If you trace back the various steps of the manufacturing process for building performance, functions, quality, and design into a product, everything begins with the raw materials used. From workers on the factory floor to product engineers and even the designers, the widespread knowledge and interest in aluminum as a material at Yamaha can be attributed to the company’s culture and tradition of producing cast parts in-house. And because delivering unquestionable reliability is the goal when producing Yamaha outboards, the first step in the production process is at aluminum smelting sites.
Aluminum Alloys Forged by the World’s Oceans
Aluminum ingots have various classifications depending on their purity and composition. The material Yamaha employs for its outboards is an aluminum alloy, in which various other metal elements are added to the base aluminum prior to use. Yamaha developed its first outboard motor, the P-7, in 1960. Since then, we have endeavored to develop aluminum alloys better suited for use in the harsh marine environment, and that R&D has continued for more than sixty years now.
Corrosion is the mortal enemy of metal parts in outboard motors and it is no exaggeration to state that our history of metals research has been a battle against corrosion. Furthermore, the dramatic rise in performance of outboards over the years has resulted in ever-greater demands on aluminum as their chief material. Outboard motor parts must not only be lightweight but also thin as well as tough. What’s more, the aluminum must have the elasticity enabling casting into complex shapes and designs. In short, these and other requirements have only driven up the difficulty and expectations for aluminum as an outboard material. But, Yamaha’s materials research departments have closely collaborated with the metalworking industry for decades, working to bring more advances to the material in order to rise to meet these always-evolving needs.
Stacks of aluminum alloy ingots stand like small towers in the casting factory. They are made from an alloy developed exclusively for Yamaha outboard motors, forged from a wealth of knowledge acquired on the world’s oceans, our challenge to offer quality that exceeds customer expectations, and a never-ending pursuit of beauty when building our products.
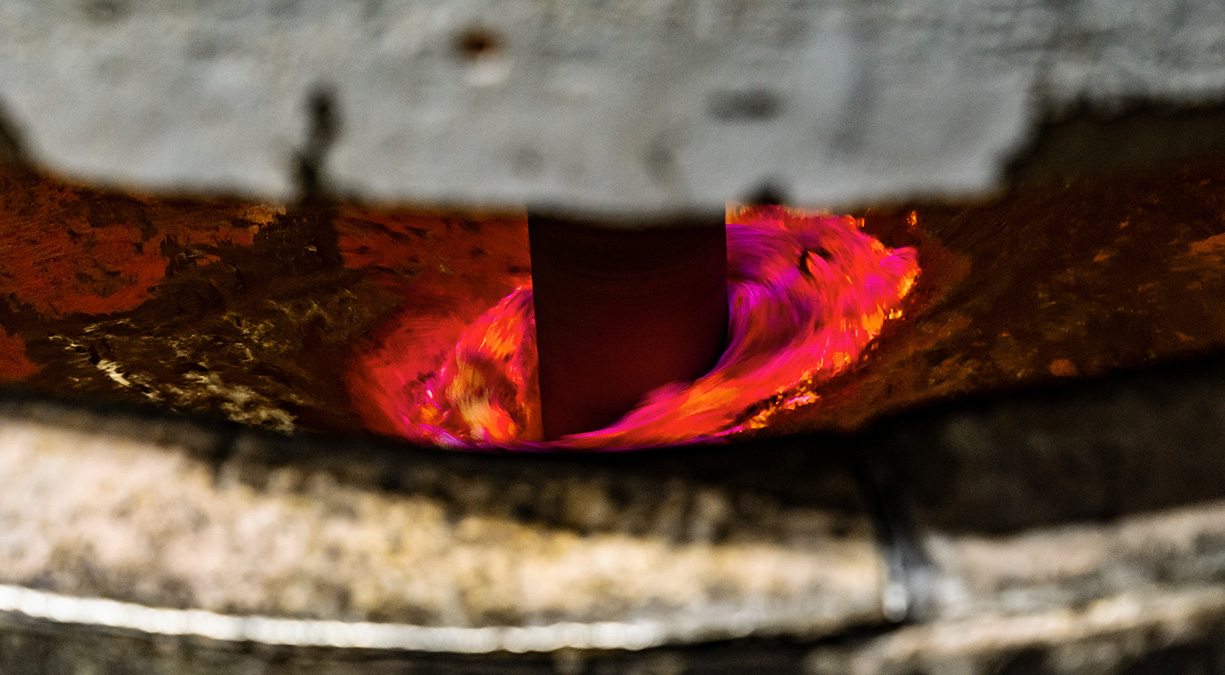
Carefully Controlled Smelting to Extract the Material’s Potential
When the outlet of the melting furnace opens, red-hot molten aluminum gushes out. When the liquid aluminum comes into contact with the air in the factory, it gains a slightly more viscous consistency and takes on a semi-metallic color as it flows to fill the waiting pouring ladle. The sight is powerful and beautiful every time—the very first step in the Monozukuri process.
