Workpiece supply setup work needs to be made easy.
Use of vision feeder eliminates setup work! Workpiece jamming no longer occurs!

User:
Parts feeders require setup work, which takes a lot of work man-hours and there is a risk of a workpiece jamming.

Background of target
- Workers who can perform the setup work are limited.
→It is necessary to pass on skilled work techniques. - Product model change is performed on a flexible schedule.
→Production is planned and flexible production is not possible. - Inventory and management of various parts is required, which takes man-hours.
With conventional system...
- There is a difference in start-up time and adjustment results between those who are accustomed to doing the replacement work and those who are not.
- Not suitable for frequent product model changes.
- Man-hours are required to manage multiple bowls, attachments, and straight feeders.
- Workpiece jamming causes the equipment to stop.
- There is a difference between the test workpiece and actual workpiece, and workpieces cannot be supplied properly.
- Workpieces are likely to rub against each other and scratch.

Use of vision feeder eliminates setup work!
Workpiece jamming no longer occurs!

Yamaha's answer to the user's needs:
- There is no difference regardless of worker’s skill level.
- Stress associated with product model change is minimized and flexibility at production sites is improved.
- Owned parts and units are minimized and suggestions for management man-hours are also achieved.

It takes almost no time to perform the setup work, so many models can be manufactured in one day!


Parts supply problems such as setup work, adjustment work,
and workpiece jamming are eliminated.

Electronic component manufacturer
People in charge of production engineering
The startup period was significantly shortened when compared to the conventional system, and quality problems were also resolved by reducing workpiece scratches.
We, at Production Engineering, are studying and collecting information to increase the production volume of the equipment.
The reason we decided to consider Yamaha’s robot this time was to ask ourselves, “What is the cause of the drop in production volume?”. After analyzing the current situation, we came to the conclusion that the cause was short breakdown times in the parts supply, and the setup work associated with model change, and we decided to start investigating improvements of the setup work.
There are various types of setup work that occur at our company, but one of the challenges we faced was man-hours required to perform the setup work of the parts feeder to supply different parts depending on the product model. In addition, the bowl feeder has a risk of workpiece jamming, which may affect the production schedule due to short breakdown times if workpiece jamming occurs.
Challenges include problems with workers performing the setup work (work time, finishing adjustments, etc.), inability to respond to sudden changes in production schedules, storage of various parts required for the setup work, human intervention required for simple restoration work, and management.
The first time, we checked whether the workpiece could be seen using the robot vision, and then we actually prepared the hand and parts and checked the mounting accuracy. As a result, we were able to confirm in advance that it could be used on site without any problems. Vision is of course easy to use, but whereas with a conventional bowl feeder it takes two to three months from the initial meeting to actual testing, with the Vision + Vision Feeder, we were able to complete the demonstration within a few weeks of our request to Yamaha. We felt that this was a big advantage.
When we actually used the new system, we were able to smoothly change product models and short breakdown times due to workpiece jamming were eliminated. So, as a next step, we would like to try a line for small quantity and many kinds production.
Functional description and merit of RCXiVY2+
Multiple cameras achieve highly accurate mounting.
When workpieces are picked up and supplied, there are cases where the accuracy is insufficient for various reasons.
Yamaha’s robot vision RCXiVY2+ can connect multiple cameras, so by using the upward camera for position correction after workpiece pickup, it is possible to supply workpieces with higher precision.
The system can also recognize QR codes and barcodes, making it ideal for applications such as traceability management, workpiece sorting, sealing tracking change, etc., where the operation is changed according to the contents of the code.

[Example of application with three cameras]
① Workpiece supply position is corrected by the downward camera.
② Workpiece is positioned and angle is corrected by the upward camera.
③ Placement position is corrected by the downward camera.
Case Study PDF
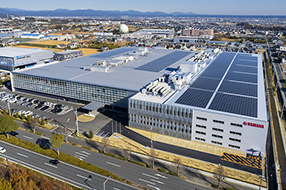
Robotics Business Unit
Sales & Marketing Section
FA Sales & Marketing Division
127 Toyooka, Chūō-ku, Hamamatsu, Shizuoka 433-8103, Japan
Telephone +81-53-525-8350 /
Facsimile +81-53-525-8378