Controllers Features & Benefits
Setting the parameters is simple and setting acceleration/deceleration is easy.
Feature
01Optimal setup
Setting the parameters is simple
Robot controllers are designed in-house for YAMAHA robots. Optimal values for servo parameters required for operating the robot such as gain are stored beforehand in the robot.
Setting acceleration/deceleration is easy
The acceleration/deceleration is a critical factor in determining the machine service life. Setting the acceleration too high will shorten the machine service life, while setting it too low will prevent effective use of motor power and lower the tact time. The acceleration/deceleration on YAMAHA robot controllers is determined to a fine degree for each model by the payload. By simply entering payload parameters, acceleration and deceleration rates will be automatically optimised to provide suffiecent robot service life and motor performance. Detailed robot knowledge from YAMAHA is what makes this possible. Moreover, SCARA robots are also equipped with zone control function that constantly delivers maximum performance that takes into account fluctuations in inertia due to the state of the arm (folded/extended). (Note. On pulse train input types the acceleration/deceleration must be set by the customer.)
02Diverse command methods
YAMAHA controllers allow the user to select from an ample array of control methods including programming, point trace and pulse train to match the customer's application.
Program entry
YAMAHA SRC language <examples> | |
---|---|
MOVA 1 , 100 | Move to point No. 1 at 100% of speed. |
DO 1 , 1 | Turn general-purpose output No. 1 to ON. |
WAIT 2 , 1 | Wait until general purpose input No. 2 turns ON. |
YAMAHA BASIC language <examples> | |
---|---|
IF DO(10)=1 THEN *END | Jump to *END if general-purpose input No. 10 is ON. If not ON, then proceed to next line. |
MOVE P, P2, STOPON DI(1) =1 | Move to point No. 2. Stop if general-purpose input No. 1 is ON during movement. |
WAIT ARM | Wait until robot arm operation ends. |
P3=WHERE | Write the current position in point No. 3. |
*END: | Defines the label named "END". |
HOLD | Pause the program. |
Single-axis robot controllers use the YAMAHA SRC language Note which is simple yet contains all required functions such as I/O outputs and conditional branching, etc. The multi-axis controller RCX series uses the YAMAHA BASIC language capable of more sophisticated programs and includes all types of arithmetic computations, flexible setting of variables and various conditional branching, etc. Both are easy to use robot language conforming to BASIC. These match all manner of needs from simple beginning operations to sophisticated expert user tasks.
- Note.
- The 2-axis controller DRCX also uses YAMAHA SRC language.
I/O point trace
The host device specified a point No. in binary and the robot moves to that point No. when a start signal is input. The controller can operate just by teaching the point data and does not need a program.
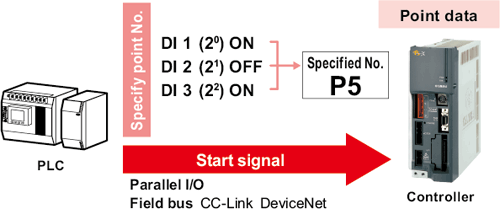
Remote command
This uses CC-Link or DeviceNet word functions to issue various data or commands to the robot. It makes full use of word function expandability ranging from simple operation instructions to writing of point data and other sophisticated instructions and allows fully and flexibly using robot controller functions from a host device.
- Note.
- These functions are operable when selecting the option network board.
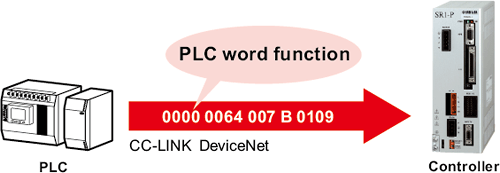
Pulse train
A pulse train sent from the positioning unit controls the robot. The controller does not have to handle programs or point data. This control method is convenient when one wants to concentrate control in a host or upstream device.
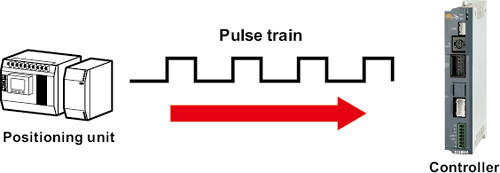
Online instructions
A PC connected via RS232C or Ethernet Note can be used to issue various commands and data directly to the robot controller or receive data and status. All operations performed from a teaching pendant can be executed from a PC.
- Note.
- Ethernet is operable by selecting the option network board.
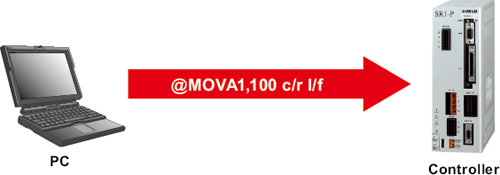
03Multi-functions and expandability
- Multi-axis controllers support up to 10,000 points, and single-axis controllers up to 1,000 points (255 points on the TS series). Up to 100 programs can be made on either type controller.
- Supports various field networks including CC-Link, DeviceNet, Profibus, Ethernet, EtherNet/IPNote.
- Note.
- Some models do not support all networks.
- The TS series, RD series, SR1 series, and RCX series utilize a dual power supply system where the control power supply and (main) power supply are separate.
- Controllers support CE markings for EU (European) safety standards and so can also be used with confidence overseas. The TS series (except for TS-S), SR1 series, and RCX series can support safety category 4.
Select the page for each controller from the navigation bar on the left for more information on each controller.
Controller
Related contents
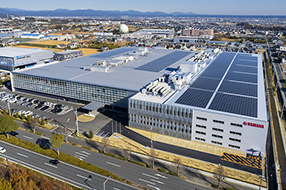
Robotics Business Unit
Sales & Marketing Section
FA Sales & Marketing Division
127 Toyooka, Chūō-ku, Hamamatsu, Shizuoka 433-8103, Japan
Telephone +81-53-525-8350 /
Facsimile +81-53-525-8378