Yamaha Motor Co., Ltd. has just developed a new automobile suspension technology called the Relative Absorber System (REAS) that optimizes control of the relative movement of the right and left wheel suspensions. Featuring a REAS valve situated between the highperformance left and right shock absorbers, the system functions to smooth out lateral roll and greatly improve the road grip of both the right and left tires, thus giving a more comfortable ride and handling stability.
The usual automobile suspension performs two functions. The first is to absorb shocks from the road to provide a comfortable ride, while the second is to attain good handling stability by maintaining a stable chassis attitude in relation to the road by controlling the forces of acceleration and braking and centrifugal force when cornering. However, these two aims are often mutually conflicting, as typified by the fact that stiffening the suspension in order to improve stability naturally decreases comfort due to reduced shock absorption.
The newly developed REAS features an entirely new mechanism that functions not only to achieve a comfortable ride with a relatively small amount of damping force in cases like when both tires hit a gap in the road, but also functions to stabilize the body of the automobile against lateral "rolling" motion by adding a suitable amount of extra damping force and absorb the force acting in the lateral roll direction, as when cornering, when the pattern of depressions and protrusions in the road surface are different on the left and right wheel sides or when subjected to cross winds. In this way, it is possible for the new system to achieve both a comfortable ride and outstanding handling stability.
The structure of the REAS system includes right and left shock absorbers with exceptional responsiveness which are connected to each other by means of a shared hydraulic passage and a third unit positioned at the mid-point on this passage between them. This third unit consists of (1) a REAS valve, (2) a gas chamber and (3) a free (separating) piston. The system is constructed so that the phase of damping speed of the two shock absorbers is reflected in direct proportion by the amount of hydraulic fluid flowing through the REAS valve.
Making use of this proportional motion principle, the REAS system functions by means of the REAS valve's capability to automatically generate a suitable amount of additional damping force when necessary based on differential piston speed between the two shock absorbers. In other words, this system can be called a "speed-differential-sensitive shock absorber." |
 |
 |
REAS characteristics |
 |
 |
1. |
By stabilizing automobile body movement, especially lateral rolling motion, it achieves greater handling stability and reduces unpleasant laterals way. |
2. |
Because the system can automatically generate additional damping force when necessary, softer springs can be used, thus making possible an even more comfortable ride. |
3. |
By stabilizing the body attitude with relation to the road, the force of contact between the tires and the road is optimized, which enables the tires to function to their fullest potential. |
|
This new technology has the potential to be applied to a wide range of motor vehicles, from passenger cars to trucks, buses and racing cars. When adopting this system on production automobiles, it is necessary to develop individualized designs to fit the distinct specifications and layout of the automobile involved. |
 |
 |
The Aim in developing the REAS system |
 |
 |
The main components of a suspension are the spring and the shock absorber. The spring functions to soften the shock, while the shock absorber serves to absorb the force of the shock by converting it's energy to heat. The combination of these two components is a vital element determining the comfort of a car's ride and its handling stability.
Research and development efforts by various manufacturers have been directed at the improvement of shock absorbers in recent years, resulting in the development of valve form devices that generate damping force, hydraulic passages and various improvements to the related mechanisms. Recently, as a result of research into the various characteristics of shock absorbers, several types of electronic-control suspension technology aimed at actively controlling the motion of the car body have been put into use.
In the development of the new REAS system, we developed a system with a mechanism capable of generating damping force that would effectively absorb lateral roll energy and thus achieve the desired combination of a comfortable ride and outstanding handling stability. Furthermore, the REAS system is one that is amicable to the human sensibilities of the driver and passengers because it functions with no annoying time lag or inconsistency. It also has the merits of being lightweight and simple in design with no complicated mechanisms, thus affording great design flexibility when applied to automobiles. |
|
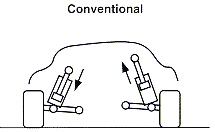 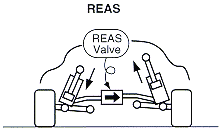 |
 |
 |
Structure and function of REAS |
 |
 |
The three main points of the REAS structure are as follows |
1. |
The left and right shock absorbers have separate oil chambers with a REAS valve positioned on the connection flow passage. |
2. |
A single gas chamber is shared by the left and right. |
3. |
Using the separate actions of hydraulic fluid and gas, a separating piston is activated by the coupled movements from the right and left. |
|
The following is an explanation of the working principle of the REAS system in the cases of the two extremes of complete opposite-phase and complete in-phase motion. |
 |
 |
In the case of opposite-direction motion between the left and right suspensions (opposite-phase) |
 |
 |
Diagram 1 is an illustration of the system when the car is viewed from the rear and shows the movement of the absorbers and the flow of hydraulic fluid when the car is turning to the right. In such a condition centrifugal force is causing the car to roll to the left.
In this situation the left shock absorber is compressed and the right tries to extend. Because the flow of hydraulic fluid in an amount equivalent to the volume displaced by the travel distance of the left shock absorber's piston rod supplements the hydraulic fluid being displaced by the travel of the right piston rod, the hydraulic fluid passing through valve b (REAS valve) becomes flow B. In this way, at the contracting shock absorber on the left, the damping force of valve b supplements the damping force of valve a, while at the extending shock absorber on the right, the damping force of valve b supplements the damping force of valve c, to absorb the lateral roll energy acting on the car body. |
|
[Diagram 1] |
![[Diagram 1]](images/g1.gif) |
 |
 |
In the case of same-direction motion of the right and left suspensions (in-phase) |
 |
 |
Diagram 2 shows a case in which both the right and left wheels hit a depression in the road at the same time. In such a case, the volume of hydraulic fluid displaced by the travel of the piston rods of the right and left pistons becomes flow B, which is absorbed by the movement of the separating piston without passing through valve b (REAS valve). As a result, a damping force of only the main valves a and c is in action relatively to achieve a soft and elastic drive feeling. |
|
[Diagram 2] |
|