Premium High-efficiency Modular YRM20 Overview
The 1 head solution has reached an ultimate stage. An all-around surface mounter delivering both overwhelming productivity and flexibility!


The 1 head solution has reached an ultimate stage. An all-around surface mounter delivering both overwhelming productivity and flexibility!
- Fusion with Σ technology achieves overwhelming productivity
- Broad-ranging production capability thanks to the 1 head solution
- Standard features that maintain component mounting quality at a peak level!
- Ensures high-efficiency production with a full range of functions!
Function and Feature
2-beams – 2-head with highest speed level in its class 115,000CPH

Needs no head replacement! 0201mm to large-size components

Overdrive motion

Dual-stage conveyor

Recommend for Such Production Site
For customers who want to mount high mix, enhanced-value product PCB using a single lane.

Yamaha's unique machine functions realize high-productivity, high operating rate and a high quality mounting line
The Yamaha 1 head solution provides both high speed mounting for chip components and flexibility for mid-to-large components.
- RM head:A newly developed head that realizes both high-speed chip mounting and flexibility for mid-sized components up to 12mm, T6.5mm.
- HM head:Realizes large component high-speed mounting and flexibility via 10 fully proven inline heads + scan camera.
- Dual stage: Yamaha’s unique “Internal dual stage” provides high efficiency including features like dual lane mounting via a single lane. Large PCBs up to L810mm can also be handled the same way.
The Yamaha unique solution ensures there is no drop in operating rate even during high-mix production.
- ALF:Applies a unique center-open method to successfully realize non-skilled operation + labor-saving by tape and reel presetting + improved pickup rate.
- ZS feeder: Light-weight single feeder that can be carried in one hand with reel attached allows external setups/changeovers of reel-setting tasks. This vastly reduces the load on the operator.
- Non-stop feeder replacement type carriage: Inserts-removes feeder during mounting to allow feeder replacement with no machine downtime. The light weight and compact design reduces the operator work load.
- IT Option- Components Remain Counter:Gives pre-warning of component shortage (stockout) to allow preparing spare tape and reels and splicing the tape before the machine stops.
