Our History of Casting Vol. 6 - Strong Personnel and a Strong Company
Manufacturing is the cornerstone of Yamaha's business and we continue to refine our casting technology. This is the story of how these technologies join the present with the future.
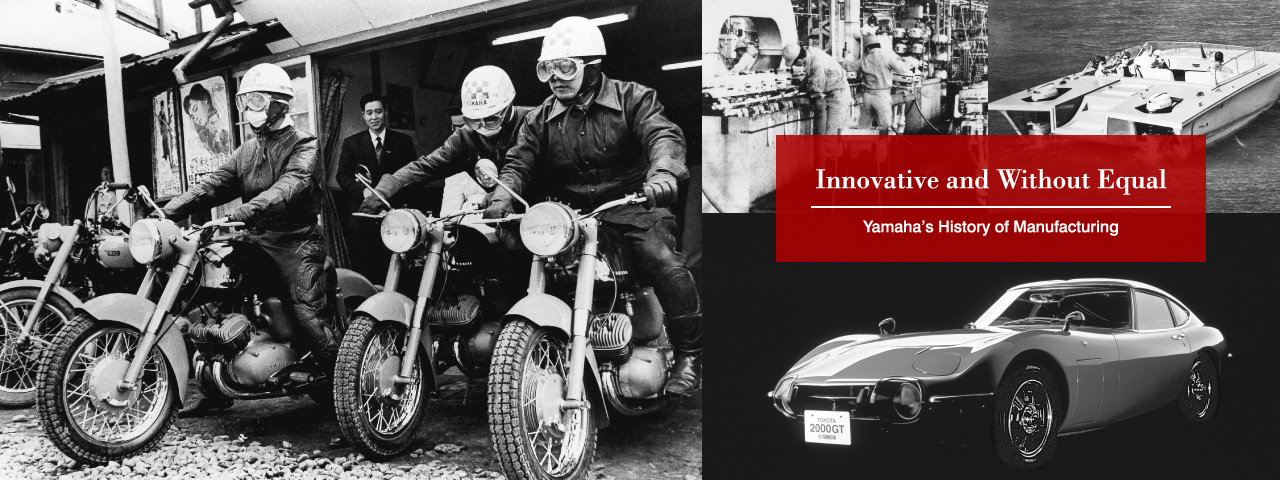

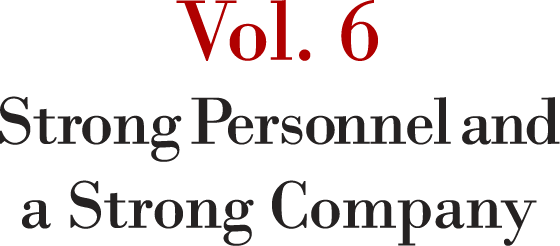
Forming the Basis for Global Development
To demonstrate its Monozukuri as world-class,
Yamaha Motor has actively endeavored since its founding
to be a player on the world stage.
However, it is against the nature of Yamaha's casting engineers
to simply send equipment and molds overseas.
Their way is to always devote great time and effort to the task
because that's what eventually brings lasting success.
Japan's bubble economy had reached its peak in 1989, and just a year later in 1990, the bubble burst and the stock market crashed. For the next ten years, Japan was mired in recession. Domestic consumer spending had essentially frozen and sales of motorcycles and watercraft were in a downward spiral. In spite of these dire economic circumstances, the reason Yamaha Motor's net sales continued to grow was largely thanks to strong sales in other Asian countries.
While Japan was gasping for breath and trying to stay afloat during this drawn out economic downturn, the other economies of Asia experienced a period of strong growth from the mid-1980s to the early ‘90s, and their motorcycle markets in turn had also seen steady growth. Yamaha Motor was already globalizing its operations by that time, and the company's Asia operations in particular were firing on all cylinders. New models were introduced in quick succession, each with its own grand advertising campaign that got people talking. That rapid progress was supported and made possible by the tireless efforts of the company's manufacturing divisions.
