Intelligent SMD Storage System YST15 Feature
An intelligent automated storage system that does highly efficient component loading / unloading and refills by Direct Handling and Reel Components Batch loading / unloading
Direct handling for highly efficient Loading & Unloading
Direct handling brings a whole new level of efficiency to tasks
Directly unloads just each required reel. No dedicated storage box required and work efficiency greatly improved.
YST15 [Direct handling]
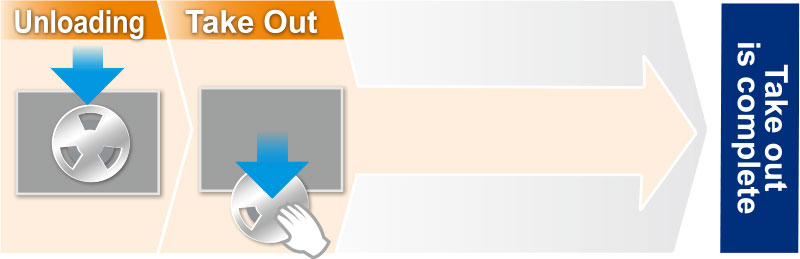
Box type
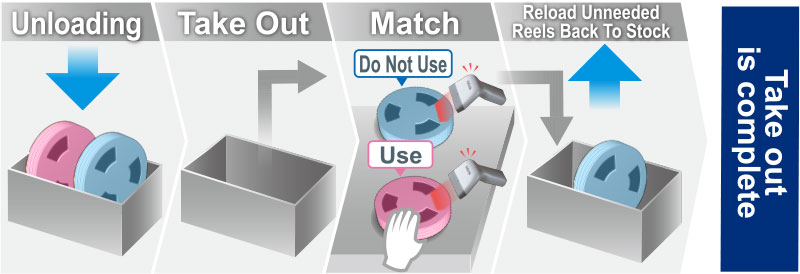
Only the reels you need are unloaded.

Direct Handling unloads just the reels you need. Compared to systems that unload several unneeded reels in a dedicated box there is no need to return unneeded reels so efficient component unloading is achieved.
No need for component verification when taking out.
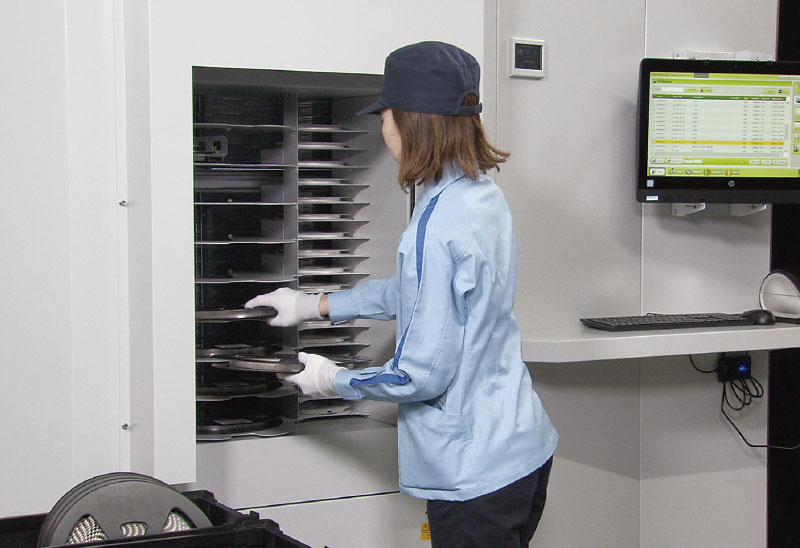
Only unloads the reels that are needed and does not unload the reels that are not needed, so there is no need to verify them when you taking out the reels. This reduces the operator's workload.
Eliminates the cost of preparing storage boxes and space to store them.
Direct handling eliminates the dedicated storage boxes for reel components. (Except for some components) This realizes cost savings and there is no need to save the box storage space.
Batch Loading / Handling of up to 33 reels
Effectively use of waiting time during loading and unloading
Multiple reels can be loaded or unloaded at the same time. This means that this time can be effectively used for other tasks while YST15 is loading or unloading components compared to the automated storage where loading just 1 reel at a time.
