Outboard motors spend the majority of their lives almost entirely submerged in water, dutifully propelling the boats they are mounted on to and from port. The only part constantly visible to those at work or play on the boat is the powerhead cowling that envelops the engine. While it must be well engineered and functional to protect the engine from the water, it also serves as the “face” of the outboard and thus must also sport a highly attractive and refined design. To enhance the natural beauty of the cowling’s curves and contours, Yamaha’s craftsmen bring their finely honed senses and skills to bear.
Fingertip Detection of Imperfections
The palms of the craftsman have caressed the curved plastic surfaces of so many powerhead cowlings that they instinctively know the form a properly shaped piece should have. As his fingertips run across the surface, if they detect even the slightest irregularity, he performs a careful visual inspection to check the cowling’s condition. Should a correction be needed, he selects from among the many nearby polishing tools one best suited to the task.
Neatly arranged on the shelf are the tools of his trade, with varying grades available for sandpaper, chemicals, and metal polishing tools. The craftsman carefully brings the tool in his hand to the cowling’s surface and repeatedly makes delicate movements with intense focus, manipulating the tool to eliminate the imperfections his fingertips detected earlier.
Once they are press-formed, the powerhead cowlings are not sent directly to the paint shop; they must all first pass through this atelier for smoothing and polishing their surfaces. The shelves behind the craftsman are stacked high with cowlings awaiting his attention, but each one must wait its turn. Polishing work is about taking the time to perfect one place and then spending even more time to perfect another until completion, thus it cannot be rushed and there cannot be compromise. Each cowling also presents something different; some are ready with one or two finishing touches, while others require ample time and concentration to complete.
“The powerhead cowling is an outboard’s face,” says one craftsman. “It must be nothing else but beautiful.” Only after meeting a craftsman’s approval is each cowling considered satisfactory.
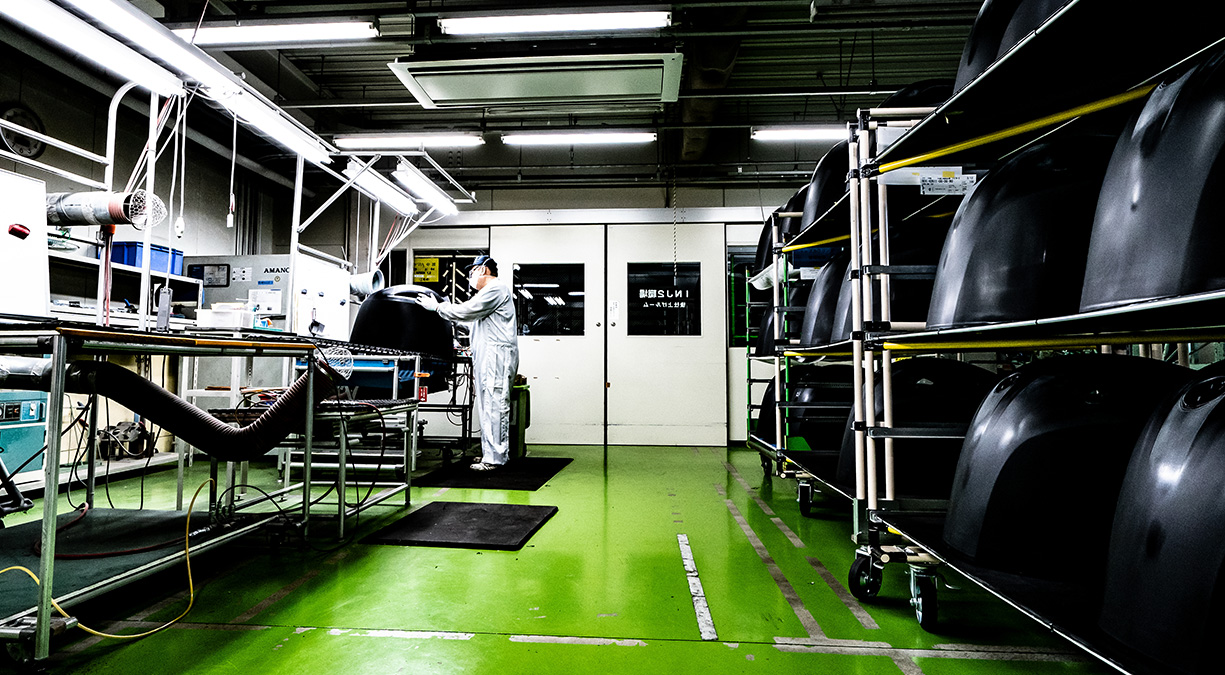
A Mirror-Like Painted Surface
Craftsmen of a different aesthetic specialty await each powerhead cowling that rolls off the paint line. The surfaces of the cowlings are duly prepared prior to painting and they all already look beautiful. Nevertheless, as the painted workpieces arrive via the assembly line, the beauty and finish of each one is individually inspected in the hands of these craftsmen.
