Yamaha Motor adds Single-Axis Robots ABAS and AGXS to Robonity series - Improving usability and operations while pursuing a balance between cost & reliability -
December 9, 2020
IWATA, December 9, 2020—Yamaha Motor Co., Ltd. (Tokyo:7272) announced today new additions to the Robonity series* of the single-axis Basic model: ABAS and Advanced model: AGXS robot positioner EP-01 sets. These are scheduled for release later on January 6, 2021.
*“Robonity” is a coined word that incorporates “robot” and “infinity.” The name expresses the concept of a series with a rich array of variations.
These models have greater usability by further improved operability and supporting IoT, while maintaining the features such as high quality and long life cultivated through the company’s development of robots over the last 40 years. In addition, we have newly developed the robot positioner EP-01 as a controller for the ABAS / AGXS models, achieving both reliability and low prices while improving functionality and reducing costs.
While inheriting the characteristics of the motorless single-axis actuators LBAS and LGXS released in March 2019, this new model has abundant lead lengths and stroke variations, as well as higher rigidity and accuracy. Customers are also able to select from a wider range of different models in this line up to suit their requirements. In addition, outstanding usability and area productivity can be also improved by combining it with the robot positioner EP-01 that are downsized, comes with Ethernet ports as standard equipment, which supports industrial Ethernet. Despite the low price, the functions have been greatly expanded compared to conventional models, this helps provide excellence in cost performance.
Yamaha Motor develops and manufactures a variety of industrial robots necessary for automated production lines, with our wide product range featuring single-axis robots, SCARA robots, articulated robots, and linear conveyors. By expanding the lineup of the Robonity series, Yamaha Motor is working to provide the optimal solution for a broader range of automation requirements.
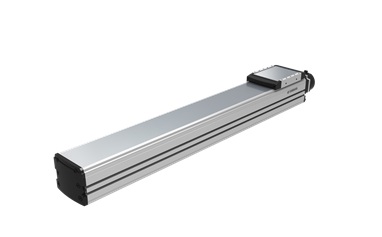
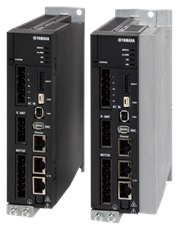
Single-axis robot AGXS (left) and the newly developed Robot Positioner EP-01 (right)
Name | Launch Date | Price | Target Sales | |
---|---|---|---|---|
Single Axis RobotRobonity Series | Basic Models: ABAS | January 6, 2021 | Open Price | 3,600 units (total series / first year from time of release) |
Advanced Models: AGXS | ||||
Robot Positioner | EP-01 |
Robonity Series Single-axis Robots ABAS / AGXS Robot Positioners EP-01 Main Features
Inheriting the features of the Motorless Single-axis Actuators LBAS / LGXS
The basic model ABAS integrates the guide rail and frame. It is compact yet highly rigid. In addition, the Advanced model AGXS uses ground ball screws as standard, creating high-precision models which also deliver high reliability and durability. Usage in clean environments is now also possible as standard, simply by connecting piping and applying suction.
Wide Variations
With a wide variety of lead lengths and strokes, you can choose the specifications that best suit your needs. As it supports up to 1,450mm, it can also be used in long-distance transportation.
Improved Area Productivity
Both the robot and the controller have been significantly reduced in size. The single-axis robot ABAS05 is about 20% smaller than the width dimension of the conventional model T6L, and the Robot Positioner EP-01 is 37% smaller than the conventional model TS-X by volume ratio. Furthermore, when the EP-01 is installed in parallel, it can be installed in closer proximity with a gap of only 1mm. This greatly contributes to improving the productivity area at the factory.
High Cost Performance
Through drastic redesign from the conventional model in order to reduce costs, the EP-01 is available at much lower price. In addition, this unit offers extremely high cost performance provided with enhanced features such as standard equipment for industrial Ethernet, feedback pulse output, direct value control function expansion, and real-time output. In addition, the support software EP-Manager is provided, which contributes to reducing customer equipment costs.
Improved Usability
As the EP-01 unit comes with an Ethernet port as standard equipment, the communication cable dedicated to PC connection - which was needed in the past - is no longer required. This reduces issues on startup, and therefore less man-hours are required on start-up.
Contributing to the realization of a line that does not require stoppages
- ・
- Batteryless absolute support
As the system supports the batteryless absolute method, there is no need for battery replacement.
- ・
- Attach the absolute battery to the cable section
Even where specifications include a battery, the absolute battery is attached to the cable area, so absolute data is retained when the controller is replaced.
- ・
- TRIP Function
The running time and distance can be reset, which is useful for management when replacing parts.
