We want to stably produce high-quality products while saving labor.
Labor saving and traceability are achieved by a SCARA robot.

User:
❶ The number of operators needs to be reduced.
❷ The quality requirements from end users need to be met.

Background of target
- It is difficult to maintain shift work personnel.
- Quality requirements from the end users are getting higher and higher.
- By storing products in the box, the products are damaging each other.
With conventional system…
Tracing is not possible when a product failure occurs.
[Process procedures]
- After the workpiece has been taken out by the take-out robot, it is dropped into the box by the conveyor.
- When the box is full of workpieces, a worker rearranges the workpieces from the box onto the pallet.
- Since the workpieces are stored in the box once, cavity numbers are unidentified and cannot be traced.

Labor saving and traceability are achieved by a SCARA robot.

Yamaha's answer to the user's needs:
By arranging the workpieces on the pallet with a SCARA robot, it is possible to keep a history of taken-out workpieces in order of cavity number.
[Two types of YAMAHA SCARA robot labor savings proposals]
- ① Low cost high performance model YK-XE
▶︎ System can be introduced at low cost. - ② Omni directional model YK-TW
▶︎ System can support large pallet sizes.

Hidden costs are reduced and quality is improved!
Conventionally, equipment costs were compared by multiplying personnel costs by the cost amortization period, but in reality, costs for personnel management and quality control could also be reduced.

Labor savings and traceability management are achieved at the same time.

Mold product manufacturer
People in charge of manufacturing engineering
By adopting a SCARA robot, labor savings and traceability management that could not be performed until now have been achieved at the same time.
We have a large number of injection molding machines and produce products by shift work. Recently, we have been experiencing difficulties in maintaining personnel due to the recent labor shortage, but we have managed to continue production.
The reason for considering labor saving was not to solve the labor shortage, but to meet the requirements of our customers. Although this should not have happened, defective products that had passed through the inspection process were released to the market, ,and we had to increase the severity of quality control as corrective actions. Therefore, we considered associating the cavity numbers when arranging workpieces on the pallet that was not possible until now.
The reason why we could not perform the management until now is that workpieces need to be stored in the box since one worker checks multiple injection molding machines. We thought that using a robot to perform the management could solve the labor saving and strengthening of quality control at the same time, so we consulted with YAMAHA, which sells inexpensive SCARA robots, and they worked with us on this project.
Thanks to YAMAHA's video report of the actual system evaluation, the reporting within the company went very smoothly.
We are currently evaluating the system after its introduction in the first few lines, but we would like to expand it to other lines in the future.
Functional description and merit of YK-XE

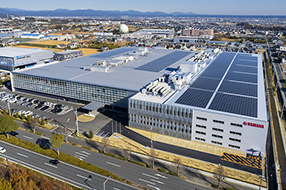
Robotics Business Unit
Sales & Marketing Section
FA Sales & Marketing Division
127 Toyooka, Chūō-ku, Hamamatsu, Shizuoka 433-8103, Japan
Telephone +81-53-525-8350 /
Facsimile +81-53-525-8378