Simultaneously unloads different size reels
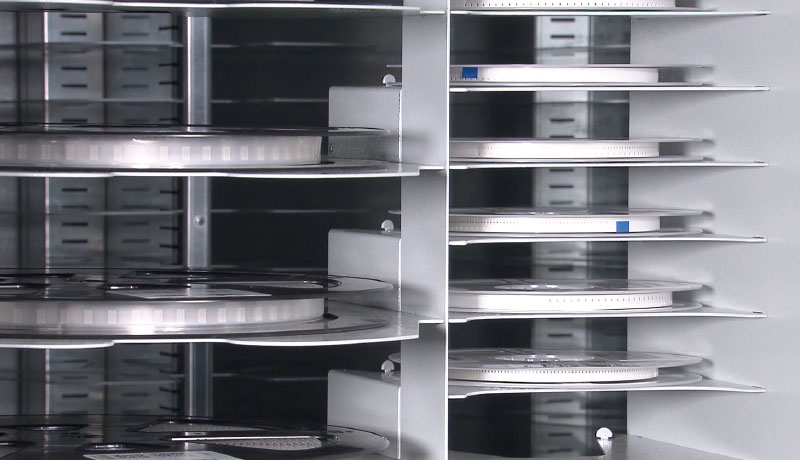
The reels are directly gripped during direct handling so that even different size reels can be unloaded. YST15 handles many different component types so the unloading operation is more streamlined and efficient.
Eguipped with built-in barcode reader as a standard
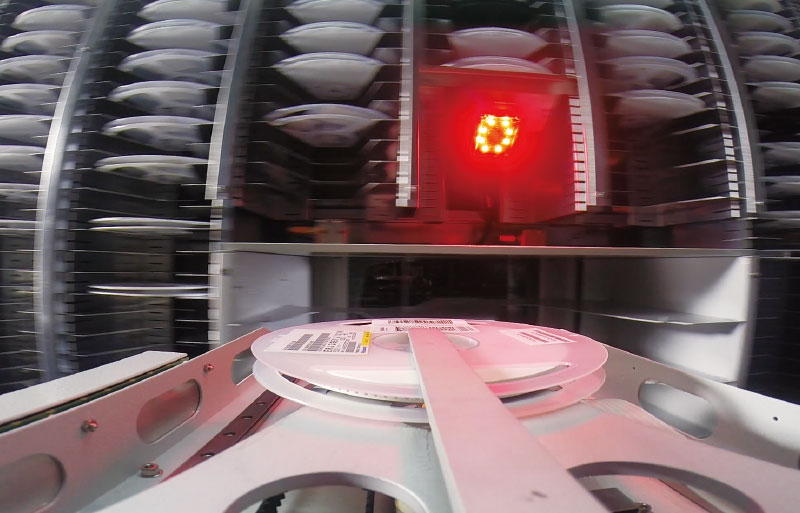
The component storage internal barcode reader automatically scans the barcodes on all reels during batch loading. This prevents read-out errors caused by human error and eliminates the scanning process, making the receiving process more efficient.
Mounter Collaboration functions support component setup & refill.
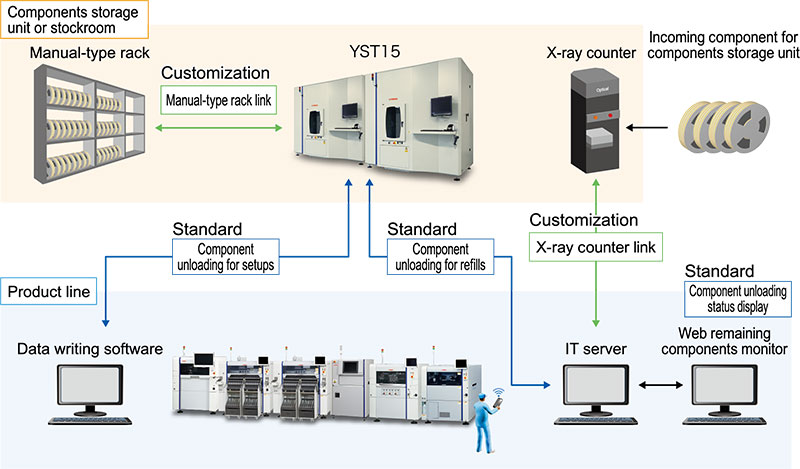
Component unloading for refills
After receiving a mounter component remaining component warning, the next required components can be automatically unloaded from stock. The components are placed on the fast extraction shelf in priority over other components, allowing the operator to take them immediately. In addition, components that will be needed in a certain period of time can be unloaded in batches based on the information on the number of components remaining on the mounter. This operation is highly compatible with Auto Loading Feeder and greatly improves efficiency when refilling the mounter with components.
