Satisfaction on the production floor. Quantity x Quality x Labor-saving: SMT solution
Here are various SMT solutions that can be realized by adopting a production floor consisting of Yamaha’s SMT equipment.
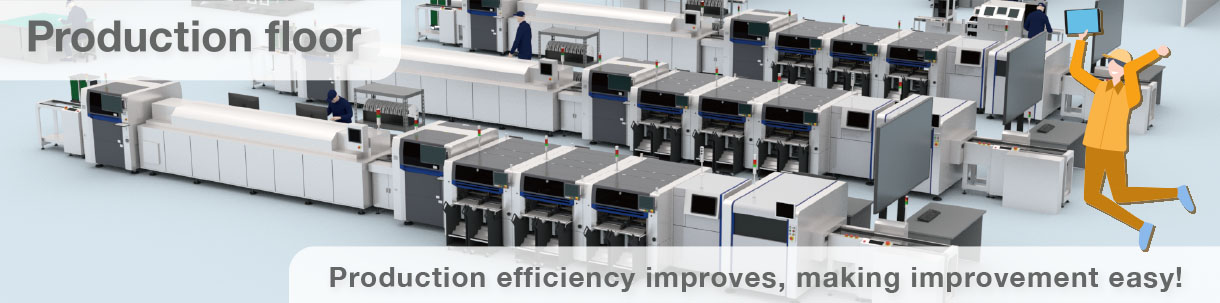

Flexible inspection lineup to matching production styles
Are there times when you want to perform inspections to ensure production quality but the cost is prohibitive?
Yamaha offers a wide variety of inspection options to suit the quality you require without threatening your budget.
A wide range of inspection machine lineup
Inspection machines offer many optional settings for both AOI and SPI, forming the heart of the 1 STOP SMART SOLUTION.
You can choose options according to the needs for your line, such as an economical combination of just 2D inspection for AOI and one projector for SPI, or a fully equipped high-performance option.
3D Hybrid Optical Inspection System YRi-V

3D High-speed Solder Paste Inspection Machine YSi-SP

Printer: Low-cost inspection solution with built-in SPI
If inspection machines lie outside your budget and you cannot adopt SPI, or do not have the space for SPI, we can propose a built-in SPI for printers. By putting a designated camera inside your printer, you can even perform solder printing inspections at low cost.
Built-in SPI for printers

Automatic feedback system

Features linked to visual inspection support system
Sometimes, a visual inspection support system is used in the inspection process, especially for SMT production for automotive-related PCBs, to raise the accuracy of secondary evaluation. Yamaha AOI can be linked to the products of visual inspection support system manufacturers, to make secondary evaluation more accurate.
Visual inspection support system


Defect sources identified right away: Causes identified accurately and effortlessly
When defects occur, the key point is to respond appropriately to prevent them from happening again.
1 STOP SMART SOLUTION enables you to take efficient and effective steps to put these measures in place.
Identifying the cause of a defects by comparing images from each process
When defective PCBs were found after reflow, production has been hard to improve because it has been difficult to identify which process was responsible.
To speed up improvement, 1 STOP SMART SOLUTION can compare images from all processes and identify which process started to show defects.
Process Correlation

[Example of identifying the source of a defect]
Foreign object found on components
[Cause]
The cause was the foreign object sticking to the components from the beginning.
[Measure]
Feed back the finding to the component manufacturer

[Example of identifying the source of a defect]
The components were upside down
[Cause]
The defect was identified to have happened when the reel was switched.
[Measure]
Training conducted again on splicing.

