The Delicate and Dynamic Task of Handbuilding Pools in a Factory
Almost half a century ago, Yamaha Motor began making swimming pools by calling on the fiber-reinforced plastic (FRP) construction techniques we acquired through boatbuilding. Even today, the process of making such large, beautiful, and high-precision products relies on the incredible skills of master craftsmen.
Precision Guaranteed Down to the Fingertips
“The fingertips and touch make the difference.” This is a common phrase uttered by commenters in the world of competitive swimming and is by no means an exaggeration. The instant a swimmer reaches for the wall of the pool, whether their finger is pointing straight ahead or is slightly bent, can determine a win or a loss, a record broken or not. To ensure fairness wherever such top-level competitions are held, the pools must all have the same high degree of construction precision. For this reason, the standards swimming pools must meet for official certification for competition are very strict.
Approximately two million liters of water is needed to fill a 50-meter, 8-lane competition pool. By comparison, even a standard 25-meter school pool must be able to withstand the enormous pressure of about 360,000 liters. But the forces exerted by the water are not the only factor in play. For a swimming pool exposed to direct sunlight and thus subjected to temperature changes around the clock, the contraction and expansion of the material must also be taken into account in its design. To satisfy these stringent requirements and harsh conditions, Yamaha’s FRP pools are built to millimeter precision to guarantee even a fingertip difference remains fair and fact.
Further, a pool’s level of safety and durability present even more important requirements to meet. Shortly after the Tohoku earthquake and tsunami in 2011, Yamaha Motor assembled a large investigative team to go and inspect the FRP pools manufactured and installed by the company in Iwate, Miyagi, and Fukushima prefectures. With the exception of areas declared off limits, the team carried out multipoint checks and damage inspections on a total of 329 pools. While they did find damaged piping and other issues caused by land subsidence, none of the pools suffered significant functional damage. These inspections once again proved the high earthquake resistance and toughness of the materials used in Yamaha’s FRP pools. In fact, at 64 evacuation shelters and facilities, some of these pools were repurposed to allow pool water to be used by evacuees in areas where city water had been cut off.
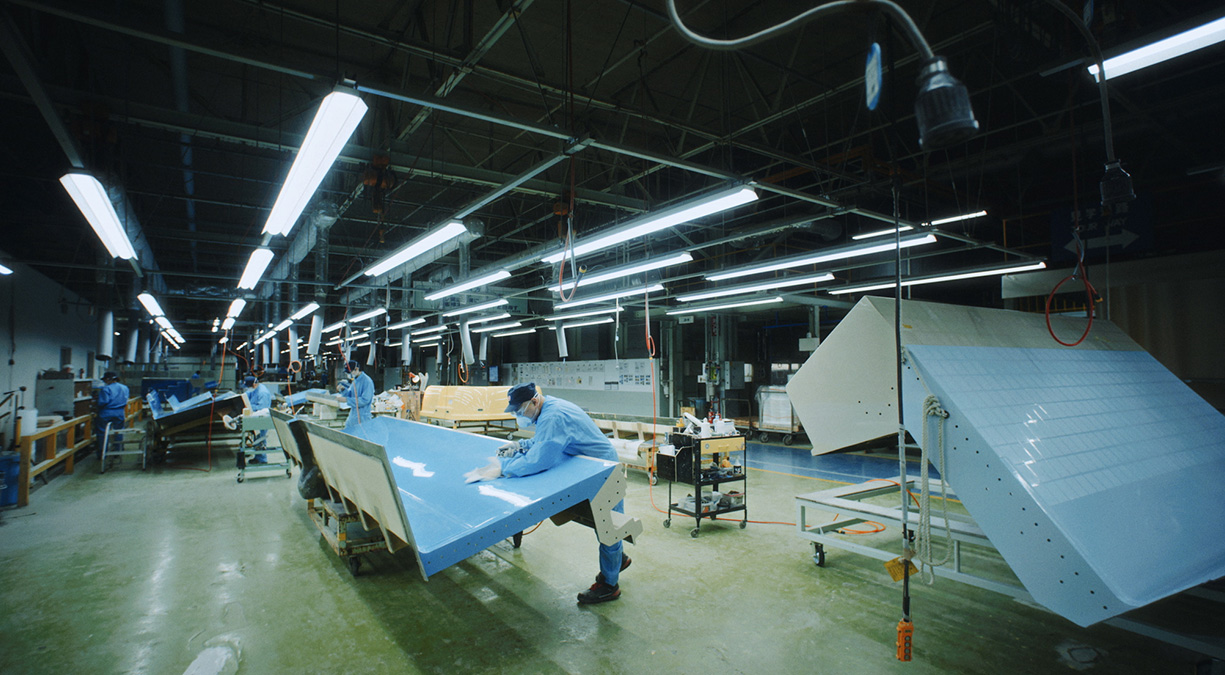
Monozukuri Begins with the Finishing Process
To build a Yamaha FRP pool, individual units are first constructed at the company’s quality-controlled factory before they are transported to the client’s location and assembled on site. It is hard to imagine the kind of factory in which pools are made by hand, but the interior of the factory near Lake Hamana where the sections of these FRP pools are built presents a very different picture from those manufacturing and producing Yamaha motorcycles and outboards.
