“I take great pride in it,” states one of the inspectors when asked about the job. Then, after a brief pause, he confesses that “it is a pride born of an immensely heavy responsibility.” By the time a Yamaha outboard finally reaches the inspection site, it has already passed through the hands of numerous expert craftsmen. To confirm that no mistakes have been made along the way, the veteran inspectors here rely on their “sensors,” i.e., a sharp eye and a sensitive touch.
A Small Ocean in a Corner of the Factory
For a Yamaha outboard, the materials used for every component—down to each bolt—are carefully selected, precisely machined, and considerable time and effort expended to add extra touches throughout to make it that much stronger and that much more beautiful. Only after the countless parts and components that make up the outboard have been properly strengthened and refined in the hands of our many craftsmen do they reach the assembly factory. Here is where they are combined to deliver the performance and reliability for which they are renowned.
The official name of the facility is the Fukuroi South Factory, but those who work here proudly call it “the world’s best outboard assembly factory.” The factory’s total floor area is an expansive 37,768 m2 and its attractive white and blue exterior calls to mind whitecaps on a sea of blue.
In one corner of the factory is a series of water tanks designed to simulate the open sea, small “indoor oceans” where newly completed engines are given their final tests and checks. “Should an engine fail on the open water, it can lead directly to the boat being swept away in the current,” explains an inspector. “Putting an outboard likely to do that into the hands of our customers would be inexcusable.” Unsurprisingly, the stern mood at the worksite where the outboards are tested and undergo their final inspections seems to fill the air.
Large volumes of water are constantly circulated through the three high-capacity inspection tanks. Here, every outboard engine—without exception—gets its baptism in one of these tanks with a full-throttle test run to verify its performance and working condition before being shipped out to countries and waters around the world.
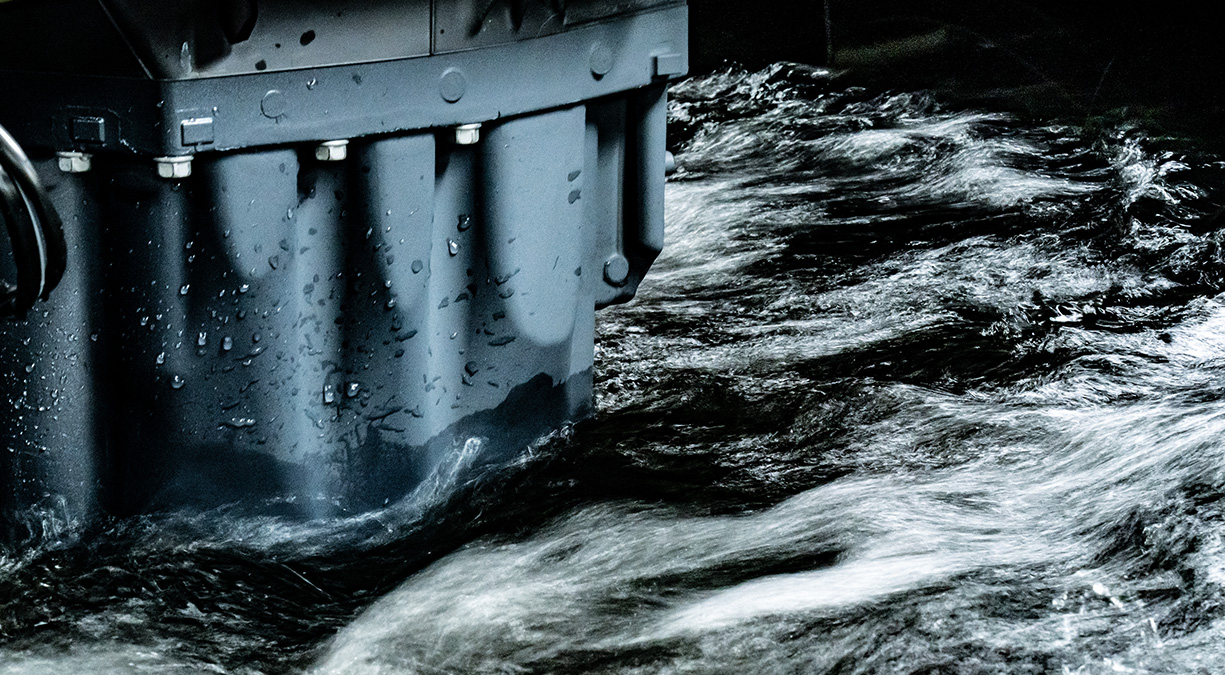
Dawn at a Quiet Harbor Before Shipment
It takes about 30 minutes to perform the full final inspection for a single outboard motor and more than 500 units are produced at this factory every day, so the inspection line never stops. Outboards stripped of their bodywork are transported via overhead conveyor hooks into the water without disruption.
