The Workmanship Within a Polished Aluminum Fuel Tank
Aluminum has about only one-third the mass of steel, and since a chassis’ weight directly influences a motorcycle’s performance, aluminum is used for creating numerous parts. However, using aluminum for fuel tanks brings a different story. Because aluminum is difficult to stretch and form, mass-producing fuel tanks with the metal has long been a challenge. Although Yamaha overcame the high hurdles that emerged for manufacturing the beautiful aluminum fuel tanks for the YZF-R1, creating one still remains an ever-present challenge for those on the factory floor.
In spite of—or perhaps because of—that, Yamaha’s craftsmen almost seem to relish the test this presents to them. “If we’re going to make the tanks out of aluminum, let’s polish them to a mirror finish and really show what we can do.” It was with these words that they embarked on their challenge to not only mass-produce aluminum fuel tanks, but do so while putting their mastery of the material on display.
An Industrial Art Piece Made by Hand
in a Facility for Mass Production
After its pre-treatment work is carefully completed, the MT-09’s 3-cylinder engine is fed through to the painting line with its aluminum body completely exposed. About an hour after being sent off, the engine returns to its starting point, now dressed in a coat of beautiful Crystal Graphite paint.
As the units make their trip down the painting line like a row of recruits, no human hands will touch them. A black box mounted above the line controls robotic arms that apply the coating with the delicate movements of a master, and the baking, drying and cooling processes that follow have all been automated.
The engine painting line at the Iwata Main Factory was completed in 2015 and brought various innovations to the matte black painting process; everything from pre-treatment to the application of the final coating was meticulously reviewed and revised.
The new line that was built occupies just one-third the space of the previous arrangement, and the number of processes needed were reduced by nearly 75%. The driver of these dramatic improvements was to program robots to learn the skills of our master craftsmen. This enables the robots to perform the high-quality work of their teachers over and over, accounting accordingly for difficulty and detail with each high-speed repetition.
The fine control of the spray pressure, volume of paint, distance and angle of the spray nozzles, and nimble movements of the robot arms faithfully mimic the hard-won skills of the master craftsmen that “taught” them.
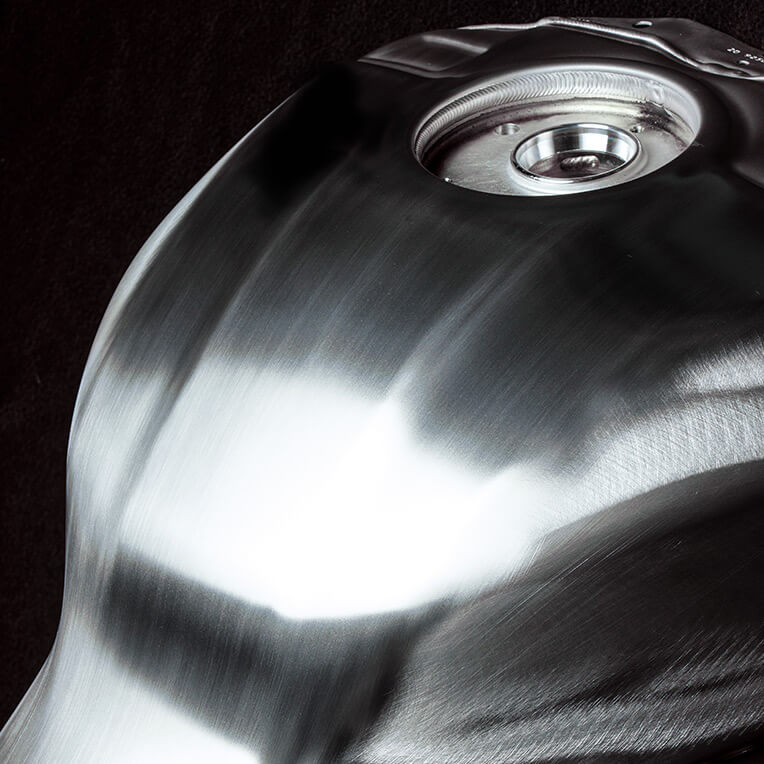
Visualizing Each Move toward “Checkmate”
When forming aluminum, countless tiny pores tend to open in the direction it is being rolled and stretched in. First, a buffing wheel fitted with a coarse cloth of non-woven fabric is used to remove these imperfections. It cannot be rushed and must be performed with care. After roughly 10 minutes, the aluminum transforms into the polisher’s canvas, ready for the final act.