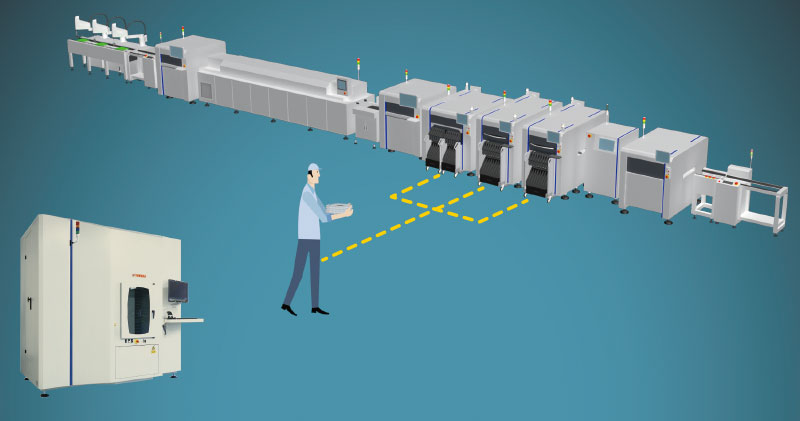
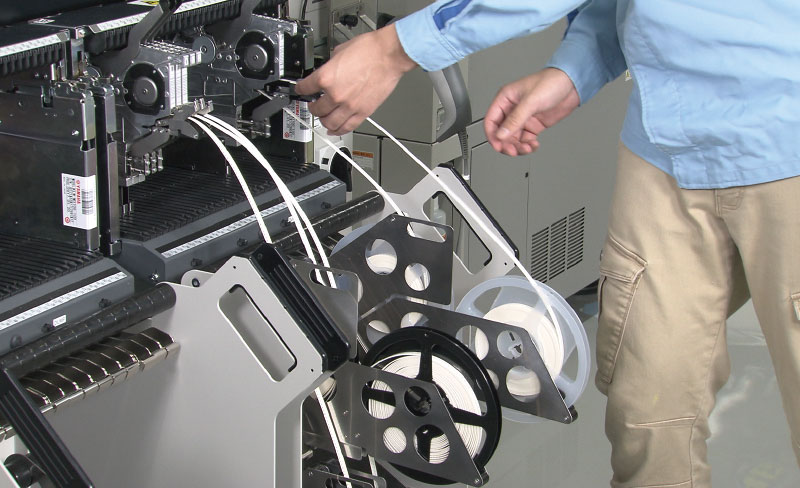
Component unloading for Setups
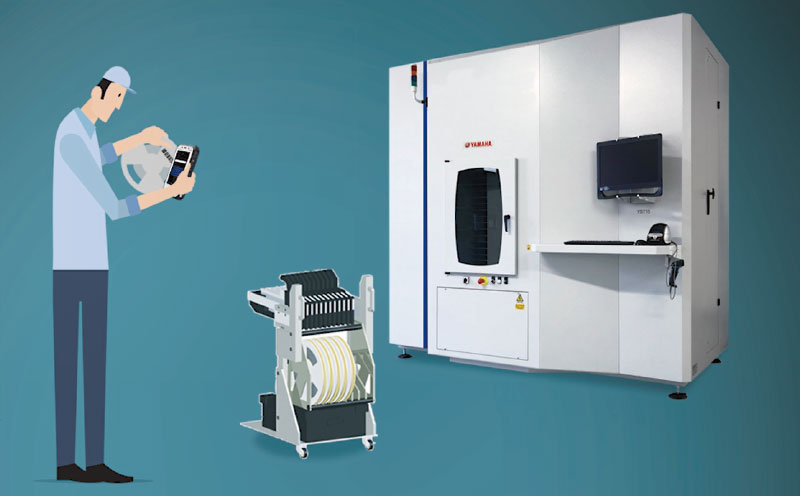
Components needed for the setup are automatically unloaded from the setup list created on the Yamaha Offline software. The number of feeders to place on the Yamaha feeder carriage (holds 32 feeders/8mm width) can all be unloaded in one batch. This helps made efficient setups by unloading components in specified carriage units. Lists can also be imported from other systems.
Component unloading status display
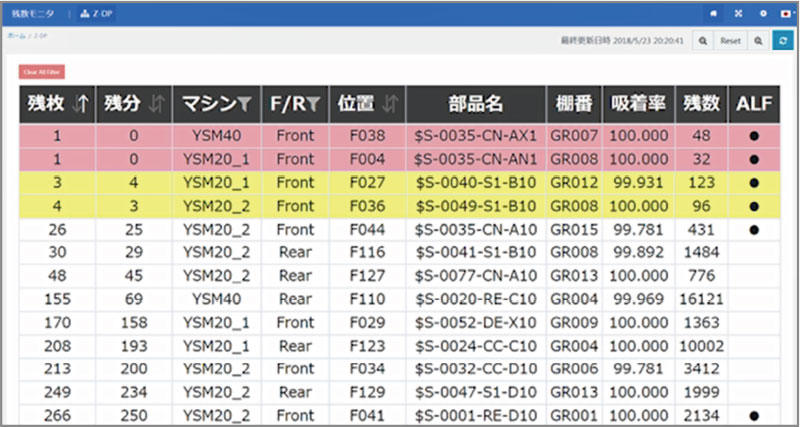
The status of components required during production, including the status of YST15 unloading and the status of reservations, are displayed on the monitor of the web browser. This information is displayed on a large-size monitor or tablets so the component pickup and collection tasks can be efficiently performed at the required timing.
