Our History of Casting Vol. 5 - A Source for Forward Strides
Manufacturing is the cornerstone of Yamaha's business and we continue to refine our casting technology. This is the story of how these technologies join the present with the future.
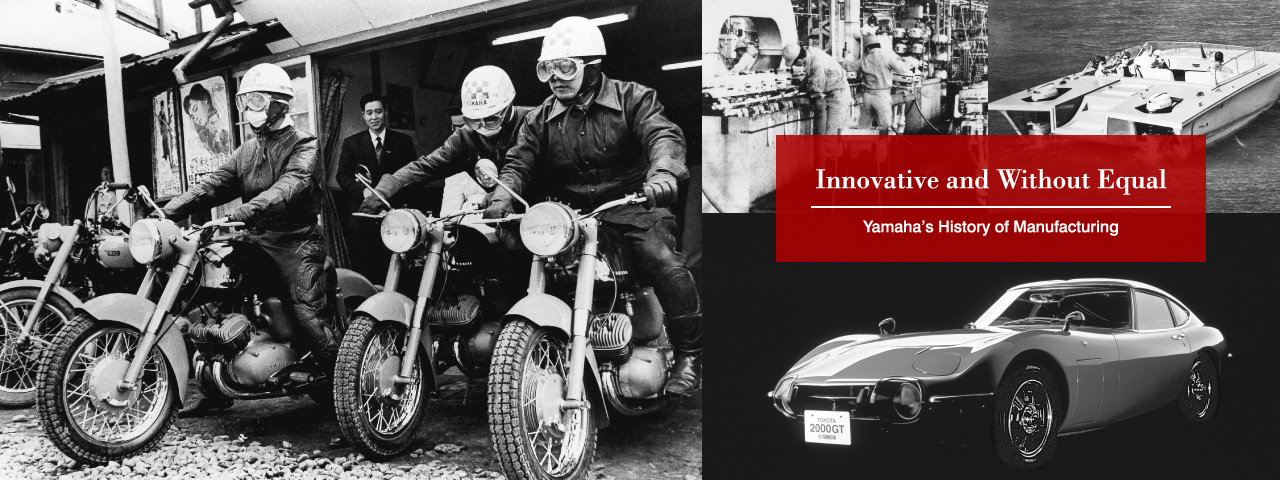

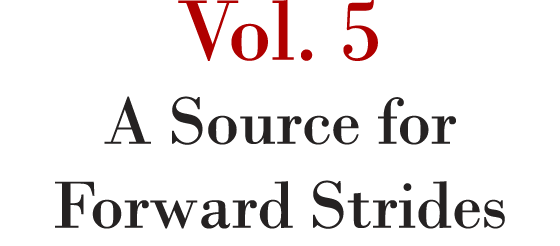
Always Remembering to Review and Revise
From motorcycles on the land and outboards on the sea
to industrial-use unmanned helicopters in the sky,
Yamaha Motor continued its rapid progress, with automation
and mechanization evolving to meet the era's demands for greater efficiency.
However, Yamaha's casting engineers never forgot their roots:
the wealth of knowledge and experience their predecessors earned
through their sweat and toil―a priceless treasure.
Yamaha's casting factories are a vast repository of accumulated wisdom and experience. Some of this knowledge is neatly and systematically organized, while some of it seems to be random and scattered. Much of it shines brightly, clearly lighting the path to follow, while other knowledge appears mundane and without purpose.
But later―be it days, months or years―when this mundane-appearing knowledge is reexamined, it may too be what illuminates the solution to a complex and vexing problem. What looks like a normal factory building is in fact one of Yamaha Motor's greatest treasure troves. Here, among the myriad of successes and failures resides the heart and soul of Yamaha's casting technology.
By the mid-1980s, the wave sweeping the manufacturing industry to standardize and automate slowly but surely began reaching the casting factories, all in the name of greater precision, higher quality and increased efficiency. However, the complex designs and advanced casting techniques involved to create Yamaha's 2-stroke engines―the company's specialty since its earliest days―or its outboards that were starting to win worldwide acclaim, the car engines praised for their high performance, or the company's groundbreaking DOHC 5-valved 4-stroke engines meant automation would be no easy task. From the outset, casting has always been a natural phenomenon difficult to control or master with human intellect alone. Skilled casting technicians must hone their intuition and learn the tricks of the trade through years of experience.
