Yamaha Motor Adds LBAR and ABAR Rod Types to Robonity Series — Slider type lineup gains slimmer LBAS12 and ABAS12 models —
December 2, 2021
IWATA, December 2, 2021—Yamaha Motor Co., Ltd. (Tokyo: 7272)
announced today that its Robotics Operations has added new rod type models to the basic model lineup of the Robonity industrial robot series* and that slimmer models with reduced height will be added to the existing lineup of slider types. Both will be released sequentially from December 2, 2021. These additions to the Robonity Series will expand it to 29 models, offering clients an even greater range of products to choose from.
The Robonity Series includes motorless single-axis actuators that enable clients to use motors and drivers they are accustomed to and single-axis robots that are bundled with the EP-01 robot positioner. The Series is composed of “basic models” featuring high rigidity, compact construction, and low cost, and “advanced models” boasting high precision, high durability, and cleanroom-ready specifications, allowing clients to select models that best suit their needs.
Newly added to the basic model range are the LBAR motorless single-axis rod type actuator and the ABAR single-axis rod type robot. Their main features include 1) a built-in linear guide design that ensures rigidity so that straight-line performance is unaffected even when a radial load is applied and high operational precision with ±0° rod non-rotating accuracy, 2) construction contributing to equipment downsizing with a size some 65% more compact compared to conventional models, and 3) support for long strokes up to 800 mm.
Added to the slider type lineup are the slimmer LBAS12 motorless single-axis actuator and ABAS12 single-axis robot. Greater stability has been achieved by reviewing the design and reducing the height. These are ideal when used for the X-axis of Cartesian robots and also contribute to overall downsizing.
*“Robonity” is a coined word combining “robot” and “infinity” together and the name is meant to express the series’ rich array of variations.
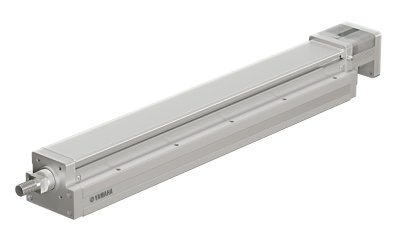
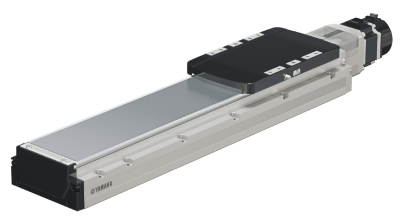
LBAR motorless single-axis rod type actuator (left) and ABAS12 slim single-axis slider type robot (right)
Name | Launch Date | Target Sales | ||
---|---|---|---|---|
Robonity Series:Basic models | Rod type | LBAR motorless single-axis actuator | Dec. 2, 2021 | 600 Units (total series / |
ABAR single- axis robot |
Jan. 20, 2022 | |||
Slider type (slim) | LBAS12 motorless single-axis actuator | Dec. 2, 2021 | ||
ABAS12 single- axis robot |
Jan. 20, 2022 |
Main Features of Robonity Series’ LBAR and ABAR Rod Type Models
High rigidity, compact design, long stroke availability
- •
- High-rigidity specification with built-in linear guide: Thanks to the one-piece construction with built-in linear guide, straight-line performance is not impaired even when a radial load is applied. Further, juddering in the direction of rotation is inhibited and tools attached to the tip of the rod achieve ±0° of non-rotating accuracy. It also becomes possible to eliminate the need for an external guide, which saves on the time, effort, and cost involved in installing one.
- •
- Approx. 65% greater compactness than conventional models: Compared to a conventional model (TRANSERVO Series SRD05), a LBAR05 of the same size is some 65% narrower in width. This contributes to the downsizing of factory equipment.
- •
- Supports long strokes: Features a maximum stroke of 800 mm. Compared to a conventional model (TRANSERVO Series SRD05), a LBAR05 of the same size supports approximately twice its stroke capability at 600 mm.
Main Features of Robonity Series’ LBAS12 and ABAS12 Slim Slider Type Models
Slim construction enables a lower center of gravity, making it ideal for the X-axis of Cartesian robots
By completely reviewing the design, external width has been reduced to 120 mm and the height lowered to 76 mm, thereby contributing to the downsizing of facility equipment. In addition, the center of gravity is lower thanks to the slimmer construction, making the unit ideal for use as the X-axis of a Cartesian robot. It can also be used across a wide range of situations as it is compatible with both 200W and 400W motors with the same frame width.
Other Features of the Robonity Series
Simulator makes it easier to select optimum specifications
You can check projected cycle time and ball screw life by entering basic parameters into the simulator on the website.
*For rod types, only cycle time can be checked.
