Manufacturing products of multiple models in small lots without lowering the operating ratio
Setup time is almost zero!

User:
Lost time due to setup work is reduced to increase the operating ratio of the equipment.

How to increase the operating ratio
- Manufacture the same model collectively as much as possible.
- Simplify the setup work as much as possible to reduce the work time.
- Accumulate and manualize the work know-how to improve the efficiency.
Improving the conventional system…
It is difficult to increase the operating ratio.
- Each product needs the setup work such as changing of the stopper position.
- Each product needs an individual jig.
- Risk of work mistakes due to setup work cannot be eliminated.

Setup time is almost zero!

Yamaha’s answer to user’s needs:
Proposal of linear conveyor module (LCMR200/LCM100)
- Stop position is freely set or changed by the program.
- Setup work is not needed.
- Jigs can be made common.(Reduction of manufacturing and management costs)

Setup time is reduced 16 hours (2 days) per month!
<Example> Time required for setup work (Factory operation hours: 8 hours/day, 20 days operation)

Full automation by improving the setup work using the LCM and reading the QR code

Small motor manufacturer
People in charge of equipment design
“Zero setup” that is long standing subject is achieved.
Until now, we have been focusing on improving the product model change work in order to operate the multi-product model production efficiently.
As a result, we were able to reduce the work time by 50%, from 10 minutes to 5 minutes, and we have been introducing the effect of the improvement to our customers when they visit our factory.
However, even though we were able to reduce the work time, it was not efficient that five-minute work occurs several times a day, and we had to prioritize the production of product models with large production volume and devise the production such as collective production in order not to decrease the operating rate.
We considered Yamaha Motor's LCM this time based on the expectation that we would like to further increase the operating rate.
Since the stop position of the LCM can be changed by the program, "no setup work" has been achieved and the expected effect has been obtained.
In addition, the next equipment also uses the LCM and a mechanism to read the QR code of the product is installed on the input side of the equipment. As a result, the operation from the touch panel is stopped.
So, we can achieve the full automation. The operating rate is increased dramatically and there is no need to change the product model. So, we do not mind receiving small lot orders nowadays.
LCM and conventional conveyor system
(Comparison with conventional method)
Changing the stop position


- 1.
- 3-axis robot is required to change the work position. So, the equipment size becomes large.
- 2.
- Stopper position change work occurs and man-hour is needed.


- 1.
- LCM is responsible for one axis of the robot to change the work position, so a two-axis robot is enough. Therefore, the equipment required can be reduced.
- 2.
- Stop position is freely set or changed by the numeric value.
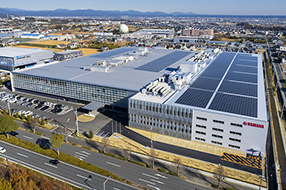
Robotics Business Unit
Sales & Marketing Section
FA Sales & Marketing Division
127 Toyooka, Chūō-ku, Hamamatsu, Shizuoka 433-8103, Japan
Telephone +81-53-525-8350 /
Facsimile +81-53-525-8378