Yamaha Motor Co., Ltd. will unveil the 2003 European model Yamaha Sport "YZF-R6" at the "Intermot Munich 2002" (3rd international motorcycle and scooter show) to be Munich, Germany for five days starting September 18. (Press introduction day is Sept. 17th.) This will be the first production model to feature parts cast by the new Yamaha "CF Aluminum Die casting Technology."
After its debut at the Intermot show in September of 1998, the original YZF-R6 quickly won acclaim in Europe as "a supersport machine that offers full enjoyment of 600cc power" and became the new standard in the mid-class supersport category. The 2003 model represents first model change of the YZF-R6 in four years and was developed around the same original model concept while adding further refinement of cornering performance and even more exciting engine performance.
The main changes in the new YZF-R6 include, (1) a new engine comprised of about 90% new parts, (2) fuel injection, (3) meets EU2 emissions standards, (4) first production motorcycle frame made exclusively of cast parts, (5) chassis parts made by Yamaha's new CF Aluminum Die Casting Technology rear frame and rear arm) and (6) styling that tells you at a glance this is the 2nd-generation YZF-R6.
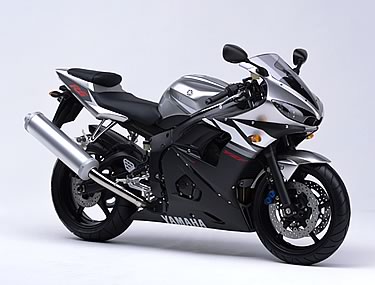 |
2003 European model Yamaha Sport "YZF-R6" |
|
Name: |
Yamaha Sport "YZF-R6" |
Release date: |
December 2002
(varies with European sales companies) |
|
 |
 |
Main Features and Changes |
 |
 |
 |
Engine |
|
1) New engine with 90% new parts including new-design pistons |
The new YZF-R6 adopts a new liquid-cooled 4-stroke DOHC in-line 4-cylinder 4-valve engine with about 90% new parts including new forged pistons designed for optimum strength balance, new high-lift cams and a redesigned crank case.
While maintaining the outstanding character of the existing engine based on the bore x stroke dimensions, compression ratio and the combustion chamber shape, the new engine is characterized by boosted performance across the full rpm range due to improvements such as optimized intake/exhaust efficiency and measures to reduce pumping-related horsepower loss. As a result, a power increase of about 3 hp has been achieved while maintaining the same maximum power output rpm of 13,000 rpm (while ram-air intake is in effect). |
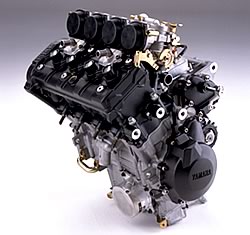 |
|
2) Liner-less direct plated cylinder |
In order to reduce the resistance of the piston in motion, a new type of cylinder has been adopted which eliminates the cylinder sleeve and applies plating directly to the inner wall of a die-cast cylinder for what is called a "direct-plated cylinder." Elimination of the sleeve enables outstanding heat dissipation characteristics, good strength balance and a more precise cylinder design. What's more, increasing the strength of the land that holds the rings, optimizing the thickness of the top ring and revising the ring tension all contribute to more stable piston movement. All this helped in achieving a more consistent gas seal and excellent oil-consumption characteristics.
Furthermore, the new crankcase design with enlarged passages between the cylinders reduces fluctuation in air volume due to the pumping action of the pistons, thus reducing pumping-related horsepower loss. This helps produce to outstanding response characteristics. Horsepower loss has also been reduced by various design measures like optimizing the crank balance to reduce the load on the crank journal.