Upon setting foot in the factory, the first thing that catches your eye is the sheer size of the neatly lined up pool sections. Each of these units are used to construct a pool—called “workpieces”—and have a presence that bestows the factory with a unique air. The bigger pieces are a whopping 8 meters long, but are still assembled to form the final pool, almost like a massive plastic model set. So it comes as no surprise that this factory looks very different from one for motorcycles.
There’s yet another big difference: almost every process that takes place in this factory is done with the hands of craftsmen. As a result, there are no loud noises from large machinery echoing throughout the factory. It is a large but quiet space filled with big structures, and the only sound is of swimming pools being born.
Yamaha’s FRP pools are constructed by setting layers of fiberglass into a female mold and then permeating it with resin. This process is repeated until the desired shape and thickness is achieved. Because the side of the FRP facing the mold will be the pool’s surface, the craftsmen must exercise extreme care in their pursuit of beauty to ensure that the surface where the FRP touches the mold is as flat and smooth as possible. Even the smallest imperfections—including those undetectable by the human eye—become permanent. This is why having a razor-sharp eye is critical.
With most products, painting constitutes part of the final finishing process, but when working with FRP, Yamaha’s Monozukuri begins with the delicate finishing process of applying the fiberglass. This is where the beauty and quality of the final finish is determined, only after which are numerous layers of fiberglass added to increase strength. When completed, the workpiece is smooth and beautiful. This now becomes the canvas on which the craftsmen who apply the gel coat will display their artistry with a spray gun in a spray booth located in a corner of the factory.
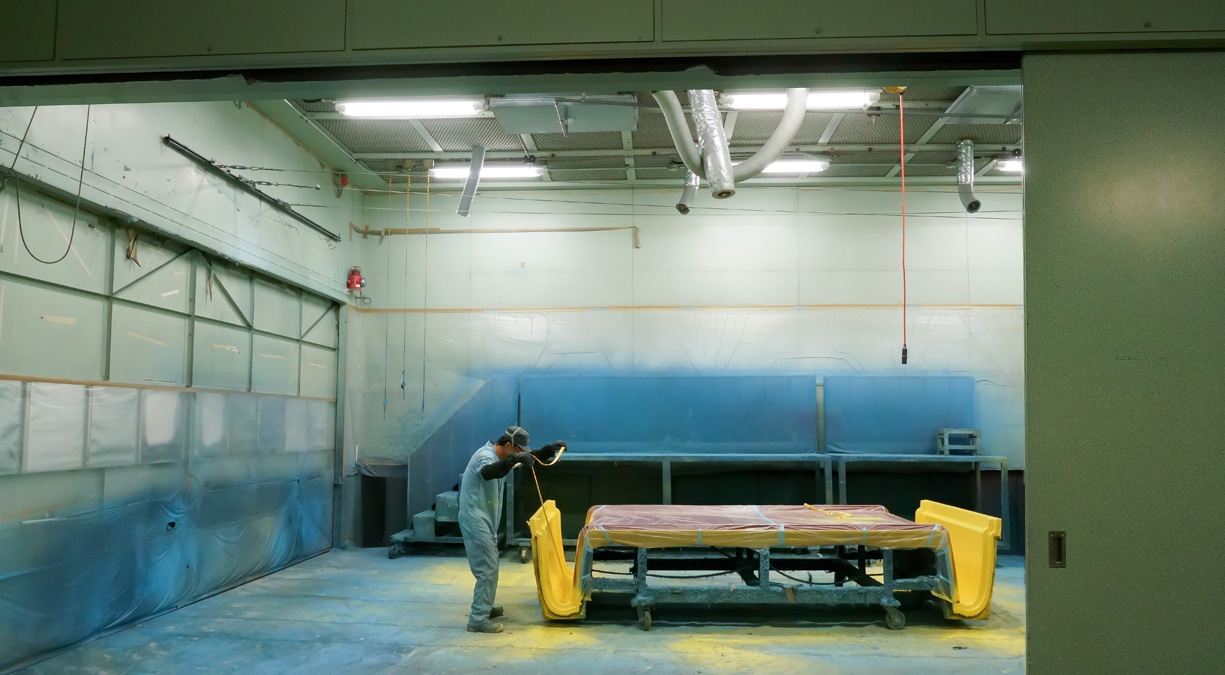
A Fluid and Graceful Performance
The graceful movements of the craftsman tasked with spraying the gel coat are a study in elegance, and one struggles to describe the beauty of his motions in simple terms. Holding the spray gun in his right hand and the air hoses with his left, with his head cocked slightly to the side and his body at an angle, he makes small and careful steps around the workpiece. His every motion part of a well-choreographed sequence, he moves smoothly, fluidly, and calmly. If he had no tools in his hands, he would almost appear to be dancing. His entire body is constantly in motion as he deftly sweeps the spray gun over the workpiece, changing the angle of the gun and the intensity of the paint applied.