The cowlings are not only in Yamaha’s traditional metallic grey either. With the greater variety of colors introduced in recent years, powerheads now come in white, black, and the subtle gradations in between. This has raised the level of difficulty for these inspectors and their eyes must now be even more critical.
Although all the cowlings already appear sufficiently attractive, they still receive yet more attention. The craftsmen use polishers to slowly bring out the true brilliance of the metallic painted surface. Reflected deep within the paint’s tiny metallic particles are the eyes of the craftsmen bestowing it with its final beautiful luster.
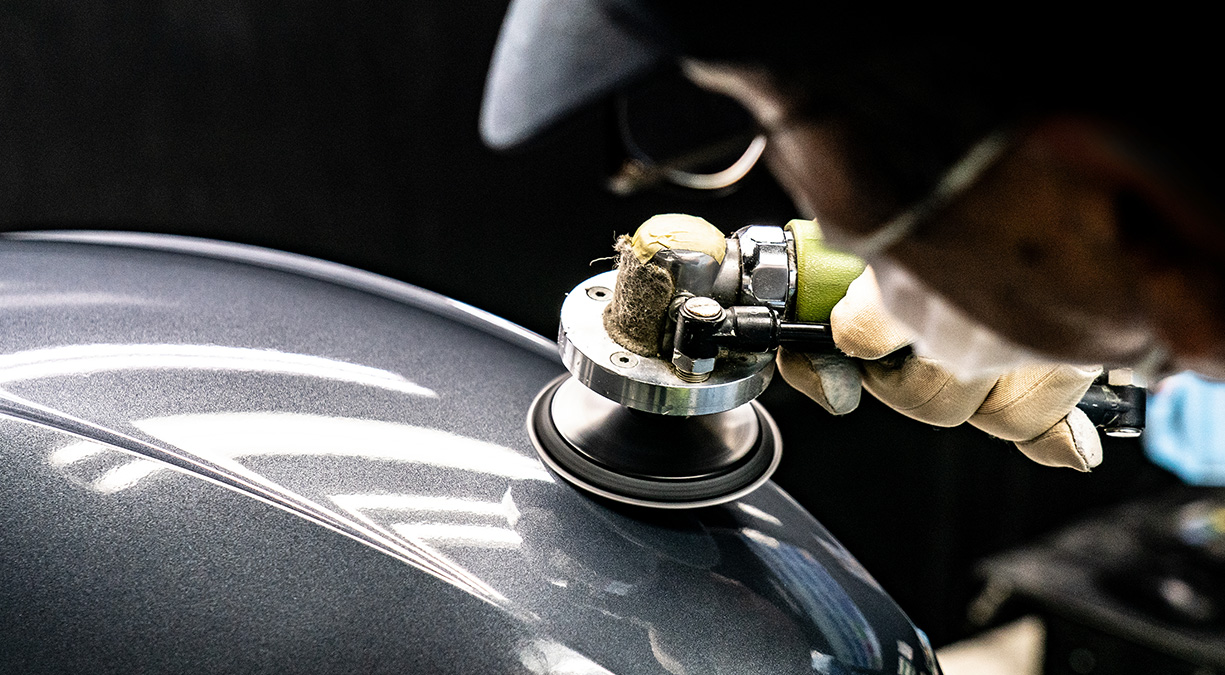
Knowing the Right Angle and Pressure
The quick pace with which the experts here apply decals to the cowlings requires the angle of the squeegee against the surface be maintained and that the pressure be just right. These are the foundational skills needed in the graphics application workshop. To acquire the muscle memory for mastering this specific set of movements as well as learn how to adjust and correct the degree of pressure applied, the men and women working here perform repeated trial applications with a scale constantly measuring the amount of pressure they are applying to the surface. One worker in the shop likens it to doing endless practice swings in kendo.
