It goes without saying that when small things are enlarged, they reveal hidden aspects or traits not easily discernable. But there are also certain qualities that only show themselves when performing the opposite. An example of this is the many days that were devoted to creating a precise 1/6-scale miniature replica of the iconic SR400’s fuel tank. This project not only renewed the team’s appreciation for the iconic SR400 but also became a pleasant pursuit to rediscover and reevaluate the machine’s place in history.
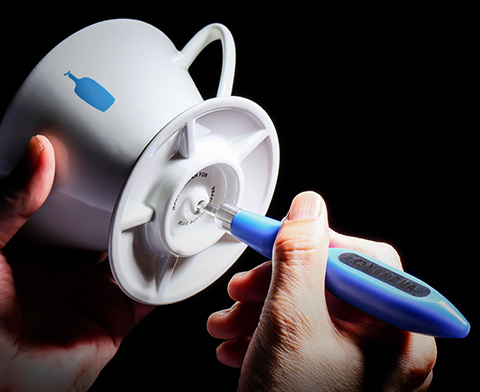
Seeking Techniques for a Faithful Reproduction
After 43 unforgettable years, production of the widely loved SR400 unfortunately came to an end. In response to SR enthusiasts voicing their desires to keep the bike’s beautiful fuel tank with them somehow as a memento, a project was devised to manufacture a miniature replica of the classic naked’s tank. However, since Yamaha Motor is where the tank originated from, recreating a faithful replica covering all the aspects that made it special would be an extremely challenging undertaking. Accordingly, it was brought to the manufacturing technology departments with the following request: If we’re going to be the ones making it, we want to aim for exacting precision with this replica and its exterior.
One engineer said, “I knew for sure that conventional manufacturing methods wouldn’t suffice.” At first, it all sounded quite straightforward and they enthusiastically accepted the task, but it took some time for them to realize just how challenging it would be to clear the requirements for a faithful reproduction 1/6th the size of the actual tank.
What stumped the engineers were the subtle curvatures on the upper surface of the SR’s tank. The slight bulge just in front of the fuel filler cap is hard to see even with the naked eye. “Aiming for exacting precision” meant that even such details were part of the request. In that sense, it was natural for the engineers to conclude that the usual approaches wouldn’t do the job.
Needless to say, the material used for the replica is the same as the one used in the original: SPCE-grade steel, a galvanized, cold-rolled steel well suited to deep drawing applications and adorned with a zinc-plated finish. The same simulations as the full-size machine were used to examine the folds produced during pressing, and this led the team to make some alterations to the design and to select a thinner steel.
That’s not all; the engineers were dedicated to using the same manufacturing processes as the original for the miniature tank’s individual parts and machining. The main components consist of the left and right sides and the single panel forming the bottom. Hardcore SR fans know that the left and right panels are asymmetrical, and that too has been faithfully replicated.
Still, no matter how many simulations are run, when a hydraulic press forms these three panels, small wrinkles can form depending on the strength and angling of the steel. While creating prototypes for the replica tank, minute vertical creases appeared on the front and upper surfaces.
This is where the skills of Yamaha’s craftsmen came to the rescue. Changing the shape of the tank ever so slightly—to a degree essentially imperceptible to anyone—would make the wrinkles disappear. However, this “shortcut solution” was unacceptable to the craftsmen. Instead, they would have a scrap section of the workpiece absorb the wrinkles and cut it off after pressing was complete. To make this work, this section of the workpiece was repeatedly redesigned until it properly served its purpose in a fix the team could accept.
