The lower unit is the bottommost part of an outboard motor and is made from a single large aluminum casting. Its rugged housing protects the driveshaft while its beautiful streamlined and hydrodynamic shape offers minimal resistance when passing through the water. Its high resistance to corrosion while submerged in the harsh operating environment of the world’s waters is the product of carefully selected materials, precision machining techniques, and the application of a proprietary undercoating using first-rate painting technologies.
Handling Harsh Conditions with Toughness and Refinement
Each outboard motor is composed of some 3,000 individual parts, each of which is important in its own way. Among these, the lower unit’s role is especially vital as this large and resilient part of the outboard is constantly exposed to the harshest operating conditions. Further, it must also be durable enough to protect the outboard’s driveshaft—a part essential to the entire drivetrain. That is the most important task of this cast aluminum part.
However, fulfilling this role is no easy task; the lower unit is nearly always immersed in either seawater or freshwater. It is also not uncommon for the unit to be struck by branches and other matter either floating or under the water. The lower unit is already in the most rust-prone location, so a scratch or damage that exposes the aluminum body is like an open invite to a corrosion buffet for oxides. To protect this part so crucial to the outboard’s propulsion, Yamaha casts the lower unit with a carefully developed corrosion-resistant aluminum alloy. It is the unsung hero of an outboard’s function and performance, faithfully carrying out its role while remaining largely unseen by those aboard the boat.
The lower unit for a high-horsepower outboard is about as big as a small tuna fish. However, peering inside gives one a good idea of how very intricate its actual shape is. The lower unit is made using high-end aluminum casting technologies to not only bestow it with sufficient strength but also a precisely formed structure. To guarantee the quality and precision of the finished piece, Yamaha technicians perform strict inspections with non-contact 3D scanners.
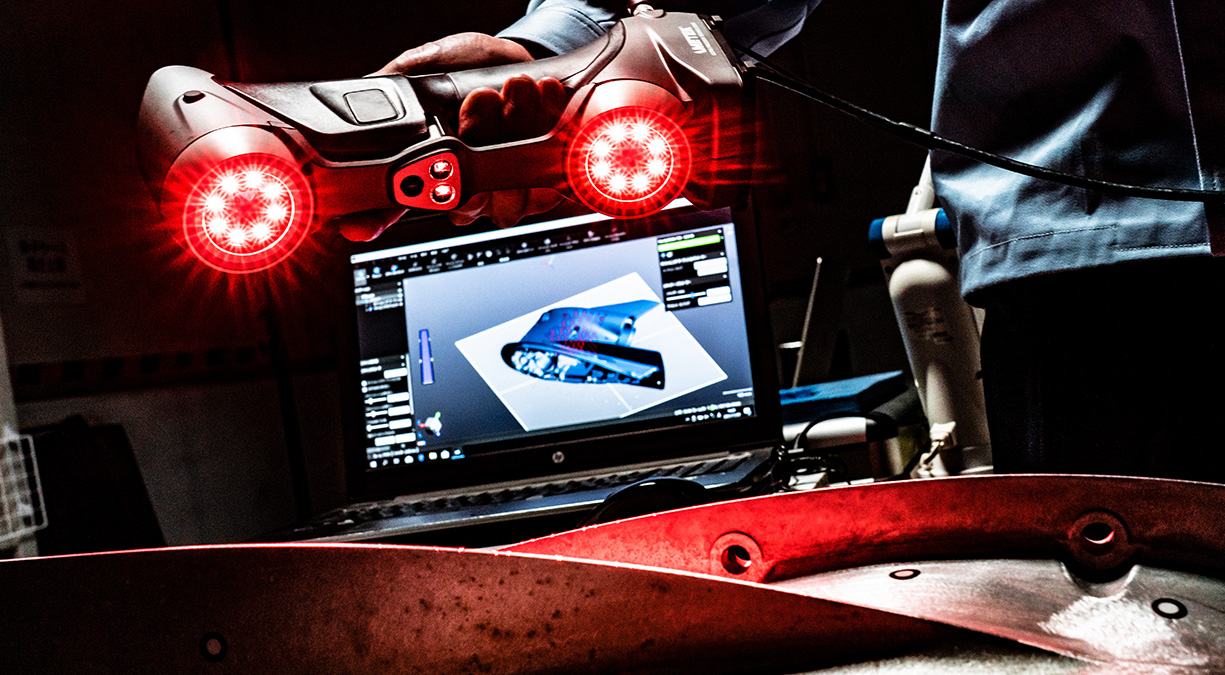
Comprehensive Protection for Long-Term Durability
After a thorough inspection, the large lower unit for the flagship F425 5.6-liter V8 outboard is transported to the paint shop. The dark gray mass of aluminum alloy moves steadily down the line until reaching two waiting rackers, who silently confirm its arrival with quick glances at each other.
Part of the work to protect the lower unit from corrosion falls to the craftsmen at the paint shop. Three coats of paint are applied and the unit bake-hardened twice. To imbue its outboards with the highest levels of corrosion resistance, Yamaha has developed and refined its own proprietary undercoating process.
