peripheral devices had to be removed when the index tables needed to be adjusted.
When we were introduced to YAMAHA's linear conveyor module “LCMR200” at the exhibition, we felt “this is it!”.
We found that the layout of the demonstration machine was neat and clean, which made it easy to design the mechanism and work around the machine, and that traceability was possible using the slider ID, so we decided to adopt it immediately in the next equipment.
Until now, four index tables were arranged, and a belt conveyor and transfer robot were used to connect each index table, but with the LCMR200, we were able to design a line configuration of 2.5 meters each way using the horizontal circulation method.
When we needed to make minor adjustments to the equipment, we did not need to move any peripheral devices, but only needed to adjust the position of the slider. So, even I, a female person, could easily make adjustments and reduce man-hour.
In addition to space savings, less parts are required, and traceability can be easily achieved, so the time required to investigate the cause can be reduce man-hours.
Additionally, the time required for maintenance could be reduced by 50%, which is very efficient.
Since each slider can be operated freely, the production volume has been increased regardless of the time difference between processes.
In fact, thanks to the introduction of this “LCMR200”, we were able to win the in-house president's award, which is a good thing.
We would like to continue to design efficient and highly productive lines.
LCM and conventional conveyor system
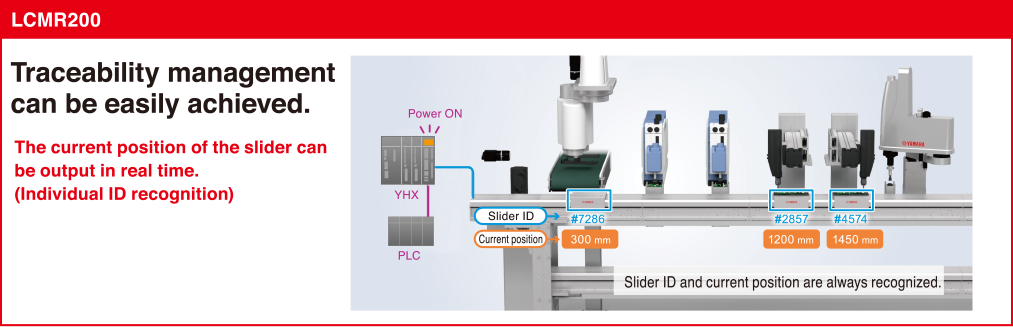
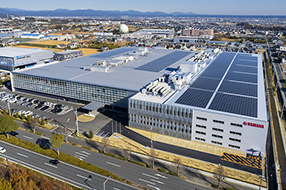
Robotics Business Unit
Sales & Marketing Section
FA Sales & Marketing Division
127 Toyooka, Chūō-ku, Hamamatsu, Shizuoka 433-8103, Japan
Telephone +81-53-525-8350 /
Facsimile +81-53-525-8378