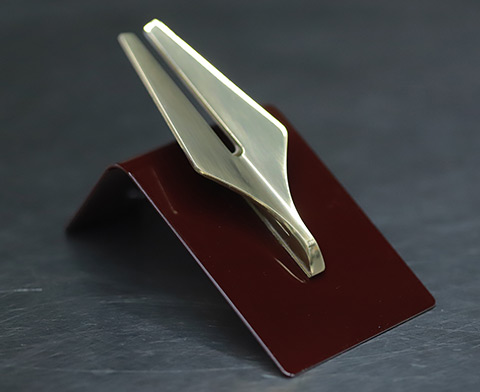
A Teardrop Resting Quietly in Your Hand
In this way, the left and right outer panels and the bottom inner panel were fashioned. The next task was how to join the three pieces together.
On the full-sized tank, electric resistance welding and arc welding were used, so of course, those techniques were tried, but the different thickness of the sheet metal used resulted in deformations in the various test pieces. After studying the problem—and putting the highest priority on the quality of the final product—it was decided to forgo using the original welding methods, and the team instead repeatedly tried brazing, soldering, and a number of other methods to join the pieces. In the process, the engineers arrived at a method that satisfied all their requirements for both strength and exterior quality: utilizing a special gun to join the pieces with construction-grade metal adhesive.
It was a joining process requiring both time and patience. When it was done, the SR’s beloved and all-too-familiar teardrop tank finally took shape. The joints were then carefully sanded and polished and all that was left was the painting process.
However, the extra touches that define Yamaha Motor Craftsmanship are hidden. The project demanded that even the flange where the pieces interconnect be exactly the same as the original. The press process intentionally lays the flange down at a -15° angle and a jig was specifically prepared to hand-form it into the proper shape. If you get a chance, closely compare the details of this miniature tank with the full-size original. You will see the extra efforts made by Yamaha’s engineers to ensure that even the 1/6-scale flange has this slight angle.
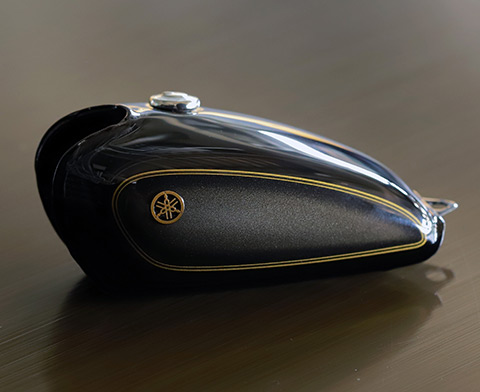

Sunburst Paint Design Recreated with Water Transfer Printing
Once the miniature tank was fully assembled, it was taken to the same paint shop that was responsible for the original bike. The first step was to apply a chemical conversion coating, over which what we pride as being our best black paint was sprayed—Yamaha Black. To recreate the sunburst paint and pin striping, the water transfer printing graphic featured on the SR400 Final Edition Limited was used. There are only three craftsmen at the Yamaha paint shop that have acquired the skills needed to apply these graphics at a level satisfactory for complete products.
These highly experienced and multi-talented craftsmen deftly swap between their hard and soft squeegees with practiced proficiency to remove the water from between the transfer and the tank and erase any wrinkles. Years ago, these same craftsmen were the ones that applied a graphic of Valentino Rossi’s signature atop the fuel tanks of a special limited-production batch of YZF-R1s.
“Some distortions are so minute that only I can pick them up, and certain wrinkles can be entirely invisible to others,” says one of the specialists. Passing the squeegee smoothly and with equal pressure over the very thin film, she makes it conform to the curvature of the tank, and there is no pausing or hesitation in how her hands move. “The difficulty is what makes it interesting,” she explains before changing the angle of the light to perform a visual confirmation. “And more than anything, it’s beautiful to the eye.”
●
Only a limited number of these scaled-down SR400 fuel tanks were produced. The team of engineers were of one voice when looking back on the project, stating that the process of making something small like that helped them rediscover and relearn a great deal. “Back in 1978 when the manufacturing devices available were limited and machining techniques were not nearly as advanced, the fact that our predecessors were able to create such a beautiful tank gave us a renewed appreciation for their knowledge, skills, and dedication.”