The phrase “Monozukuri is Hitozukuri” means that the engineering and manufacturing that goes into creating products is also about the nurturing and development of the very personnel who create them. It is a phrase often heard in the Japanese manufacturing industry, but this saying has special importance among Yamaha's Iwata Metalworking Team. The casting engineers at Yamaha are undivided in their belief that casting is not just about having the right equipment or molds. Only when this equipment is operated by trained and skilled hands are quality, cost and delivery requirements met and subsequently improved. This belief is no different when it comes to establishing casting operations overseas either.
In July 1996, Yamaha Motor established PT. Yamaha Motor Parts Manufacturing Indonesia (YPMI), a motorcycle parts manufacturing facility in Indonesia. Full-scale production of cast parts began the following year. Parts were being cast in Indonesia prior to that time, but that was merely a small part of the wide range of operations―from painting to assembly―performed by Yamaha's overseas production divisions. After the establishment of YPMI, a casting division was established and a dedicated casting factory built, quickly boosting both production volume and quality.
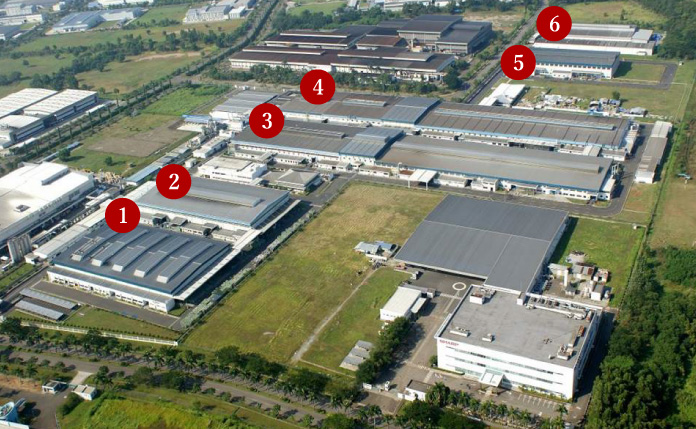
Yamaha expanded its local production and sales facilities while strictly observing the regulations of each country. YPMI was established in Indonesia in 1996, when it was decided to expand the capabilities of Yamaha's local subsidiary (photos 1–6). The casting division was established the following year, increasing both the number of parts produced locally and part quality.
Ever since the company's founding, Yamaha excelled in development and manufacture of 2-stroke engines, known for their low cost, light weight, compactness and high power. However, stricter emissions standards and greater concern for the environment prompted Yamaha to switch to producing 4-stroke engines for developed countries from the mid-1980s. By the mid-1990s, the transition to 4-stroke engines was also taking place in the countries of the ASEAN region. The impetus for putting a casting factory in operation in Indonesia came from the need to quickly switch to 4-stroke engines and raise the level of production. This step was also necessitated by the need to abide by laws and measures put in place by ASEAN countries at the time to increase the percentage of locally produced items.
The Iwata Metalworking Team maintains a strong group consciousness to ensure that each Yamaha overseas manufacturing base has the exact same level of Monozukuri as the “mother factory” in Japan, and that includes using the same level of casting equipment as Japan. By ensuring that the casting equipment in each country meets global standards, those factories can use molds made in Japan without any modification, use the same metal materials and use the same casting methods. This means that regardless of whether a part is made in Japan or overseas, each factory can cast parts with the same high level of quality. In establishing YPMI, Yamaha made a concerted effort to acquire the export license needed to export the equipment, with representatives making frequent trips to the Ministry of International Trade and Industry in Tokyo.
