The Cell Manufacturing Line: Where Master Craftsmen Work Their Magic
The simple construction and functional beauty of the SR400’s engine has won it many fans around the world. Although it is considered a relatively uncomplicated single-cylinder engine, it is still the thumping heart of the motorcycle and is actually not as straightforward an engine as many people imagine. It contains about 600 parts and components, and the careful and precise assembly of all those parts is what results in the SR400’s endearing sound and pulsing feel.
Like a fine watch, each engine is hand-assembled in its entirety from the ground up by a single craftsman. Even for a worker with highly experienced eyes and hands, the assembly process for a single engine demands a full hour of intense concentration. Despite this mentally taxing task, these veritable Zen masters of the profession spend countless hours handling engine parts, and some have assembled as many as 3,000 SR engines.
(Photos shot in June 2019)
The Cell Manufacturing Line,
aka the Craftsman’s Workshop
Yamaha Motor’s motorcycle production and assembly methods can be largely divided into three different types.
Models with the highest production volumes are put together on the divided workflow assembly lines. These are about 70 meters long and manned by 50 or so people who perform separate tasks along the line to assemble each unit.
The short lines dedicated to assembling big-displacement bikes in smaller volumes have multiple modular stations with their own set of tasks for assembling the motorcycle. Two people in each module work as a team to install the componentry pertinent to the station they are in.
The third method is the cell manufacturing area, also sometimes called the “craftsman’s workshop.” Here, one worker—or sometimes a small group—singlehandedly assembles an entire motorcycle. As some manufacturers began to garner attention for putting together precision equipment like cameras or wristwatches in this way, Yamaha also introduced this production method around 2010 for certain products. Among motorcycle mass-production facilities, this production approach is extremely rare to see.
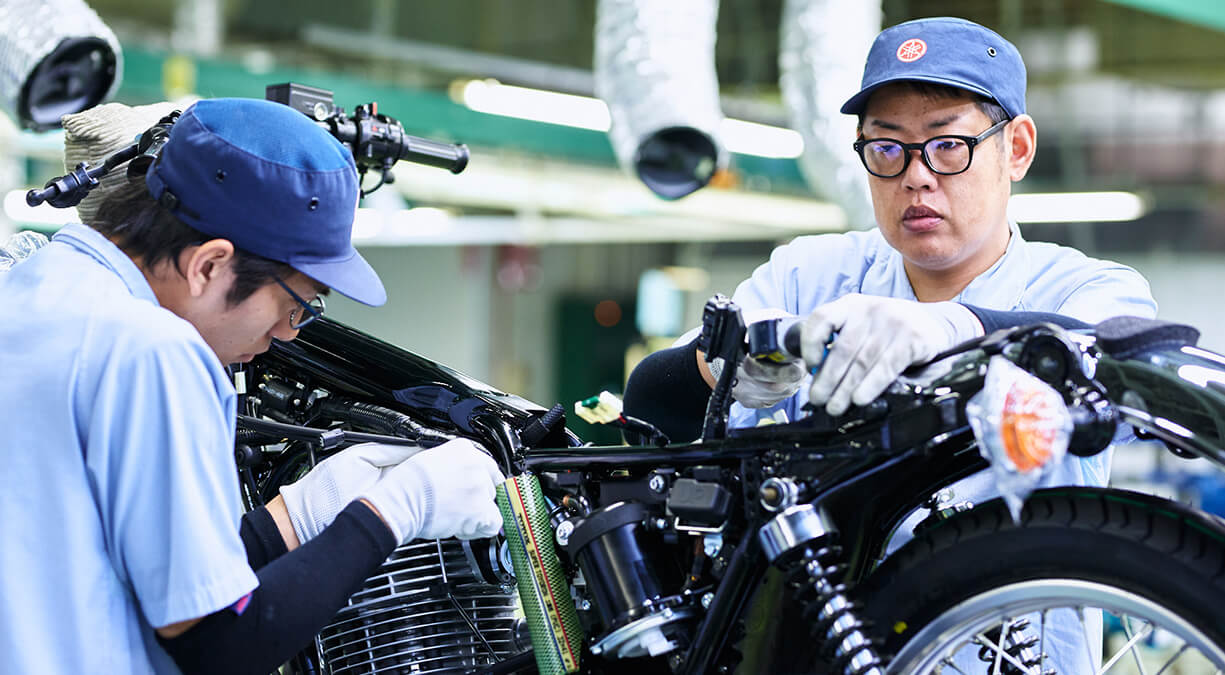
Taking Aim and Hitting the Mark
When assembling an SR400 engine in the cell manufacturing area, every step in the process is performed by a single craftsman. Of course, assembling the approximately 600 parts into a complete engine requires more than 600 hand movements. These are referred to as “the step number.” On the mass-production lines where each person works 1 to 2 minutes on their specific task, the step number is 00. However, in the cell manufacturing section where the SR400 engine is assembled, the step number totals over 600 and it takes even a highly experienced worker one hour to complete everything.
