Though most patrons will not give it too much thought, the construction and shape of this dripper for Blue Bottle Coffee is the result of a dutiful application of the laws of physics. To produce a delicious cup of coffee each time, the forty ridges ensure a steady flow of coffee at the ideal speed down to the single hole at the bottom, with the shape carefully crafted and fired in a pursuit of both beauty and precision by masters of Arita ware porcelain. The material is beautiful as well as delicate and helping inspect the work of these artisans down to 1/100 mm levels of precision is Yamaha’s prototyping factory and our craftsmanship spirit.
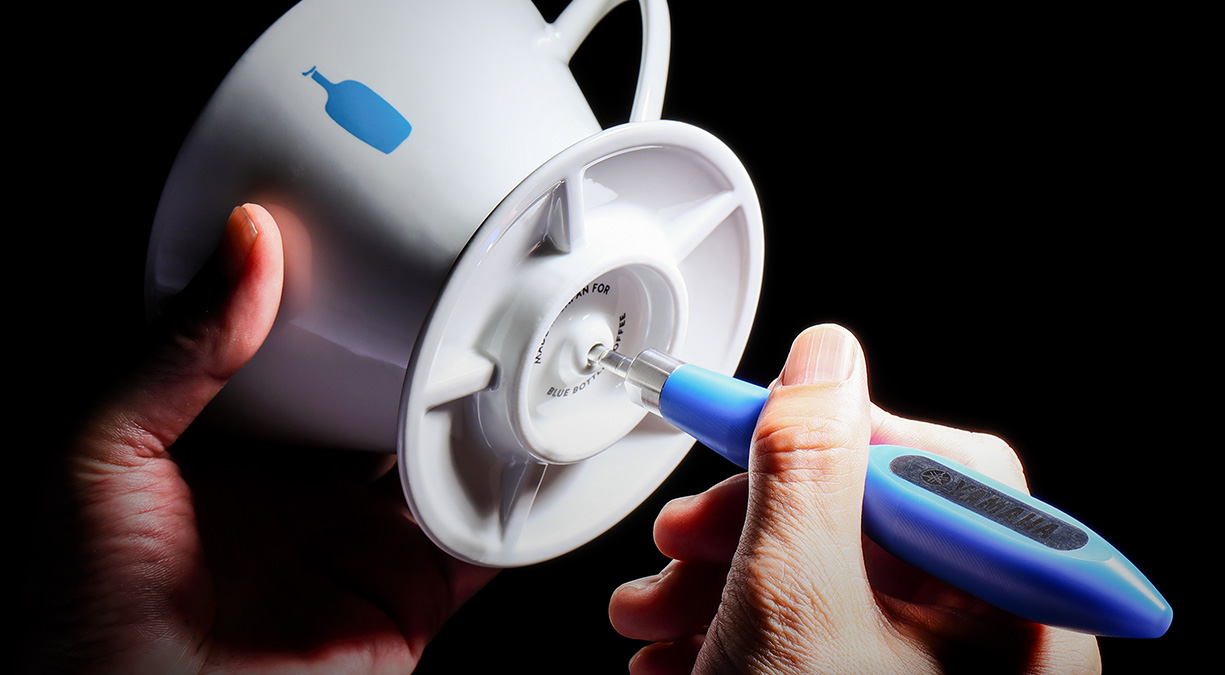
A Place with No Boundaries or Limits
Those at Yamaha Motor’s prototyping factory often speak of “alpha value,” a traditional term they coined and use in conversation. “We create things the world has never seen. And if we can’t do something now, we work at it until we can, and once we can, we rack our brains and put in that extra effort to make it even better,” says one of the craftsmen. “The unique joy of our jobs here building prototypes lies within all of that. The ‘alpha value’ we’ve long spoken of here is essentially synonymous with ‘Yamaha Motor Craftsmanship.’”
