The Result of Aluminum Research: The DiASil Cylinder
Introducing the stories behind Yamaha Motor's technologies.
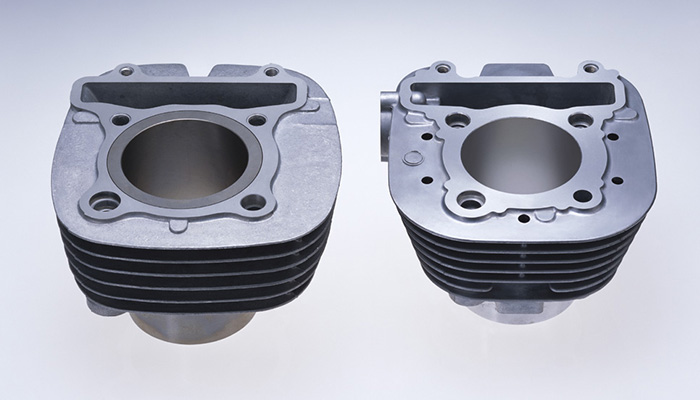
The specific gravity of aluminum is 2.7 and steel’s is 7.8. This gives aluminum about 1/3 the weight of steel. It also has the advantages of being well-suited to metalworking, being easy to recycle and its resistance to rust (corrosion). For these reasons, aluminum is used for many parts in motorcycles and outboard motors. Yamaha was quick to recognize the potential of aluminum and has continued to conduct research into various aspects of the material.
Casting aluminum parts involves pouring or injecting molten aluminum into a mold, and there are two methods for doing so: “gravity casting” and “die casting.” As the name implies, gravity casting uses the natural force of gravity to let the molten aluminum flow into the mold. Die casting uses high levels of pressure to inject the molten aluminum into the die at high speed. Yamaha Motor has used this latter method since the 1960s, but high-pressure injection die casting tends to leave air bubbles in the solidified work pieces and thus increases the possibility of a decrease in strength. It is also unsuitable for casting large but thin parts.
What solved these problems was a new technology that Yamaha Motor brought into practical use in 2002 named “Controlled Filling (CF) Aluminum Die Casting.” This new method involved controlling the temperature at which the molten aluminum would solidify in the die, keeping the inside of the die at a near vacuum (at or below 50 hPa) to inhibit air bubbles from forming in the cast piece’s crystalline structure, and precisely controlling the speed of injection. By successfully creating this Yamaha-exclusive “recipe” of injection and solidification conditions, the CF aluminum die casting method succeeded in reducing the amount of bubble-forming gas in the work piece by 80%. In other words, this almost completely eliminated the presence of structure-weakening bubbles.
Putting this CF aluminum die casting method into practical use enabled Yamaha to cast large parts with thin sections that retained high levels of strength, parts with intricate curves and parts with sections of varying thickness. This resulted in a greatly expanded use of aluminum die-cast parts. First utilized for creating the swingarm for the 2003 YZF-R6, the CF aluminum die casting method is used today for manufacturing a wide range of major motorcycle components.
CF aluminum die casting technology has also revolutionized the manufacture of the cylinders that constitute the heart of an engine. Conventional cylinders have a pressure-inserted steel sleeve to reduce friction between the piston and the cylinder wall. But this construction has the drawback of inhibiting heat dissipation. Though other constructions such as cylinders with an aluminum liner or plating of the cylinder wall can serve as alternatives to the steel sleeve, they make the manufacturing process more complex and raise costs overall.
To provide a solution to the downsides of these conventional cylinder formats, Yamaha Motor applied its die casting expertise and became the first manufacturer in the world to mass-produce an all-aluminum cylinder in 2004. Named the “DiASil Cylinder,” it uses an aluminum alloy with a high silicon content (20%), something that had been considered a difficult technical hurdle to overcome until then. This new production method achieved an excellent balance between the type of aluminum alloy used, the efficiency of the manufacturing technology and the impact on the environment, and the cylinder boasted the highest levels of cooling efficiency (at the time) while also reducing production costs. The initial DiASil Cylinder was created with the near-vacuum injection process and an aluminum alloy with 20% silicon content. Ensuing improvements have been made and it is now used on models ranging from the 250cc Majesty scooter to commuter models for the ASEAN markets and sport models like the YZF-R25 (#1, #2), YZF-R3 and MT-25 (#3).