Magnesium Chassis Parts for Motorcycles
Examples of large, cast magnesium parts with thin sections
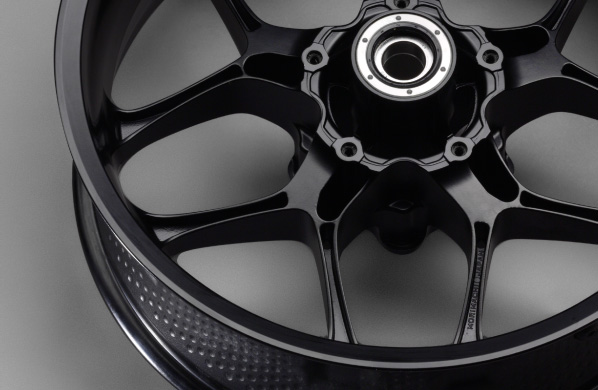
Based on our CF (controlled filling) die-casting technology for aluminum, Yamaha was able to successfully develop casting methods yielding even melt flow and solidification for magnesium-specific part designs; optimized control of vacuum degree in the mold cavity, mold temperature, and melt injection speed; and melt control that minimizes impurity content. These and other achievements made it possible to cast large magnesium parts with thin sections, thereby practicalizing the use of magnesium for large motorcycle chassis parts. Following the casting process, these magnesium parts are given a special highly corrosion-resistant surface treatment prior to painting, bestowing them with strength and corrosion resistance equal or superior to identical aluminum parts (based on Yamaha standards).
Need
- Use magnesium for parts in order to reduce motorcycle chassis weight
DevelopmentDirection #1
- Ensure sufficient safety for handling magnesium in manufacturing
DevelopmentDirection #2
- Product and part design optimized for using magnesium
DevelopmentDirection #3
- Optimize control parameters in the work processes
Solution
01Safety Management
Conducted technician education, procured dedicated equipment, enacted thorough countermeasures for work dust/chips, etc.
02Concurrent Engineering
Developed and established designs and manufacturing methods capitalizing on the qualities of magnesium as a material
03CF Magnesium Die-Casting Technology
Adapted our CF aluminum die-casting technology for magnesium as a method that offers substantial freedom in part engineering and design
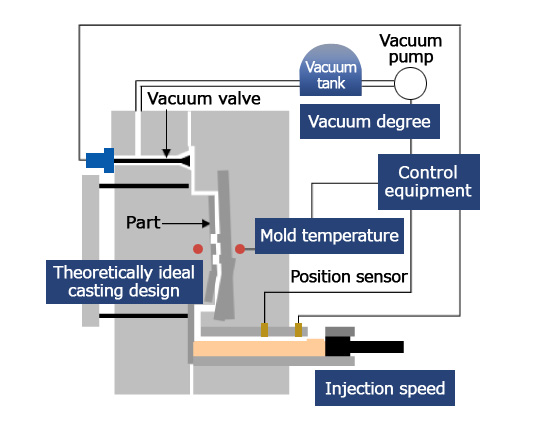
Result
- 01Achieved significant motorcycle chassis weight reductions, e.g., a 500 g reduction with a magnesium subframe and an 870 g reduction with die-cast magnesium wheels
- 02Succeeded in the challenging task of casting large magnesium parts with thin sections while still ensuring high quality
- 03Ensured that appropriate safety controls were in place at worksites and facilities

We apologize for any inconvenience caused and we are hoping for your kind consideration.