Core of Advanced Robotics Automation Platform Yamaha Motor Launches YHX Series Integrated Controller Superior Scalability - Significant Reductions in Space, Cost, and Setup
October 17, 2016
IWATA, October 17, 2016—Yamaha Motor Co., Ltd. (Tokyo: 7272) announced today that it will launch the new YHX series integrated controller from December 1, 2016, which achieves coordination and synchronous control of all robots and peripheral devices in an automated line in the"Advanced Robotics Automation Platform" integrated control robot system.
The YHX series consists of a high-functionality and high-performance host controller, a driver unit compatible with a wide range of motor controls, a high-capacity power unit which can wirelessly supply the power necessary for multiple axis drive, a remote IO unit which efficiently connects to peripheral devices with a minimum of cabling, and finally a gateway unit which responds to a variety of control needs.
The industry-first*1 stacking structure delivers significant reductions in the space required for the control cabinet, tremendous saving on cabling, and significant reductions in setup time and equipment costs for automated lines.
Moreover, the controller features an internal high-performance PLC*2 based on IEC 61131-3*3, and newly-developed high-versatility robot language. Additionally, flexible connection to various major field networks is possible, and the controller has the flexibility and expandability to work with IoT and Industrie4.0 etc. in the future.
Operation is easy with the full-screen Programing Pad touch panel.
*1 October 2016, Yamaha Motor data
*2 Abbreviation of Programmable Logic Controller a control device modeled on relay circuits.
*3 International PLC programing standard issued by the International Electrotechnical Commission (IEC).
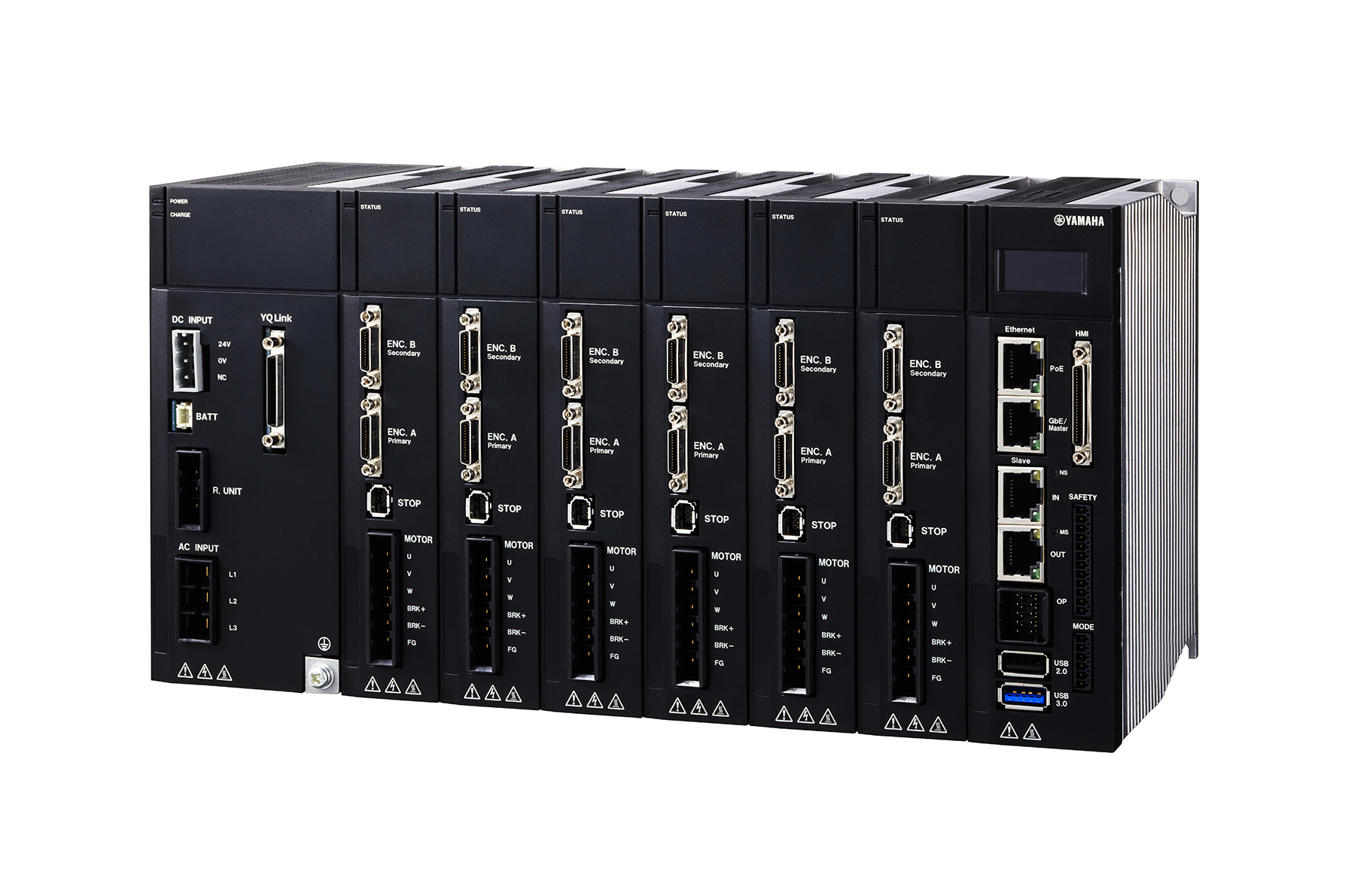
Model | Launch Date | Price | Target Sales |
---|---|---|---|
YHX Series Integrated Controller |
December 1, 2016 | Open Price |
8,000 units |
Main Features of the YHX Series
1) The industry-first stacking structure delivers significant reductions in control board cost and space, also reducing setup time
Through integrated control of single-axis robots (AC servo motor specification and stepping motor specification), SCARA robots, linear conveyors, and image processing cameras etc. compatible with the Advanced Robotics Automation Platform as well as peripheral devices, the YHX Series enables building advanced automated systems.