“What I consider important here is having the desire to improve and the ability to concentrate,” says one veteran with some 3,000 SR400 engines under his belt. When he was first selected to join the craftsman’s workshop, it took him around 90 minutes to assemble one engine. Today, he can assemble one in just over 50 minutes. By constantly analyzing where he was losing time or making mistakes, he was able to up his pace to where it is now, and since he no longer has to race against the clock, this motivated him to strive for even greater precision in his work. “For example, when adjusting the valves for clearance, I now take aim to hit the mark and get them just right.” When he succeeds, knowing the engine will put out its best performance fills him with immense satisfaction.
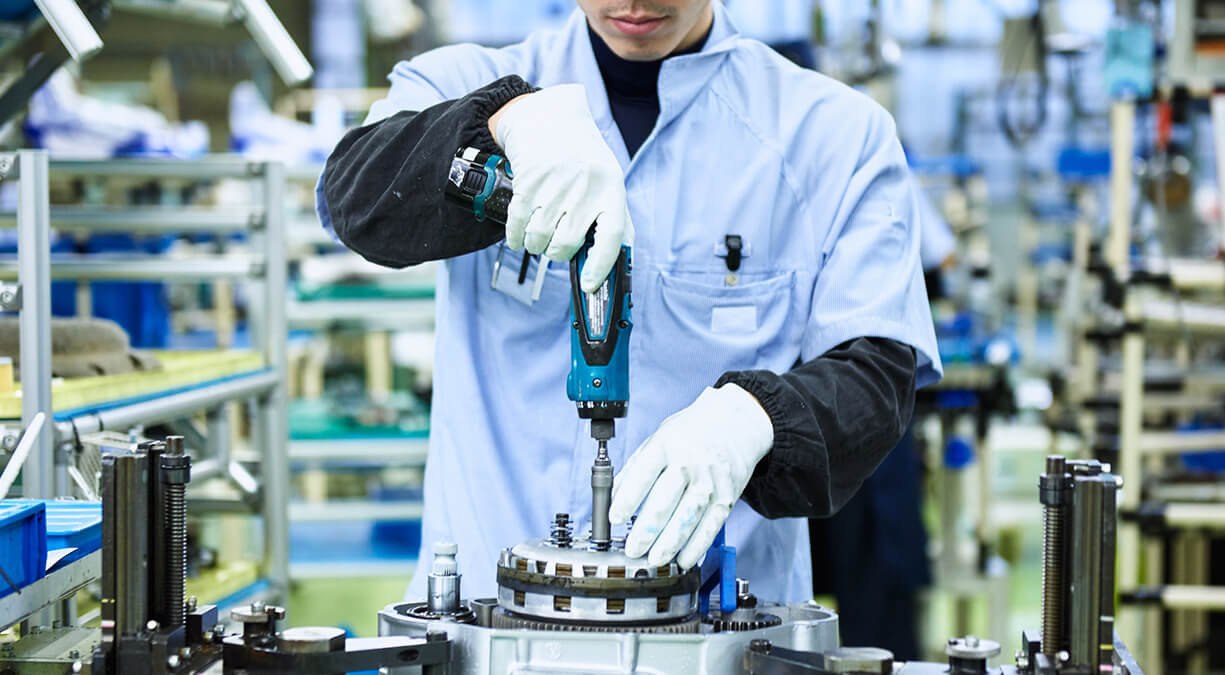
A Ceremony and “Side Effects”
When a craftsman finishes each hour-long process, there is still a ceremony to perform—the cleaning of the workspace. This is performed wholeheartedly and with gratitude, and when the worker deems the job satisfactory, the holding jigs are returned with care to their starting positions for the next job. The positioning must be exact, for those in the workshop do not accept anything less. Once this is finished, they cast a careful gaze across the now-clean workspace. Are the carts all in the correct position and facing the proper direction? Are there any chemicals or fluids spilled on the floor? After running through this mental checklist and confirming everything is neatly in place, the ceremonial ritual comes to an end and a short relaxing sigh finally escapes their lips.