The rackers manipulate a crane to hoist up the heavy lower unit and attach it to the factory’s line of overhead hangers and it is then transported to the entrance of the painting line. Once inside the paint booth, multiple painting robots will apply primer, a base coat of color, and a clear coat. The unit will scarcely see human hands again until inspectors check it once the painting process is complete. The lower unit’s trip through the paint booth is a long one, taking around three and a half hours.
However, the aluminum surfaces of the lower unit must be properly prepared before the robots can start painting. Moving slowly down the line suspended from above, its journey to the paint booth begins with repeated cleaning operations. This includes a hot shower, a chemical spray down, and more to methodically remove the different residues and oils left after the machining and production processes.
Even the water used for cleaning is specialized. “Ordinary tap water contains calcium and other minerals,” says a technician. “If those substances remain on the workpiece after washing, it will degrade the beauty of the paint.” The large washing equipment near the paint shop constantly filters out impurities to create purified water ready for use in cleaning. “Readying this purified water for the unit’s shower is an absolute necessity.” This thorough cleaning process is how Yamaha prepares each lower unit so that the primer, paint, and clear coat will adhere to the aluminum properly.
Now meticulously clean, the lower unit moves down the line and finally reaches the paint booth where the articulated painting robots await its arrival.
The painting process begins with the application of the primer undercoat. Yamaha uses its own primer blend that includes corrosion-resistant ingredients, and the bare aluminum surfaces—now devoid of all oils—are sprayed by the robots. The metallic base coat is applied next, followed by a clear coat to bring out the paint’s true luster. Protected from overspray by covers and moving in a controlled and agile rhythm, the 6-axis articulated robot arm replicates the finely honed motions of expert bodywork painters, from the width, volume, speed, and angle of the spray to the swaying, wrist-like motions. The end-result is virtually impeccable.
However, even robots aren’t perfect; they may be able to mimic the techniques of a master, but the knowledge and keen sense for quality paint work remain the hard-won possessions of master craftsmen: “The temperature and humidity inside the paint booth change with the seasons. We pick up on that and correct for it with the paint mix, method, and viscosity.”
The craftsmen’s senses are like finely tuned instruments. “First thing in the morning, the workpieces are cool and even between before and after lunchtime, the temperature of the aluminum changes slightly,” explains one. “If we paint them all as-is without adjusting for these changes, the paint can run and other blemishes are more likely to occur.” The eyes and hands of the master craftsmen stand constant watch over the paint shop, adjusting the robots’ programming when needed like teachers guiding their students.
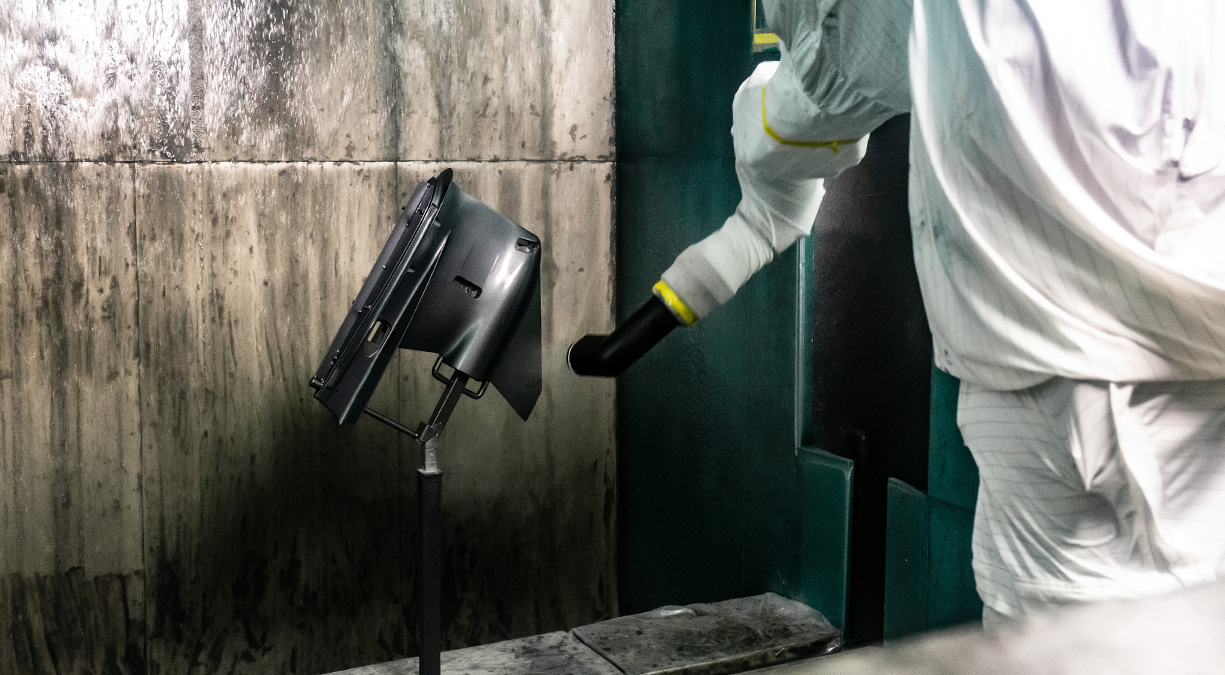
Coordinated Craftsmanship: Painting Is a Team Job
After the lower unit receives its three coatings of paint and is bake-hardened twice, it is lowered to the inspection area as it slowly cools. The nearly complete part emerges from the darkness of the long transport tunnel into a brightly lit workspace. Here, the faultfinding eyes of the inspectors will ascertain whether or not the painting robots have done their job properly.