Moreover, the industry-first stacking structure including as far as motor drivers and motor drive power supply enables tremendous saving on cabling and simplification of the number of power supplies. By standardizing all of the control power supply, motor drive unit power supply, high-speed network communication, and safety circuit to stack connections, wiring between units becomes redundant, reducing wiring cost and wiring setup time by 30%-50% compared with previous models.
The YHX Series host controller can simultaneously control up to 64 robots including 255 motors. Moreover, through network cable connections, this controller can function as a host or slave in various field networks.
2) Internal PLC based on international standards; IoT compatibility also complete
The YHX Series includes a high-functionality and high-speed versatile general-purpose PLC, and through the ability to use five types of language based on IEC61131-3, control of overall automated devices including robots and peripheral devices is possible. Additionally, the controller has the flexibility and expandability to work with IoT and Industrie4.0 etc. in the future.
3) Easy operation on the full-screen Programing Pad touch panel.
The Programing Pad has an easy-to-operate interface with safety functions included on the full-screen approximately 10-inch LCD touch panel. The three languages available are Japanese, English, and Chinese.
Key Specifications
4-Axis Configuration Example | Integrated Controller Configuration (1 high-capacity power unit + 1 host control unit + 4 driver units) |
Gateway Configuration (Gateway unit + 4 driver units) |
---|---|---|
Controllable Robots | Single-axis (AC servo/step) |
Single-axis (AC servo/step) Multiple axis (cartesian, [SCARA]) |
External Dimensions | H150mm x W232.2mm x D125mm | H150mm x W158.8mm x D125mm |
Weight | Approx. 4.5kg | Approx. 3kg |
Power Capacity | Single-phase 3.4kVA/three-phase 6kVA | Single-phase 2.2kVA/three-phase 4.4kVA |
Allowable Motor Capacity | Single-phase 1.6kW/three-phase 3kW | Single-phase 1kW/three-phase 2.5kW |
Maximum Number of Connected Axes | 16 | |
Field Network | Master [PROFINET・EtherNet/IPTM・EtherCAT] Slave [PROFINET・EtherNet/IPTM・EtherCAT・(CC-Link*) (DeviceNet*)] |
Slave [PROFINET・EtherNet/IPTM・EtherCAT・(CC-Link*) (DeviceNet*)] |
Functions | PTP/Press-in/Coupling 3-dimensional interpolation (straight line/arc/helical etc.) Synchronization (electronic cam/electronic gear etc.) PLC functions [ladder/FB/ST/etc.] |
PTP/Press-in/Coupling 3-dimensional interpolation (straight line/arc) |
Programing Pad | Connectable | Not connectable |
*Connection adapter required.