Effective management of environment for correctly storing different components
Humidity Management
A humidity control function is installed as a standard feature, which can also be used for components that require moisture-proof control. The dehumidifiers operate in turns 24 hours a day to dehumidify the inside of the storage unit.
Time Limit Management
The YST15 also manages the usage expiration dates of stored components. This feature limits unloading expired components to prevent defects from occurring due to mistakenly using those components.
Temperature Monitoring
This feature monitors the temperature within the component storage unit and confirms whether the components can be stored at the correct temperature. This supports quality maintenance.
Unloading Priority Settings
These set the first-in, first-out priorities for materials including priority unloading by manufacturing date and priority unloading for currently used components.
Related contents
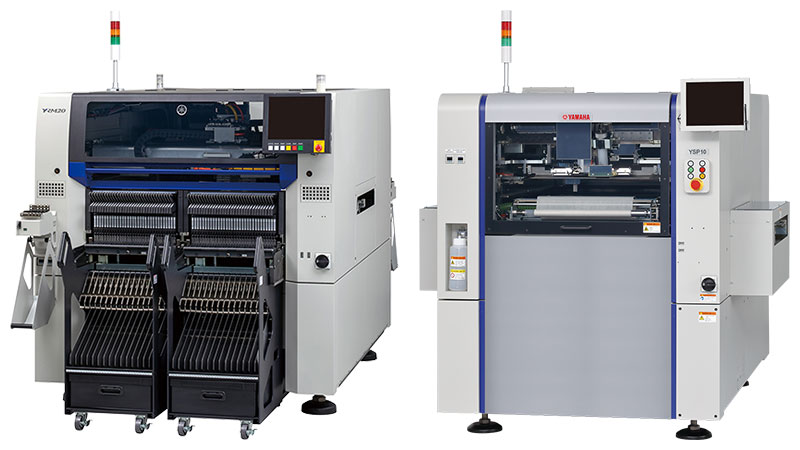
- Product
- Introduce our product lineup, including surface mounters, solder printers, and visual inspection machines.
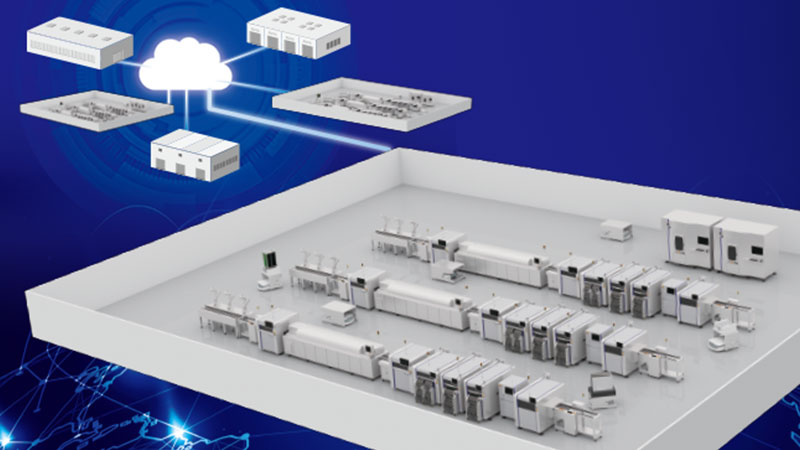
- Showroom
- Find and explore SMT Smart Showroom or Virtual Showroom
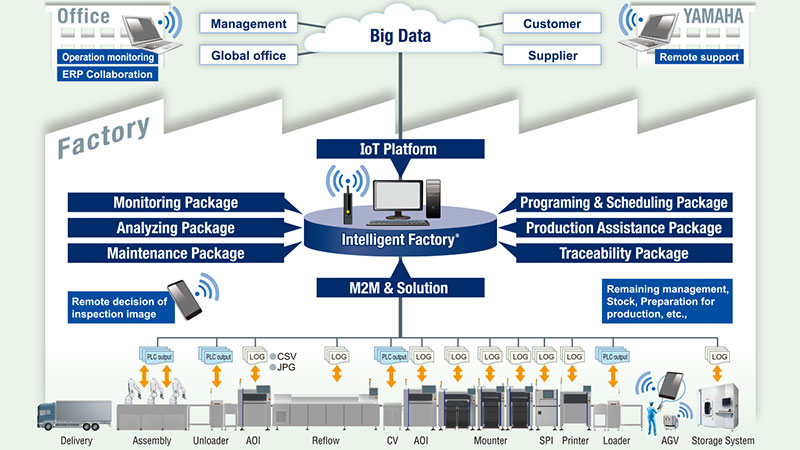
- Intelligent Factory
- IoT/M2M Integration system - System allows linking our SMT machines to equipment made by other companies and give all-around high productivity in the mounting process.