The personnel here train their discerning gazes on the freshly finished workpieces that arrive. All of them are highly experienced in the various aspects of the painting process in their own right and have passed a special test for performing color and hue inspections; no defect or imperfection, however slight, escapes their scrutiny. “They can clearly see things that we can’t,” the younger technicians at the paint shop respectfully admit. “It may be how they are able to perceive things from a different perspective.”
At the worksite, a row of zeros is prominently displayed. They stand as proof that any mistakes made by the painting robots did not go unnoticed. Each outboard model requires its own robot painting program and paint mixture, and the paint booth’s environment must be constantly monitored and corrected for. Like a skillfully conducted orchestra, it is only when these and the other requisite processes are in perfect harmony that the painted surface is truly complete and reflects Yamaha’s signature quality.
“Good painting is about good teamwork,” says a paint shop veteran. “Each of us are craftsmen and embrace this philosophy. Each time there is a line of zeros up there, it deepens our team spirit and we share in the joy of having performed quality work.” On this day, another zero was added to the line and the brighter mood in the workshop was tangible.
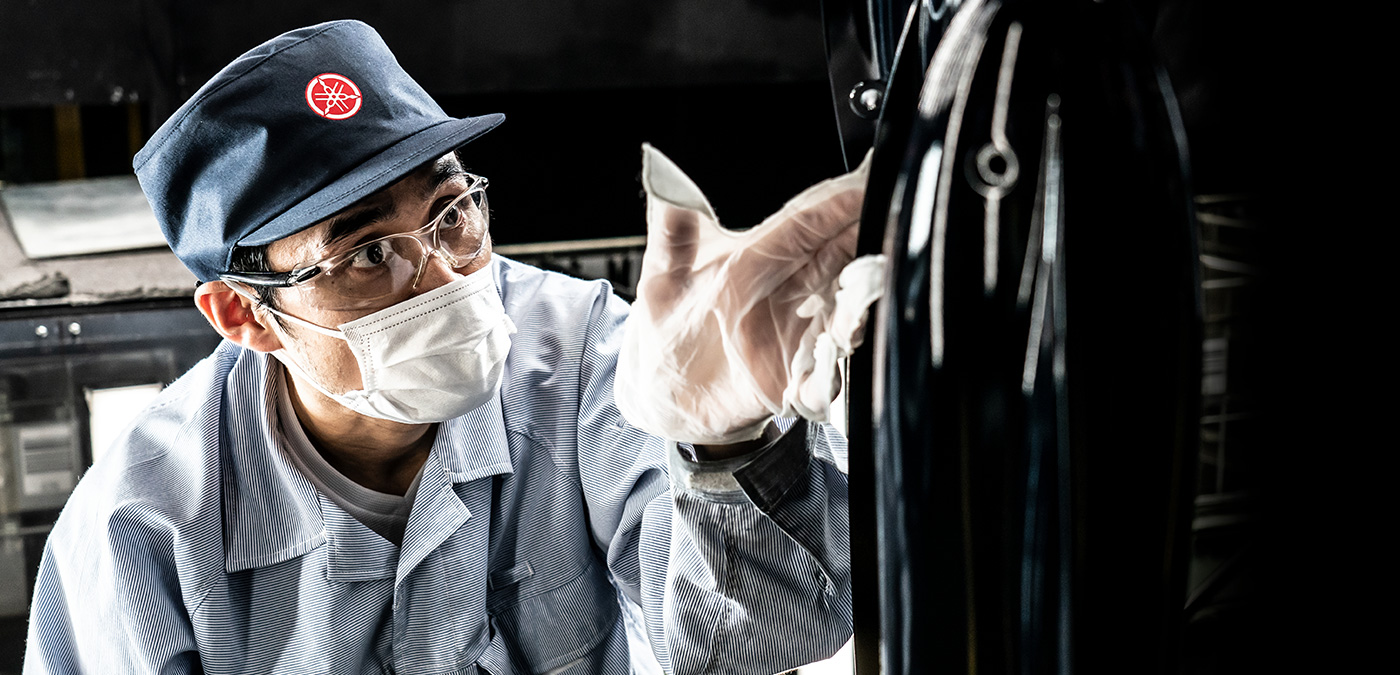