|
|
3) Fuel Injection system with suction piston |
In order to obtain both outstanding intake efficiency and good response, this model adopts the same suction-piston type fuel injection (FI) system that has won such high acclaim on the 2002 model YZF-R1. This system uses the motion of a free piston that moves in accordance with the air pressure fluctuations to regulate air intake flow from the low-speed range, thus making possible both linear throttle response that retains a natural (carburetor-like) intake feeling and the outstanding response and reliability of electronic control. This enables the new YZF-R6 to achieve acceleration characterized by a second acceleration curve beginning at 8,000 rpm and excellent top end power development that continues without stress past 12,000 rpm. |
|
4) New-design intake system |
To improve engine response in conjunction with the adoption of the new FI system, the air cleaner capacity has been increased (7.3 → 7.6 liters) along with the diameter of the throttle body (37 → 38 mm). The same "ram-air system" used on the existing model is adopted, and to accommodate the new FI system, the volumes of the intake air passages at the open and closed states have been optimized to produce even better performance. |
|
5) New-design titanium muffler |
The exhaust system has also been completely re-designed for improved performance and weight reduction. The previous two-section interior structure of the diffuser has been replaced by a single-unit titanium structure. The double-layer tube structure with glass wool stuffed in between the two layers is given a curved shape that provides both outstanding exhaust efficiency and reduced noise. In addition, a lightweight aluminum outer cover for the silencer has been adopted along with other changes including an increased overall size for the exhaust system, new pipe length dimensions and joint position, new silencer expansion chamber ratio and changes in the sizes of the various tubing, all designed to bring out the new engine characteristics to the fullest. All in all, this new exhaust unit is a full kilogram lighter that the existing unit even when the weight of the new catalyzer element is added.
|
|
6) Other changes |
Other changes include (1) clearing EU2 emissions standards, (2) optimization of the shape of the crankcase cover to improve oil return, (3) adoption of a lightweight aluminum oil cooler, (4) weight reduction through the use of plastic for some internal engine parts, (5) rare-earth element magneto adopted for a thinner ACM, (6) revision of shift rigidity and change in shift revolving mass and (7) adoption of a round radiator with excellent cooling performance with no increase in size compared to the previous unit. |
|
|
 |
Chassis |
|
1) Deltabox III frame characterizing the 2nd-generation YZF-R6 |
To achieve high-level cornering performance, this model adopts an all die-cast aluminum frame. Called the Deltabox III frame, this new frame is still different from the Deltabox III frame on the YZF-R1, particularly in its two-piece mold-cast construction. Made possible by a new Yamaha die-casting technology in which all the conditions of the casting process are precisely controlled, this new construction greatly reduces the number of welding points (16 → 2), which in turn enables optimized strength and rigidity balance and reduced weight, while also adding a look of quality in its external appearance.
This frame is 50% more rigid with regard to lateral torsion than the existing model's, achieving a level equivalent to the YZF-R7's frame. This is an important factor that contributes to this model's outstanding handling characteristics. The engine mounting was changed from the existing three-point forward adjustable system to a directly rigid mount that contributes to lighter handling and increased sense of rider-machine unity.
|
|
2) Long rear arm adopting CF Aluminum Die Casting Technology |
The rear frame and rear arm on the new YZF-R6 employ the advanced Yamaha-exclusive "Controlled Filling (CF) Aluminum Die Casting Technology" for the first time ever on a production model. The resulting rear arm is characterized by its smooth curved form and minimal-thickness design that reaches a mere 2.5mm at its thinnest points. On the rear frame as well, it is possible to achieve a minimum thickness of just 2mm at some points, thus enabling considerable weight reduction and ideal rigidity balance. (This is the first production model ever to use aluminum die-cast parts for the main frame, the rear frame and the rear arm.)
|
|
3) 35mm fork offset and other optimized dimensions and pivot position |
With the aim of achieving even more outstanding handling characteristics, the same wheelbase and caster dimensions as the existing model are maintained while new dimensions including a shortening of the fork offset by 5mm to 35mm, an accompanying change in the axle bolt mechanism for the front wheel and thinning of the inner tube of the front fork have been made to achieve optimized balance.
Furthermore, reducing the distance between the drive axis and the pivot axis from 96m to 86 mm reduces the effect of the chain tension on the drive force during acceleration. The rear arm has also been lengthened by 10mm to 575.5mm to achieve an optimum balance in regard to rebound road force. The combined result is a more stable, lighter feeling to the steering and outstanding traction. |
|
4) New-design lightweight 5-spoke wheels |
Adoption of newly designed lightweight 5-spoke wheels reduces unsprung weight. Employing a thinned out design that treats the hub and spokes as one structural unit has enabled an optimum strength-rigidity balance. |
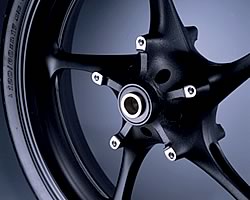 |
|
5) "New Edge Form" design, Gatling beam headlights |
For the body design a "New Edge Form" concept has been adopted to define the new styling character of the R series models. In particular, the design reflects the new engine's improved intake efficiency with a body design that accentuates an active intake of airflow into the machine.