Robinity Series Basic Specifications
Basic model (rod type): LBAR motorless single-axis actuator
Model | LBAR04 | LBAR05 | LBAR08 | ||||||
---|---|---|---|---|---|---|---|---|---|
Compatible motor (W) | 50 | 100 | 200 | ||||||
Repeatability (mm)*1 | ±0.01 | ±0.01 | ±0.01 | ||||||
Deceleration Mechanism | Rolled ball screw Φ10 (C7 class) | Rolled ball screw Φ12 (C7 class) | Rolled ball screw Φ16 (C7 class) | ||||||
Stroke (mm) | 50–500 (50 mm pitch) | 50–600 (50 mm pitch) | 50–800 (50 mm pitch) | ||||||
Maximum Speed (mm/sec)*2*3 | 720 | 360 | 1,200 | 600 | 300 | 1,200 | 600 | 300 | |
Ball Screw Lead (mm) | 12 | 6 | 20 | 10 | 5 | 20 | 10 | 5 | |
Maximum payload (kg)*3 | Horizontal | 15 | 25 | 15 | 25 | 50 | 30 | 60 | 80 |
Vertical | 3 | 5 | 4 | 8 | 16 | 8 | 20 | 30 | |
Maximum pressing force (N)*3 | 83 | 167 | 100 | 200 | 400 | 201 | 402 | 804 | |
Rod non-rotating accuracy | ±0° | ||||||||
Main unit maximum cross-sectional form (mm) | W44 x H46 | W54 x H54.7 | W82 x H73.5 | ||||||
Overall Length (mm) | Straight | ST+263 | ST+269.5 | ST+326 | |||||
Folding | ST+245 | ST+249 | ST+312.5 | ||||||
Operating environment temperature (°C), humidity (% RH) | 0–40 °C, 35–85% RH (non-condensing) | ||||||||
Compatible servo motors | Yaskawa Electric, Keyence, Mitsubishi Electric, Omron, Panasonic, Sanyo Denki, Tamagawa Seiki, Delta Electronics, FANUC Corporation, Siemens, Schneider, Beckhoff, Allen-Bradley |
Yaskawa Electric, Keyence, Mitsubishi Electric, Omron, Panasonic, Sanyo Denki, Tamagawa Seiki, Delta Electronics, FANUC Corporation, Kingservo, Siemens, Schneider, Beckhoff, Allen-Bradley |
Yaskawa Electric, Keyence, Mitsubishi Electric, Omron, Panasonic, Sanyo Denki, Tamagawa Seiki, Delta Electronics, Siemens, Schneider, Kingservo |
||||||
Compatible stepping motors | Oriental Motor, NEMA standard |
- *
- 1: Positioning repeatability in one direction
- *
- 2: Maximum speed may not be reached when the movement distance is short or under some operating conditions. When the effective stroke exceeds 300 mm (350 mm for the LBAR05, 400 mm for the LBAR08), resonance of the ball screw may occur depending on the operating area (critical speed). In this case, adjust to reduce the speed using the maximum speed shown in the table as a guide.
- *
- 3: May not meet the stated specifications depending on the motor installed.
Basic model (rod type): ABAR single-axis robot
Model | ABAR04 | ABAR05 | ABAR08 | ||||||||||||||||||||||
---|---|---|---|---|---|---|---|---|---|---|---|---|---|---|---|---|---|---|---|---|---|---|---|---|---|
Motor output AC (W) | 50 | 100 | 200 | ||||||||||||||||||||||
Repeatability (mm)*1 | ±0.01 | ±0.01 | ±0.01 | ||||||||||||||||||||||
Deceleration Mechanism | Rolled ball screwΦ10 (C7 class) | Rolled ball screwΦ12 (C7 class) | Rolled ball screwΦ16 (C7 class) | ||||||||||||||||||||||
Stroke (mm) | 50–500 (50 mm pitch) | 50–600 (50 mm pitch) | 50–800 (50 mm pitch) | ||||||||||||||||||||||
Maximum Speed (mm/sec)*2 | 720 | 360 | 1,200 | 600 | 300 | 1,200 | 600 | 300 | |||||||||||||||||
Ball Screw Lead (mm) | 12 | 6 | 20 | 10 | 5 | 20 | 10 | 5 | |||||||||||||||||
Maximum payload (kg) | Horizontal | 15 | 25 | 15 | 25 | 50 | 30 | 60 | 80 | ||||||||||||||||
Vertical | 3 | 5 | 4 | 8 | 16 | 8 | 20 | 30 | |||||||||||||||||
Maximum pressing force (N) | 83 | 167 | 100 | 200 | 400 | 201 | 402 | 804 | |||||||||||||||||
Rod non-rotating accuracy | ±0° | ||||||||||||||||||||||||
Main unit maximum cross-sectional form (mm) | W44×H46 | W54×H54.7 | W82×H73.5 | ||||||||||||||||||||||
Overall Length (mm) | Straight | ST +326.5 | ST +344 | ST +401 | |||||||||||||||||||||
Folding | ST +245 | ST +249 | ST +312.5 | ||||||||||||||||||||||
Position detection | Absolute Encoder Batteryless Absolute Encoder |
||||||||||||||||||||||||
Resolution | 23 bits | ||||||||||||||||||||||||
Operating environment temperature (℃), Humidity (% RH) |
0 to 40 °C, 35 to 85% RH (non-condensing) |
- *
- 1: Positioning repeatability in one direction
- *
- 2: Maximum speed may not be reached when the movement distance is short or under some operating conditions. When the effective stroke exceeds 300 mm (350 mm for the ABAR05, 400 mm for the ABAR08), resonance of the ball screw may occur depending on the operating area (critical speed). In this case, adjust to reduce the speed using the maximum speed shown in the table as a guide.