“From here on, the buffing work is like playing a game of shogi (Japanese chess). You make one move but are always visualizing the next to make, and the one after that,” says the craftsman. The right kind of hairline polishing makes the tank look its absolute best when seen from the rider’s perspective. Polishing parts with more typical shapes is rather straightforward; the buffing is all done in a single direction. But because a fuel tank has a more complex curves and surfaces, the way it appears from different perspectives becomes important.
For example, the areas where curving surfaces and lines converge are tricky. The unidirectional hairline polish buffed toward the front of the tank must suddenly change directions. To address this, several test tanks were built, buffing techniques considered, and the desired aesthetic clearly defined before the team devised a polishing map to standardize the procedure.
Step by step, the polisher brings out the inherent beauty of the aluminum tank. His eyes grow sharper and even more discerning as he continues, becoming nigh uncompromising during the final checks of his work before deeming it complete.
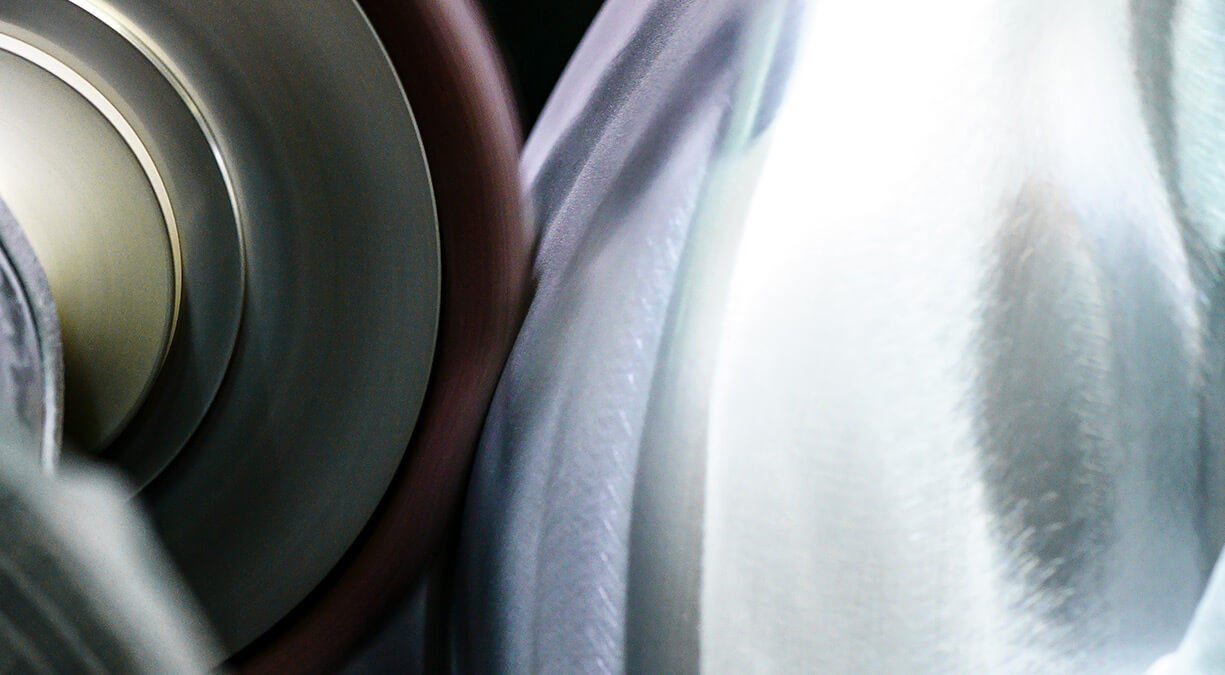
Hone It. Nurture It. Pass It Down.
“The more time you spend at the buffing machine, the better you get. There’s no other way and there are no shortcuts.”
