Initiatives for Motorcycles
Introducing Yamaha Motor’s initiatives to ensure motorcycle quality.
Quality Assurance Structure
In Yamaha Motor’s Motorcycle Business, we established an independent Quality Assurance Division in 2020 by consolidating the quality assurance functions in order to provide customers with higher-quality products. With this independence, the Quality Assurance Division aims to deliver products that earn the trust and confidence of our customers by working from the customer’s perspective to carry out quality assurance activities across all processes—including planning and development, manufacturing, procurement, and service—while coordinating with, monitoring, and providing checks and balances for the relevant divisions.
Ikki Tsuukan Assurance(One Consolidation Assurance) for Motorcycle Quality
At each key milestone, from product planning and concept through to the start of production, we confirm the progress and maturity level of each related division to establish a framework that ensures the continued creation of appealing products. This framework is referred to as “milestone management,” and it includes strict rules that prevent progression to the next stage if the criteria for each milestone are not met.
Furthermore, after production begins, we collect customer feedback and feed it back into the next planning and activities to create better products and services.
Vehicle Certification to Mass Production
In 2020, the Finished Vehicle Inspection Division was separated from the conventional Manufacturing Division, and in 2021, the Vehicle Certification Division was separated from the Development Division and transferred to the Quality Assurance Center. By clarifying the certification process and responsibilities, this system establishes a mechanism for confirming and guaranteeing the functions, safety, legal compliance, and marketability of completed vehicles from a customer-centric perspective.
Finished Vehicle Inspection
To ensure compliance with the laws and regulations of each country and our internal standards, we conduct full inspections before the shipment of finished vehicles. Finished vehicle inspectors are exclusively personnel who meet our internal standards for competency, and under strict management, they confirm not only functions, safety, and legal compliance but also product marketability, including exterior quality.
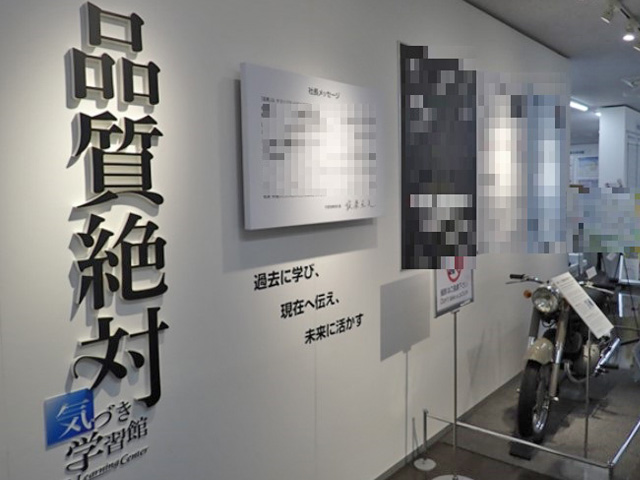
Vehicle Legal Compliance (COP: Conformity of Production)
For items requiring periodic sampling inspections as part of Vehicle Legal Compliance (COP: Conformity of Production), the Quality Assurance Division conducts tests to ensure compliance. We guarantee legal compliance by performing appropriate tests in accordance with strict rules.
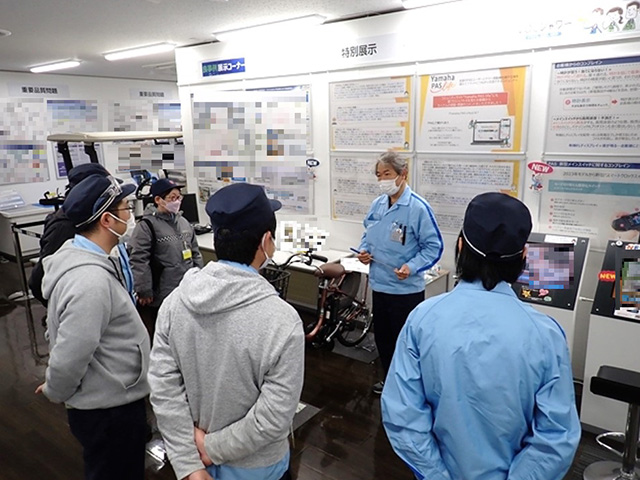
Collection and Analysis of Quality Information / Quality Improvement
We have established a system in which quality issues that arises in the market are registered in a database through the services of sales companies in Japan and overseas, allowing consolidation of information. The information is delivered to the development and production divisions as well as the procurement division (suppliers), and each division coordinates to determine the cause and implement countermeasures, while handling the issue appropriately for the customers and developing measures to prevent recurrence.