Although the melt in the pouring ladle is covered by a silver-colored membrane, when scooped off it reveals the still red-hot molten aluminum below. To remove inclusions and impurities from the melt, a cleaning agent called flux is injected and the molten aluminum is thoroughly stirred. This causes the impurities to rise to the surface in silver-colored lumps.
All Yamaha outboards use a special aluminum alloy. To make the most of its potential, the melt must be maintained in a very clean state. While few in number, the aluminum ingots that arrive at the factory still contain small inclusions called hard spots within them. If these impurities are not removed prior to casting and make it through to the machining processes, they may leave flaws on the cut surfaces of parts, which can lead to eventual corrosion. This is another reason Yamaha has carried out extensive research not only for cleaning aluminum for casting but also on inspecting its purity.
One of the techniques used at Yamaha’s casting worksites is a simplified PoDFA (Porous Disc Filtration Apparatus) method for evaluating the cleanliness of melts.
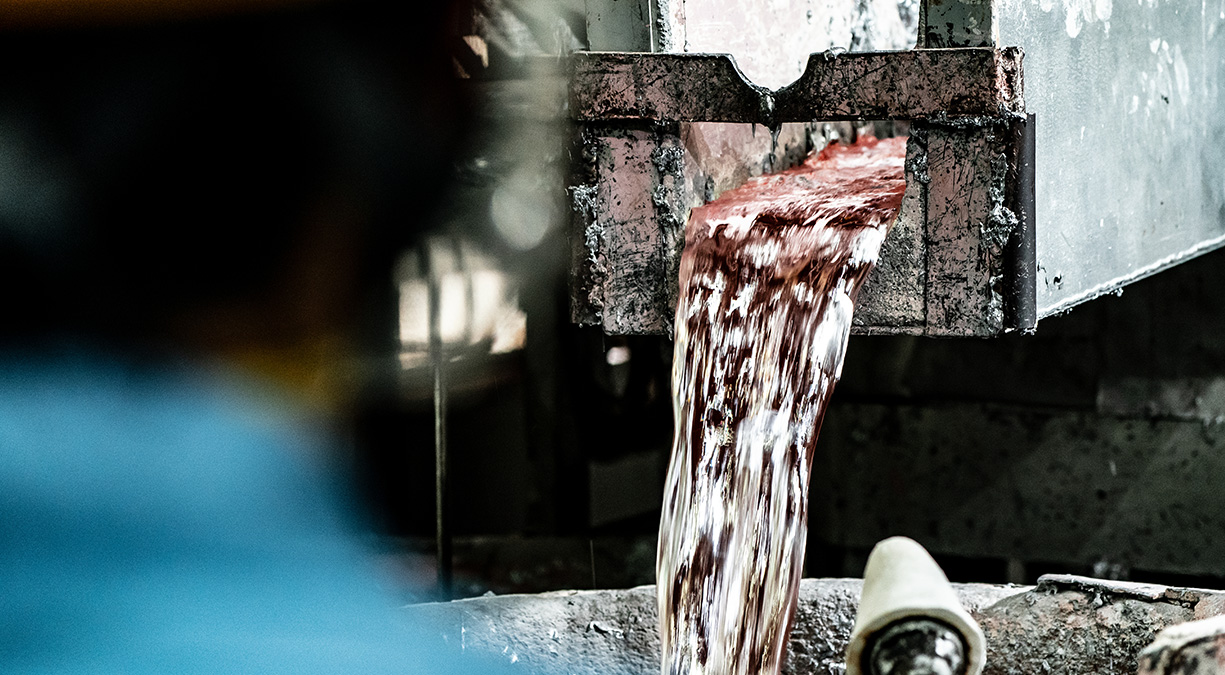
Pushing the Limits for Purity
The standard approach for evaluating the cleanliness of a melt is the K-Mold test. The cleaned melt is poured into a mold and allowed to cool. The piece is then immediately fractured and an evaluation made based on a visual inspection of the cross sections of the casting.
