Always Striving for Something Better: A Yamaha Tank-Forming Tradition
Motorcycle fuel tanks store and supply the gasoline for the engine and hence are fundamental to the machine’s very operation. Additionally, because the fuel the tank holds is highly flammable and volatile, safety is the first priority in its construction. However, the tank’s exterior appearance and presence plays a defining role in the motorcycle’s overall design. Further, the shape of the tank’s knee grip area is another heavy responsibility as it is a key factor in producing the rider’s feeling of unity with the machine.
Yet, this component that must perform so many important roles simultaneously at a high level must be fashioned from pieces of steel sheet metal—no easy task. This is especially true with the new MT-09, the face of the MT Series that features a unique visual character composed of numerous complex lines and surfaces.
The Natural Enemies of Nice Skin: Wrinkles and Roughness
A massive press machine sits in the center of Yamaha’s tank-forming work area. “I can’t say it’s the most modern press,” says one technician. “But we’ve been using it for so long that we know its little quirks inside out. And while the process for pressing tanks is very dynamic, it’s also very delicate. It’s always an on-the-limit ‘clash’ between our skills and the steel, and this intimate familiarity or innate sense with our tools and equipment becomes critically important.” In describing what they do, on or at “the limit” is constantly uttered by the tank press technicians.
Imagine a single sheet of steel being pressed into its final shape instantly from an enormous force. Due to the desired three-dimensional shape being very complex, any areas subjected to excessive pressure will stretch and roughen, and in turn, this roughened steel ends up creating wrinkles in the surface somewhere else. In a way, the rough skin and wrinkles are the natural enemies of the nice skin the craftsmen are trying to create in the tank-forming workshop.
To successfully create a tank that is not only safe and stylish but also has a smooth surface finish all at once, Yamaha’s craftsmen must make use of the sheet steel’s characteristics to the very limit. The way the engineers and technicians carefully tackle and finish the more delicate parts of the work are what push it into the world of artisanry. “If our Monozukuri was based on only doing what we know we can do, making fuel tanks wouldn’t be that difficult,” one technician says as the press thumps loudly in the background. “But when our goal is to take things to the very limit, difficulties are always part of the journey.”
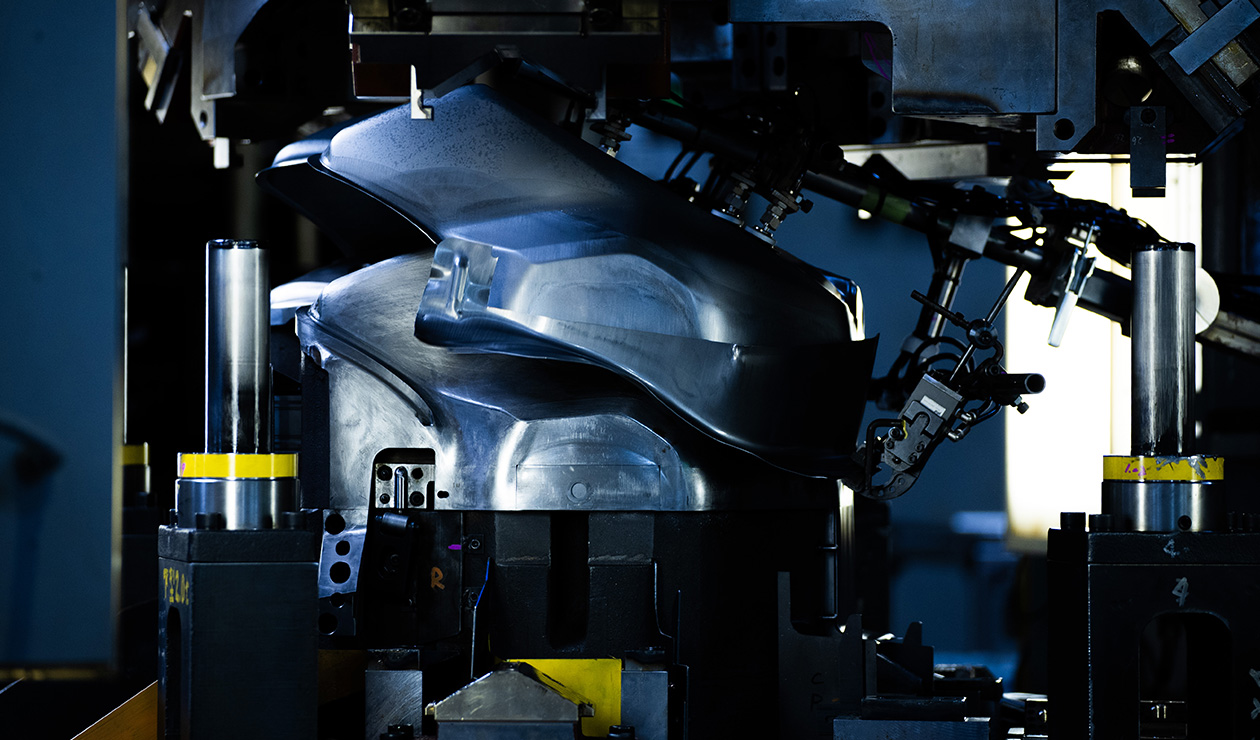
Eliminating Deformations with Master Craftsmanship
After the press has formed the sheet metal into shape, the tank moves to its next stage and is split from the top into left and right halves before rendezvousing with another formed sheet that will become the bottom of the tank. The three pieces are seam-welded together, resulting in a joint-free tank. However, as the separate pieces are welded together, welding tracks and slight deformations occur. Controlling their breathing, Yamaha’s craftsmen carefully use their welding electrodes to gently massage the two pieces together while eliminating these deformations at the same time.