As for the new-design headlights, better illumination is ensured by adopting a Gatling beam headlight characterized by the outstanding evenness of its light distribution. This is accompanied by a re-shaping of the front assembly that provides superior protection as well as an impressive new look to the front face of the machine. |
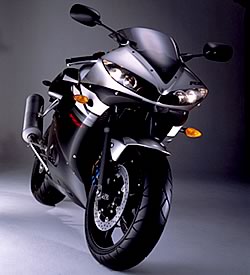 |
|
6) Others, forged aluminum parts, etc. |
Forger aluminum parts are adopted for the footrest and rear shock absorber parts that give an added look of quality (previously cast aluminum parts). Changes have also been made in the rear brake system (caliper, disc, master cylinder changed). Other changes include the addition of a storage space for a "U" lock under the seat for added convenience. |
|
|
 |
 |
Reference |
 |
 |
The Yamaha CF Aluminum Die Casting Technology |
Due to the controlled conditions under which the molten aluminum is injected into the metallic mold (die) at high speeds and high pressure in conventional high-pressure die casting, a certain amount of air and oxides inevitably enters along with the aluminum, resulting in air pockets in the final cast metal. As a result, there was a limit to how thin sections of the cast parts could be and how sharp the curves in the parts could be. This was a weakness of the conventional die casting method that left room for improvement. The "Yamaha CF Aluminum Die Casting Technology" is the result of development efforts focused on the "shaping technology" applied to aluminum die cast parts in order to improve on this weakness in the conventional methods.
The technical focus in developing this new method was to optimize the flow characteristics of the molten aluminum to obtain the best possible flow into the die in the short time before the aluminum begins to solidify with optimum evenness in the final lie of the aluminum before it hardens.
To achieve this, we built on the technological base acquired from our long years of experience in vacuum aluminum die casting and added an exclusive new method for improving the completeness of the vacuum in the die which also made possible more precise control of the various aspects of the casting process. Specifically speaking, we optimized the conditions of the molten aluminum injection into the die by (1) introducing an exclusively developed new type of seal material for sealing the die parts together to increase the completeness of the vacuum inside the mold and reduce the air resistance (six-fold improvement over conventional method), (2) controlling the temperature of the mold in order to achieve a more stable temperature in the molten aluminum and, (3) Increasing the speed of the molten aluminum injection (five times conventional method). The combined effect of these measures reduced the amount of air (gases) in the resulting cast metal to one-fifth the content of the conventional method. This results in a stronger quality aluminum that, unlike conventional die cast aluminum, is strong enough to be welded, which in turn makes possible the mass production of aluminum die cast parts that are both large and thin in certain sections.
What has been achieved thanks to this new method is the capability to manufacture parts with the "high (mass) production efficiency" of high-pressure die casting and the strength and pliability of gravitational casting. This has made it possible to mass produce the kind of large but thin aluminum die cast parts that were difficult under the conventional die casting methods. Also, since this new method enables the mass production of cast aluminum parts designed for extreme thinness and more complex curves, it will enable new design standards for cast aluminum parts. |
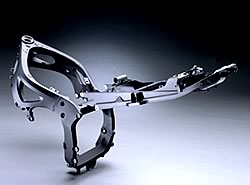 |
 |
The two-piece mold-cast frame and the rear frame employing the new CF Aluminum Die Casing Technology |
The rear arm made by Yamaha's new CF Aluminum Die Casing Technology |
|
|
 |
 |
2003 Model Yamaha"YZF-R6" Technical Specifications
(Garman market specifications) |
 |
 |
Overall length x width x height
Seat height
Wheelbase
Dry weight
Engine type
Cylinder arrangement
Displacement
Bore x Stroke
Compression ratio
Maximum power
Maximum torque
Starting system
Fuel tank capacity
Fuel supply
Tire size(Front / Rear) |
2,025mm x 690mm x 1,090mm
820mm
1,380mm
162kg
Liquid-cooled, 4-stroke, DOHC, 4-valve
In-line 4 cylinder
600cc
65.5mm x 44.5mm
12.4: 1
86.0kW(117HP)/13,000rpm
66.4N-m(6.78kgf-m)/12,000rpm
Electric
17liter
Electronic-control fuel injection
120/60ZR-17M/C 55W / 180/55ZR-17M/C 73W |
|
*Maximum power during ram-air intake is 90.5kW (123HP) @ 13,000rpm |
|
|