However, certain issues need to be kept in mind with this approach; evaluations can vary depending on the technician performing the test and confirming an evaluation can also consume considerable time. As an alternative, Yamaha developed its own simplified PoDFA method. This test expresses an evaluation result numerically, greatly expediting the time required for analysis. The time saved through this made it possible to conduct more minute tests and analysis right at the melting furnace.
A small stainless steel wire mesh is inserted into the pouring ladle and when the jig holding the net is swirled around in the melt, the aluminum adheres to the mesh—this will be the sample for conducting the evaluation. Within the sample are miniscule amounts of impurities that couldn’t be removed during the flux cleaning process. By measuring and tracking the weight of the mesh, we can guarantee the aluminum’s level of quality. The melt is inspected as it leaves the furnace as well as when it fills each pouring ladle—there are no exceptions.
To extract 100% of the proprietary aluminum alloy’s potential, Yamaha is pushing the limits of purity by performing numerous extra steps in the cleaning process by hand and developing its own evaluation methods to ensure the quality of the resulting alloy. This scrupulous preparation is where Yamaha’s Monozukuri begins.
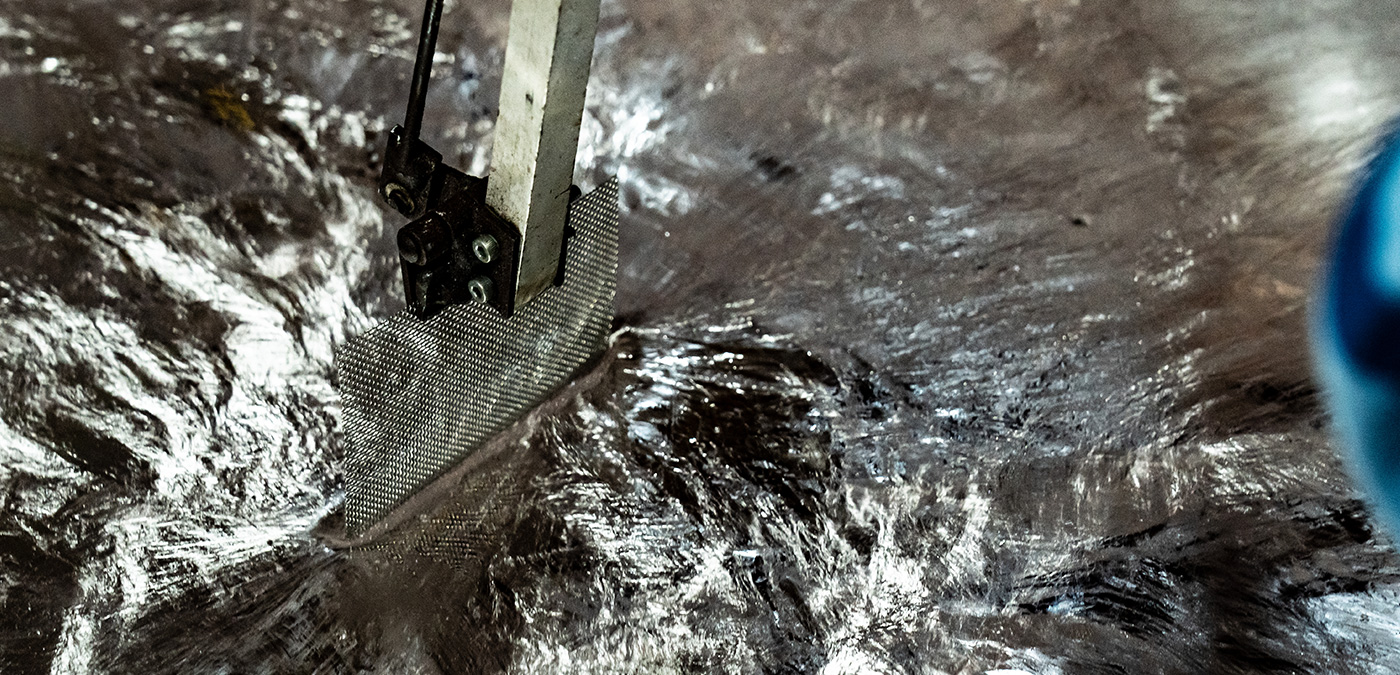