Solder-Paste Printer YRP10e Feature
Single-lane printer that achieves high-quality printing through high universality and multifunctionality
High quality printing
Original 3S head has excellent flexibility and fits various types of PCBs
YAMAHA’s original 3S head allows operators to set/change arbitrarily all the parameters including the squeegee angle, speed, and pressure.
This enables the handling of a wide variety of solder and stencil types to ensure printing under optimal conditions.
Improved filling efficiency and extended stencil life
In order to improve the printing quality, a squeegee excellent in rolling performance was developed. This reduces solder adhesion issues to minimize solder waste. The blade hardness is adjusted to extend the stencil life.


Stable printing quality

A stencil vacuum mechanism reduces the effects of stencil and PCB distortion to achieve stable high-precision printing. The setup time is reduced as there is no need to input offsets during reciprocating printing.
Never overlooks printing failures
The built-in 2D inspection function inspects solder printing conditions in place of the SPI. YRP10e prevents overlooking printing failures to complete the printing process within itself. Feedback from inspection results allows automatic over-printing and stencil cleaning to support nonstop production.
Dedicated inspection camera

Large view field size

Squeegee pressure control reduces variation

A load cell sensor installed in the head measures squeegee pressure to perform feedback. This enables always printing by a constant pressure to reduce variation between forward and backward printing.
High production
Simultaneous operations reduce time loss
Fast transfer contributes to achieving a short cycle time of the whole line.

Conducting cleaning in parallel with transfer improves practical productivity.

Reduction in transfer time improves productivity

Using a 3 division conveyor enables staging up to 3 PCBs inside the printer. Reducing distances needed for standby, print, and carrying-out decreases the substantial cycle time, contributing to an improvement in productivity.
Achieves both high workability and high quality

Adjusting the feeding amount of cleaning paper and using a large-capacity solvent tank minimize the replenishment frequency to decrease the downtime. Even a minimum feeding amount can maintain a high cleaning performance.
Flexibility
Easy stencil replacement without errors
The stencil holder can be replaced with another one selected from seven stencil sizes with a single-touch. Place a stencil at a specified point, and the machine will automatically move it to the right position and fix it there. This provides anyone with an easy stencil replacement procedure free from human errors.


Timely and efficient solder refillment
The system measures the amount of solder on the stencil regularly and alert as necessary the timing of refillment and prevent failure of solder refillment. Based on the measurement results, it can also trace the relationship between the amount of solder and printing defects.

Transfer system handles almost all PCB types
This is a PCB transfer system without stoppers, which is hardly affected by external PCB forms. The mechanical stopper on the side of the camera unit responds flexibly to extremely complicated shaped PCB.
High-speed transfer without stoppers
Achieves high-speed transfer without mechanical stoppers.

Flexible mechanical stopper
The stopper can be descended to an arbitrary position.

Preventing solder from lifting and scattering
The original squeegee operation (belly roll) performs solder rolling by keeping the squeegee and solder in contact. This prevents solder from scattering and reduces solder loss. It provides a stable printing quality regardless of solder types or printing conditions.

Related contents
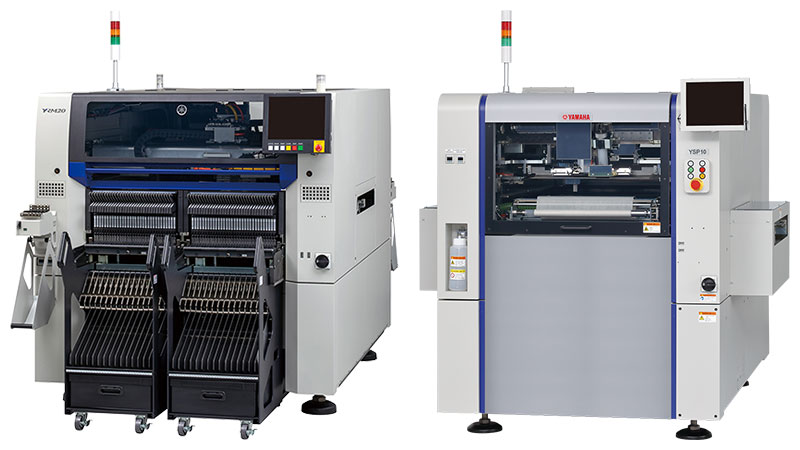
- Product
- Introduce our product lineup, including surface mounters, solder printers, and visual inspection machines.
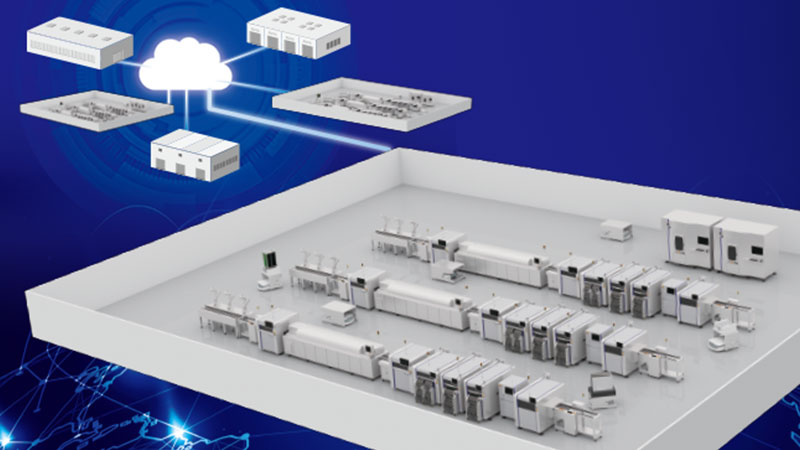
- Showroom
- Find and explore SMT Smart Showroom or Virtual Showroom
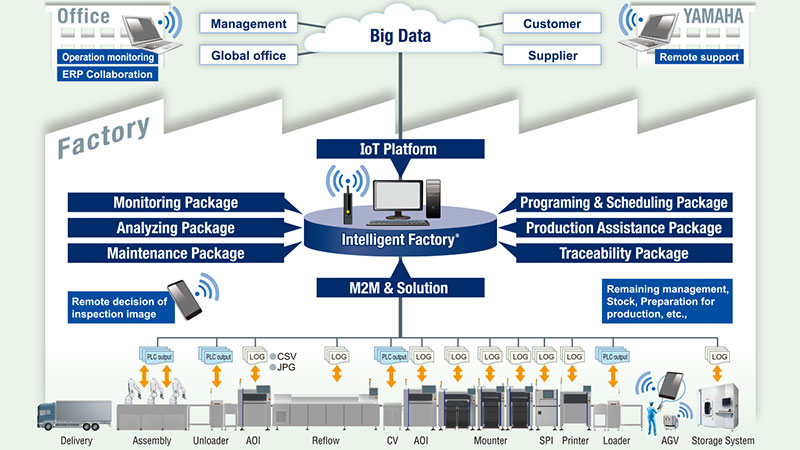
- Intelligent Factory
- IoT/M2M Integration system - System allows linking our SMT machines to equipment made by other companies and give all-around high productivity in the mounting process.