The number of workers who pack baked sweets into boxes needs to be reduced
Process that has required 8 workers conventionally is now operated by 1 worker!

User:
Process that packs wrapped baked sweets is automated to achieve labor-saving.

Background of target
- The number of required workers varies depending on the sweets packing quantity
- Workers need to be secured according to the maximum packing quantity
- Workers are difficult to be secured due to the nature of the region
- Human errors also occur
With conventional system…
Difficult to secure and adjust workers
- Up to 8 workers are required
- Labor cost increases
- There are excess workers when the lot with a small packing quantity is processed

Solved by SCARA & Vision & Linear conveyor (LCM)

Yamaha's answer to the user's needs:
- LCM supplies boxes to packing positions for baked sweets
- SCARA robot packs baked sweets in supplied boxes
- Changing the LCM stop position supports changes in number of squares in the box

Process that has required 8 workers conventionally is now operated by 1 worker! A drastic reduction of labor cost is also achieved

<Improvement effect>

- Automation achieves labor-savings of 7 workers per line.
- As 1 worker/line is achieved, 3 work shifts are used to make a 24-hour operation possible.
- More production capability is created by 24-hour operation. If the line is stopped, this loss can be recovered by increasing the production quantity after that.
Labor-saving and stable production even during busy season are achieved.
24-hour operation is also possible.

Sweets manufacturer
People in charge of production engineering
Free from the worries of a labor shortage. Furthermore, productivity improvement and stable quality are achieved.
We considered automation for the first time. When we visited the websites of various manufacturers for the introduction of robots, we were attracted by the wide variety of YAMAHA's lineup.
This lineup includes from small actuators to Cartesian, SCARA, and vertically articulated robots, as well as vision systems and conveyor systems. So, we thought that YAMAHA would propose systems suitable for various cases.
We are a long-established baked sweets manufacturer that has been in business for 100 years. Thanks to this, the demand has increased year by year and we have been suffering from chronic labor shortages.
In the process that packs wrapped sweets in boxes, each worker packs one type of baked sweets in boxes, so the number of required workers may vary depending on the packing quantity.
Therefore, there was a waste because it was necessary to arrange the workers according to the largest packing quantity.
When we consulted with YAMAHA about this issue, they suggested that automation using robots could operate the process with only one worker instead of eight workers that were previously required for this process.
We found that when we can reduce the number of workers to one, the hurdle for shift work lowers dramatically, and we can perform stable production even during the busy season that occurs multiple times a year.
The robots were introduced for the purpose of labor savings, but we are glad that it has improved productivity, reduced costs, and reduced human errors resulting in stable quality that is better than we expected.
Thanks to YAMAHA, it seems that we can continue to preserve our history and tradition, incorporate changes of the new era, and provide even more delicious baked sweets to our customers.
Functional description and merit of YK-XE

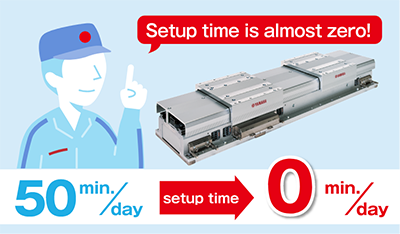
- Setup time is almost zero!
- Manufacturing products of multiple models in small lots without lowering the operating ratio
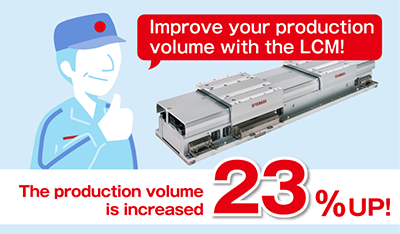
- The production volume is increased by approx. 23%.
- Increasing productivity per line for cost reduction.
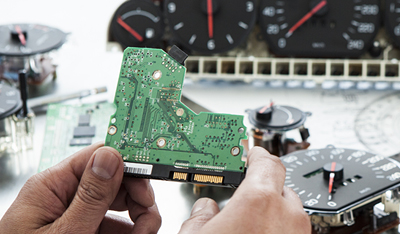
- Reduce setup time by 80%.
- Why does it take surprisingly short time to build up a robot vision system?
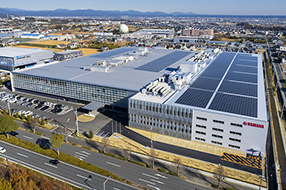
Robotics Business Unit
Sales & Marketing Section
FA Sales & Marketing Division
127 Toyooka, Chūō-ku, Hamamatsu, Shizuoka 433-8103, Japan
Telephone +81-53-525-8350 /
Facsimile +81-53-525-8378