The first skill one must master is to leave polishing lines that are ruler-straight. And that also includes acquiring the steady hands to always leave precisely parallel buff lines even when polishing the same surface over and over. It takes an enormous amount of time just to reach that level.
“It’s not just working with your hands. Doing this requires you to be able to see even the slightest imperfections. You need the ‘Yamaha eyes’ that ensure absolute quality.” The pride behind these words does not allow him to let a single tank leaving his hands be deemed unacceptable.
After their skilled work on the YZF-R1M, word of Yamaha’s polishing experts spread throughout the company. For their fellow Monozukuri colleagues, they no doubt felt that Yamaha had once again acquired another specialty, and before long, developers and designers began requesting more polished aluminum parts for models under development.
Yamaha honed and mastered these skills with the aluminum tank and is dedicated to ensuring they live on. While there are only three people that can do it now, they will be the ones that pass down the techniques of their craft to the next generation.
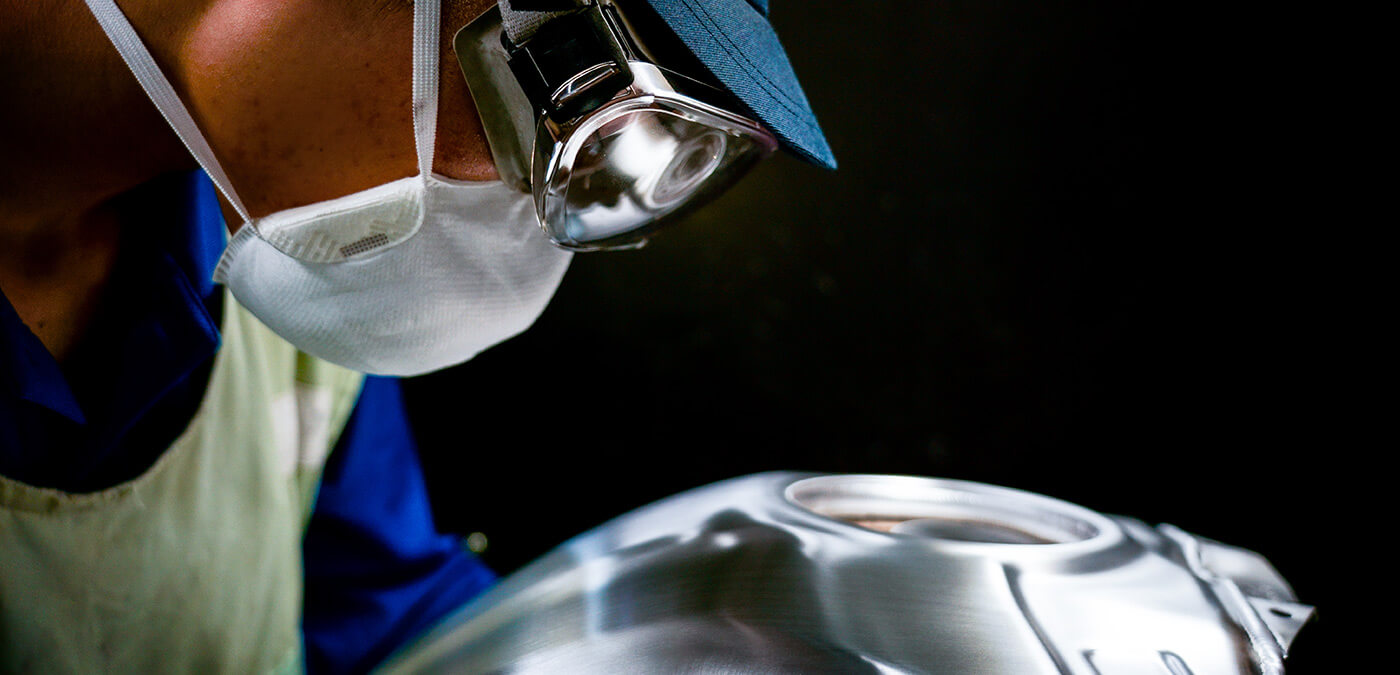