Thinner Cooling Fins and Weight Reduction for Scooter Engines
An example of concurrent engineering for making thinner cooling fins
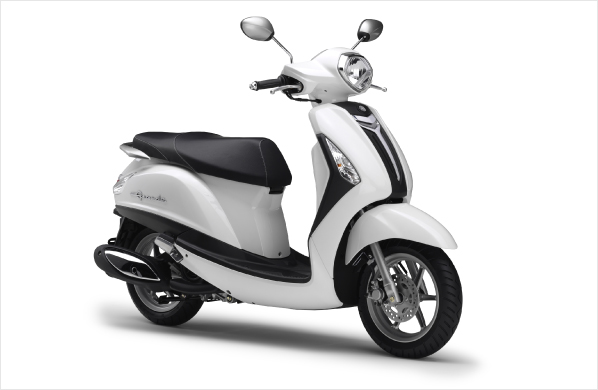
This is an example of our engine designers and casting department engineers attempting to push the limits of thinning parts through concurrent engineering. Scooter engines present challenging requirements in that they must not only deliver both high levels of performance and fuel efficiency but also do so at as low a cost as possible. By optimizing the respective functions of both solidification analysis and molding technology, Yamaha successfully produced thinner engine cooling fins with low-pressure die casting.
Need #1
- Thinner cooling fins for an air-cooled engine for scooters
DevelopmentDirection #1
- Optimize casting conditions to create thin-walled shapes by means of high-accuracy melt flow control and solidification analysis
Need #2
- Optimize the standard thickness for the engine’s fins
DevelopmentDirection #2
- Control the vacuum in the cavity to improve melt flow for the thinner engine cooling fins
Solution
01Analysis
Using flow analysis incorporating robust casting conditions brought the flexibility to respond to changes in production conditions. This enabled consistent casting.
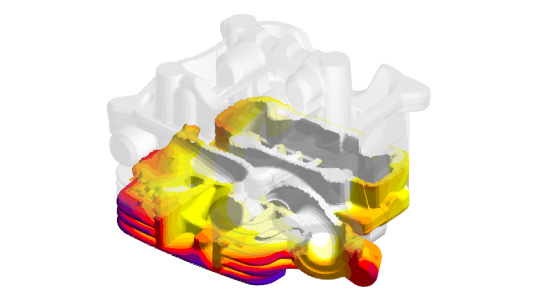
02Molding technology
Utilized technology for controlling the vacuum in the mold cavity. Installed air duct piping on the interior side of the engine fins to use the vacuum to improve melt flowability.
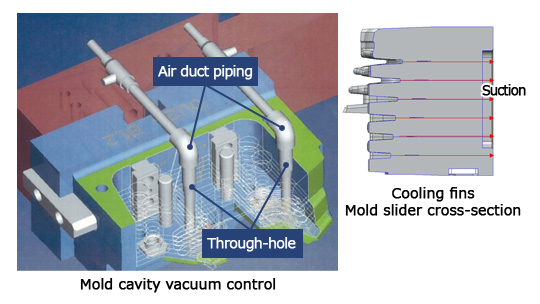
Inducing a vacuum by using the air in the venting channels for the fins’ cavity insert
Result
- 01Thinner cylinder head cooling fin thickness (3.0 mm to 2.0 mm)
- 02Higher cooling performance for the combustion chamber, contributing to lower fuel consumption
- 0314% lower weight compared to the previous model (cylinder head standalone weight)
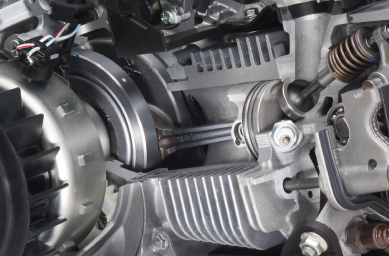
We apologize for any inconvenience caused and we are hoping for your kind consideration.