The first stages of the inspection process are actually rather quiet. Automatic diagnostic equipment is used to check the electrical components and to confirm that the ECU is functioning properly. Once that is complete, the highly experienced inspectors mainly rely on their eyes as they run through an extensive checklist, verifying how well the engine fires up, restarts, how the oil pressure builds, idling stability, and more.
Internal combustion engines require fuel, air, and a spark in order to run. If even one of these is not being used or functioning correctly, the engine will shake or vibrate ever so slightly to the sides, alerting the inspector that something is wrong. Although this is a rare occurrence, it is precisely because it is so infrequent that the inspectors must be especially watchful.
In this engine break-in room, the engines are warmed up in preparation for the hard testing that awaits. After raising the outboard’s rpm enough to get their lubricating oil circulating fully, they are sent to the test cell beyond a heavy soundproof door.
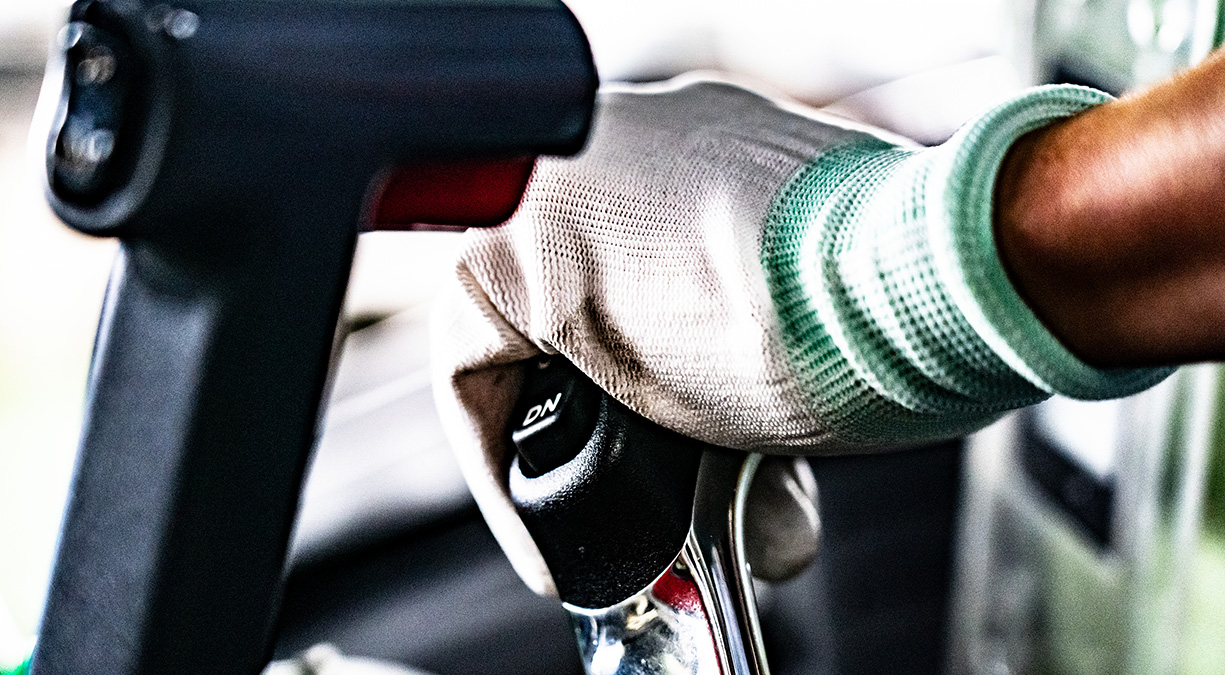
Senses Attuned to Yamaha’s Reliability Standards
During takeoff, a jet plane produces about 130 decibels. Inside the test cell, the walls are shaken by a similar level of noise and the inspectors here all wear noise-reducing earmuffs for protection. A high-horsepower outboard running at full throttle is a spectacle of sight and sound!
While closely observing the values shown on the measuring equipment, the inspector shines a flashlight on various locations of the outboard. He’s looking for oil or cooling system water leaks, bolts that might be loose, and other major issues on his checklist. At times like this, the inspector’s finely tuned senses are at their peak.
The inspectors here all receive special training and have an intuitive sense of how a properly manufactured outboard engine should run and behave. In other words, the inspector’s body itself is a precision measuring instrument, able to notice without fail if the outboard’s vibration and movements, sound, or even smell are not within Yamaha’s standards. But can an inspector really detect if a bolt is loose or if there is some other small problem when the engine is running at full throttle? “Actually, we can,” says one. “When you shine light on a properly assembled engine, it is just reflected back as-is. But a loose bolt will alter the way the light is reflected back, with the vibration making it flash irregularly. Although we’re only looking at a bolt, it’s the movement of the light that tells us that something’s not right.” For Yamaha’s outboard inspectors, there is a clear difference between merely “looking” and actually “seeing” something.
