Increasing productivity per line for cost reduction
The production volume is increased by approx. 23%. Cost of jigs reduced

User:
Need equipment with improved productivity

Possible options
- Increase the number of production line
- Reduce processing time
- Increase transfer speed between work stations
- Optimize operation by reducing frequent short line stops
Ordinary upgrade options:
Productivity improvement is limited due to long transfer time between work stations
- Carriage positioning time at each work station with stopper and pneumatic cylinder
- Buffer is required between work stations
- Frequent short line stops resulting from numbers of sensors required in line

High speed transfer and high precision positioning of LCM

• Repeatability: +/-5 μm (single slider)
* The operating time is calculated when the tolerance is +/-0.005 mm.
As the tolerance is increased, the operating time is shortened.
Yamaha’s answer to user’s needs:
- Reduction of transfer time by high speed LCM
- Eliminates buffer with reduced transfer time
- High precision positioning by absolute point data entry


The production volume is increased by approx. 23%. Cost of jigs reduced
<Example> Estimation based on 8 operation hours per day and operating ratio of 100%.

Manufacture cost is greatly reduced by increasing the production volume.

Automotive parts manufacturer
People in charge of production engineering
Both tact time and production time percentage are improved and production volume has exceeded the target.
In the past, in order to increase the production volume, we have done several KAIZEN actions focus-ing on shortening production time and increasing production percentage. The result was somewhat successful, however, by reducing the operation time, frequency of short line stops was not reduced and production volume was not increased as expected. Then I learned LCM of Yamaha at an exhibi-tion and saw some potential in it for increasing production volume. So we started an evaluation. Our feasibility study on LCM concluded that a reasonable ROI is expected so, we made a decision and started designing production line with LCM. Once the operation started we saw substantial reduction of transfer time and number of in-process workpiece which met our target. From the reduction of transfer time, we no longer needed to squeeze assembly cycle time of robot operation. As a result, frequency of short line stops by transfer error has been greatly reduced and that assembly line has become a model line in our plant. LCM greatly improved the production rate of the line and as a result the production volume has exceeded our original target. As a staff in charge, I believe choosing LCM was a right decision.
LCM and conventional conveyor system (Comparison with conventional method)




Case Study PDF
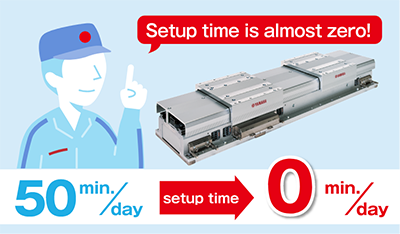
- Setup time is almost zero!
- Manufacturing products of multiple models in small lots without lowering the operating ratio
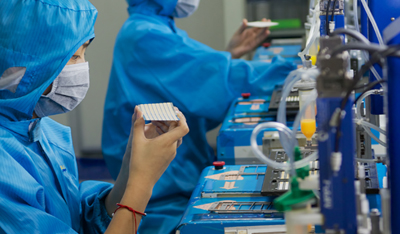
- Shorten takt time by 2 seconds!
- Selection of linear conveyors that defy conventional wisdom for lines.
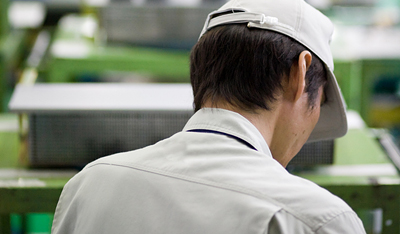
- Shorten equipment startup time to half!
- A brand new idea that replaces index tables
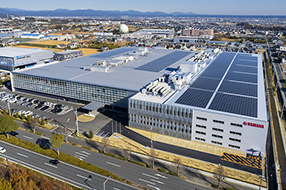
Robotics Business Unit
Sales & Marketing Section
FA Sales & Marketing Division
127 Toyooka, Chūō-ku, Hamamatsu, Shizuoka 433-8103, Japan
Telephone +81-53-525-8350 /
Facsimile +81-53-525-8378