Yamaha Motor Co., Ltd.s in-house company IM Company (President: Tsuneji Togami; Location: Hamamatsu City, Shizuoka Pref.) has succeeded in the development of its new "YMS Series" rod-type single-axis (single arm) robots in two models, the YMS45 and YMS55, featuring quieter and cleaner operation than air cylinder type models as well as lower energy consumption and the capacity to operate under conditions of greater environmental stress. These new models will be released along with the new type robot controller "ERCD" on July 1, 2004.
The new "YMS Series" models represent a new type of compact single-axis robots designed so the rod extends out and back from the main body and they are suitable for jobs involving transport employing a variety of tools that can be fastened to the end of the rod or jobs where the rod is used to push the work piece. Supplementing the high quality and high precision functioning are unique structural elements that produce a high level of unit rigidity and make possible a longer maintenance-free period. Adopting the same high-performance servo motors as the Yamaha T4 and T5 models of the "FLIP-ZX Series," these new models achieve a high level of reliability. Whats more, with innovations like making these models compatible with the existing programming devices and computer software used by the users, Yamaha has radically changed the conventional concept of rod-type single-axis robots. In terms of cost performance, we have been able to reduce the price by about 10% compared to our existing FLIP-X series models when sold in combination with the new type robot controller "ERCD." The result is a low price on par with the air cylinder type models.
All of this makes the new "YMS Series" compact single-axis robots products that are sure to find an expanded market due to their capacity to answer the diversifying needs of todays users. |
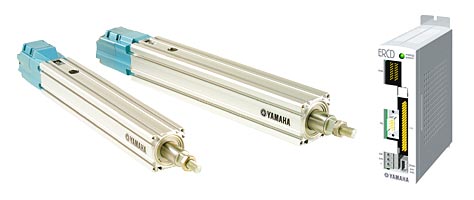 |
Yamaha Rod-type Single-axis Robots "YMS Series" |
Name: |
Yamaha Rod-type Single-axis Robots "YMS Series"
YMS45, YMS55 |
Release date: |
July 1, 2004 |
|
 |
 |
Market Background and Product Summary |
 |
 |
The new "YMS Series" rod-type single-axis (single arm) robots in two models, the YMS45 and YMS55, represent next generation single-axis robots intended to replace air cylinder type models in the primary functions of work clamping and pressure insertion. These new models have been developed for compactness, low cost and ease of use that will surely answer the needs of todays production line robots.
Elimination of pressurized air use and reduction of energy use are two important objectives for production line operators in recent years. By replacing present air cylinder type robots with the YMS Series robots, production line operators can make their facilities more environment friendly (no lubricating oil to pollute the environment), eliminate the typical exhaust noise of air cylinder type robots (low noise level), make their lines more energy efficient (energy saving) and also greatly reduce running cost to about 1/3.
As todays products become more and more compact, the need for production line facilities that are more efficient, compact and inexpensive are accelerating rapidly. Adopting the same high-performance motors as the models of the Yamaha "FLIP-ZX Series," greater rigidity and a maintenance-free rod mechanism, these new models achieve a higher level of reliability and greater compactness.
Furthermore, when used in combination with the new type robot controller "ERCD," the YMS series models offer lower cost, the reliability of servo motors and the ease of use of stepping motor operation.
By thus providing new possibilities for the production line, it is hoped that these new models will find strong demand among operators wishing to switch from their present air cylinder type robots.
|
 |
 |
Product features |
 |
 |
 |
(1) Compactness |
|
|
- |
The width of the YMS45 has been kept to a narrow 45 mm and the overall length to a 212 mm with a stroke of 50 mm. |
|
- |
The YMS55 adopts a cylinder with f 25 mm and by setting a larger rated load moment, this model is capable of handling applications that require a considerable load. |
|
- |
By adopting brake-fitted motors, the YMS45 and YMS55 can also be used in the vertical position. |
|
- |
With a repeat positioning accuracy of + 0.02 mm, these models have been made capable of holding work in a pressure-applied state ((static) push operation). |
|
|
|
 |
(2) Super compact robot controller "ERCD" with selected functions |
|
|
- |
As with the existing ERCX robot controller, the new ERCD robot controller has been developed as a new type that combines the reliability of servo motors with the ease of use of stepping motor operation. With the capability for programmed operation, point trace function and a new pulse train input capability, this controller performs three functions in one unit.
Besides being programmable using the same program language as existing Yamaha robot controllers, it is possible to set up to a total of 64 positioning point using the newly added point trace function which then makes for easy operation by just inputting the positioning point by number.