If affixing protective film to a smartphone screen without creating any air bubbles seems difficult, imagine the skill it takes to do the same thing with a large decal over half a meter in size to a curved surface! The task is made even more challenging by the decal’s powerful adhesive. Out on the water, an outboard is exposed to wind, rain, and extreme heat, making it easy for the decals to peel off. To prevent this, the adhesive paste used for powerhead decals is much stronger than those for motorcycles or other products—once you begin, there’s no going back.
However, technology does help make this difficult job a little easier. A laser from behind projects the correct placement for the decal on the cowling, with the red lines showing where to start applying it and guiding the worker’s hands throughout the process. After the initial application, the worker uses her squeegee to apply pressure to the decal in a single flowing motion to seal it to the cowling—she’s nailed it again. All those hours of “practice swings” day after day is how each expert skillfully adds the final touch to a Yamaha outboard’s face.
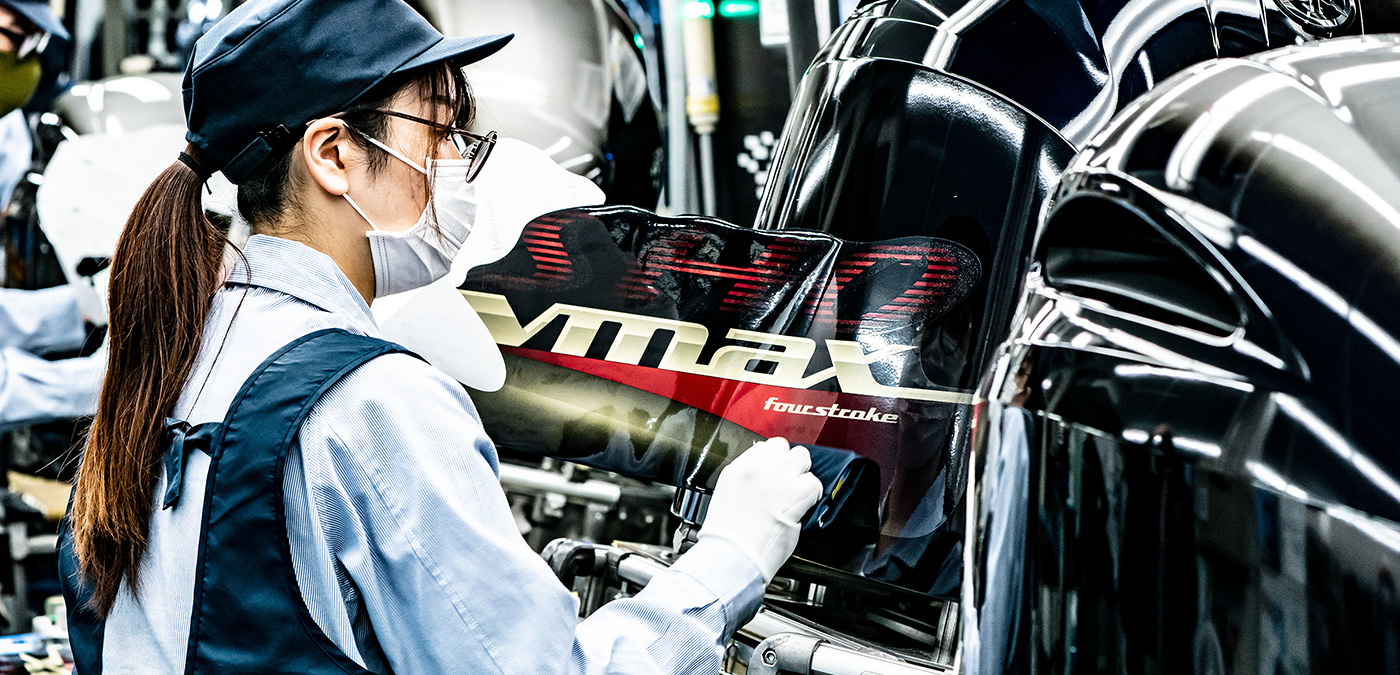