The prototyping factory performs two critically important tasks in Yamaha’s manufacturing operation. The first is producing prototype parts for R&D while the second is building prototypes to prepare for mass production during product development. Whether it’s the former or latter, for Yamaha’s product developers, the facility is an irreplaceable part of the process for bringing forth all-new creations. The prototype parts crafted here eventually become the basis for final part blueprints, thereby playing a pivotal role in raising the value of the end product.
When it comes to the requests or consultations that arrive at the factory doors, there are no limits or boundaries for the field in question or degree of difficulty, hence all manner of Monozukuri requests arrive. These range from a creating a single special screw to large, advanced development parts for our MotoGP machines. It isn’t unheard of for some requests to be undeniably outlandish but even those are not refused outright and are given due consideration. Ascertaining the requirements and putting together the necessary conditions is where the pride of these prototyping craftsmen comes to the fore. In order to transform the ideas and requests they receive into reality, these veteran craftsmen have all kinds of materials, machining techniques, and manufacturing equipment at their disposal, which they combine with the company’s deep well of knowledge and experience as well as their own love of Monozukuri.
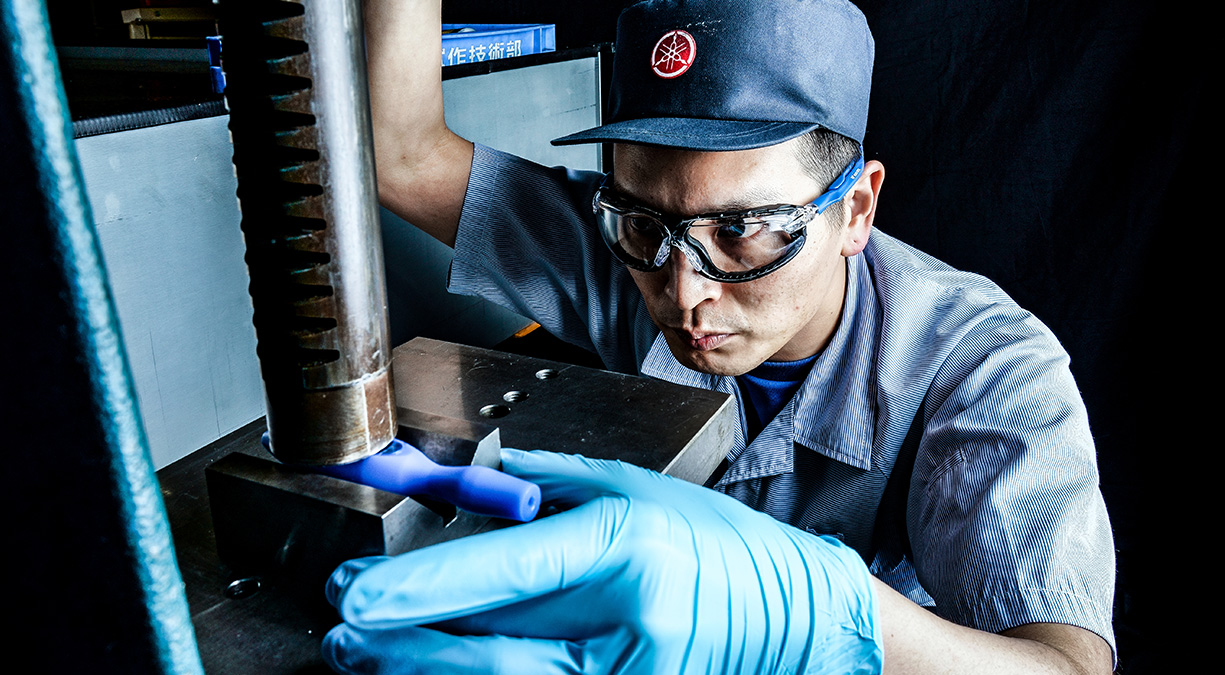
The Recognition and Mutual Respect
Found Among Fellow Craftsmen
“Now that’s interesting.” The prototyping technicians couldn’t help but express their interest during the meeting suddenly requested by Blue Bottle Coffee to discuss an inspection tool for their dripper.
