 |
Shizuoka, September 11, 2007 - Yamaha Motor Co., Ltd. (the "Company") today announced that it will be the first in the world to use magnesium die casting technology to manufacture rear frames for mass produced motorcycles. Yamaha Motor has developed a new technology - Yamaha CF Magnesium Die Casting Technology - that makes possible large, thin, high-quality magnesium die casting components. |
 |
The need for lightweight body components has grown in step with rising demand for maneuverable, fuel-efficient motorcycles. Yamaha Motor's new rear frame units are approximately 20% lighter than conventional aluminum units and will contribute to improving handling performance for riders by more effectively concentrating weight distribution. This technology will first appear on the 2008 YZF-R6 (600cc) model for the European market. |
 |
The Company had been focusing its attention on aluminum due to its performance characteristics and minimal environmental impact, efforts that eventually resulted in two important breakthroughs - CF Aluminum Die Casting Technology 1 and DiASil Cylinder 2. CF Magnesium Die Casting Technology builds upon the know-how derived from working with aluminum to achieve another milestone: cost-effective application of die casting magnesium to the mass production of body components. |
 |
1 |
Yamaha CF (Controlled Filling) Aluminum Die Casting Technology: Manufacturing technology that reduces the amount of gas in the die casting product by 80% through optimized casting conditions (internal vacuum level and die temperature, molten metal injection speed) thereby facilitating mass production of high-quality aluminum die casting body components. First used for the rear arm, etc. of the 2003 model YZF-R6; now used for structural frames on large displacement sport models and large scooters. |
 |
2 |
Yamaha DiASil (Die Casting Aluminum-Silicon) Cylinder: Manufacturing technology that combines aluminum containing 20% silicon and Yamaha's CF Aluminum Die Casting Technology to yield an all-aluminum die casting cylinder with unique bore processing characteristics. Used on the Grand Majesty 250 and the T135 for the ASEAN market. |
|
 |
 |
 |
Benefits of CF Magnesium Die Casting Technology |
 |
 |
1) |
Mass production of large (1~2m), thin (2mm), high-quality magnesium components now possible |
2) |
Strength allows use as body components |
3) |
Sufficient corrosion resistance to allow use as exterior components |
|
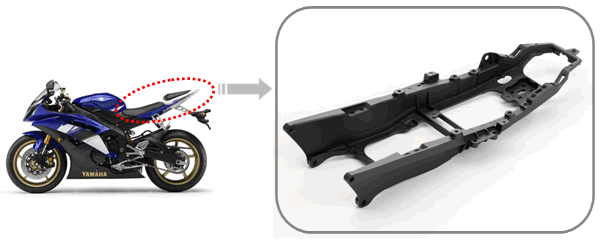 |
2008 model YZF-R6 (left) and rear frame (right)
manufactured using CF Magnesium Die-Casting Technology |
 |
 |
 |
Development Background |
 |
 |
A lightweight body is important because it has a direct impact on maneuverability and fuel efficiency. In recent years, however, the growing use of electronically controlled equipment to improve emissions has led to an increase in gross weight for most motor vehicles, motorcycles included. The result has been a rise in demand for lighter weight body components. |
 |
Yamaha Motor proactively adopted lightweight metal materials, with a primary focus on aluminum, for its body components, tailoring these materials to its motorcycle design characteristics. CF Aluminum Die Casting Technology is used for the mass production of body components because it makes possible the manufacture of large, thin aluminum components while maintaining productivity levels and significantly reducing the number of parts. Despite these advantages, the flow characteristics of molten aluminum place constraints on the final product's thinness and minimum weight. |
 |
Among all lightweight materials, magnesium is the most practical (the specific gravity of magnesium is two-thirds that of aluminum) and is considered a next-generation solution for many design problems now confronting manufacturers. However, compared to aluminum, magnesium rapidly cools and solidifies from its molten metal state making it difficult to obtain large, thin casts of consistent quality. Furthermore, when impurities (iron, nickel, etc.) in the material exceed a specified level, a significant decrease in corrosion resistance is observed. For these reasons it was difficult to achieve the consistent quality levels that body components require to ensure proper strength during a lifetime of use, resulting in Yamaha Motor restricting the use of magnesium on mass produced motorcycles to small parts such as engine covers. |
 |
 |
 |
Technical Overview |
 |
 |
Yamaha Motor's CF Magnesium Die Casting Technology is based on CF Aluminum Die Casting technology that has been optimized to allow for the mass production of large, thin magnesium body components. More specifically, this technology was designed exclusively for use of magnesium for consistent flow and solidification of molten magnesium. The technology has been made possible by optimizing process control of the vacuum inside the die, the die temperature, the injection speed of the molten metal, etc., so that the mold is filled with molten metal prior to solidification. The molten metal is also carefully controlled to minimize impurities. |
 |
Yamaha Motor applies an exclusive corrosion-resistant undercoat and painting to components following casting, and has achieved a level of corrosion resistance equal to or greater than aluminum (based on in-house standards). |
 |
This, then, is the technology that has made possible the mass production of large, thin, high-quality magnesium die casting body components. |
 |
 |
 |
Basic CF Magnesium Die Casting System |
 |
 |
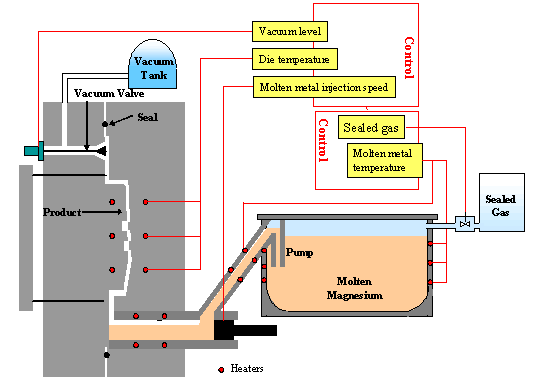 |