Contradictions abound at Monozukuri worksites. For example, computer simulations can lead to “ideal” solutions to production issues, but they still remain extrapolations of what to expect. The ideal result determined via analysis and the small variations that creep into and accrue in the 4Ms (Man, Machine, Materials, Method) inherent to manufacturing are what produce these deviations and deformations, and when all is said and done, they are eliminated by a craftsman’s proficient handwork. How their hands move dynamically over the workpiece with a certain beauty and care is truly the mark of industrial craftsmanship.
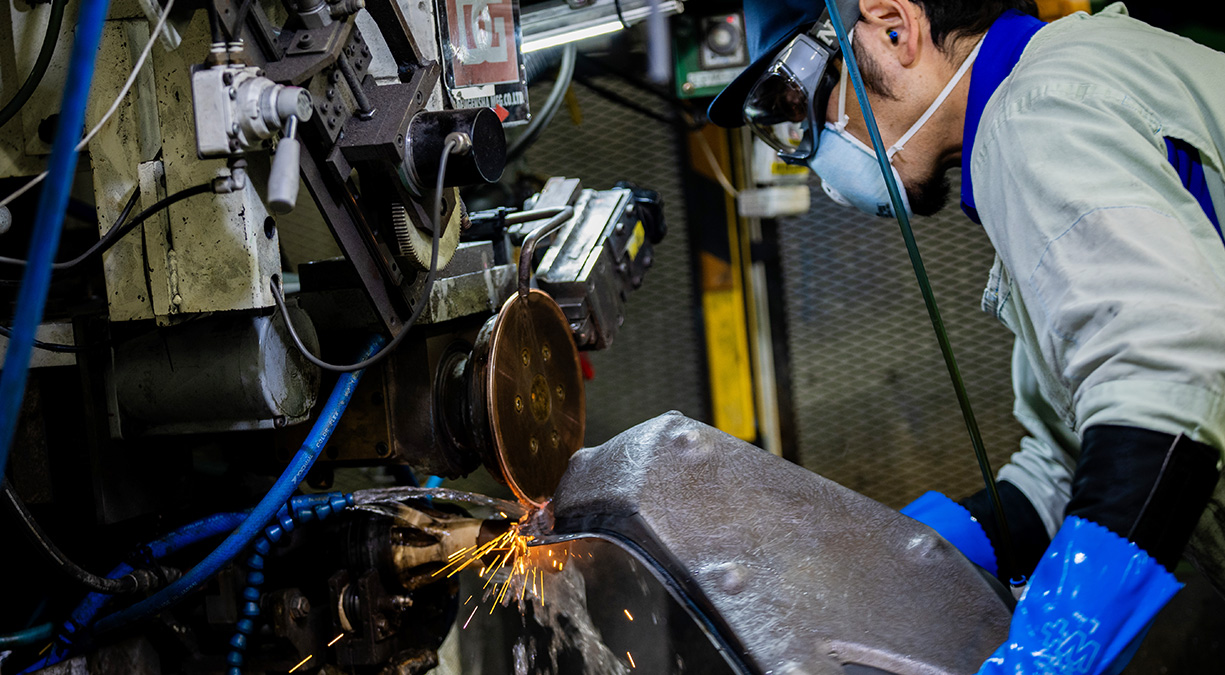
Eyes and Hands That Notice the Changes of Each Day
The fuel tank is one of the main parts heavily influencing the overall design appeal of a motorcycle. As such, no compromises are allowed in ensuring it is beautiful to the eye. However, the molds, steel sheets, presses and welding equipment all change slightly from long hours of daily use. It is up to the craftsmen to notice these changes with their eyes and hands and make the required fine adjustments to compensate. This day-by-day concern is vital for mass-producing products with consistently high quality.