Basic model (slim slider type): LBAS12 motorless single-axis actuator
Model | LBAS12 | ||||||||||||||||||||||||
---|---|---|---|---|---|---|---|---|---|---|---|---|---|---|---|---|---|---|---|---|---|---|---|---|---|
Compatible motor (W) | 200W | 400W | |||||||||||||||||||||||
Repeatability (mm)*1 | ±0.01 | ||||||||||||||||||||||||
Deceleration Mechanism | Rolled ball screwΦ16 (C7 class) | ||||||||||||||||||||||||
Stroke (mm) | 50–1,250 (50 mm pitch) | ||||||||||||||||||||||||
Maximum Speed (mm/sec)*2 | 1,800 | 1,200 | 600 | 300 | 1,800 | 1,200 | 600 | 300 | |||||||||||||||||
Ball Screw Lead (mm) | 32 | 20 | 10 | 5 | 32 | 20 | 10 | 5 | |||||||||||||||||
Maximum payload (kg)*3 | Horizontal | 20 | 40 | 80 | 100 | 35 | 50 | 95 | 115 | ||||||||||||||||
Vertical | 3 | 8 | 20 | 30 | 8 | 15 | 25 | 40 | |||||||||||||||||
Rated thrust (N)*3 | 105 | 170 | 341 | 683 | 218 | 339 | 678 | 1360 | |||||||||||||||||
Main unit maximum cross-sectional form (mm) | W120 x H76 | ||||||||||||||||||||||||
Overall Length (mm) | Straight | ST +294 | |||||||||||||||||||||||
Folding | ST +270.5 | ||||||||||||||||||||||||
Operating environment temperature (℃), humidity (% RH) |
0 to 40 °C, 35 to 85% RH (non-condensing) | ||||||||||||||||||||||||
Compatible servo motor | Yaskawa Electric, Keyence, Mitsubishi Electric, Omron, Panasonic, Sanyo Denki, Tamagawa Seiki, Delta Electronics, Siemens, Schneider, Kingservo |
- *
- 1: Positioning repeatability in one direction
- *
- 2: Maximum speed may not be reached when the movement distance is short or under some operating conditions. When the effective stroke exceeds 600 mm, resonance of the ball screw may occur depending on the operating area (critical speed). In this case, adjust to reduce the speed using the maximum speed shown in the table as a guide.
- *
- 3: Maximum payload / rated thrust is the value assuming that the installed motor outputs the rated torque.
Basic model (slim slider type): ABAS12 single-axis robot
Model | ABAS12 | ABAS12H | |||||||||||||||||||||||
---|---|---|---|---|---|---|---|---|---|---|---|---|---|---|---|---|---|---|---|---|---|---|---|---|---|
Motor Output AC (W) | 200 | 400 | |||||||||||||||||||||||
Repeatability (mm)*1 | ±0.01 | ||||||||||||||||||||||||
Deceleration Mechanism | Rolled ball screwΦ16 (C7 class) | ||||||||||||||||||||||||
Stroke (mm) | 50–1,250 (50 mm pitch) | ||||||||||||||||||||||||
Maximum Speed (mm/sec)*2 | 1,800 | 1,200 | 600 | 300 | 1,800 | 1,200 | 600 | 300 | |||||||||||||||||
Ball Screw Lead (mm) | 32 | 20 | 10 | 5 | 32 | 20 | 10 | 5 | |||||||||||||||||
Maximum payload (kg)*3 | Horizontal | 20 | 40 | 80 | 100 | 35 | 50 | 95 | 115 | ||||||||||||||||
Vertical | 3 | 8 | 20 | 30 | 8 | 15 | 25 | 40 | |||||||||||||||||
Rated thrust (N) | 105 | 170 | 341 | 683 | 218 | 339 | 678 | 1360 | |||||||||||||||||
Main unit maximum cross-sectional form (mm) | W120 x H76 | ||||||||||||||||||||||||
Overall Length (mm) | Straight | ST +369 | ST +385 | ||||||||||||||||||||||
Folding | ST +270.5 | ST +270.5 | |||||||||||||||||||||||
Position detection | Absolute Encoder Batteryless Absolute Encoder |
||||||||||||||||||||||||
Resolution | 23 bits | ||||||||||||||||||||||||
Operating Environment Temperature Humidity (℃) Humidity (% RH) |
0 to 40 °C, 35 to 85% RH (non-condensing) |
- *
- 1: Positioning repeatability in one direction
- *
- 2: Maximum speed may not be reached when the movement distance is short or under some operating conditions. When the effective stroke exceeds 600 mm, resonance of the ball screw may occur depending on the operating area (critical speed). In this case, adjust to reduce the speed using the maximum speed shown in the table as a guide.