Each pass of the spray gun deposits a layer 0.2 mm thick. Two passes followed by a lighter final pass builds up the coat to the required 0.55 mm. The volume of gel coat sprayed from the gun is strictly controlled to prevent any excessive thickness in the coat.
The flicks of his wrist are where to train your eye. Although the gel coat is applied using repetitive passes, it’s when the gun changes direction that applying additional spray becomes physically unavoidable—unless you use a technique particularly difficult to master. If the same rhythm used for the back-and-forth movements is employed here, the buildup at the end of each stroke can cause runs and unevenness in the coat. By deftly snapping his wrist at the end of each pass to temporarily direct the gun away from the surface and then smoothly start the next stroke, the craftsman ensures that a consistent layer of material is applied. It looks much easier than it actually is. The speed at which the sprayer passes over the workpiece can neither be too fast nor too slow—it must be uniform.
The opposite movement is used when making the return pass. Anticipating that the gel coat will become thicker, he adjusts the distance with the gun ever so slightly to reduce the volume that reaches the surface. And because the gel coat tends to accumulate in corners and angled areas, he uses a similar technique to prevent it. “It’s all muscle memory now. My body just knows what to do,” he says.
Although the spray booth is maintained at room temperature, on cold winter mornings and the like, there are times when he senses that the spray from the gun feels dulled and more difficult to apply. When the craftsman senses these subtle changes in the ambient environment, he adjusts the gun’s air pressure or changes the speed of his movements to achieve the best result.
The technologies used to create Yamaha’s FRP pools have their roots in the building of boat hulls. Taking advantage of the lightness, strength, and freedom of design qualities inherent to FRP, Yamaha began manufacturing swimming pools almost 50 years ago. They are not only strong, durable, and accurate to the millimeter but also beautiful to the eye, nice to the touch, and very user-friendly. By retracing the history of Yamaha’s boatbuilding, the care and craftsmanship called upon to produce our FRP pools reveals itself.
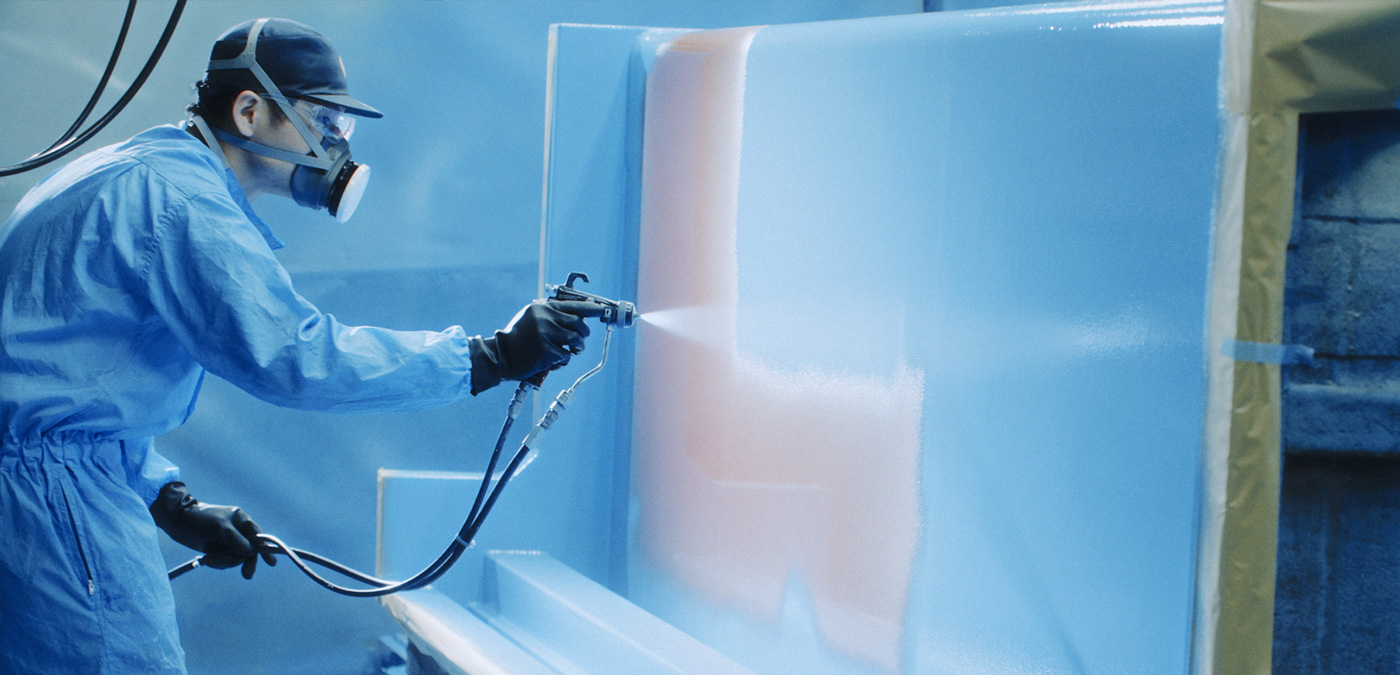