Compact High-Speed Modular YRM10 Feature
Packed with the technology of the YRM series’ high-end systems. “Just right” small, multi-purpose high-speed mounter
Outstanding cost efficiency
Supports diverse PCBs with one head, achieving great productivity
Features YR series’ high-speed multi-purpose inline head. Supports a wide range of components from super miniature chips to large 100 x 55 mm components without head replacement. Also realizes the high speed of 52,000 CPH, demonstrating great productivity with just one head.
High-speed multi-purpose in-line head
Achieves high-speed mounting of 52,000CPH (under our optimized conditions).
Also secures an accuracy of ±35μm (cpk≧1.0).

Scan camera
The head side features a component-recognition camera to identify components during transportation.
Shortest-route transportation from pickup to mounting, improving productivity.


High-quality production
Detects posture anomalies of components before mounting
The side view camera checks the posture of components before mounting and rejects factors that cause defects, for defect-free production.

Prevents defects from warped leads
Coplanarity checker detects QFP’s warped lead before mounting, preventing defects.


Accurately detects BGA ball missing
Side lighting meticulously detects missing BGA balls that cannot be detected with lighting from underneath.

Achieves steady pickup and mounting
The head can change speed momentarily during pickup and mounting to maintain production and steady quality.

Great usability
Slim and light feeder improves operability
Compact feeder weighing under 1kg, operable with one hand for better work efficiency.


Components can be supplied “anytime” with “no specific skills”
Remaining components monitor and Auto Loading Feeder are combined to supply components efficiently at any chosen timing, optimizing operators’ component-supply work.



Efficiently supplies tray components
YRM10 can feature the space-saving, cost-effective 15-magazine tray component feeder sATS15R.

Nozzle is automatically replaced, requiring no changeovers
The nozzle is automatically replaced according to the mounting PCB. The nozzle holder can be detached with just one touch, providing ease of maintenance and changeovers.


Easy maintenance
Nozzle is automatically cleaned and its condition is checked.
Blow station automatically cleans air channel. Nozzle vibration and exterior are automatically checked to see if there are any abnormalities. Enables production under consistently good equipment conditions.
Nozzle health check

Camera checks nozzle abnormality

Nozzle vibration is checked

Factors that cause defects are detected and eliminated in advance
Automatically identifies the cause of pickup errors and instructs improvements
Dashboard performs automatic analysis of what caused pickup errors. It suggests replacing problematic feeders and checking the nozzle to support maintenance and improvement for operators.

1 STOP SMART SOLUTION
High-efficiency, defect-free production, made possible as Yamaha is a manufacturer of inspectors, printers and mounters.
The target mounter will be automatically stopped if a defect is detected.
The mounter and AOI will be linked and the mounter in question will be instantly stopped if a defect is detected. Defect images are sent to mobile devices so that OK/NG decisions can be made remotely. Prevents continuous stream of defects, and quickly identifies the cause of defects.

All recognition images are automatically saved to identify the cause of defects.
Images of all components during pickup and mounting will be taken and automatically saved, significantly reducing the time taken to analyze the cause of defects.

Seamless automatic switching of production types for efficient multi-production.
Automatic change-over function automatically switches production program during production, to be ready to produce the next PCB.

Related contents
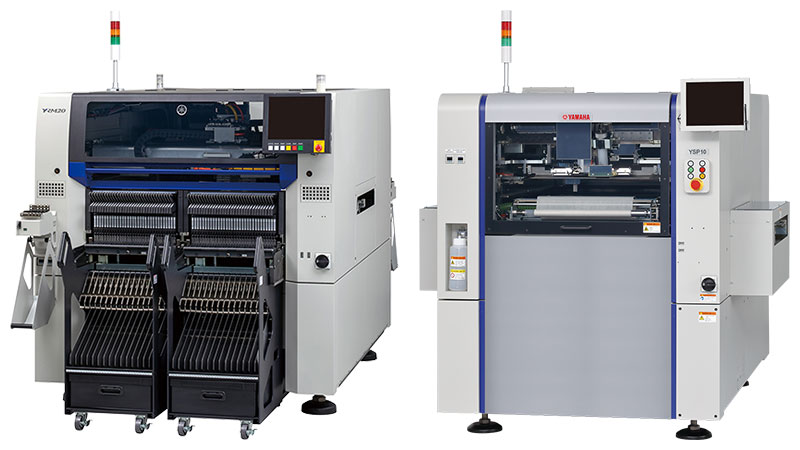
- Product
- Introduce our product lineup, including surface mounters, solder printers, and visual inspection machines.
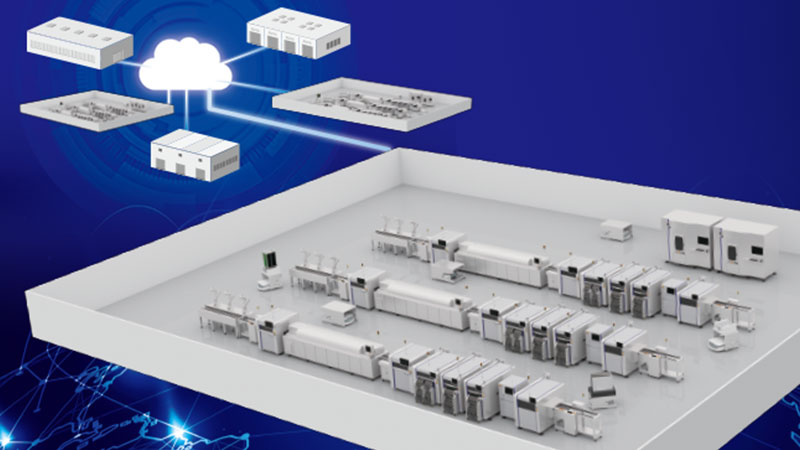
- Showroom
- Find and explore SMT Smart Showroom or Virtual Showroom
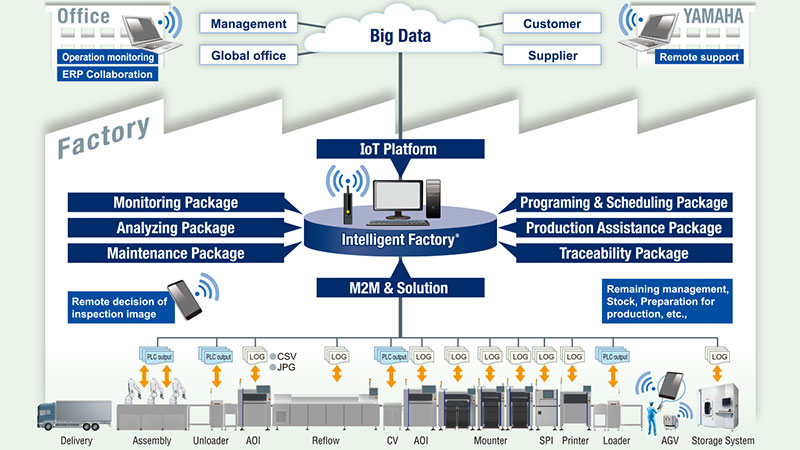
- Intelligent Factory
- IoT/M2M Integration system - System allows linking our SMT machines to equipment made by other companies and give all-around high productivity in the mounting process.