Identifying the causes of defects from data
To help you identify the cause of defects, 1 STOP SMART SOLUTION enables you to identify relationships between equipment from huge volumes of log data output from the equipment. One example is the SPI can detect a tendency that the amount of solder is decreasing when the rolling diameter of the printer becomes smaller.
Analysing Dashboard

Preventing defects by linking inspection machines and mounters
Sometimes defects are suddenly seen to happen one after another during production.
Because Yamaha links the mounter and AOI, if a defect is detected, the mounter that generated it is instantly stopped, preventing more defects down the line and helping you identify why the defect occurred.
QA option

Related contents
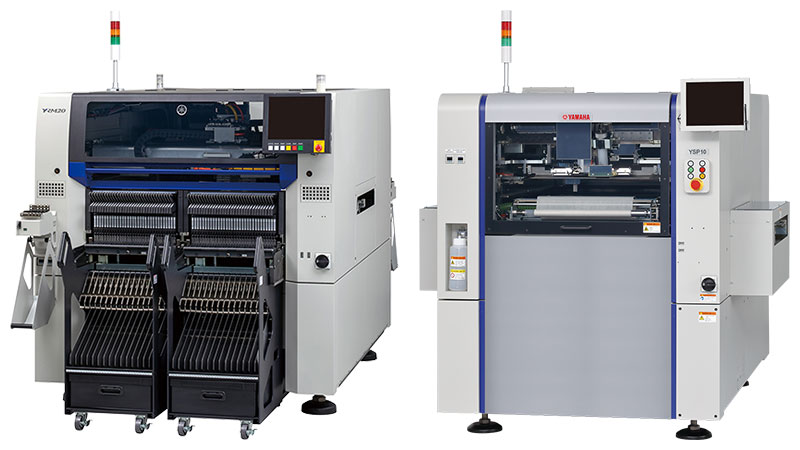
- Product
- Introduce our product lineup, including surface mounters, solder printers, and visual inspection machines.
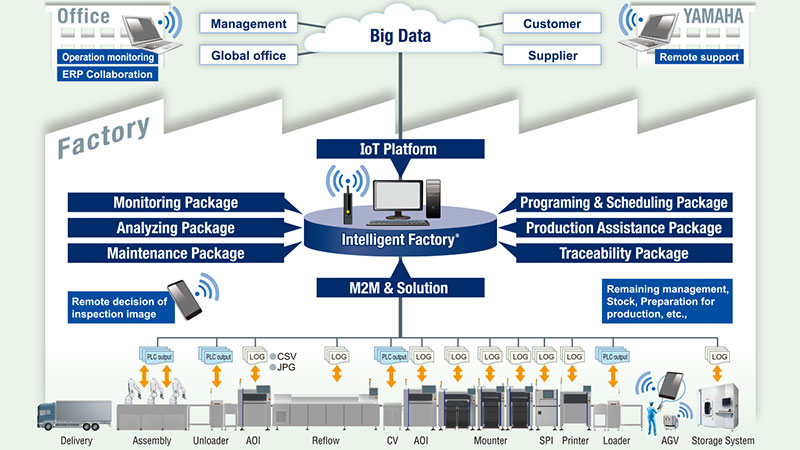
- Intelligent Factory
- IoT/M2M Integration system - System allows linking our SMT machines to equipment made by other companies and give all-around high productivity in the mounting process.
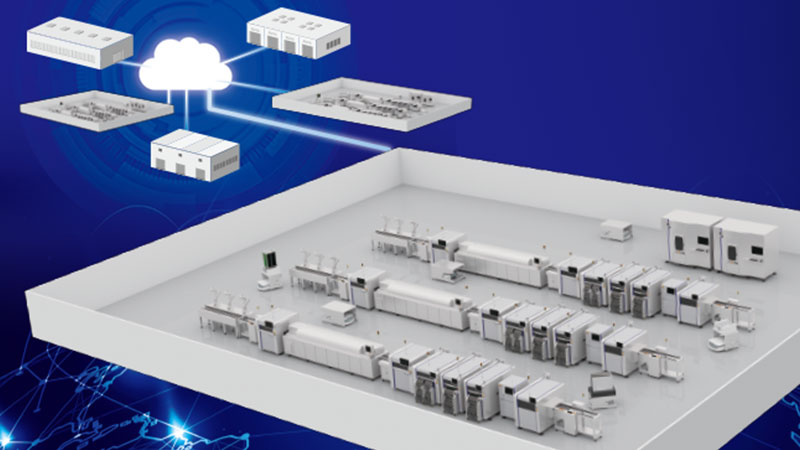
- Showroom
- Find and explore SMT Smart Showroom or Virtual Showroom

- Model Lineup
- The following showcases our lineup of models that solve customers' issues.