Yamaha’s technicians were undoubtedly drawn to Blue Bottle Coffee’s single-minded pursuit of giving each customer a great cup of coffee, and even more so when they learned that the dripper was crafted and fired as fine Arita ware porcelain. As craftsmen also innately familiar with what constitutes excellent Monozukuri, they could intuitively understand what it took to make the beautiful indigo fluid fall like a fine thread from the dripper. “They had to calculate as well as compensate for the thickness of the glaze as well as the shrinkage from the firing in order to ensure accuracy down to 1/100 mm, and their dedication inspired us to use all the technologies at our disposal to help,” said one Yamaha technician. It was not long before a team of specialists with a wide range of experience was assembled.
Ideas for an inspection tool were brainstormed, studied at length, and many prototypes were made. These were sent to Arita down in Kyushu and the town’s renowned ceramicists provided their frank feedback over days of online meetings. The tool would be used daily by artisans who are continuing a 400-year tradition, and it would not only need to ensure the high level of precision expected of their brand but also be easy to use and thus allow the craftsmen to fully focus on their work. If circumstances allowed for it, Yamaha’s craftsmen wanted to visit Arita in person to see the ceramicists working up close, examining how they used their hands and sharing their observations and opinions. However, the continuing spread of COVID-19 throughout the country made this impossible.
●
Blue Bottle Coffee has locations around the world and each cup of their drip coffee uses drippers crafted of Arita ware porcelain hand-fired in Kyuemon kilns. The thickness of a dripper is often what saps away the heat of the hot water poured in, and to achieve the approx. 3 mm thickness at its thinnest sections in order to meet Blue Bottle Coffee’s quality guarantee, the dripper required a particularly strong pottery stone as well as the traditional techniques of Arita’s famed ceramicists. Blue Bottle Coffee sent an American engineer on a search to create the ideal coffee dripper and he found his way to Arita’s Kyuemon kilns. He eventually settled into the small town of less than 20,000 and worked together with its artisans to create more than 20 sample drippers.
“I was really moved with how far they would go in their dedication for a single cup of coffee,” recalls one Arita craftsman. “The same goes for Yamaha’s engineers. As a man of Monozukuri myself, the way they thought through just about anything and everything with the end users in mind and then demonstrated the technical capabilities to bring the result of that thinking to life was immensely impressive.”