Response to serious defects such as recalls
We have established a system to quickly deliver information to management for discussion and decision-making in the event of a product-related accident or a problem that may infringe on laws and regulations. In case of its determined that market measures are necessary, we will promptly and reliably notify the authorities of the country where the incident or defect occurred according to its laws and regulations, then our dealers notify the users of the product that free repairs will be provided by direct mail, phone, announcement on the website, or other means.
Recall | Improvement measures | Service campaign | ||||
---|---|---|---|---|---|---|
Number of cases | Number of units | Number of cases | Number of units | Number of cases | Number of units | |
2022 | 4 | 19,447 | 2 | 2,594 | 1 | 9 |
2023 | 2 | 19,293 | 2 | 46,159 | 1 | 9,839 |
2024 | 5 | 497,751 | 0 | 0 | 1 | 41,659 |
Global Quality Initiatives
Our Motorcycle business aims to deliver products that provide safety and reliability to customers worldwide by realizing the same high level of quality globally. To achieve this, we are working to establish a system that enables manufacturing with the same level of quality assurance at all production sites around the world and to foster human resources with a high awareness of and skills in quality.
MC Quality Management System (MCQR: Motorcycle Quality Rule)
The MCQR (Motorcycle Quality Rule) is a Yamaha Group regulation based on ISO 9001 that incorporates Yamaha’s unique motorcycle quality management philosophy. All production sites, both in Japan and overseas, comply with the MCQR in carrying out quality assurance operations to achieve the same level of quality across all sites.
Global Quality Assurance Meetings
Bringing together quality members from production bases in various countries, these meetings are held multiple times each year according to specific themes. A wide range of quality-related topics are gathered, and discussions are held on challenges and concerns, information is exchanged, and examples of quality activities at each base are introduced. In addition to discussions in meeting rooms, host bases organize factory tours, and by emphasizing the location, situation, and objects and engaging in timely and frank communication, we foster collaboration among bases.
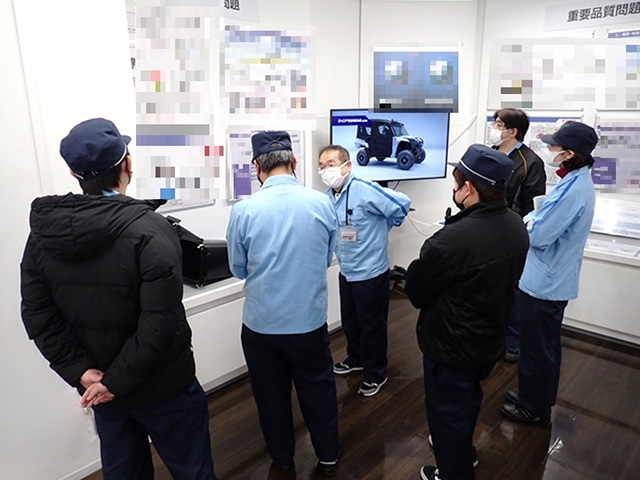
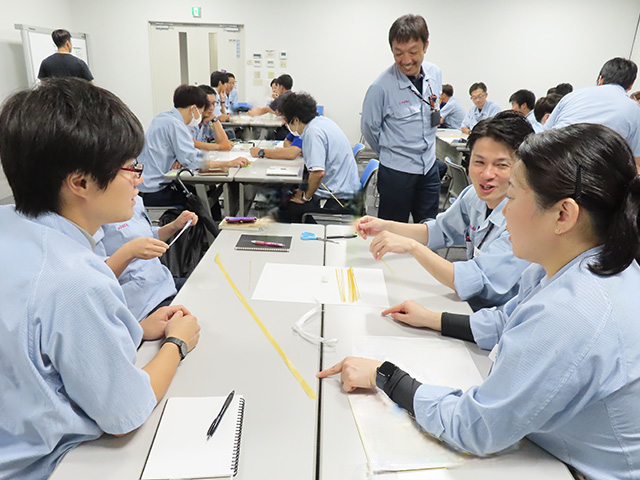
Overseas site support
At Yamaha Motor Co., Ltd., we are working to visualize and standardize inspection skills at our major production sites with the goal of achieving uniform quality across all sites.