Creating the tank’s exterior finish involves a multi-step process with inspections best suiting the tank in question. The tactile check has the inspecting craftsmen run the palms of their hands across the tank’s various surfaces to feel out any tiny imperfections that may escape the human eye. There is also the Polinet cloth polishing inspection for detecting even smaller flaws in the surface. Conducting this inspection properly also requires the right sense and skills, as only highly experienced craftsmen can polish the tank in a manner that reveals such minute flaws. Only after clearing numerous strict visual inspections at the end is a Yamaha fuel tank finally certified as complete.
“The worksite is filled with the desire to always strive for something better,” professes one engineer. “The tank for the new MT-09 is a good example. The deep cavity that stretches from the protruding top edge of the tank down to the knee grip area is a shape we couldn’t produce with our previous Monozukuri. But we just kept striving for it until we succeeded at making another step up.”
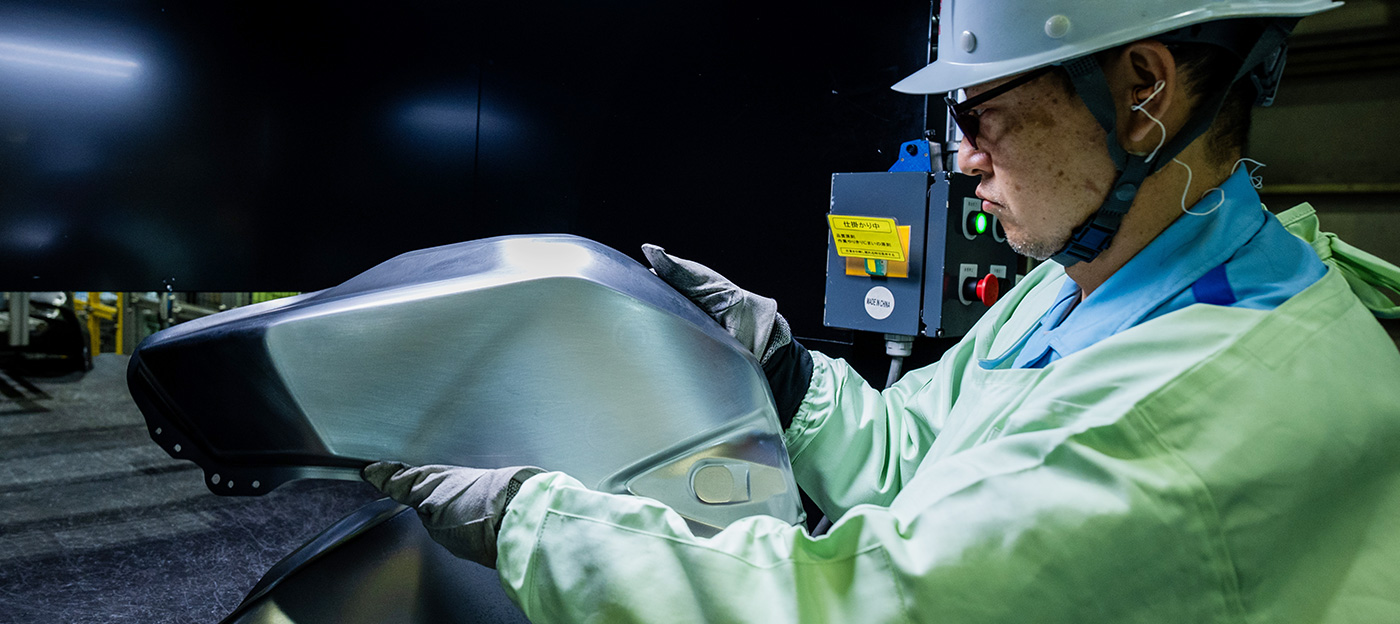