Yamaha Motor Releases High-Function 2-axis Robot Controller - RCX320 — Equipped with real-time output function for predictive maintenance info —
November 1, 2019
IWATA, November 1, 2019—Yamaha Motor Co., Ltd. (Tokyo: 7272) announced today that its new RCX320 will go on sale from December 1. The RCX320 is a 2-axis model of the RCX340 multi-axis robot controller, which has become a best seller due to its high performance and ease of use.
The RCX320 inherits the advanced functionality and flexible expandability of the RCX340 realizing synchronous control of multiple robots, and a high-level equipment construction. Compared to previous models RCX221/222, basic performance has improved significantly, such as the multi-tasking option number, memory capacity, and number of points. In addition, link functionality using YC-Link/E, Ethernet/IP, EtherCAT, and PROFINET are supported, along with the newly installed real-time output of predictive maintenance information ability.
This contributes to the realization of an “unstoppable production line” by enabling flexible equipment construction, faster execution speed of various applications, more comfortable operability, and higher precision for trajectory accuracy.
This product will be on display at the " International Robot Exhibition 2019" being held at Tokyo Big Sight from December 18 (Wednesday) to 21 (Saturday).
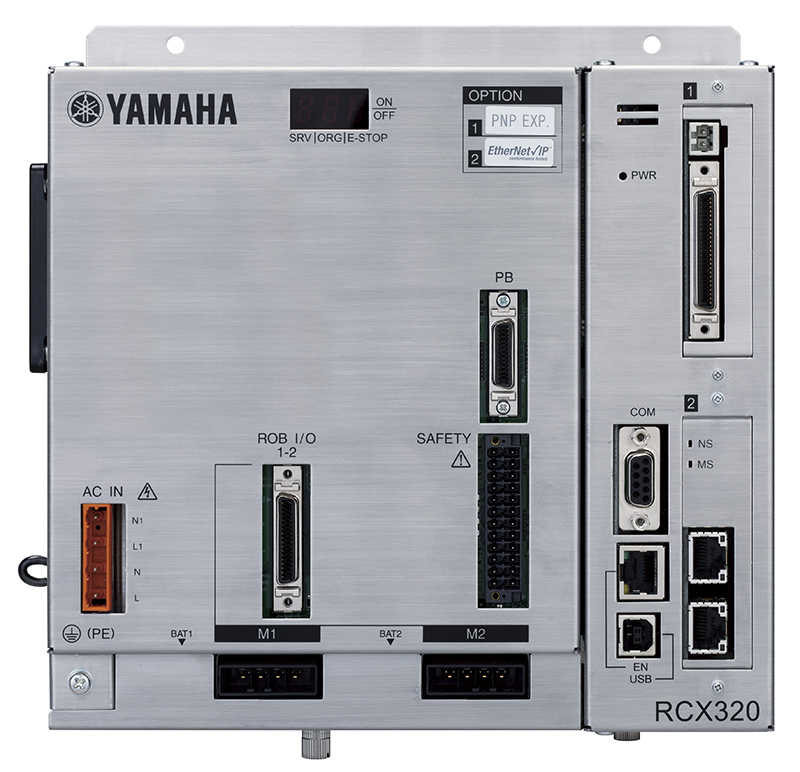
Model | Launch Date | Recommended Retail Price | Target Sales |
---|---|---|---|
Robot controller RCX320 | December 1,2019 | 220,000 yen (Excl. Tax) | 3,000 Units (one year from release) |
Main Features of the RCX320
Significantly Improved Basic Performance
Base performance is greatly improved on previous models RCX221/222.
- Multi-tasking: Up to 16 tasks (RCX221/222: 8 tasks maximum)
- Memory capacity: 2.1MB (RCX221/222: 364KB)
- Number of programs: Up to 100 programs (Equivalent to the RCX221/222)
- Points: 30,000 points (RCX221/222: 10,000 points)
Controlling ability from small to large cartesian robots via one unit
All Yamaha Motor 2-axis robots from small to large can be used with this machine, including the XYX series 2-axis cartesian robot, the FLIP-X series servo motor single-axis robot, and the PHASER series linear motor single-axis robot etc.
Easy control of dual robots
You can easily control a dual robot that drives two axis synchronously.
Achieves 6-axis* control at low cost
In addition to the control of 2-axis robots, inter-controller communication YC-Link/E can be used to easily connect to the RCX340. Low cost 6-axis* control capability is also available.
*Not applicable in the articulated robot YA series.
Synchronous control of multiple robots
Inter-controller communication YC-Link/E enables synchronous control of multiple robots such as in cartesian robots + SCARA robot combinations. Significant reductions in system startup times are achievable as operations can be carried out by a program using only the master controller. The RCX320 controller is compatible with both master and slave specifications, enabling a flexible system build.
*Up to four RCX320 and RCX340 units can be connected by the inter-controller communicating YC-Link/E.
Enhanced field network support and other optional functions
Supports six types of international field networks: Ethernet/IP, EtherCAT, CC-Link, DeviceNet, PROFINET, and PROFIBUS. Building a system that meets your needs is more possible now that the RS-232C and Ethernet ports are equipped as standard, and optional functions such as gripper and vision systems are also supported.