The shape, material, weight balance, and functionality were all important factors considered for the inspection tool, and while it is small and fits nicely into the palm of the hand, it houses not only technologies that guarantee extreme precision but also ideas unique to the prototyping factory as well as the respect given to the fellow craftsmen of Arita.
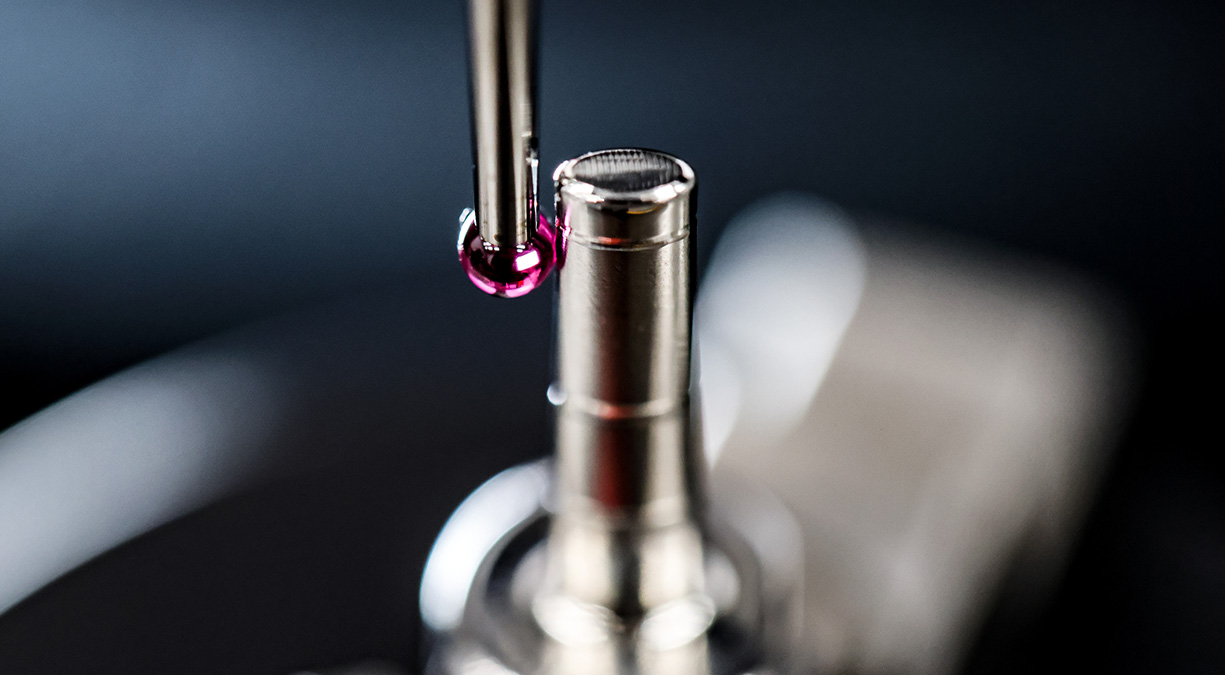
Quality Guaranteed with an Artisan’s Seal
The stainless steel gauge at the tip of the tool is what works to ensure the size of the dripper’s hole has no deviations. After extensive discussion and deliberation of what material would be best, Yamaha selected a precipitation hardening stainless steel that is not just hard but also resistant to corrosion. Its shape conceals a range of machining knowledge and technologies imperceptible to the human eye.
The design of the gauge’s elliptical taper is one such feature. The gauge itself is inserted through the dripper’s perfectly round outlet but making it elliptical is what allows the rest of the gauge to pass through far more smoothly and with little effort. This elliptical gauge is also tapered from its tip down its axis, but the taper angle is so incredibly minute that it is nearly impossible to discern with the naked eye. In addition, the gauge was given two lines to indicate the range of tolerance. If the dripper hole does not pass the first line, it is too small. If it passes the second line, it is too large. In either case, the dripper is not to specification and will not be shipped. Porcelain is such a delicate material that even in the practiced hands of skilled artisans, defects can and do occur. These stringent inspections and quality control stand as the final gate the dripper must pass through to ensure each cup it brews at Blue Bottle Coffee delivers the delicious flavor they promise. Accordingly, the blueprints drawn up for the inspection tool that would guarantee this level of quality control required extremely difficult machining techniques.
First, the high-performance multi-axis machining center precisely carves the gauge’s subtle yet complex shape. It takes roughly an hour just to machine a single gauge. Once the long machining process is complete, the gauge—about the size of one’s little finger—is sent to the inspection room for 3D measurement. The contact-type 3D measurement tool uses a stylus tip that emits a ruby red light and can detect imperfections at the micron level. As it gently traces the outline of the gauge, the corresponding 3D data slowly emerges on a nearby monitor.
“This dripper combines the passion and high demands of Blue Bottle Coffee with the centuries-long tradition and techniques of Arita ware,” explains one member of the Yamaha team. “This high-level collaboration between people who take immense pride in their work is what leads to each delicious cup of coffee. The tool we made for them is like an artisan’s seal that guarantees the level and value of their work. It gave us great pleasure to contribute to such a worthwhile pursuit by applying the full breadth of our prototyping knowledge and technologies.”
