Yamaha Motor Co., Ltd. has developed the "YC8," a new compact modular type surface mounter capable of mounting or pressure-inserting large or odd-shaped components of up to 100 mm × 100 mm in length and width, 45 mm in height and weighing up to 1 kg. The model goes on sale April 1, 2012. The new YC8 maintains the high levels of mounting accuracy and ease of operation that Yamaha surface mounters are known for, while adding the capacity to mount heavier components such as the power modules used in today's electric (EV) and hybrid (HV) automobiles as well as the capability to mount larger components such as the shielding cases used in smart phones and tablet devices or components like large connectors that require high-load pressure mounting (pressure-insertion). This makes it possible for the new YC8 to automate processes that could not be performed by conventional surface mounters until now. Designed with a mounting head with a stroke of 100 mm, an increased capacity to handle taller components of up to 45 mm and adopting components including an automatic nozzle station capable of automatically exchanging large f25 mm nozzles and the ATS15 automatic tray supply unit, the new YC8 offers outstanding versatility extending to work processes that involve the mounting of large and/or odd-shaped components. |
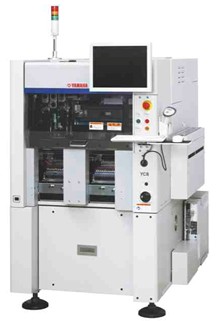 |
Yamaha "YC8" wide-range compact modular surface mounter
|
Model name |
Yamaha "YC8" wide-range compact modular surface mounter |
Release date |
April 1, 2012 |
First (full) year sales plan |
50 units (first full year / Japan and overseas) |
The rapid growth in recent years of mobile IT devices such as smart phones and tablet devices and the electronic control units used in today's electric (EV) and hybrid (HV) automobiles has on one hand, resulted in these new devices requiring printed circuit boards mounting increasingly compact, densely grouped and multifunction electric/electronic components, while on the other hand there remain some components that are difficult to make more compact and lighter and others that need to be inserted in exacting positions on the circuit boards or pressure-inserted in order to fix them in place. Until now, these latter insertion processes could not be automated and had to be performed manually.
Recognizing this need, the new YC8 has been designed as a multi-purpose surface mounter with functions to handle those mounting processes that previously had to be performed manually in SMT (surface mount technology) production lines geared toward compact part, high density mounting as well as the capacity to perform functions that were difficult with conventional SMT machines. The resulting YC8 is capable of mounting larger and heavier components and also pressure-inserting components, making it a highly versatile surface mounter that significantly expands the range of mounting work that can be automated on the SMT production line.
The new YC8 inherits the advanced technologies such as image recognition, high-accuracy placement and accuracy compensation technology that Yamaha surface mounters are known for and uses the same operational software as existing Yamaha surface mounters in order to ensure high levels of overall quality control on the production line. This means improved operation rate and traceability for the user.
|
(1) |
Outstanding mounting capability
●Features a head stroke of 100 mm and a capacity to mount taller components of up to 45 mm in height ●Has the ability to handle heavier components weighing up to 1 kg and the capability to pressure-insert components |
|
(2) |
Optional equipment for good flexibility across a wide range of operations ●Adopts an automatic nozzle station capable of automatically exchanging large φ25 mm nozzles ●Utilizes the ATS15 automatic tray supply unit capable of handling up to 15 trays |
(3) |
Compact machine width of 880 mm allows for more efficient use of factory floor space Easy to position in the work spaces previously used for manual operations |
|
|
(4) |
Compatible with the "SS Feeder" and "ZS Feeder" electric-drive intelligent tape feeders that employ microcomputer control to provide high-speed components supply and high-accuracy components positioning, thus ensuring excellent job setup efficiency and enabling job failure prevention functions. |
|
|
(5) |
High level of mounting quality Yamaha's MACS(*1) system for multi-staged mounting accuracy compensation is adopted on this model. This system provides comprehensive compensation for deviations in the numerous factors involved in accuracy multiple times, ensures a mounting accuracy level of ±0.05 mm at all times. *1 MACS:Multiple Accuracy Compensation System. |
|
|
Model name |
YC8 |
Applicable PCB |
L50×W50 mm to L330×W360 mm |
Mounting accuracy |
Absolute accuracy (μ+3σ): ±0.05 mm/QFP |
Repeatability (3σ): ±0.03 mm/QFP |
Mounting capability |
2.5sec/chip |
Mountable components |
Component size: 4 mm×4 mm to 100 mm×100 mm (Some sizes bigger than 45 mm × 45 mm with conditions) Component height: Maximum of 45 mm |
Maximum transportable mass |
1 kg |
Component supply/Number of component types |
Tape reel: 28 types (Max., 8 mm tape reel conversion) Stick Trays: Capacity for up to 15 trays |
Power supply |
3-phase AC 200/208/220/240/380/400/416V±10% |
Air supply |
0.45MPa or more |
External dimensions (excluding protrusions) |
L880×W1,440×H1,445 mm (Main body) L880×W1,765×H1,500 mm (when equipped with ATS15) |
Weight |
Approx. 1,000 kg |
|
|