Yamaha Motor Co., Ltd. has developed the new robot driver "TS-SD" dedicated to the TRANSERVO series that supports pulse train command input and offers low price and easy operation while achieving high performance. The company will begin selling the TS-SD on October 1, 2011.
The TS-SD has been developed as a new driver that can perform closed-loop control and is dedicated for use with the single-axis robot TRANSERVO series, which utilizes a stepping motor controlled with a vector control method. The result is a model that supports a variety of command pulse input methods while achieving low price and easy operation. |
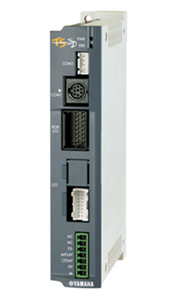 |
Yamaha Robot Driver "TS-SD"
|
Model name |
Yamaha Robot Driver "TS-SD" |
Release date |
October 1, 2011 |
First (full) year sales plan |
1,200 units (domestic and overseas) |
The need to both reduce cost through automation and semi-automation of production systems, and decrease energy consumption by replacing air-driven equipment with motor-driven equipment has recently been expanding the market for actuators that are compact, low-cost, highly reliable and durable.
Yamaha Motor窶冱 existing TS-S model has gained a reputation as a low-price, easy-operation position controller that can control the single-axis robot TRANSERVO series, offering both high functionality and efficient energy use.
At the same time, market needs have been rising for a low-priced driver for the TRANSERVO series that supports pulse train command input. Yamaha Motor has developed the robot driver TS-SD in response to these needs.
The TS-SD is suitable for a variety of work processes and uses in facilities involved in the manufacture of electric/electronic parts or components for compact precision machinery that require high-precision assembly. These processes and uses include assembly, inspection, transfer, feeding/conveying, etc., and uses are also anticipated in the medical and food product fields for handling and inspection process applications.
|
(1) |
Vector control adopted
Inheriting the advantages of the existing Robot Position TS-S controller, the TS-SD has achieved functionality and performance equivalent to those of AC servos at a low price. 1) Minimized reduction in torque at high speeds Because the TS-SD uses a vector control method like the TS-S, it suffers little torque loss in the high-speed region and can operate at high speed even with higher transport loads, thereby shortening tact time. 2) Extremely quiet operation The high-pitched sound characteristic of stepping motors is suppressed, achieving the same quiet operation as AC servos. |
|
(2) |
Closed-loop control by resolver High-resolution of 20,480 pulses per revolution and closed-loop control have achieved high-precision positioning and eliminated the problem of loss of synchronization commonly associated with stepper motors. |
(3) |
Supporting a variety of pulse train command input methods Supports both the open collector method and the line driver method.
Also, the open collector method is compatible with a power supply of between 5V and 24V.
|
|
|
(4) |
Operations using the dedicated TS Series software TS-Manager As with conventional TS Series controllers, the TS-SD can be operated using the TS-Manager, equipped with a wide variety of convenient functions such as robot parameter setting, backup, and real-time trace. |
|
|
Model |
TS-SD |
Controllable robots |
TRANSERVO series |
External dimensions |
W30 × H162 × D82mm |
Weight |
Approx. 200g |
Input power supply |
DC24V±10% |
Power capacity |
Over 3A |
Position detection method |
Resolver |
Resolution |
20480 pulses/rev |
Control method |
Closed-loop, vector control method |
Command pulse input |
Line driver method: 500kpps or less
Open collector method: 100kpps or less (5V to 24V±10%)
|
Operation temperature/Storage temperature |
0 to 40°C/-10 to 65°C |
Operation humidity |
35 to 85%RH (non-condensing) |
|