About 3 times the CPU processing capacity
The processing capacity of the CPU has been tripled compared to the previous model. Control performance, such as motion trajectory and internal processing time, is greatly improved
Improved trajectory accuracy
As the unit is equipped with a servo motion engine equivalent to RCX340, the follow-up performance has been improved compared to the previous model along with smoother movement. Shortened positioning time and improved trajectory accuracy.
Supporting software RCX-StudioPro
Compatible with RCX-StudioPro common to RCX340. As RCX320 is equipped with an emulator function, programs can be created and debugged without a controller. The cycle time between two points can be calculated quickly, and the optimal robot can be easily selected. Even after startup, real-time tracing and debugging information of multiple tasks can be displayed at the same time to check the status.
Industrial Ethernet option real-time output functionality
An “unstoppable production line” is achieved when an industrial Ethernet option (Ethernet/IP, EtherCAT, or Profinet) is selected, this enables information necessary for predictive maintenance such as error status, current positions, electric current values, motor load rates, and operation times to be output in real time.
RCX320 Basic Specifications
Item | Details | |||||
---|---|---|---|---|---|---|
Basic Specifications | Applicable Robots | Single-axis, linear single-axis, cartesian, and pick-and-place type robots | ||||
Connected motor capacity | 2 axis, total 1200 W or less | |||||
Power Capacity | 2400 VA | |||||
Exterior Dimensions | W 213×H 195×D 130 mm (Unit only) | |||||
Weight | 3.6 Kg (Unit only) | |||||
Input Power Supply | Control Power Source | Single Phase AC 200-230 V ±10 % 50/60 Hz | ||||
Main Power Source | Single Phase AC200-230V±10% 50/60Hz | |||||
Axis Control | Control Axis No. | Max 2 axis Up to four RCX320 and RCX340 units can be connected by the inter-controller communicating YC-Link/E. |
||||
Drive system | AC full digital servo | |||||
Position detection method | Resolver, magnetic linear scale | |||||
Control method | PTP operation (Point to Point), arch motion, linear interpolation, circular interpolation | |||||
Programing | Program Language | Yamaha BASIC II (JIS B8439 <SLIM language> compliant) | ||||
Multi-task | Max 16 Tasks | |||||
Sequence Programs | 1 Programs | |||||
Memory Capacity | 2.1 MB (total capacity of programs and points) (The program usable capacity when using the maximum number of points is 300 KB) |
|||||
Programs | Up to 100 programs (Max program no.) 9999 lines (maximum number of lines per program) |
|||||
Points | 30000 points (Max point no.) | |||||
Point Teaching Method | MDI (coordinate value input), direct teaching, teaching playback, off-line teaching (data input from outside) | |||||
External Input/output | SAFETY | Input | 2 x Emergency Stop Input Systems 2 x Automatic Mode Input Systems (valid only for CE specifications) |
|||
Output | 2 x Emergency Stop Input Systems 2 x Enable Contact Outputs Systems (valid only when using PBX-E) 2 x Motor Power Ready Output Systems |
|||||
Brake Power | Transistor Output (PNP Open Collector) | |||||
External communication | RS-232C: | 1CH(D-SUB 9 Pin 〈Female〉) | ||||
Ethernet: | 1CH(IEEE802.3u/IEEE802.3 Compliant) 100 Mbps/10 Mbps(100BASE-TX/10BASE-T) Auto Negotiation Compatible |
|||||
RS-422: | 1CH(PBX Only) | |||||
Optional | Option Board | Parallel I/O board | Standard specifications | Dedicated Input 8 points, Dedicated Output 9 points General Input 16 points, General Output 8 points (Maximum 1 board, NPN/PNP Spec. selection) |
||
Extended Specifications | General Input 24 points, General Output 16 points (Maximum 4 board, NPN/PNP Spec. selection) |
|||||
CC-Link Board Ver 1.1/2.0 | Remote I/O | Dedicated Input/Output: 16 points each General Input/Output: 96 points each |
||||
DeviceNetTM Board | ||||||
EtherNet/IPTM Board | ||||||
PROFIBUS Board | Remote Register | Input/Output: 16 Words each xxx | ||||
PROFINET Board | ||||||
EtherCAT Board | ||||||
YC-Link/E Board (Master/Slave) |
Communication Cycle: 1 ms, Control Cycle: Minimum 1 ms/Maximum 8 ms, Maximum Robot Np.: 4 Maximum Control Axis No.: All 14 axis (including 2 master controller axis) Up to 12 axis when only with slaves |
|||||
YRG (Gripper) Board | Position Detection Method: Optical Rotary Encoder, Minimum setting distance: 0.01 mm Speed Setting: Set at 20-100 % of the maximum parameter speed, Number of grippers connected: Up to 2 Drive Power Supply: DC 24 V ±10 % 1.0 A Max |
|||||
Tracking Board | Number of Encoders Connected: Max. 2; Target Encoder: 26LS31/26C31 equivalent line driver (RS422 compliant) Encoder Power Supply: DC 5 V (2 x Counters (ch) total less than 500 mA) (supplied from the controller) |
|||||
iVY2 Unit | Camera Pixel No.: Max. 5 million pixels, Number of types set: 254 types, Number of Connected Cameras: Max. 2 Power Supply: DC 24 V ±10 % 1.5 A Max |
|||||
Programing Box | PBX, PBX-E | |||||
Absolute Battery | 3.6 V 2750 mAH/Axis Backup retention period: approx. 1 year | |||||
PC Software | RCX-Studio Pro |