Robot driver RDV-X / RDV-P
Introduces the robot driver RDV-X and RDV-P.
Specification
Model | RDV-X | RDV-P | ||||||
Driver model | RDV-X205 | RDV-X210 | RDV-X220 | RDV-P205 | RDV-P210 | RDV-P220 | RDV-P225 | |
Number of controllable axes | Single-axis | |||||||
Controllable robots | Single-axis robot FLIP-X | Linear motor single-axis robot PHASER | ||||||
Basic specifications | ||||||||
---|---|---|---|---|---|---|---|---|
Capacity of the connected motor | 200V 100W or less | 200V 200W or less | 200V 600W or less | 200V 100W or less | 200V 200W or less | 200V 400W or less | 200V 750W or less | |
Maximum power consumption | 0.3kVA | 0.5kVA | 0.9kVA | 0.3kVA | 0.5kVA | 0.9kVA | 1.3kVA | |
Dimensions | W40×H160×D140mm | W40×H160× D170mm |
W40×H160×D140mm | W40×H160× D170mm |
W55×H160× D170mm |
|||
Weight | 0.7kg | 1.1kg | 0.7kg | 1.1kg | 1.2kg | |||
Input power supply | Control power supply | Single phase 200 to 230V +10%, -15%, 50/60Hz +/-5% | ||||||
Motor power supply | Single phase / 3-phase 200 to 230V +10%, -15%, 50/60Hz +/-5% | |||||||
Axis control | ||||||||
Position detection method | Resolver | Magnetic linear scale | ||||||
Control system | Sine-wave PWM (pulse width modulation) | |||||||
Control mode | Position control | |||||||
Maximum speed Note 1 | 5000rpm | 3.0m/s | ||||||
Input/output related function | ||||||||
Position command input | Line driver signal (2M pps or less) (1) Forward pulse + reverse pulse (2) Sign pulse + Command pulse (3) 90-degree phase difference 2-phase pulse command One of (1) to (3) is selectable. | |||||||
Input signal | 24V DC contact point signal input (usable for sink/source) (24V DC power supply incorporated) (1) Servo ON (2) Alarm reset (3) Torque limit (4) Forward overtravel (5) Reverse overtravel (6) Origin sensorNote 3 (7) Return-to-origin (8) Pulse train input enable (9) Deviation counter clear |
|||||||
Output signal | Open collector signal output (usable for sink/source) (1) Servo ready (2) Alarm (3) Positioning completed (4) Return-to-origin complete |
|||||||
Relay output signal | Braking cancel signal (24V 375mA) | - | ||||||
Position output | Phase A, B signal output: Line driver signal output Phase Z signal output: Line driver signal output / open collector signal output N/8192 (N=1 to 8191), 1/N (N=1 to 64) or 2/N (N=3 to 64) |
|||||||
Monitor output | Selectable items: 2ch, 0 to +/-5V voltage output, speed detection value, torque command, etc. | |||||||
Internal function | ||||||||
Display | 5-digit number indicator, Control power LED | |||||||
External operator | PC software "RDV-Manager" monitoring function, parameter setting function, operation tracing function, trial operation function, etc. USB2.0 is used. Windows Vista / 7 / 8 / 8.1 personal computer can be connected. |
|||||||
Regenerative braking circuit | Included (but without braking resistor) | |||||||
Dynamic brake Note 4 | Included (Operation conditions can be set.) (No DB resistor, connection: 2-phase short circuit) | Included (Operation conditions can be set.) (with DB resistor, connection: 2-phase short circuit) | ||||||
Protective function Note 2 |
Semi-enclosure type (IP20) | |||||||
Protective functions | Over-current, overload, braking resistor overload, main circuit overvoltage, memory error, etc. | |||||||
Options | ||||||||
Support software for PC | RDV-Manager | |||||||
General specifications | ||||||||
Operating temperature | 0°C to +55°C | |||||||
Storage temperatureNote 5 |
-10°C to +70°C | |||||||
Operating humidity | 20% to 90%RH (non-condensing) | |||||||
VibrationNote 6 | 5.9m/s2(0.6G) 10 to 55Hz |
Note 1. These data are parameters and calculation range in controlling the robot driver and do not indicate the capacity of the robot at the maximum speed.
Note 2. JIS C 0920 (IEC60529) is used as the base for the protection method.
Note 3. GXL-8FB (made by SUNX) or FL7M-1P5B6-Z (made by YAMATAKE) is used for the origin sensor. The power consumption of the origin sensor is 15mA or less (at open output) and only 1 unit of the origin sensor is connected to each robot driver. (future specification)
Note 4. Use the dynamic brake for emergency stop. Note that the braking may be less effective depending on the robot model.
Note 5. The storage temperature is the temperature in the non-energized state including transportation.
Note 6. The JIS C 60068-2-6:2010 (IEC 60068-2-6:2007) test method is uses as the base.
Robot driver RDV-X / RDV-P
Related contents
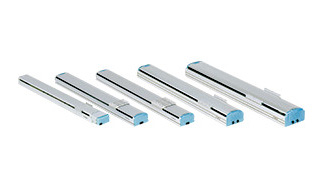
- Single axis robots FLIP-X Series (Electric slider)
- FLIP-X series include many models of 6types and 29variations for a wide range of applications.
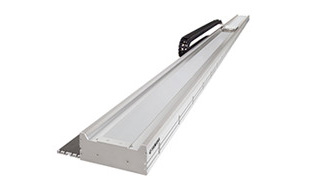
- Linear motor single axis robots
- Linear motor single-axis robots, PHASER series, utilizing the features of both the shaft type and flat type.
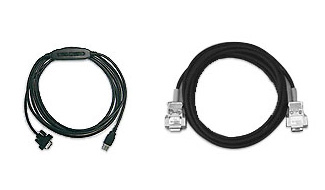
- Cable
- Dimensional diagrams and model numbers of the robot cables, cable terminals, and connectors are available.
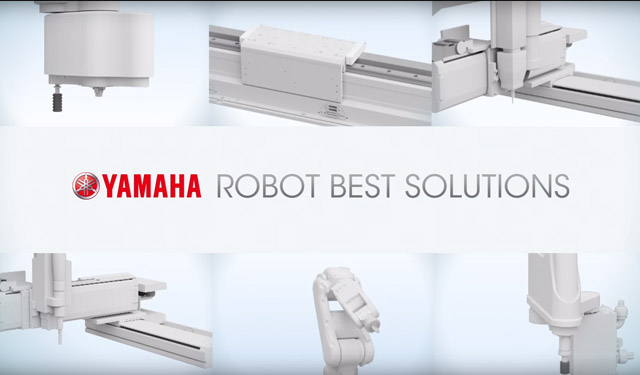
- Robot Movie Channel
- Yamaha Motor Robot Official Channel
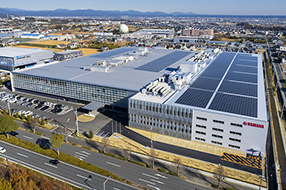
Robotics Business Unit
Sales & Marketing Section
FA Sales & Marketing Division
127 Toyooka, Chūō-ku, Hamamatsu, Shizuoka 433-8103, Japan
Telephone +81-53-525-8350 /
Facsimile +81-53-525-8378