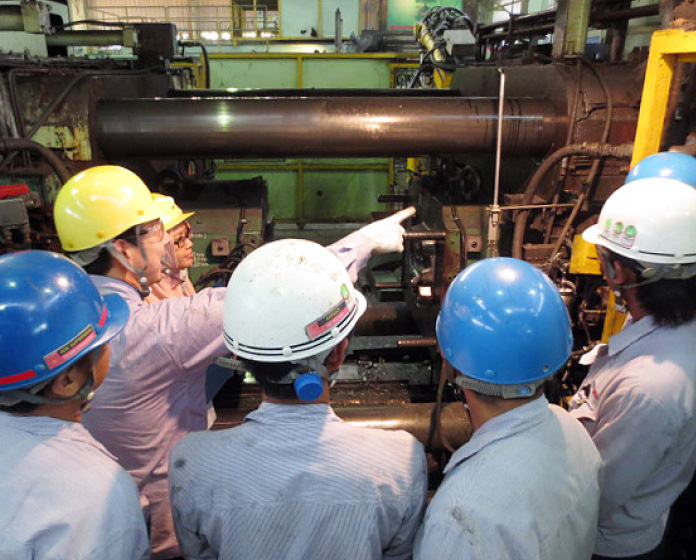
Yamaha has always taken great pains to train and nurture personnel for the casting factory. New technologies and Monozukuri practices are adopted through the enthusiastic efforts of the local workers as globalization of quality manufacturing forges ahead.
While this and other tasks to establish the factory in Indonesia entailed a tremendous amount of work, Yamaha put even greater resources towards training the personnel. “The most difficult task was Hitozukuri, training the factory workers,” recollects the Yamaha employee charged with setting up the factory. “We could bring the equipment and molds from Japan and put them into operation in Indonesia; that's somewhat straightforward. But the most important task was training the Indonesians to be skilled operators of the equipment. We spent a lot of time and effort training people.” The Indonesian people were eager to study and master the technologies and Monozukuri mentality they had never known before. They absorbed the Japanese Monozukuri spirit with enthusiasm and made it their own.
Yamaha has long been committed to training its personnel. Motorcycles—like many of our other products—are complex machines that continuously demand time and skill to build, as does actively developing and implementing new production technologies. But we know that it is people that must master these technologies and put them into practice, so we put the same level of dedication toward training and developing them as well. This attitude also extends to the development of our overseas operations.
When it comes to enhancing Monozukuri at our overseas bases, it is not Yamaha's style to simply set up the equipment and then leave the rest to the locals. Japanese technicians are sent overseas to hold technical training classes, or staff from the overseas factory are sent to temporarily live in Japan in order to learn the relevant skills and technologies at the Iwata Main Factory or at equipment manufacturers. Such initiatives require significant time to reach completion, but like how fertile soil eventually results in prize-winning produce, this method of training personnel leads to solid results in the end. Back when first establishing YPMI, the young Indonesians that learned so much back in the mid-1990s are now in key positions, from department manager to factory foreman, standing as living proof of how they successfully led Yamaha Motor's growth in Indonesia.
In addition to the Indonesian casting factory described here, Yamaha Motor has had similar success with this initiative in Brazil, China, France, India, Taiwan, Thailand and Vietnam. The background and reasons that led to the creation of each factory differ by country, but every factory is capable of producing high-quality cast products. To that end, Yamaha heavily emphasizes the training of personnel in these countries too.
Casting technology is ultimately something made possible by people. “No matter how advanced standardization and automation become, the quality of a finished cast product depends on the skills of the people doing the work,” says one Yamaha casting engineer. “This is true not only for casting, but for any job in the manufacturing industry; things often end up coming down to the people. If people are responsible for a defect, they also deserve the credit for producing excellent products. Nowhere is this axiom truer than in the casting world. If the people are talented, the company is also talented.”
After Yamaha Motor established YPMI, it set up the casting factory in 1997. However, this was the same year that the Asian financial crisis began in Thailand. This currency crisis spread very quickly, dealing a heavy economic blow to the surrounding Asian countries. Yamaha was no exception and was also affected by the extreme up-and-down swings in business conditions, and the volume of cast parts began to fall. However, when one door closes another opens; Yamaha saw a new and different path to travel amidst the chaos. Although cast aluminum parts are generally associated with engine parts, Yamaha pushed aside this thinking and looked to bring aluminum casting into the realm of chassis parts―a perfect example of how a strong company becomes stronger. (Continues in Vol. 7)
Our Business
We apologize for any inconvenience caused and we are hoping for your kind consideration.