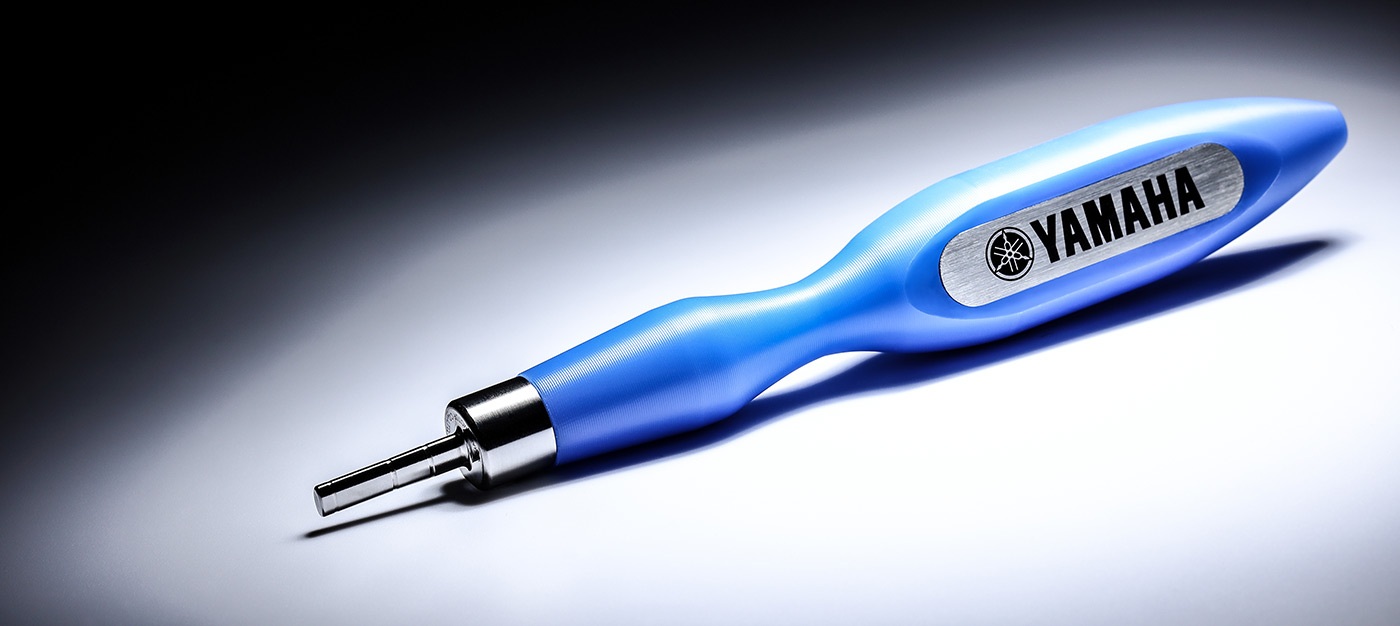
Blue Bottle Coffee
Dripper Inspection Tool
Each Blue Bottle Coffee dripper is made of Arita ware porcelain by Kubota Minoru Ceramics Ltd. and hand-fired in a Kyuemon kiln. This dedicated tool for inspecting the dripper’s outlet size—a deciding factor in the final brew—was commissioned by Blue Bottle Coffee Japan and planned, designed, and produced by Yamaha Motor’s Prototype Technology Division.
Machined for an Ergonomic Shape and Better Grip
Although the gauge section may wear with continued usage over time, the ergonomically designed grip was made separate from the gauge so that it can be reused. The grip is made of MC nylon thermoplastic resin to make it light and provide the right weight balance when in the hand. The various parts of the grip are carefully machined to exacting width and curvature for a natural feel and with grooves to reduce the chance of it slipping while in the user’s hand. The grip area is 12 mm in diameter, making it very easy to hold. To create it, multiple prototypes with different grip angles, weight balances, and more were made and given to the artisans for testing. Their feedback was faithfully reflected in determining the final specifications of the grip.