The assembled engine is then sent to another cell manufacturing location for chassis assembly, where it is mounted in the frame and slowly becomes the heart of a completed motorcycle. The newborn bike is then sent to the test station. As the tester works the kickstarter, the engine spurts to life with a thump, thump, thump. What was just a few hours ago a spread of 600 different parts now emits the distinctive exhaust note of the SR400. “Mmm, that sounds good. Right on the mark,” says the craftsman. He can tell by the sound that he got everything just right—the mark of his unrivaled workmanship. For these experts, perhaps the unconscious penchant to train their ears on the sound of each SR400 around town is one “side effect” of the job.
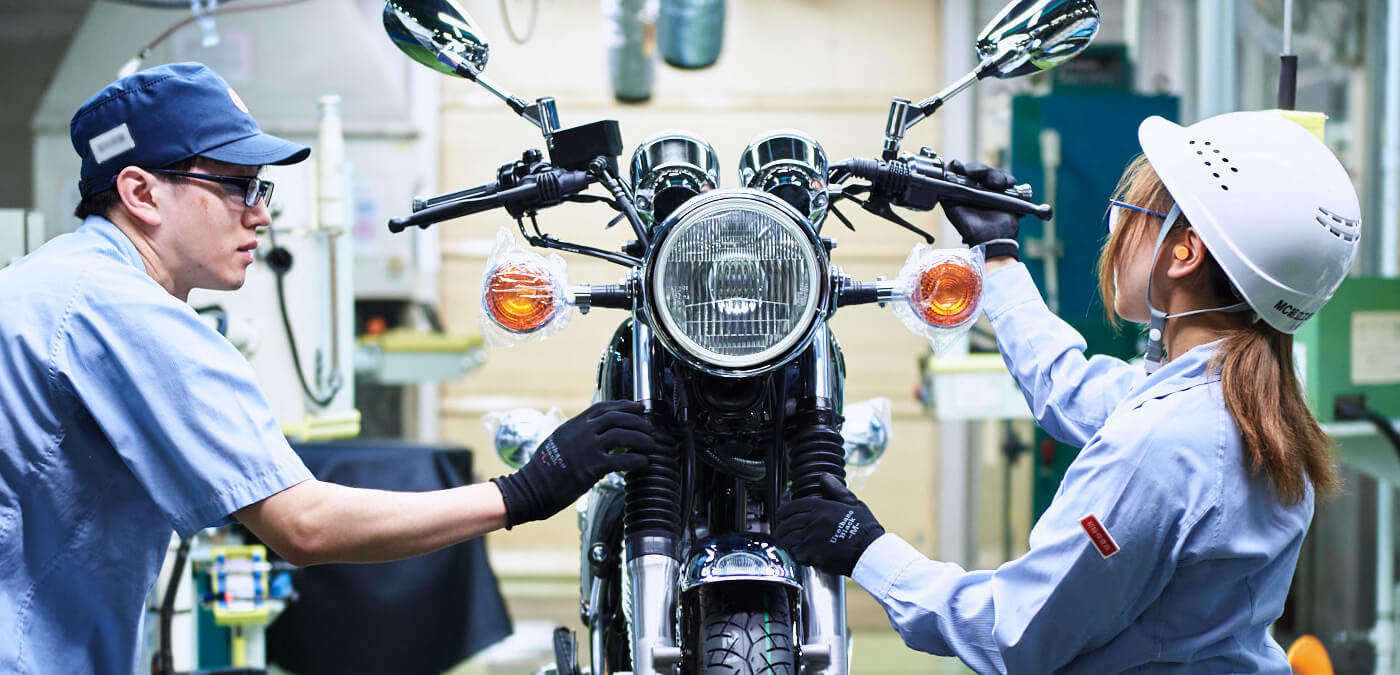