For example, to create an updated mold for the cylinder head of a 2-stroke engine is a difficult and time-consuming task. Even slight deviations in the shape of the intake or exhaust ports can significantly affect engine performance with a 2-stroke. So it was rather common for engine designers to personally visit the factory for “on-site adjustments,” shaving away portions with a deft hand to get just the right shape for the mold. In other words, the resulting shape would determine the engine's very performance in ways blueprints could not.
The casting engineers would also often end up frustrated with their heads in their hands after conversations with the designers about creating the updated mold:
”Use this blueprint as a reference for the port's inlet and outlet shapes,” the designers would say.
”But what about the mid-section?” reply the engineers.
”The mid-section? Just make something cool.”
”And how are we supposed to do that?”
”Just make it like the existing one.”
But if they did make the updated mold exactly like the blueprint, the engine wouldn't produce the performance it was designed for.
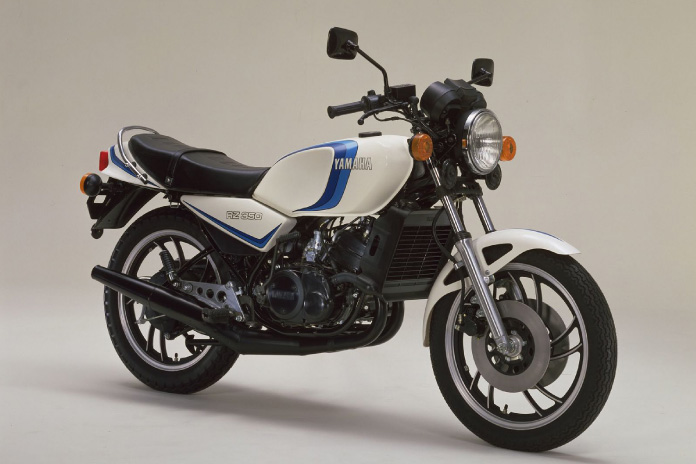
The slightest differences in the shape of scavenging ports on a 2-stroke engine can greatly affect its performance, and the skill required to shape them—akin to craftsmanship—was passed on from one engineer to the next. These engines were a Yamaha specialty since its beginnings, and the RZ350 released in 1981 had such incredible performance that it was nicknamed the ”nanahan (750cc) killer” in Japan. As it went on to win fans around the world, it helped trigger a popular revival of the 2-stroke sport bike category.
The same was true for the complex shapes of outboard motors. It even got to the point where the engineers were told that the outboard's performance would be up to the wooden mold maker. Loose piece patterns were also used for undercut shapes so that they could be removed from the mold after casting, and they were set in place manually. In those days, engineers from other companies often chided Yamaha's outboard motor casting engineers: “It's actually quite remarkable that you all actually use such an awfully inefficient manufacturing process.” But that was simply the only way to cast the shapes an outboard required.
Used in the company's diverse range of products for the land, sea and air, Yamaha's cast parts all present their own unique challenges, and it's here that Yamaha's veteran technicians put their many years of experience on the factory floor to work.
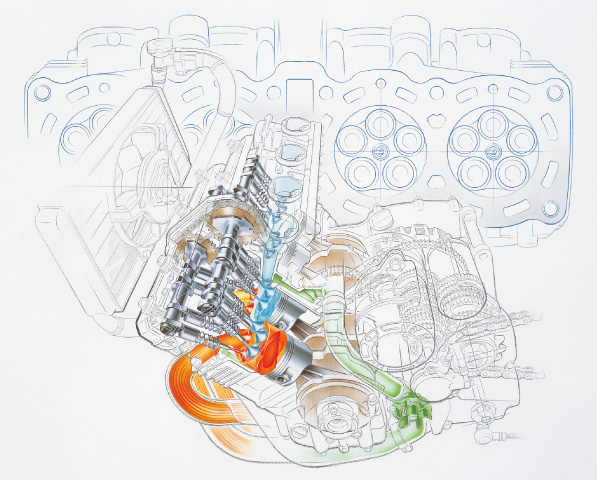
The FZ750 that debuted in 1984 featured an in-line 4-cylinder DOHC engine with five valves per cylinder, three for intake and two for exhaust. This system yielded excellent intake efficiency and the bike delivered high performance across a wide range of use, from racing to the street. The five valve format it adopted was the result of many years of R&D and was representative of Yamaha Motor’s firm determination to assert dominance of the 4-stroke engine itself.