- Automatic changeovers: Prevents changeover errors and reduces machine switchover downtime on multi-connected lines by sequentially carrying out the “next changeover’ when the next PCB lot arrives. Automatic push-up pin changerover is also available.
Solution that realizes high-quality mounting needed for mounting of high enhanced-value products.
- Side-view camera function monitors nozzle tip images to detect the component pickup position (attitude) and detects such as missing components, vertical mounting errors, and reversed components.
- Unsprung or unsupported weight has been drastically lightened to reduce impacts on ultra-small components during mounting
- Nozzle ID management allows ideal maintenance based on the number of shots. ANC holders can be mounted or removed in 1 batch, and also set and removed from the external nozzle cleaner to ensure easier nozzle maintenance.
- Self-recovery and self-diagnosis functions are realized through nozzle health care & feeder maintenance warnings. This maintains correct and continuous nozzle and feeder status nozzle and feeder along with high-quality production.
- IT option - Production Setup Verify ensures quality via barcode checks during component changeovers and refills. It also handles Material Time Limit Management & Bin Code Management tasks.
M2M solution that supports innovative traceability and easily analyzes causes of defect occurrence without requiring any special operator skills
- IT option traceability function utilizes ID information during component verification to identify the range of the defective lot.
- ALL Image Tracer saves images during component recognition and applies factor analysis to them when a defect occurs. Images from the side-view camera can also be saved.
- Dashboard analyzes the operating rate and mounting quality to support better productivity and quality. N-point collation function linked to the YSi-V and All Image Tracer help to swiftly identify the cause of defects.
Promotion Movie
Related contents
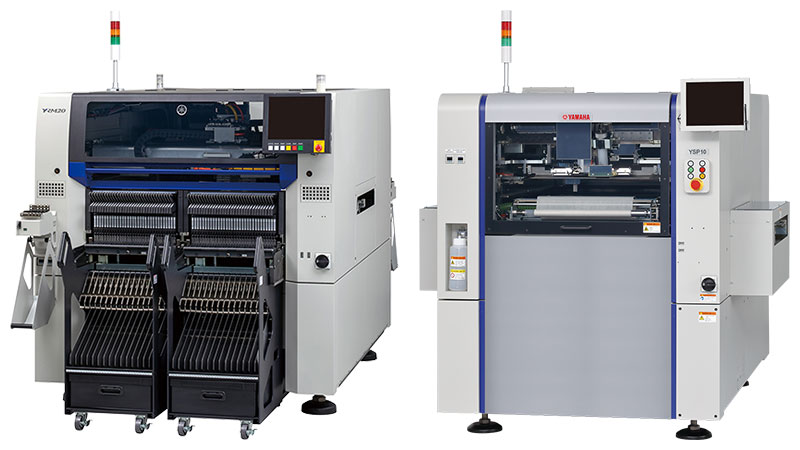
- Product
- Introduce our product lineup, including surface mounters, solder printers, and visual inspection machines.
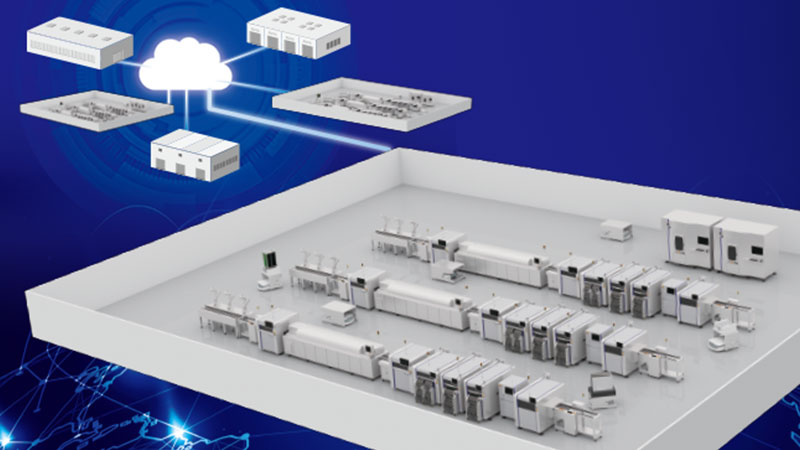
- Showroom
- Find and explore SMT Smart Showroom or Virtual Showroom
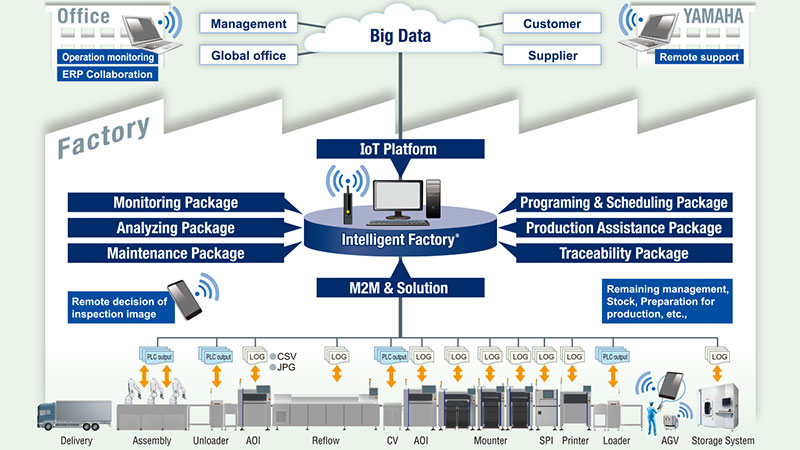
- Intelligent Factory
- IoT/M2M Integration system - System allows linking our SMT machines to equipment made by other companies and give all-around high productivity in the mounting process.