Cutting Machines Also Making Parts for the YZR-M1 MotoGP Racebike
The gauge section is the principal part of the inspection tool and is shaped with a high-performance multi-axis machining center. It uses SUS630 precipitation hardening stainless steel and is smaller than a little finger once completed, but the machining process itself is quite complex and requires very high precision, thus it takes about 60 minutes to finish one gauge. As the machine cuts away the raw material in a cloudy white high-pressure spray of cutting fluid and the gauge’s final form slowly appears, it is almost as if a new life is breaking free of its shell. This machining center is also used to create advanced development parts and special parts for Yamaha’s YZR-M1 MotoGP machine.
3D Measurement and Friction Wear Inspection Tool to Ensure High Precision
The machined gauge section is measured in three dimensions to ensure quality. These checks continue even after the gauges are shipped to their new home in the hands of Arita ware craftsmen. Yamaha machined grooves into the tip of the gauge to allow frictional wear to be checked visually and also supplied Arita with a wear inspection tool so the craftsmen can perform their own checks for wear and replace the gauge if needed. In testing the gauge’s durability, 25,000 mock inspections were performed and the supplied wear inspection tool revealed an ever-so-slight degree of wear, proving not only the gauge’s toughness but also the tool’s usefulness in ensuring quality remains top-notch.
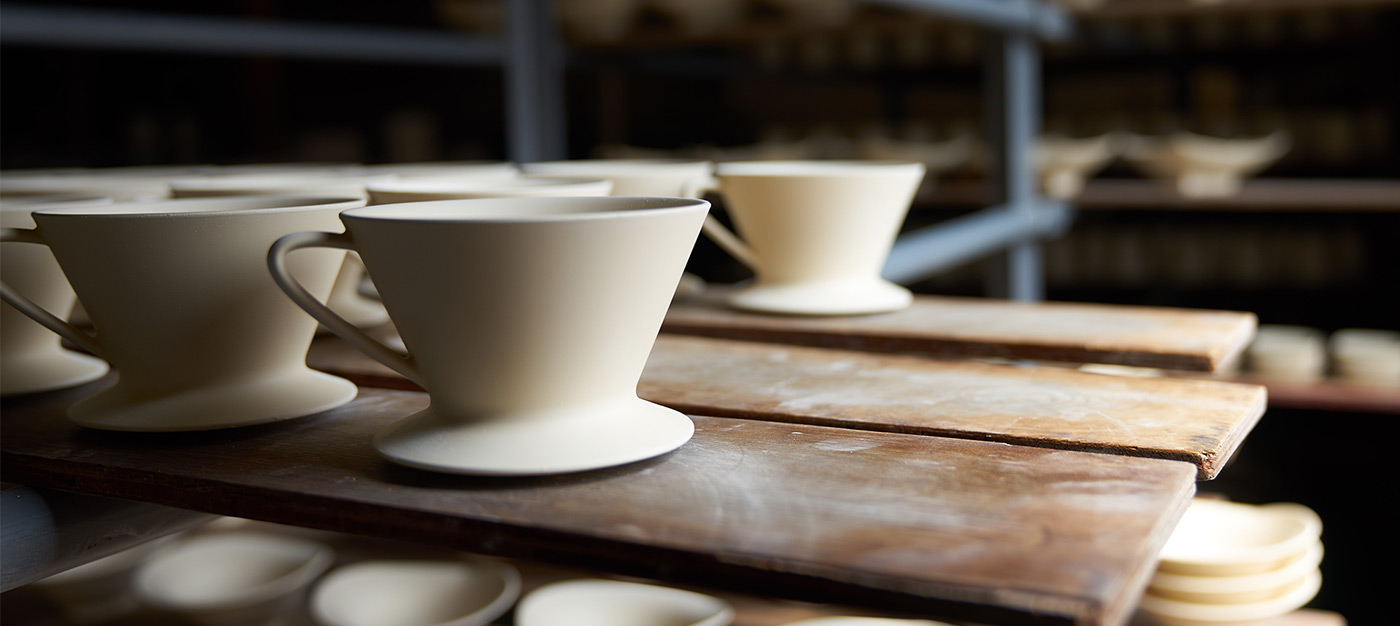