Yamaha eventually began full-scale development of 4-stroke engines. The FZ750 supersport model unveiled in the fall of 1984 was the flagship of Yamaha's 4-strokes, packing an innovative DOHC engine that used five valves per cylinder. Featuring three intake valves and two exhaust valves, this design resulted in a bi-convex combustion chamber with an almost ideal shape in addition to a host of other benefits. To create this highly complex cylinder head, Yamaha's casting engineers could no longer rely on just their skills and intuition. Even when they made the mold exactly as stipulated in the blueprint, they just couldn't achieve the combustion chamber volume the designers were aiming for. As 4-stroke engines required an exceptionally high level of engineering precision, success was less dependent on their keen senses as master craftsmen and more on concrete logic to achieve the numerical targets―shifting over to 3D data modeling had finally become an industry necessity.
This was the era when higher-performing computers began to dramatically enhance analytical techniques. However, even with the most powerful analytical tools, a vast number of parameters for examination must be set in order to determine the best solution for making complex castings. Each time you change a parameter value, you have to carefully check the resulting phenomenon caused by those changes, eventually finding the values that work best.
It was exhausting work, but the engineers who methodically unraveled these convoluted problems built the foundations for Yamaha’s casting analysis methods. When this analysis process first began, computers were still slow and many of the factory workers had little faith in their effectiveness. “You really think that thing has the answer?” they would say, full of doubt. In fact, in those days it took around two weeks to perform the analyses for just one model.
A term often heard at Yamaha casting factories is the “one-shot percentage,” meaning the degree of success had with the first try. The closer to 100% it is, the more likely the preparations for production will be efficient. In the early days of computer-based analysis, the one-shot percentage was in the 40–50% range, leading many engineers to criticize the digital devices since creating the actual molds instead was faster and straightforward. Still, rapid advances in CAD/CAM technology markedly improved efficiency on the design side, so it was only a matter of time until 3D modeling, computer analysis and automation would become indispensable even in the casting factories.
Engineers at Yamaha Motor are always drawn to the “latest and greatest,” and their innate curiosity regarding these new methods was another factor driving greater implementation. However, they also always value real experience gained on the factory floor, and didn't forget to ensure it was conjoined with these new methods. It was thanks to this that computer-based analysis didn't simply become “technology for technology's sake.”
Casting is a natural phenomenon not easily controlled by human intellect. This is a fact Yamaha's casting engineers are constantly aware of. They declare that “Casting is really tough to figure out!” or “Casting seldom goes well without a hitch,” but they then say with a grin, “But that's what makes it so interesting and worth doing.” As time passes and products take on ever more complex shapes and forms, it falls on the casting factories to boost efficiency to meet the demands for greater precision but with lower costs. The first attempts to meet such challenges are fraught with problems and casting flaws are inevitable, so Yamaha develops new casting methods to solve them. This endless game of “cat and mouse” with the natural phenomenon of casting continues without letup, a process that stimulates the engineers' intellect as they absorb themselves in challenges that result in ever newer and more efficient techniques. And although casting is not entirely controllable by human intellect, it is the skills and insight of those baptized by the heat of the furnaces that makes these breakthroughs possible.
On one occasion, a group of young engineers were using low-pressure casting to create a 2-stroke engine's combustion chamber. But no matter how many times they tried, they couldn't get the molten aluminum to solidify properly, even when they increased the pressure. In the end, the mold turned red hot, the shell fell apart and the molten aluminum spilled out. They couldn't understand the problem. Seeing the young engineers scratching their heads and frowning at their predicament, one of the senior engineers told them, “The melt doesn't necessarily rise in the two fill stalks at the same time. Since there's a slight difference in resistance between them, convection occurs due to gravity and the different temperatures of the melt, so increasing the pressure likely won't cause it to solidify. That's the only possible explanation.” This reasoning was hard for them to simply see in their heads, but when reexamining what was actually happening and then working backwards from it, they realized the advice was spot on, and later solved the problem. Although the senior engineer could not actually see what was occurring inside the mold, he was able to visualize what was happening and ascertain what was wrong. Examples such as this occur frequently in the casting factory, and at times like this, the seniors appear more like magicians than engineers.