Component Evaluation Lab Diagnosis
Yamaha Motor has established component evaluation labs at each production site to assess the quality of various parts and investigate problems. Since 2015, we have been conducting “Component evaluation Lab Diagnoses” with the aim of maintaining and enhancing the evaluation capabilities of these labs. In this initiative, members from the Quality Assurance Division at our headquarters visit overseas sites regularly to evaluate five key areas: evaluators, evaluation equipment, education systems, evaluation standards, and work process management. Based on the results of these diagnoses, we support skill development to enhance assessment capabilities, thereby contributing to manufacturing process improvements and the prompt resolution of quality issues through the effective use of inspection data.
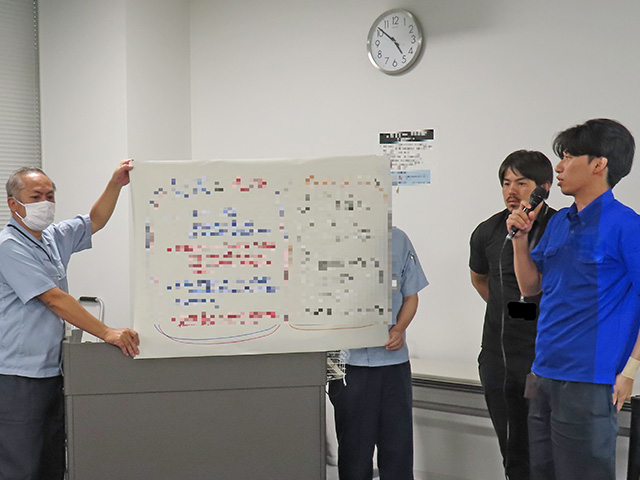
Finished Vehicle Inspector Training Program
In 2011, Yamaha Motor launched a qualification program for finished vehicle inspector trainers with the goal of enabling finished vehicle inspectors at all manufacturing sites to perform inspections at the “same level.”
A finished vehicle inspector trainers is someone certified to train and accredit finished vehicle inspectors. Trainers at each sites are responsible for maintaining, improving, and managing the competencies of the inspectors. This qualification is granted by the Quality Assurance Division at headquarters, which also regularly verifies whether the certified competencies are being maintained.
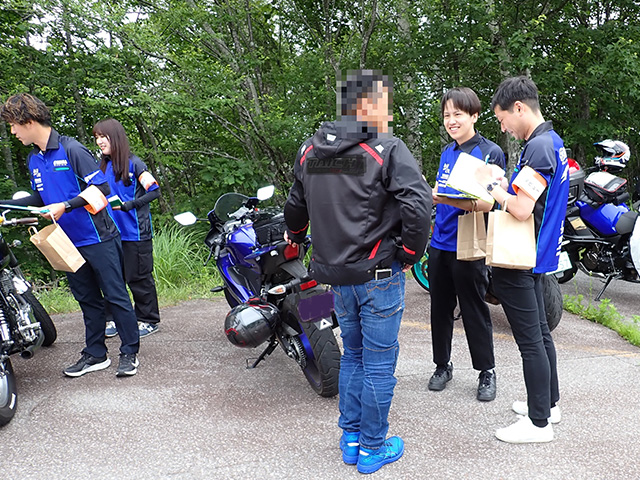
