Yamaha Motor Launches YK400XE SCARA Robot — Delivers Increased Payload and Decreased Cycle Time but Maintains Similar Price —
September 6, 2019
IWATA, September 6, 2019 — Yamaha Motor Co., Ltd. (Tokyo:7272) announced today that it will launch the new YK400XE model 400mm arm length SCARA (horizontal articulated) robot from September 17, 2019.
Despite its low price, the YK400XE is the successor model to the high-precision and high-functionality YK400XR. Thanks to improved rigidity via strengthening of the drive system and arm as well as improved performance of the RCX340 controller, the maximum payload is now 4kg, 1.4 times that of previous models, and the standard cycle time is 0.41 seconds, an approximately 10% reduction. Together, these improvements deliver increased production capacity. In addition, installation positions are fully compatible with the previous model, making upgrading work simple.
Despite the increased maximum payload and improved motion performance, the price is similar to the previous model.
The YK400XE will be exhibited at the China International Industry Fair trade show to be held in Shanghai, China, from September 17 to 21, 2019.
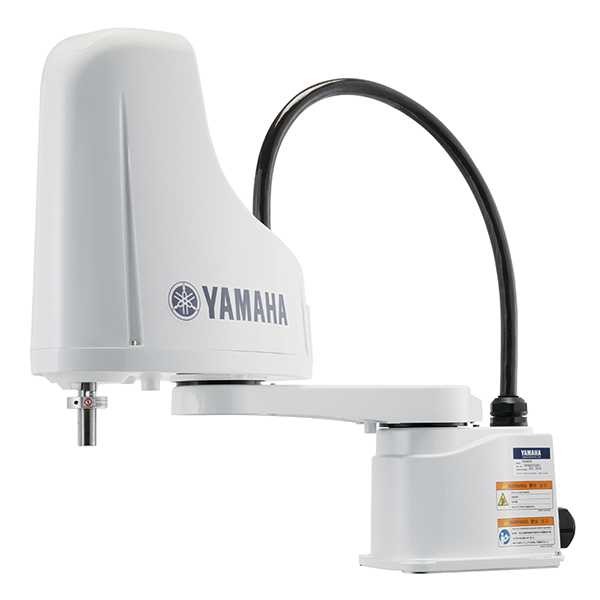
Model | Launch Date | Target Sales |
---|---|---|
YK400XE SCARA Robot | September 17, 2019 | 3,650 Units (one year from release) |
YK400XE Main Features
Maximum Payload of 4kg
Revisions to the drive system and arm structure have increased rigidity and delivered a maximum payload of 4kg, 1.4 times that of previous models. This model is suitable for a wide range of applications, such as assembling, packing, sorting, and inspecting small parts.
Standard Cycle Time of 0.41 Seconds
Revisions to the arm structure have reduced vibration and optimized motion, achieving a standard cycle time of 0.41 seconds, an approximately 10% reduction compared to previous models. The high-speed, low-vibration, and agile movements contribute to improved productivity.
Improved Trajectory Performance
Trajectory accuracy has been improved via the greater performance of the RCX340 controller and the adoption of parameters optimal for the performance area (the actual usage range), thus also delivering greater optimization for operations such as the assembly and sealing of precision parts.
Low Price
Despite improving the basic specifications such as payload, motion performance, and trajectory accuracy, the price is equivalent to the previous YK400XR model. This accessible price enables production site efficiency increases, labor saving, and stable quality.
Full Compatibility with Installation Positions
Installation positions are fully compatible with the previous YK400XR model, making upgrading work simple.
Market Background
Driven by increasing requirements for production line automation and labor-saving, the demand for SCARA robots continues to increase*.
*2018 sales: 46,550 units, 120.0% compared to the previous year. Source: Fuji Keizai Co., Ltd. “Current status and future prospects of 2019 worldwide robot related markets”
SCARA robots in the 400mm arm-length class are mainly used for assembling small parts such as in smartphones, PCs, and home appliances. By launching the YK400XE as the upgraded but compatible model with the existing and highly-rated YK400XR, Yamaha Motor aims to expand its share of the compact SCARA robot market.
Yamaha Motor SCARA Robots
Research and development of Yamaha Motor’s SCARA robots began with the aim of using them in our motorcycle production lines. Because of this, Yamaha Motor has a 43-year history* in SCARA robots, since the first was installed in one of our factories in 1976. Since then, our product lineup has been expanded, now featuring industry-leading product variations from 120mm to 1,200mm arm length, supporting factory automation in a wide range of industries and fields.
*Sales began in 1984
YK400XE Basic Specifications
X Axis | Y Axis | Z Axis | R Axis | |||
---|---|---|---|---|---|---|
Axis Specifications | Arm Length | 225mm | 175mm | 150mm | - | |
Rotation Angle | ±132° | ±150° | - | ±360° | ||
Motor Output AC | 200W | 100W | 100W | 100W | ||
Speed Reduction Mechanism | Transmission Type | Motor-Reduction Gears | Direct Connection | Timing Belt | ||
Reduction Gears-Output | Direct Connection | Timing Belt | ||||
Repeatability1 | ±0.01mm | ±0.01mm | ±0.01° | |||
Maximum Speed | 6m/sec | 1.1 m/sec | 2600°/sec | |||
Maximum Payload | 4kg (Standard Specifications) | |||||
Standard Cycle Time: With 2kg Load2 | 0.41sec | |||||
R Axis Allowable Inertia3 | 0.05kgm2 (0.5kgfcms2) | |||||
User Wiring | 0.2sq x 10 Wires | |||||
User Piping (Outer Diameter) | φ4 x 3 Pipes | |||||
Motion Limit Settings | 1. Soft limit 2. Mechanical stopper (X, Y, Z Axes) |
|||||
Robot Cable Length | Standard: 3.5m (Optional: 5m, 10m) | |||||
Weight | 17kg | |||||
Applicable Controller | RCX340 |
- 1:
- Values under constant ambient temperature (X, Y axes)
- 2:
- When reciprocating 300mm horizontally and 25mm vertically with rough positioning in an arch motion
- 3:
- The inertia must be input in the actual usage environment