Because even the most experienced casting engineers cannot see exactly what is occurring inside a mold, they must rely on their intuition and experience, which in most cases proves correct. With the passage of time, casting has become more mechanized and more automated, but the fundamental task of filling a mold with molten aluminum and making it solidify into a desired shape remains unchanged.
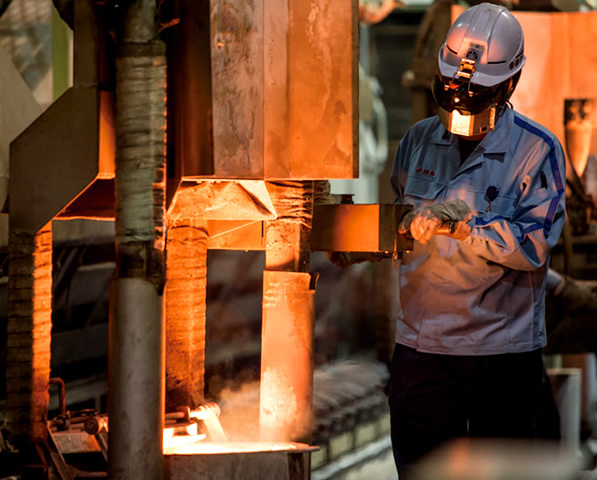
There is an ever-present philosophy at Yamaha’s casting factories: a difficult challenge is not something to be shunned, but to be sought. It is a steady resolve and passion to ”get it done” that drives the engineers and technicians as they run repeated and intricate processes of trial and error. There is knowledge and experience to be had from both success and failure, and it is with those fruits that they move toward making the next step, and the step beyond that. The Yamaha belief is that this insatiable desire to improve should remain unchanged, even as eras come and go.
The answer to every question lies in the casting itself, not solely on a computer screen, and spending time closely examining the cast piece itself is what tells an engineer what needs to be done. In the words of Yamaha Motor founder Genichi Kawakami, “Give utmost importance to raw materials and metalworking.” Yamaha Monozukuri is now and has always been based on viewing and understanding the realities of casting.
Steady increases in computing power resulted in improvements to analytical techniques and automation was implemented wherever it fit the job. This has continued since the mid-1980s and unsurprisingly, the one-shot percentage has also risen substantially. Casting large parts such as motorcycle frames is now a casting engineer's stock-in-trade, and casting technology and techniques continue to evolve. Nevertheless, the engineers at Yamaha Motor continue to draw on the extensive repository of accumulated experience and wisdom. Amongst its countless “shelves” lie shining successes and frustrating failures, but they are all experiences of priceless value earned by the sweat and tears of generation after generation of Yamaha casting engineers. (Continues in Vol. 6)
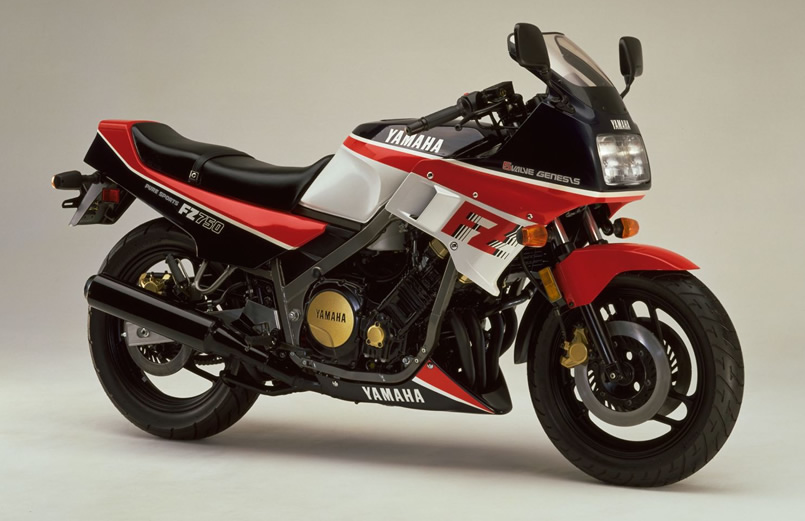
Our Business
We apologize for any inconvenience caused and we are hoping for your kind consideration.