- ・
- Calendar Function
As the time information is retained for over a year, you can use it with confidence even after an extended period of holiday.
- ・
- Real-Time Output Function
As it is compatible with IoT, the load factor and current value of the motor can be output in real time, making it easy to check the operating conditions.
Robinity Series Basic Specifications
Basic Models ABAS
Model | ABAS04 | ABAS05 | ABAS08 | ||||||
---|---|---|---|---|---|---|---|---|---|
AC Servo Motor Output (W) | 50 | 100 | 200 | ||||||
Repeatability (mm)*1 | ±0.01 | ±0.01 | ±0.01 | ||||||
Deceleration Mechanism | Rolled ball screw Φ10 (C7 class) | Rolled ball screw Φ12 (C7 class) | Rolled ball screw Φ16 (C7 class) | ||||||
Stroke (mm) | 50 to 800 (50 mm pitch) | 50 to 800 (50 mm pitch) | 50 to 1100 (50 mm pitch) | ||||||
Maximum Speed (mm/sec)*2 | 800 | 400 | 1333 | 666 | 333 | 1200 | 600 | 300 | |
Ball Screw Lead (mm) | 12 | 6 | 20 | 10 | 5 | 20 | 10 | 5 | |
Maximum Payload (kg) | Horizontal | 12 | 20 | 12 | 24 | 40 | 40 | 80 | 100 |
Vertical | 2 | 5 | 3 | 6 | 12 | 8 | 20 | 30 | |
Rated Thrust (N) | 71 | 141 | 84 | 169 | 339 | 174 | 341 | 683 | |
Maximum dimensions of cross-section of main unit (mm) | W44 x H52 | W54 x H60 | W82×78 | ||||||
Overall Length (mm) Straight | ST+277.5 | ST+295 | ST+353 | ||||||
Folding | ST+196 | ST+200 | ST+264.5 | ||||||
Position Detector | Absolute Encoder Batteryless Absolute Encoder |
||||||||
Resolution (pulse/rotation) | 23 bits | ||||||||
Operating Temperature (℃) Humidity (% RH) |
0 to 40 °C, 35 to 85% RH (non-condensing) |
- *
- 1: Pulsating repeatable positioning accuracy
- *
- 2: May not be reached if the travel distance is too short or other operating conditions.
Advanced Models AGXS
Model | AGXS05 | AGXS05L | AGXS07 | AGXS10 | AGXS12 | AGXS16 | AGXS20 | ||||||||||||||||||
---|---|---|---|---|---|---|---|---|---|---|---|---|---|---|---|---|---|---|---|---|---|---|---|---|---|
AC Servo Motor Output (W) | 50 | 100 | 100 | 200 | 400 | 750 | 750 | ||||||||||||||||||
Repeatability (mm)*1 | ±0.005 | ||||||||||||||||||||||||
Deceleration Mechanism | Ground ball screwΦ12 (C5 class) | Ground ball screwΦ15 (C5 class) | Ground ball screwΦ20 (C5 class) | ||||||||||||||||||||||
Stroke (mm) | 50 to 800 (50 pitch) | 50 to 1100 (50 pitch) | 100 to 1250 (50 pitch) | 100 to 1450 (50 pitch) | |||||||||||||||||||||
Maximum Speed (mm/sec)*2 | 1333 | 666 | 333 | 1333 | 666 | 333 | 1800 | 1200 | 600 | 300 | 1800 | 1200 | 600 | 300 | 1800 | 1200 | 600 | 300 | 2400 | 1200 | 600 | 2400 | 1200 | 600 | |
Ball Screw Lead (mm) | 20 | 10 | 5 | 20 | 10 | 5 | 30 | 20 | 10 | 5 | 30 | 20 | 10 | 5 | 30 | 20 | 10 | 5 | 40 | 20 | 10 | 40 | 20 | 10 | |
Maximum Payload (kg) | Horizontal | 5 | 8 | 13 | 12 | 24 | 32 | 10 | 25 | 45 | 85 | 25 | 40 | 80 | 100 | 35 | 50 | 95 | 115 | 45 | 95 | 130 | 65 | 130 | 160 |
Vertical | 2 | 4 | 8 | 3 | 6 | 12 | 2 | 4 | 8 | 16 | 4 | 8 | 20 | 30 | 8 | 15 | 25 | 45 | 12 | 28 | 55 | 15 | 35 | 65 | |
Rated Thrust (N) | 41 | 69 | 138 | 84 | 169 | 339 | 56 | 84 | 169 | 339 | 113 | 170 | 341 | 683 | 225 | 339 | 678 | 1360 | 320 | 640 | 1280 | 320 | 640 | 1280 | |
Main dimensions of cross sectional of main unit (mm) | W48×H65 | W48×H65 | W70×76.5 | W100×99.5 | W125×H101 | W160×H130 | W200×H140 | ||||||||||||||||||
Overall Length (mm) Straight | ST+195 | ST+236 | ST+276.5 | ST+250.5 | ST+302.5 | ST+344.8 | ST+390.8 | ||||||||||||||||||
Folding | ST+161.5 | ST+191.5 | ST+232 | ST+220.5 | ST+256.5 | ST+294.5 | ST+340.5 | ||||||||||||||||||
Air Cleanliness Class*3 | ISO CLASS 3 (ISO14644-1) | ||||||||||||||||||||||||
Suction Volume (Nℓ/min) Air*4 | 30 - 1000 | 30 - 100 | 30 - 115 | 30 - 90 | 30 - 90 | 30 - 90 | 30 - 90 | ||||||||||||||||||
Position Detector | Absolute Encoder Batteryless Absolute Encoder |
||||||||||||||||||||||||
Resolution (pulse/rotation) | 23 bits | ||||||||||||||||||||||||
Operating Temperature (℃) Humidity (% RH) |
0 to 40 °C, 35 to 85% RH (non-condensing) |
- *
- 1: Pulsating repeatable positioning accuracy
- *
- 2: May not be reached if the travel distance is too short or other operating conditions.
