Single axis robot positioner EP-01
Hurdle to introduce industrial Ethernet is lowered. Robot positioner dedicated for less expensive and easy-to-use Robonity series “ABAS/AGXS/ABAR”.
Specifications
Item | EP-01 | ||
---|---|---|---|
Basic specifications | Driver model | EP-01-A10 | EP-01-A30 |
Number of controllable axes | Single-axis | ||
Controllable robots | Single-axis robot Robonity series ABAS / AGXS | ||
Power capacity | 420 VA | 1600 VA | |
Dimensions | W 40 × H 150 × D 130 mm | W 55 × H 150 × D 130 mm | |
Weight | Approx. 0.6 kg | Approx. 1 kg | |
Input power supply | Control power supply | Single phase AC200 to 230V +/-10% 50/60Hz | |
Motor power supply | Single phase AC200 to 230V +/-10% 50/60Hz | ||
Axis control | Control method | Closed loop vector control method | |
Operating method | I/O point tracing (Positioning operation by specifying point number) / Remote command | ||
Operation types | Positioning, merge-positioning, push, and jog operations | ||
Position detection method | Optical encoder, battery absolute encoder, or battery-less absolute encoder is selected. | ||
Resolution | 8,388,608 pulses/rev. | ||
Origin search method | Absolute | ||
Points | Number of points | 255 points | |
Point type setting | (1) Standard setting: Set speed and acceleration in percent of the respective maximum settings. (2) Custom setting: Set speed and acceleration in SI units. |
||
Point teaching method | Manual data input (coordinates input) , Teaching, Direct teaching | ||
External input/output | I/O interface | Selectable from the following: EtherNet/IPTM, PROFINET, EtherCAT, NPN, CC-Link | |
Input | Servo ON (SERVO), reset (RESET), start (START), interlock (/LOCK) origin search (ORG), teaching mode (TMODE), jog motion - (JOG-), jog motion + (JOG+), point number selection (PIN0 to PIN7) | ||
Output | Servo status (SRV-S), alarm (/ALM), operation end (END), operation in-progress (BUSY), control outputs (OUT0 to 3), point number output 0 to 7 (POUT0 to POUT7), feedback pulse output (A/B/Z) (option) | ||
External communications | Ethernet (In conformity with IEEE802.3 100BASE-TX, Applicable to Auto Negotiation) | ||
Power supply for brake | DC24V +/-10% 300mA (prepared by the customer) | ||
Safety circuit | Emergency stop input, main power input ready output, emergency stop contact output (1 system: When the HT2 is used.) | ||
Options | Handy terminal | HT2, HT2-D (with enable switch) | |
Support software for PC | EP-Manager | ||
General specifications | Operating temperature / Operating humidity | 0℃ to 40℃, 35% to 85%RH (non-condensing) | |
Storage temperature / Storage humidity | -10℃ to 65℃, 10% to 85%RH (non-condensing) | ||
Atmosphere | Indoor location not exposed to direct sunlight. No corrosive , flammable gases, oil mist, or dust particles | ||
Anti-vibration | All XYZ directions 10 to 57Hz unidirectional amplitude 0.075mm 57 to 150Hz 9.8m/s2 | ||
Protective functions | Position detection error, power module error, temperature error, overload, overvoltage, low voltage, excessive position deviation, overcurrent, motor current error | ||
Protective structure | IP20 |
Single axis robot positioner EP-01
Related contents
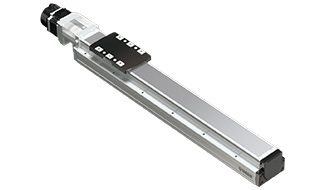
- Single axis robots Robonity Basic model Slider type ABAS
- Single-axis robots feature high rigidity, compact design, and low cost. A wide range of lead variations allows you to select optimal specifications.
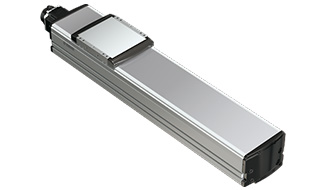
- Single axis robots Robonity Advanced model Slider type AGXS
- Single-axis robots feature high accuracy, high durability, and compliance with clean specifications as standard.
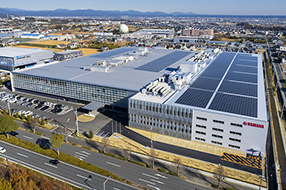
Robotics Business Unit
Sales & Marketing Section
FA Sales & Marketing Division
127 Toyooka, Chūō-ku, Hamamatsu, Shizuoka 433-8103, Japan
Telephone +81-53-525-8350 /
Facsimile +81-53-525-8378