Also, the newly added pulse train input capability makes possible a wide range of uses such as controlling the drive shaft of a specialized machine. With its super compact design measuring only 44 mm x 166 mm x 117 mm (width x height x depth) and a weight of 450 g, it fits very efficiently onto the controller platform. |
|
|
 |
 |
(3) Low cost |
|
|
- |
When sold in combination with the new type robot controller "ERCD," the cost of the new Yamaha "YMS Series" rod-type single-axis robots has been kept to a level about 10% less than the existing the Yamaha "FLIP-X Series" models. |
|
|
 |
 |
(4) Ease of maintenance |
|
|
- |
If some breakdown should occur, these robots are designed so that components in the robot body like the motor(s) can be replaced locally, thus making it possible to greatly reduce MDT (Mean Down Time). With built-in contact scraper and circulation system, these models are maintenance-free for long periods.
|
|
|
 |
 |
Main Applications |
 |
 |
These robots have a wide range of applications, ranging from assembly, insertion, ejection and transport (transfer, placement) of electrical /electronic parts and machine parts to uses involving special head attachments that can make these robots useful for a wide variety of jobs.
|
 |
 |
Specifications |
 |
 |
|
|
Basic Specifications for the Robot Body |
Model type |
YMS45 |
YMS55 |
Motor type |
AC servo motor 30W |
AC servo motor 30W |
Repeatable positioning accuracy (mm) |
+- 0.02 |
+- 0.02 |
Deceleration mechanism |
ball screw |
ball screw |
Ball screw lead (mm) |
12 |
6 |
12 |
6 |
Max. speed (mm/sec.) |
600 |
300 |
600 |
300 |
Max. transport weight (kg) |
Horizontal use |
4.5 |
6 |
5 |
9 |
Vertical use |
1 |
2 |
1 |
2 |
Rated thrust (N) |
32 |
64 |
32 |
64 |
Stroke range (mm) |
50~200 (50 pitch) |
50~300 (50 pitch) |
Overall length (mm) |
Stroke length + 212.5 |
Stroke length + 228.5 |
Width (mm) |
45 |
55 |
Height (mm) |
45(52) |
55 |
Weight (kg) |
1.5 |
2.2 |
Basic Specifications for the robot controller ERCD |
Arm (axis) control |
Compatible Motor Output |
AC servo motor (Max. 30W) |
No. of arms controllable |
One |
No. of robots controllable |
YMS45/YMS55/T4/T5 |
Control type |
AC fully digital software servo |
Positioning sensor type |
Resolver |
Position setting increment |
mm |
Operating method |
PTP operation (point trace type) |
Speed setting |
1~100%, by 1% |
Acceleration/deceleration setting |
Set automatically on the basis of robot type and carrying mass parameters |
Set on the basis of acceleration speed parameters 1~100, by 1% |
Programming related |
Programming language |
Yamaha robot language, multi-task function: max. 4 tasks |
No. of programs |
100 programs, 255 steps/one program |
No. of points |
1,000 points (64 effective points with point trace function) |
No. of program steps |
1,024 steps |
Point input method |
Manual data input (coordinate input)
Teaching play back
Direct teaching |
Command form |
I/0 |
Sequence mode |
Robot operation by specialized input signal |
Pulse train mode |
Type |
A phase/B phase, pulse train /code, one choice of CW/CCW |
Form |
Line driver (+5V) |
Frequency |
Max. 2Mpps |
Serial transmission |
Transmission/reception of various data types by transmission command, parameter setting, robot operation
Transmission/reception of various data types by TPB (option), point teaching, robot operation |
External Input/output |
Multipurpose input/output |
6 points / 6points |
Specialized input/output |
8 points / 3 points |
External electric power source |
DC24V max. 5A (varies with robot used) |
External communication |
RS-232C 1CH (with programming device or PC communications) |
Brake on/off output |
Yes |
Emergency shut off |
Normal closed contact point (With recovery function for emergency stops) |
General specifications |
Electrical source |
24V +- 10% 3A |
External dimensions |
44 mm (W) x 166 mm (H) (including stays) x 117 mm (D) |
Body weight |
0.45 kg (controller only) |
Operational temp. range |
0~40 degrees C. |
Operational humidity index |
35~85% RH (without condensation) |
Options |
Select options |
Teaching programming box (TPB), support software (POPCOM)
CC-Link, DEVICENET, PROFIBUS, ETHERNET
I/O connector (CN1, CN2), memory card (1M), PC transmission cable |
|
|