Like a chef preparing a delicious meal, the inspector’s keen sense of smell can also discern whether or not all the outboard’s ingredients are in the proper proportions. A good-running engine has a certain smell, just as there is also a particular smell when a fuel or oil leak is present, the smell of the water in the tank, lubricants, and metals, and the complex mix of them all together.
What about the engine’s sound? It too transmits its own distinct messages: a healthy engine sounds healthy, while an engine with an issue will not. These messages can range from the proper high-pitched hum within the engine’s rumble to atypical noises like a small rattling clank or even something that sounds amiss while the outboard is submerged in the water. “The type of noise and where it comes from on the engine helps us determine the problem,” the inspectors explain. Engines found to have defects are sent to a dedicated department for investigation into the cause, where their performance is again evaluated. By understanding what caused the problem, whether it was a part or a step in the production process, that feedback leads to production improvements. Repeating this process further builds the foundations for ever-higher reliability as well as customer trust in Yamaha’s outboards.Every engine is tested for performance at full throttle, during quick acceleration and deceleration, and repeated gearshifts. All the data acquired by the equipment employed to conduct this severe testing regimen is recorded and saved.
Once the inspection is over, units that have proven they have the reliability expected of the Yamaha brand are sent to what the factory workers call the “back room.” At this small harbor, the outboard’s fuel is drained, testing jigs are removed, and the unit thoroughly cleaned so that every customer receives a sparkling new product. Once the powerhead cowling and its protective cover are attached, this creation that has passed from the hand of one Yamaha craftsman to another is finally complete.
It is carefully packaged and loaded aboard a truck that departs the Fukuroi South Factory on the first leg of its journey to the world’s waters, where they will use their power and reliability not only to propel boats but also deliver Kando and peace of mind to those aboard.
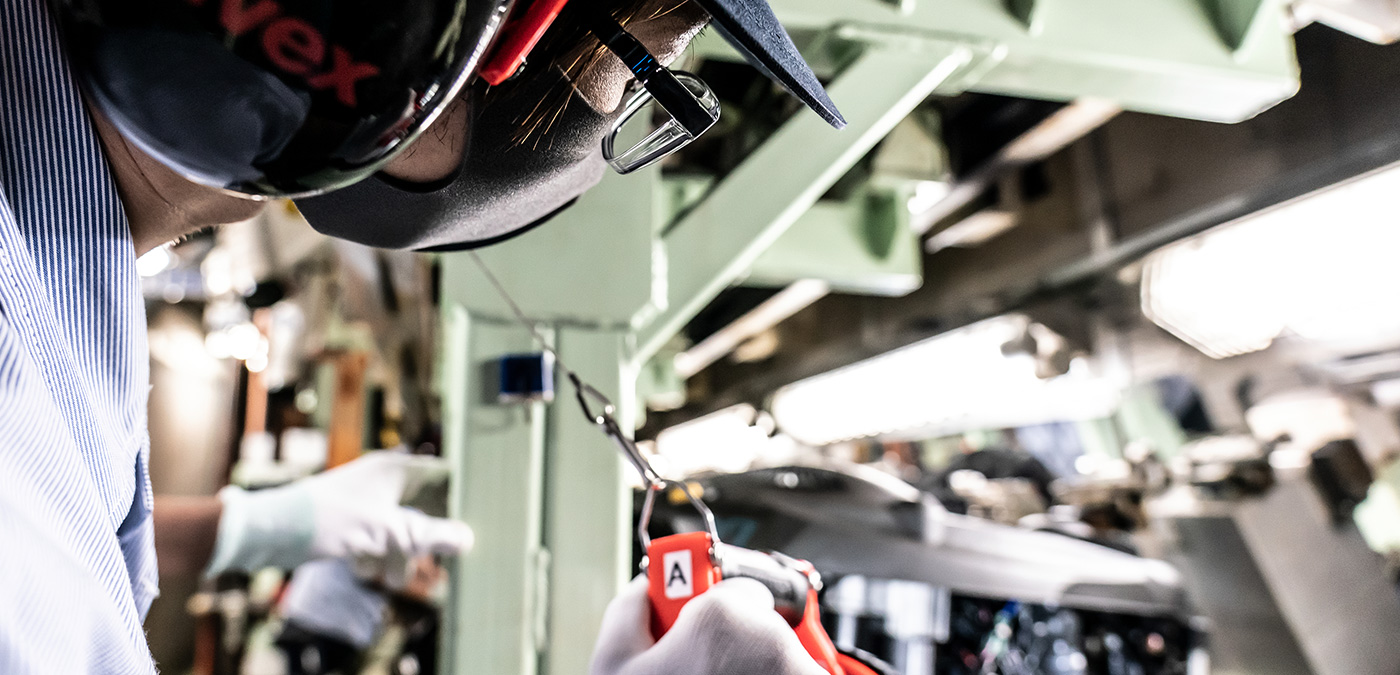