The Original Model that Led to Multipurpose Capability
Introducing the stories behind Yamaha Motor's technologies.
The Challenge Began by Using Cutting-edge Gyros
Our challenge to take to the sky has been a long one and it was first made public in January 1982 with an announcement: “Yamaha’s progress to this day can be likened to our history of developing small-engine technologies. Based on our expertise and successes in this field, we plan to enter the market for and begin providing small multi-purpose aviation engines for motorized hang gliders, unmanned aircraft and the like going forward.” The announcement garnered much attention and was in the newspapers the next day with headlines like, “Yamaha to Take On Three-Pronged Land, Sea and Air Strategy.”
In 1983, a commission was received from the Japan Agricultural Aviation Association (an external organization of the Ministry of Agriculture, Forestry and Fisheries) to develop a remote control aircraft capable of performing aerial (airborne) spraying of agrichemicals, or RCASS (Remote Control Aerial Spraying System). Initially only asked to develop an engine, the importance of the end-product operating as a complete package led to Yamaha taking charge of developing the RCASS entirely and R&D began. The prototype was dubbed the “Aero Robot RCASS” (#1).
Another request from the same organization was for the craft to use counter-rotating rotors.* Yamaha focused its R&D efforts towards achieving this and used a liquid-cooled 2-stroke single-cylinder 292cc engine for the prototype. A helicopter with counter-rotating rotors has no need for a tail rotor, making it more compact. But that also means that controlling pitch (rotating about the y-axis), roll (rotating about the x-axis) and yaw (rotating about the z-axis) becomes uniaxial, making the required mechanisms more complex to engineer. A Flight Test Stand (FTS) (#2) was developed and the team worked towards making the prototype ready for practical use, but factors like the characteristics of servomotors at the time made flying the helicopter manually very challenging.
So instead, the team decided instead to use gyro sensors—a cutting-edge technology at the time—and fully automated flight tests were carried out to verify design validity (#3). This was Yamaha’s first real step towards developing the electronic governance of an unmanned helicopter. But the aircraft still tipped the scales at over 100 kg, so practical use would still have to wait.
*Counter-rotating rotors: a helicopter format in which two rotors on the same axle rotate in opposite directions.
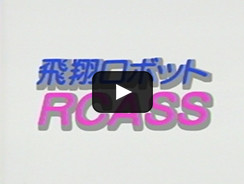
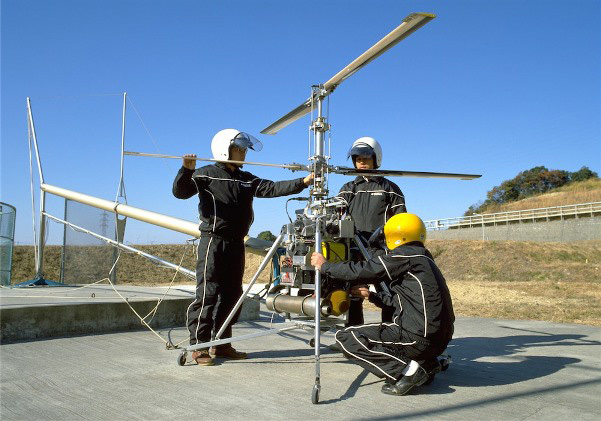
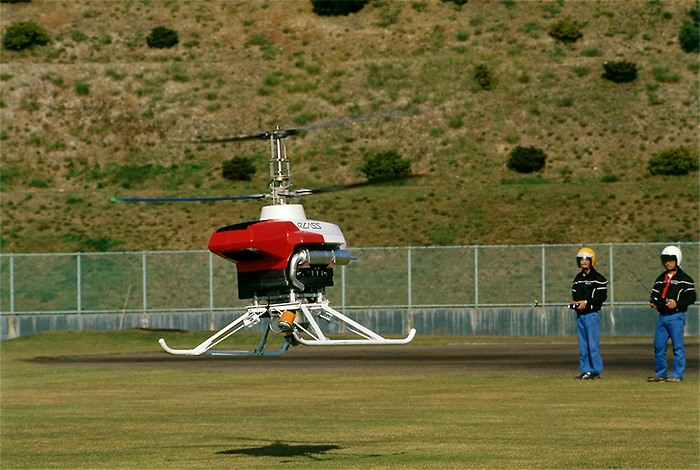
Developing and Improving the Base Model
The R-50 (#4) was developed alongside the RCASS. It used a main rotor/tail rotor format and was powered by a liquid-cooled 2-stroke, 2-cylinder, 98cc engine. After it was completed in 1987, limited sales began with end-customers providing Yamaha with their feedback as they used it. The R-50 was the world’s first unmanned helicopter for crop dusting capable of carrying a 20 kg payload. But this initial model did not feature any electronic governance as the main priority was to establish a base platform for unmanned helicopters.
Following that, R&D began on incorporating electronic altitude control for the R-50. This would allow the operator to concentrate more fully on spraying the fields below. An ultrasonic sensor was tested, but the rice paddies would absorb the waves and negate effectiveness. A laser sensor was tested after that and it worked well, so it was adopted for a system Yamaha developed to control the helicopter’s altitude, the Yamaha Operator Support System (YOSS). YOSS was eventually implemented on the R-50, but it was overly sensitive to uneven terrain in actual use and this version was later removed from production.
But further evolution came in 1995. Fiber-optic gyros developed for car navigation systems were utilized to develop the Yamaha Attitude Control System (YACS), which featured an operator-controlled model-tracing device to more faithfully respond to steering commands. It was added to the R-50 and went on sale the same year.
With early versions of the R-50, the operator had to use the control stick and fly the helicopter the entire time from takeoff until landing. But with the introduction of YACS, information gleaned from the three fiber-optic gyros and accelerometer could be processed and used to make automatic control of all axes of flight possible. The R-50’s ease of use and excellent spraying efficiency won it much popularity. The total number sold reached some 1,000 units and the model succeeded in expanding the number of industrial-use unmanned helicopter users.
Expanding Fields of Activity
After the R-50, Yamaha has constantly sought to refine and evolve the features and qualities of its unmanned helicopters. The RMAX was introduced in 1997 and featured a newly designed engine, and was followed in 2000 by an RMAX equipped for automatic flight (built-to-order model; used to investigate the eruption of Mt. Usu). The RMAX Type II G and Type II were introduced in 2003 with functions that made them easier to fly, and the RMAX G1 that featured fully automatic flight geared towards industrial use was released in 2006. The 4-stroke FAZER model went on sale in 2013, followed by the FAZER R in 2016.
Today, approximately 2,800 industrial-use unmanned helicopters are registered for operation in Japan’s agriculture industry alone (as of March 2016). They spray a total area of around 1.06 million hectares, or around 36% of the country’s rice paddy area under cultivation. Their use has now spread to crops other than rice, such as wheat, soy beans, lotus roots, daikon radishes and Japanese chestnuts. These helicopters have also seen greater use for spraying fruit orchards and vegetable farms.
The RMAX G1, which is capable of automatically flying the same pre-programmed route several times without difficulty, has demonstrated its capabilities across a variety of tasks, such as observing tideland ecosystems, conducting topography surveys and measuring radiation levels.
Yamaha’s unmanned helicopters provide solutions for both agriculture and examining our natural environment, and are symbols of Yamaha Waza and Sube that reaches into the sky.