- *
- 3: Please attach air suction couplings when using the product in a clean environment. The air cleanliness class indicates the cleanliness when used at 1,000 mm/sec or less.
- *
- 4: The suction volume required varies depending on the operating conditions and environment.
Robot Positioner EP-01
Basic Specifications | Model | EP-01-A10 | EP-01-A30 | |
---|---|---|---|---|
No. of Controllable Axis | Single-axis | |||
Controllable Robots | Single-axis Robot - Robonity series ABAS / AGXS | |||
Power Capacity | 420VA | 1600VA | ||
Dimensions | W40×H150×D130mm | W55×H150×D130mm | ||
Weight | Approx. 0.6kg | Approx. 1kg | ||
Input Power Supply | Control Power Supply | Single-phase AC200-230V ± 10% 50/60Hz | ||
Main Power Supply | Single-phase AC200-230V ± 10% 50/60Hz | |||
Axis Control | Control Method | Closed-loop vector control method | ||
Operation Type | Positioning operation, positioning connection operation, pushing operation, jogging operation | |||
Position Detection Method | Optical encoder, battery absolute or batteryless absolute selection | |||
Resolution | 8,388,608 pulse/revolution | |||
Origin Search Method | Absolute | |||
Points | No. of points | 255 | ||
Point Type Setting | (1) Standard Settings: Speed and acceleration/deceleration are set as a percentage (%) of each maximum. (2) Custom Settings: Speed and acceleration/deceleration are set in SI units |
|||
Point Teaching Method | Manual data input (coordinate value input), teaching, direct teaching | |||
External Input/Output | I/O Interface | Select from EtherNet/IPTM,PROFINET, EtherCAT, NPN, CC-Link* | ||
Input | Servo ON (SERVO), reset (RESET), start (START), interlock (/LOCK), origin search (ORG), manual mode (TMODE), Jog motion - (JOG-), jog motion + (JOG +), point number selection (PIN0 to PIN7) | |||
Output | Servo status (SRV-S), alarm (/ ALM), operation end (END), operation in progress (BUSY), control output (OUT0 to 3), point number output 0 to 7 (POUT0 to POUT7), feedback pulse output (A/B/Z) (optional) | |||
External Communications | Ethernet (IEEE802.3 100BASE-T compliant, Auto Negotiation compatible) | |||
Power Supply for Brake | DC24V ± 10% 300mA (To be supplied by customer) | |||
Safety Circuit | Emergency stop input, main power input ready output, emergency stop contact output (1 system: when HT2 is used) | |||
Option | Handy Terminal | HT2, HT2-D (with Enable Switch) | ||
Support Software for PC | EP-Manager | General Specifications | Operating Temperature/Humidity Range | 0°C - 40°C, 35% -85% RH (non-condensing) |
Storage Ambient Temperature / Humidity | -10℃ - 65℃, 10% -85% RH (non-condensing) | |||
Atmosphere | Indoors location not exposed to direct sunlight. No corrosion, flammable gases, oil mist, dust particles | |||
Anti-vibration | XYZ 10 to 57Hz in each direction, Single amplitude 0.075mm 57 to 150Hz 9.8m/s2 | |||
Protective Functions | Position detection error, power module error, temperature error, overload, overvoltage, low voltage, excessive position deviation, overcurrent, motor current error | |||
Protective Structure | IP20 |
- *
- CC-Link will be released at a later date